water cooled portable chiller
A water cooled portable chiller is a compact, mobile cooling device designed to circulate chilled fluid through external equipment while using an external water source (such as a tap, bucket, or cooling tower) to dissipate heat from its refrigeration system. Unlike stationary water-cooled chillers, these units are lightweight, often mounted on casters, and feature integrated handles for easy transport, making them ideal for applications where cooling needs are temporary, mobile, or space-constrained. They combine the high efficiency of water-cooled systems with the flexibility of portability, typically maintaining fluid temperatures between -10°C and 30°C with precision ranging from ±0.1°C to ±1°C, depending on the model. This unique blend of performance and mobility makes them indispensable in settings ranging from temporary laboratory setups to field-based industrial testing.
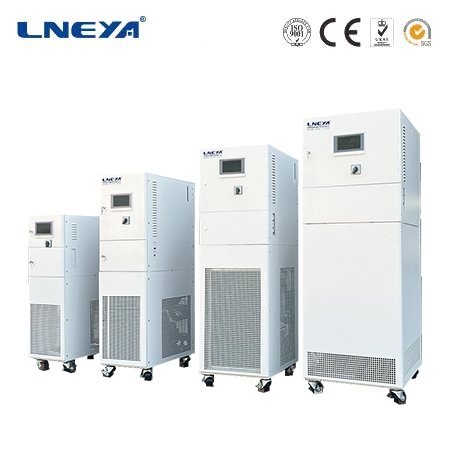
The operation of a water cooled portable chiller is based on a closed-loop fluid circulation system paired with a water-cooled refrigeration cycle. Here’s a detailed breakdown of its working mechanism:
The chiller draws warm fluid from the connected equipment (e.g., a laser cutter or analytical instrument) into its internal fluid circuit via a pump. This fluid passes through an evaporator, where it comes into contact with a cold refrigerant. The refrigerant absorbs heat from the fluid, causing the fluid to cool down. The chilled fluid is then pumped back to the equipment, completing the cooling loop.
Simultaneously, the refrigerant, now heated from absorbing the fluid’s heat, flows to a water-cooled condenser. An external water source (e.g., tap water) is pumped through the condenser, absorbing heat from the refrigerant and carrying it away. The cooled refrigerant then passes through an expansion valve, which reduces its pressure, causing it to cool further before re-entering the evaporator to repeat the cycle.
A built-in temperature controller monitors the temperature of the chilled fluid using a sensor (e.g., RTD or thermocouple). It compares this reading to the user-set temperature and adjusts the refrigeration system’s output (e.g., compressor speed) to maintain the desired temperature, ensuring stability even as the equipment’s heat load fluctuates.
A water cooled portable chiller comprises several key components that work together to deliver efficient, precise cooling:
The compressor is the heart of the refrigeration system, responsible for pressurizing the refrigerant to raise its temperature, enabling it to release heat in the condenser. Portable chillers typically use reciprocating or scroll compressors, chosen for their compact size, low noise levels, and efficiency in small to medium cooling capacities (ranging from 500 watts to 10 kilowatts).
The water-cooled condenser is a heat exchanger that transfers heat from the refrigerant to the external cooling water. It is usually a shell-and-tube or plate-type design, where refrigerant flows through one set of channels and cooling water through another, maximizing heat transfer via direct contact between the two fluids. The condenser’s compact size is critical for portability, often featuring quick-connect fittings for easy attachment to external water sources.
The evaporator is another heat exchanger, this time transferring heat from the process fluid (the fluid cooling the external equipment) to the refrigerant. It ensures efficient heat absorption, with designs optimized to minimize pressure drop in the fluid circuit, preserving pump efficiency.
The fluid pump circulates the process fluid (typically water or a water-glycol mixture) through the closed loop connecting the chiller and the equipment. Portable chillers often use centrifugal or gear pumps with variable-speed controls, allowing adjustment of flow rates (usually 1 to 20 liters per minute) to match the equipment’s cooling needs.
The temperature controller is a user-friendly interface (digital or touchscreen) that allows setting the desired fluid temperature. It uses PID (proportional-integral-derivative) algorithms in higher-end models to maintain tight temperature control, adjusting the compressor and pump output based on real-time temperature readings from the sensor.
The external water inlet/outlet is a distinguishing feature, with hoses or quick-disconnect ports for connecting to the cooling water source. Some models include a flow switch that shuts down the refrigeration system if the external water flow is insufficient, preventing overheating of the condenser.
Water cooled portable chillers offer several advantages that make them preferred for specific applications:
High efficiency is a standout benefit, as water’s high heat capacity allows the condenser to dissipate heat more effectively than air-cooled systems. This results in lower energy consumption compared to portable air-cooled chillers, especially in high ambient temperatures (above 30°C), where air-cooled units struggle to release heat efficiently.
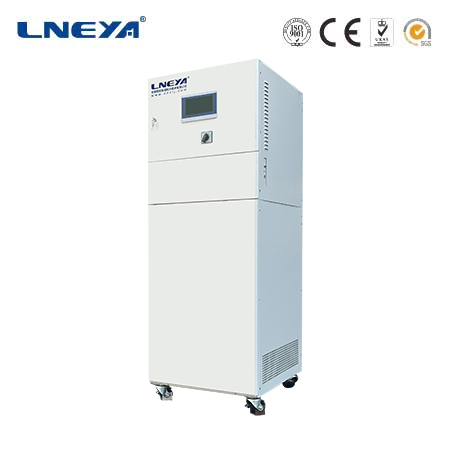
Compact size and portability enable use in tight spaces, such as crowded laboratories, mobile workshops, or field sites. Most models weigh less than 50 kilograms and feature casters, making them easy to move between equipment or locations as needed.
Low noise operation is achieved by eliminating the noisy fans used in air-cooled chillers. The only moving parts are the compressor and pump, which are often enclosed in sound-dampening housing, making these chillers suitable for noise-sensitive environments like medical clinics or research labs.
Precise temperature control is maintained even in varying conditions, thanks to advanced PID controllers and efficient heat exchange. This makes them suitable for temperature-sensitive applications, such as calibrating scientific instruments or cooling medical devices.
Flexibility in water sources allows them to use a range of external water supplies, from municipal tap water (for short-term use) to recirculating cooling towers (for extended operations). Some models can even use a bucket of water for very temporary setups, though this requires frequent refilling to maintain flow.
Water cooled portable chillers are used across diverse industries where mobility, efficiency, and precision cooling are required:
In laboratories and research facilities, they are used with temporary or mobile equipment setups, such as portable spectrometers, PCR machines, or reaction vessels. For example, a research team conducting fieldwork might use a portable chiller to cool a portable mass spectrometer, ensuring accurate readings by maintaining stable detector temperatures. Their compact size also makes them ideal for shared lab spaces, where multiple teams can move the chiller between workstations as needed.
The medical and healthcare sector employs these chillers for mobile medical equipment, such as laser therapy devices used in dermatology clinics or portable MRI scanners in remote healthcare camps. They cool the equipment’s electronics and laser components, ensuring consistent performance and preventing overheating during procedures. Their low noise operation is particularly valuable in patient care areas, where quiet environments are essential.
Industrial field testing and maintenance rely on water cooled portable chillers to cool equipment during on-site repairs or performance testing. For instance, technicians servicing industrial motors or pumps might use a portable chiller to simulate operating conditions by cooling the equipment while monitoring its performance. They are also used in trade shows or exhibitions to cool demonstration models of machinery, where permanent cooling infrastructure is unavailable.
Food and beverage processing uses these chillers for temporary cooling needs, such as small-batch production runs or mobile food trucks. They can cool mixers, fermentation tanks, or display cases, with food-grade fluid circuits (using stainless steel components and food-grade glycol) ensuring compliance with hygiene standards.
Events and temporary installations, such as outdoor concerts or temporary data centers, use water cooled portable chillers to cool audio-visual equipment, servers, or lighting systems. Their portability allows them to be deployed quickly, and their efficiency ensures they can handle the heat loads of temporary setups without consuming excessive energy.
Selecting the right water cooled portable chiller requires evaluating several key factors to match the unit to the application’s specific needs:
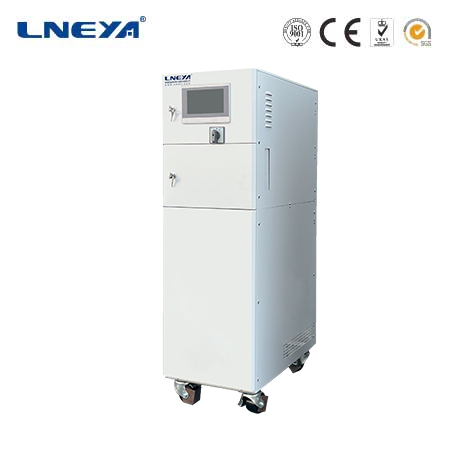
Cooling capacity (measured in watts or BTU/h) is the primary consideration, representing the amount of heat the chiller can remove. It must exceed the heat load generated by the equipment being cooled. To calculate the required capacity, consider the equipment’s power consumption (most of which is converted to heat) and any additional heat from the environment (e.g., sunlight in outdoor settings).
Temperature range and precision must align with the application. For laboratory instruments requiring stable temperatures, choose a model with a range that includes the target temperature (e.g., 5–20°C) and a precision of ±0.5°C or better. Industrial applications with broader tolerance ranges (e.g., ±1°C) can use less precise models, which are often more cost-effective.
Flow rate (in liters per minute) determines how quickly the chiller can circulate fluid through the equipment. The chiller’s pump must deliver a flow rate within the equipment’s recommended range to ensure efficient heat transfer. Variable-speed pumps offer flexibility, allowing adjustment if the heat load changes.
External water requirements include flow rate and pressure. Most portable chillers require 1–5 liters per minute of cooling water at a pressure of 1–5 bar. Ensure the available water source (e.g., tap, bucket) can meet these requirements; some models include a built-in pump to draw water from low-pressure sources like buckets.
Fluid compatibility is critical, as the process fluid (water or water-glycol mixture) must not corrode the chiller’s internal components or the equipment’s cooling circuit. For sub-zero temperatures, glycol is added to prevent freezing, with concentrations ranging from 20–50% depending on the minimum temperature. Food-grade glycol is necessary for food-related applications.
Portability features such as weight, casters, and handles affect ease of movement. For frequent transport, choose a lightweight model (under 30 kg) with sturdy casters and ergonomic handles. Some models also feature a compact design to fit through narrow doorways or into elevators.
Additional features like built-in reservoirs (to maintain fluid volume), digital displays for monitoring temperature and flow rate, and safety alarms (for low water flow or high temperature) enhance usability. Models with quick-connect fittings for hoses reduce setup time, which is valuable in temporary applications.
Proper maintenance of a water cooled portable chiller ensures reliable performance, extends its lifespan, and maintains temperature precision:
Regular cleaning of heat exchangers prevents efficiency loss. The water-cooled condenser can accumulate mineral deposits (scale) from the external water source, which reduce heat transfer. Flush the condenser monthly with a descaling solution (e.g., citric acid) to remove scale, following the manufacturer’s instructions. The evaporator should be cleaned annually to remove any debris from the process fluid, using a mild detergent and a soft brush.
Fluid circuit maintenance includes checking the process fluid level in the reservoir (if equipped) and topping up with the recommended water-glycol mixture as needed. Inspect the fluid for contamination (e.g., dirt, algae) quarterly and replace it annually to prevent corrosion or clogging of the pump and heat exchangers.
External water connection inspection ensures there are no leaks in the hoses or fittings connecting the chiller to the water source. Check for cracks or wear in the hoses, replacing them if damaged. Clean the inlet filter (if present) monthly to prevent debris from entering the condenser and causing blockages.
Temperature calibration verifies accuracy. Annually, compare the chiller’s displayed temperature to a calibrated thermometer placed in the process fluid line near the equipment inlet. If the discrepancy exceeds the specified tolerance, recalibrate the sensor using the controller’s calibration function or contact a technician.
Compressor and pump maintenance helps prevent breakdowns. Listen for unusual noises (e.g., rattling or grinding) from the compressor or pump, which may indicate worn bearings or impellers. Check refrigerant levels annually (for models with accessible ports) and recharge if necessary, as low refrigerant reduces cooling capacity. Lubricate pump bearings as recommended by the manufacturer (for non-sealed units).
Safety system testing ensures protective features function correctly. Test the low-flow switch monthly by temporarily reducing the external water flow; the chiller should shut down the refrigeration system and trigger an alarm. Similarly, test the high-temperature alarm by adjusting the setpoint above the current temperature to ensure it activates when the fluid overheats.
Emerging trends in water cooled portable chiller technology focus on enhancing portability, efficiency, and user-friendliness to meet evolving industry demands:
Enhanced portability is being achieved through lightweight materials (e.g., aluminum frames instead of steel) and more compact designs, with some models now weighing less than 30 kg while maintaining the same cooling capacity. Integrated water tanks are also becoming common, allowing the chiller to operate without a continuous external water source for short periods (using a built-in pump to recirculate water from the tank), ideal for field applications where tap water is unavailable.
Smart connectivity features are being added to high-end models, enabling remote monitoring and control via Bluetooth or Wi-Fi. Users can check fluid temperature, flow rate, and alarm status on a smartphone app, receive alerts if the chiller deviates from set parameters, and even adjust settings remotely. This is particularly useful for managing multiple chillers in large facilities or monitoring unattended field setups.
Energy efficiency improvements include variable-speed compressors and pumps that adjust their output based on the heat load, reducing energy consumption by up to 40% compared to fixed-speed models. Some units also feature heat recovery systems that capture waste heat from the condenser and use it to preheat water for other purposes (e.g., handwashing in field camps), improving overall energy efficiency.
Eco-friendly refrigerants are replacing traditional options with high global warming potential (GWP). Manufacturers are increasingly using low-GWP refrigerants like HFO-1234ze or natural refrigerants (e.g., CO₂) in portable models, aligning with global regulations to reduce environmental impact. These refrigerants are also less toxic, enhancing safety in laboratory and medical settings.
User-centric design improvements include intuitive touchscreen interfaces with preset temperature profiles for common applications (e.g., “laser cooling” or “spectrometer mode”), simplifying setup for users without technical expertise. Quick-connect fluid and water hoses with self-sealing valves reduce spillage during setup and teardown, making the units easier to use in time-sensitive applications.
In conclusion, water cooled portable chillers are versatile, efficient cooling solutions that combine the performance of water-cooled systems with the mobility of portable units. Their ability to deliver precise temperature control in a compact, movable design makes them essential in temporary, mobile, or space-constrained applications across laboratories, healthcare, industry, and events. By understanding their working principle, key features, and maintenance requirements, users can select and operate these chillers to maximize their performance and longevity. As technology advances, ongoing improvements in portability, connectivity, and sustainability will further enhance their value, ensuring they remain a critical tool in modern cooling applications.
Related recommendations
adiabatic chillers
176Adiabatic Chillers: A Deep Dive Introduction In the pursuit of more energy - efficient and sustainable cooling solutions, adiabatic chillers have emerged as a promising technology. They of...
View detailswater bath in the laboratory
23Water Bath in the Laboratory: Functions, Types, and ApplicationsIn the bustling environment of a laboratory, where precision and control are paramount, the water bath stands as an indispensable p...
View detailsWhat environmental usage requirements does industrial chiller machine meet?
840What environmental usage requirements does industrial chiller machine meet? 1. Choose an installation environment with high security. Due to the high temperature phenomenon gener...
View detailschiller kw
207Chiller kw In the world of refrigeration, the term "chiller kw" is of great importance. Kilowatts (kw) are a unit of measurement used to express both the power consumption of a chiller and its ...
View details
HelloPlease log in