200kw chiller
200kW Chiller
A 200kW chiller refers to a refrigeration unit with a cooling capacity of 200 kilowatts. This type of chiller is commonly used in a variety of settings where a moderate to relatively high level of cooling is required.
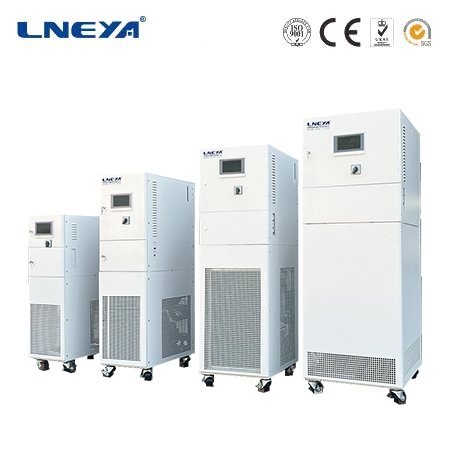
I. Types of 200kW Chillers
Centrifugal Chillers
For a 200kW capacity, centrifugal chillers can be a viable option, although they are more commonly associated with larger cooling demands. In this case, a smaller-scale centrifugal chiller might be utilized. They operate by using centrifugal force to compress the refrigerant. Centrifugal chillers are known for their high efficiency at full load. They can provide a large amount of cooling power with relatively low energy consumption when running at their rated capacity. However, at part load, their efficiency may decline more significantly compared to some other types. They are often suitable for applications where the cooling load remains relatively stable and close to the full load for extended periods.
Screw Chillers
Screw chillers are a popular choice for a 200kW chiller. They use two intermeshing screws to compress the refrigerant. These chillers offer good part-load efficiency, which makes them ideal for applications where the cooling demand fluctuates. For example, in a medium-sized commercial building where the occupancy and cooling needs change throughout the day, a screw chiller can adjust its capacity to match the load, saving energy. They are also known for their reliability and relatively simple maintenance requirements compared to some other complex chiller designs.
Reciprocating Chillers
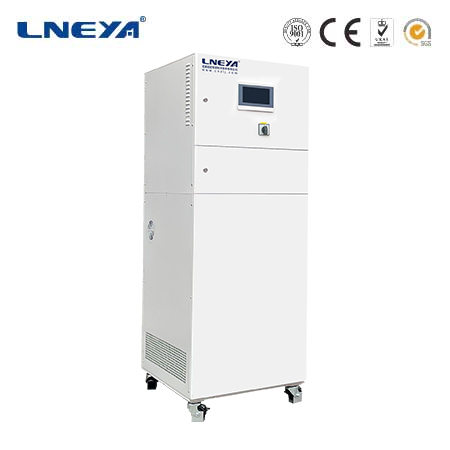
Reciprocating chillers can also be found in the 200kW range. They use a piston-cylinder arrangement to compress the refrigerant. Reciprocating chillers are generally more suitable for smaller applications or where a lower initial cost is a priority. While they may not be as efficient as screw or centrifugal chillers at high capacities, they can still provide reliable cooling for a 200kW requirement. They are often used in settings such as small industrial plants or some specialized cooling applications where the space and budget constraints are more prominent.
II. Applications of 200kW Chillers
Medium-sized Commercial Buildings
A 200kW chiller is well-suited for medium-sized commercial buildings like office complexes, shopping malls, and hotels. These buildings typically have a combination of heating, ventilation, and air conditioning (HVAC) systems that require a significant amount of cooling. The chiller can provide the necessary chilled water to cool the air handling units, which in turn maintain a comfortable indoor environment for occupants. In an office building, for instance, the chiller can cool the air during the working hours when there are many people present, and adjust its operation based on the occupancy levels.
Industrial Processes
In some industrial processes, a 200kW chiller can be used to cool machinery, equipment, or products. For example, in food processing plants, it can be used to cool food products during production, storage, or packaging. In the electronics industry, it can cool computer servers or other sensitive electronic components to prevent overheating and ensure their proper operation. Additionally, in manufacturing processes that generate a lot of heat, such as metalworking or chemical processing, a 200kW chiller can play a crucial role in maintaining the required temperature for the process to proceed smoothly.
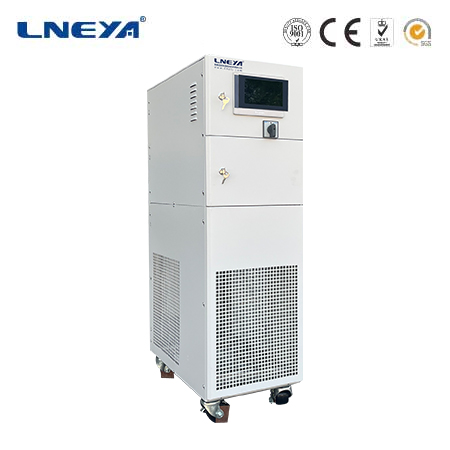
III. Energy Efficiency of 200kW Chillers
Factors Affecting Efficiency
Several factors can impact the energy efficiency of a 200kW chiller. The operating temperature of the chiller is a significant factor. Higher chilled water temperatures and lower condenser water temperatures generally lead to higher efficiency. For example, raising the chilled water temperature by a few degrees can reduce the compressor’s workload and save energy. The load on the chiller also affects efficiency. Running a chiller at or near its full load is usually more efficient than at a very low part load. Additionally, the type of refrigerant used, the quality of the heat exchangers, and the control system of the chiller can all influence its energy consumption.
Optimizing Efficiency
To optimize the energy efficiency of a 200kW chiller, regular maintenance is essential. This includes cleaning the heat exchangers to remove any scale or dirt that may reduce heat transfer efficiency. Checking and adjusting the refrigerant charge is also important, as an improper charge can lead to increased energy consumption. Installing variable speed drives for the compressor and fans can allow the chiller to adjust its operation based on the actual cooling demand, reducing energy waste. Using an intelligent control system that can monitor and optimize the chiller’s performance in real-time can also significantly improve energy efficiency.
IV. Installation and Maintenance of 200kW Chillers
Installation
Installing a 200kW chiller requires careful planning and consideration. It needs to be placed in a suitable location with adequate space for ventilation, access for maintenance, and connection to the necessary pipes and electrical systems. The piping system for the chilled water and condenser water needs to be properly sized and installed to ensure proper flow and minimize pressure drops. Electrical connections should be made by qualified electricians to ensure safety and reliable operation. Additionally, the chiller may need to be calibrated and commissioned after installation to ensure that it is operating at its optimal performance.
Maintenance
Regular maintenance is crucial for the long-term performance of a 200kW chiller. This includes checking the refrigerant levels, oil levels in the compressor, and the condition of the heat exchangers. Cleaning or replacing the filters in the system is also important to prevent dirt and debris from entering the chiller and affecting its operation. Inspecting the electrical components for any signs of wear or damage and testing the control system regularly can help identify and address potential issues before they become major problems.
V. Cost Considerations of 200kW Chillers
Initial Cost
The initial cost of a 200kW chiller can vary depending on the type, brand, and features. Centrifugal chillers may generally be more expensive upfront compared to reciprocating chillers, while screw chillers fall somewhere in between. Additional costs may include installation, piping, and electrical work. The cost of the chiller itself also depends on factors such as the quality of the components, the efficiency rating, and any additional features like advanced control systems.
Operating Cost
The operating cost of a 200kW chiller mainly consists of energy consumption, maintenance, and potential repairs. Energy costs can be a significant portion of the operating expenses, especially if the chiller is running for long periods. As mentioned earlier, improving the energy efficiency of the chiller can help reduce these costs. Maintenance costs include regular inspections, part replacements, and servicing. By performing regular maintenance, the likelihood of major repairs can be reduced, but unexpected breakdowns can still occur, resulting in additional costs.
In conclusion, a 200kW chiller is a versatile and important piece of refrigeration equipment with a wide range of applications. Understanding its types, applications, energy efficiency, installation, maintenance, and cost aspects is essential for making informed decisions when selecting and operating such a chiller.
Related recommendations
water cooler system
402Introduction to Water Cooler Systems Water cooler systems are ubiquitous in offices, schools, and public spaces, offering a convenient source of cold drinking water. These systems chill and dis...
View detailssupplier chiller
331The Role of Chiller SuppliersChiller suppliers act as an intermediary between the chiller manufacturers and the end - users. They are responsible for sourcing a wide range of chillers from differe...
View detailsindustrial chilled water system
185What are Industrial Chilled Water Systems? Industrial chilled water systems are cooling systems designed to circulate chilled water through industrial processes or equipment to absorb and dissi...
View detailsportable chiller
117IntroductionIn the realm of cooling technology, portable chillers have emerged as a practical and flexible solution for a variety of cooling needs. Unlike traditional, large - scale chiller syste...
View details
HelloPlease log in