chiller kw
Chiller kw
In the world of refrigeration, the term “chiller kw” is of great importance. Kilowatts (kw) are a unit of measurement used to express both the power consumption of a chiller and its cooling capacity. When it comes to the cooling capacity of chillers, there is a common conversion between tons of refrigeration and kilowatts. One ton of refrigeration is approximately equal to 3.517 kilowatts. This conversion helps in understanding and comparing the cooling capabilities of different chillers.
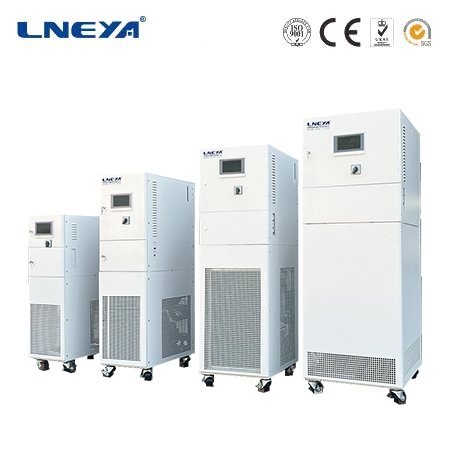
There are various types of chillers, and their power ratings in kw play a crucial role in their performance. Air-cooled chillers use ambient air to dissipate heat. A higher kw rating in an air-cooled chiller generally indicates a greater cooling capacity, allowing it to handle larger cooling loads. However, it also means higher power consumption. These chillers are often suitable for applications where water for cooling is not readily available.
Water-cooled chillers, on the other hand, use water as the heat transfer medium. They typically have a more complex setup but can be more energy-efficient in some cases. The kw rating of a water-cooled chiller determines its ability to cool a specific area or process. A chiller with a higher kw value can provide more cooling, but again, it requires a proper water supply and management system to operate effectively.
Knowing the chiller’s kw rating is essential for sizing the chiller correctly. When planning to install a chiller, the cooling requirements of the space or process need to be accurately determined. Based on this, a chiller with an appropriate kw capacity is selected. If the chiller is undersized, it will not be able to maintain the desired temperature, while an oversized chiller will result in higher energy consumption and unnecessary costs.
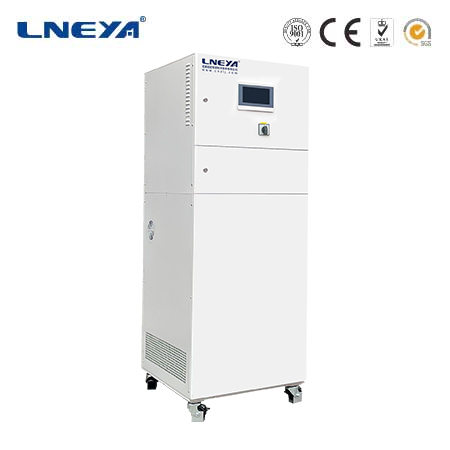
Installation also depends on the chiller’s kw rating. The electrical infrastructure needs to be able to handle the power requirements of the chiller. Higher kw chillers may require more substantial electrical connections and distribution systems. Additionally, proper ventilation and space for the chiller need to be considered, as a higher power chiller may generate more heat during operation.
Energy efficiency is a key aspect related to the chiller’s kw consumption. The Energy Efficiency Ratio (EER) or Coefficient of Performance (COP) is used to measure how efficiently a chiller operates. A higher EER or COP means that the chiller can provide more cooling per unit of power consumption (kw). Factors such as the type of compressor, the design of the heat exchangers, and the control system of the chiller can influence its energy efficiency. Modern chillers often come with features like variable speed drives for the compressor, which can adjust the compressor’s speed according to the cooling load, reducing the overall kw consumption.
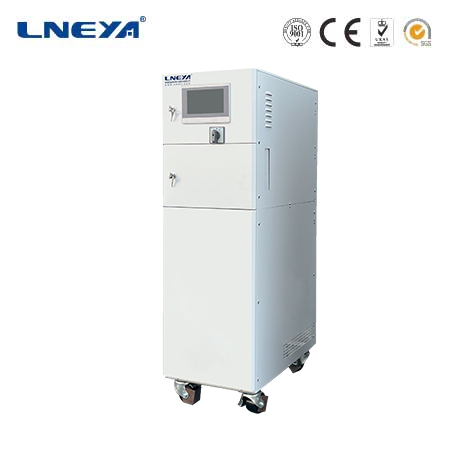
When selecting a chiller based on its kw capacity, it is important to consider the specific cooling needs of the application. This includes factors such as the required cooling temperature, the duration of operation, and the environmental conditions. For example, in a data center, where a constant and precise temperature needs to be maintained, a chiller with a suitable kw rating and high energy efficiency is crucial.
In recent years, there have been trends in chiller technology related to kw ratings. The development of more efficient compressors and heat exchangers has led to chillers with higher cooling capacities per unit of power consumption. Also, the integration of smart controls allows for better monitoring and optimization of the chiller’s operation, reducing unnecessary kw usage. Moreover, the use of environmentally friendly refrigerants is becoming more prevalent, and this can also impact the design and performance of chillers in terms of their kw ratings.
In conclusion, understanding the concept of “chiller kw” is fundamental for anyone dealing with chillers. It affects various aspects from sizing and installation to operation and energy efficiency. By carefully considering the chiller’s kw rating and related factors, users can select the most suitable chiller for their needs and ensure its efficient and reliable operation.
Related recommendations
temperature process control system
141Temperature Process Control System: A Comprehensive OverviewIn modern industrial and technological operations, maintaining accurate and stable temperature levels is often the key to ensuring prod...
View details800 ton chiller
307An 800 ton chiller is a high-capacity cooling device primarily used to remove heat from various systems and maintain specific temperature levels. Working PrinciplesVapor Compression Cycle: ...
View detailsWhat are the effects of condensation pressure and temperature changes on industrial water chiller system?
970What are the effects of condensation pressure and temperature changes on industrial water chiller system? (1) The impact of exhaust temperature In summer, the exhaust temperature of ind...
View detailsclosed cycle cryocooler
470Closed-Cycle Cryocooler Overview Closed-cycle cryocoolers are essential for maintaining low temperatures in various scientific and industrial applications. Unlike open-cycle systems, which requ...
View details
HelloPlease log in