cooling coil chiller
Cooling Coil Chiller
A cooling coil chiller is an important component in many cooling systems, playing a crucial role in providing a comfortable environment in buildings or facilitating various industrial processes.
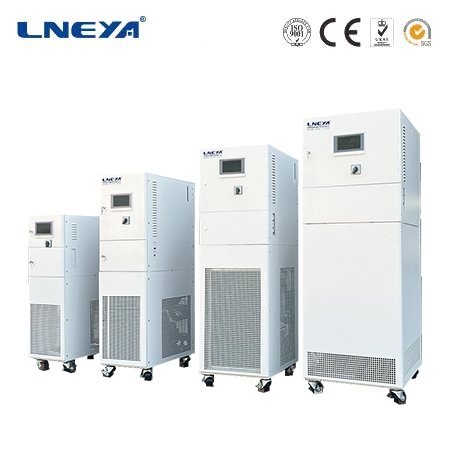
I. Definition and Components
Definition
A cooling coil chiller is a device that uses a cooling coil as a key element to transfer heat and cool the surrounding air or a fluid. The cooling coil is typically a heat exchanger that is part of a refrigeration cycle, where a refrigerant circulates to absorb heat from the medium that needs to be cooled.
Key Components
Cooling Coil: This is the primary component where the heat transfer occurs. It is usually made of a series of tubes with fins attached to increase the surface area for more efficient heat exchange. The coil can be made of materials like copper or aluminum, which have good thermal conductivity.
Compressor: The compressor is responsible for compressing the refrigerant, increasing its pressure and temperature. This is a crucial step in the refrigeration cycle as it enables the refrigerant to release heat when it reaches the condenser.
Refrigerant System: The refrigerant is the medium that circulates through the system, absorbing and releasing heat. Common refrigerants include R-410A, R-134a, etc. The refrigerant system also includes components like expansion valves and condensers. The expansion valve reduces the pressure of the refrigerant, causing it to cool down and turn into a low-pressure liquid-gas mixture before entering the cooling coil. The condenser is where the high-pressure, high-temperature refrigerant releases heat and condenses back into a liquid.
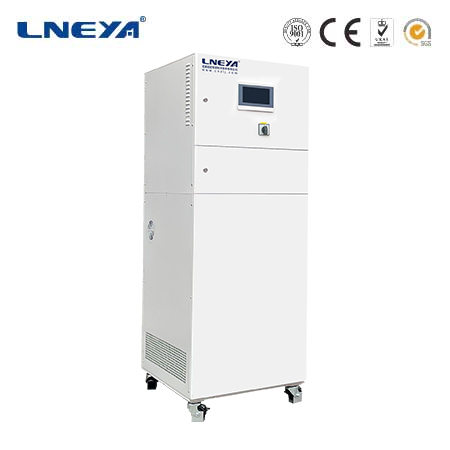
II. Working Principle
Refrigerant Cycle
The process starts with the compressor compressing the refrigerant, which raises its temperature and pressure. The hot, high-pressure refrigerant then flows to the condenser, where it releases heat to the surrounding environment (usually through air or water) and condenses into a liquid. After that, the liquid refrigerant passes through the expansion valve, which reduces its pressure and temperature, turning it into a low-pressure, cold liquid-gas mixture. This mixture then enters the cooling coil.
Heat Transfer in the Cooling Coil
When the cold refrigerant flows through the cooling coil, the air or fluid that passes over the coil transfers its heat to the refrigerant. As the refrigerant absorbs the heat, it starts to evaporate, turning back into a gas. The cooled air or fluid is then distributed to the desired area, while the now warm refrigerant gas returns to the compressor to start the cycle again.
III. Types of Cooling Coil Chillers
Direct Expansion (DX) Cooling Coil Chillers
In a direct expansion cooling coil chiller, the refrigerant flows directly through the cooling coil. The expansion valve is located just before the coil, and the refrigerant evaporates directly in the coil, absorbing heat from the air passing over it. DX chillers are often used in smaller applications, such as residential air conditioning systems or small commercial buildings. They are relatively simple in design and can provide efficient cooling for areas with relatively low cooling loads.
Chilled Water Cooling Coil Chillers
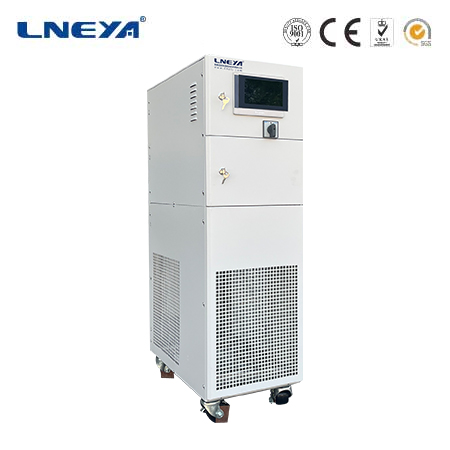
Chilled water cooling coil chillers use a secondary fluid, usually water, to transfer the cooling effect. The chiller first cools the water using a refrigeration cycle, and then the chilled water is pumped through the cooling coil. The air passing over the coil is cooled by the chilled water. These types of chillers are commonly used in larger commercial and industrial buildings, as well as in some industrial processes. They offer the advantage of being able to distribute the cooling effect over a larger area and can be more flexible in terms of system design.
IV. Applications
HVAC Systems in Buildings
Cooling coil chillers are widely used in heating, ventilation, and air conditioning (HVAC) systems in buildings. They help to cool the air that is circulated throughout the building, providing a comfortable indoor environment for occupants. In office buildings, for example, the cooling coil chiller cools the air in the air handling units, which then distribute the cooled air to different floors and rooms.
Industrial Processes
In various industrial processes, cooling coil chillers are used to cool equipment, products, or processes. For instance, in the food processing industry, they can be used to cool food products during production, storage, or packaging to maintain their quality and safety. In the electronics industry, they can cool electronic components to prevent overheating and ensure their proper operation.
Data Centers
Data centers generate a large amount of heat due to the operation of servers and other equipment. Cooling coil chillers play a vital role in cooling the air in data centers to keep the equipment at an optimal operating temperature. They help to prevent equipment failures and ensure the continuous operation of the data center.
V. Factors Influencing Performance
Coil Design and Construction
The design and construction of the cooling coil, such as the number of tubes, fin density, and coil material, can significantly affect its performance. A well-designed coil with a higher surface area and better heat transfer characteristics will be more efficient in cooling the air or fluid.
Refrigerant Type and Charge
The type of refrigerant used and its proper charge in the system are important factors. Different refrigerants have different properties, and an incorrect charge can lead to reduced cooling capacity, increased energy consumption, and potential damage to the chiller components.
Airflow or Fluid Flow Rate
The rate at which air or fluid passes over the cooling coil also impacts its performance. Adequate airflow or fluid flow is necessary to ensure that heat is effectively transferred from the medium to the refrigerant. If the flow rate is too low, the cooling efficiency will decrease.
VI. Maintenance Requirements
Coil Cleaning
Over time, the cooling coil can accumulate dirt, dust, and other contaminants, which can reduce its heat transfer efficiency. Regular cleaning of the coil, either by washing or using specialized cleaning agents, is essential to maintain its performance. This helps to ensure that the air or fluid is cooled effectively and that the chiller operates efficiently.
Refrigerant System Checks
Periodic checks of the refrigerant system are necessary to ensure that there are no leaks, the refrigerant charge is correct, and the components are functioning properly. Leaks in the refrigerant system can lead to a loss of cooling capacity and potential environmental issues if the refrigerant is a harmful substance.
Component Inspection and Replacement
Inspecting and replacing worn-out components, such as the compressor, expansion valve, or fan motors, is important for the long-term operation of the cooling coil chiller. Regular maintenance can help to identify potential problems early and prevent major breakdowns.
VII. Energy Efficiency
Efficient Coil Design
Using an efficient cooling coil design with good heat transfer properties can reduce the energy consumption of the chiller. Coils with optimized fin geometry and tube arrangements can transfer heat more effectively, requiring less energy to achieve the same cooling effect.
Variable Speed Drives
Installing variable speed drives for the compressor and fans can allow the chiller to adjust its operation based on the actual cooling demand. This helps to reduce energy waste when the cooling load is lower, as the components can operate at a lower speed instead of running at full capacity all the time.
Smart Control Systems
Implementing smart control systems that can monitor and optimize the chiller’s operation in real-time can improve energy efficiency. These systems can adjust the refrigerant flow, fan speed, and other parameters based on the current operating conditions to ensure that the chiller is operating at its most efficient point.
In conclusion, the cooling coil chiller is a vital component in many cooling systems, with diverse applications and various factors that influence its performance, maintenance, and energy efficiency. Understanding these aspects is crucial for ensuring the proper operation and optimal performance of the chiller in different settings.
Related recommendations
different type of chillers
372Different Types of Chillers: A Comprehensive Overview Chillers are indispensable in a variety of industries for cooling processes, air conditioning, and maintaining optimal temperatures for sen...
View detailsac glycol chiller
279All about AC Glycol ChillersAC glycol chillers are a specialized type of chiller system that uses a mixture of glycol and water as the heat - transfer fluid. This combination offers distinct advan...
View detailshigh temp controller
403High Temp Controller: Regulating Extreme Temperatures in Industrial Processes Introduction High temp controllers are specialized temperature control devices engineered to operate and maintai...
View detailswater cooled unit
173Water Cooled Unit: A Comprehensive GuideWater cooled units are crucial components in a wide array of industrial and commercial applications, primarily designed to facilitate efficient heat transf...
View details
HelloPlease log in