lab temperature controller
Lab Temperature Controllers: A Complete Guide
In a laboratory setting, maintaining a precise and stable temperature is often critical for the success of experiments. Lab temperature controllers are devices designed to achieve this goal. They play a vital role in a wide range of scientific disciplines, from chemistry and biology to materials science.
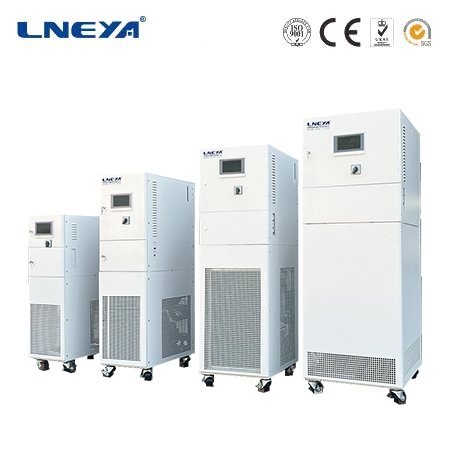
Types of Lab Temperature Controllers
Mechanical Temperature Controllers
Bimetallic Strip Thermostats: These are one of the simplest types of temperature controllers. A bimetallic strip consists of two different metals bonded together. Since the two metals have different coefficients of thermal expansion, when the temperature changes, the strip bends. In a lab – based application, this bending action can be used to open or close an electrical contact. For example, in a basic heating mantle used for simple chemical reactions, a bimetallic strip thermostat can be set to a certain temperature. If the temperature of the heating mantle rises above the set – point, the bimetallic strip bends and breaks the electrical connection, turning off the heating element. When the temperature drops below the set – point, the strip returns to its original position, closing the contact and restarting the heating process.
Advantages: They are relatively inexpensive and require no complex electronics. Their simple design makes them easy to understand and maintain. They are also reliable in basic applications where a general temperature range needs to be maintained.
Disadvantages: They lack high precision. The temperature differential between when the controller turns on and off (hysteresis) is relatively large, usually several degrees Celsius. This makes them less suitable for experiments that demand tight temperature control.
Electronic Temperature Controllers
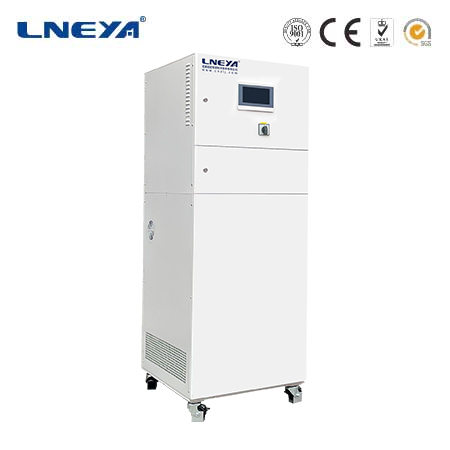
Proportional – Integral – Derivative (PID) Controllers: PID controllers are widely used in modern laboratories. They use an algorithm to calculate the appropriate output to the heating or cooling device based on the difference between the measured temperature and the set – point temperature. The proportional term responds to the current error, the integral term accumulates past errors over time, and the derivative term predicts future errors based on the rate of change of the error. For instance, in a chemical reactor where precise temperature control is crucial for a reaction to occur optimally, the PID controller can adjust the power to the heating or cooling elements very precisely. If the measured temperature is slightly below the set – point, the proportional term will increase the power output proportionally to the error. The integral term will gradually correct for any long – term deviations, and the derivative term will prevent over – shooting or under – shooting of the set – point.
Solid – State Relay – Based Controllers: Solid – state relays are electronic switches that can turn the heating or cooling element on or off based on a control signal from the temperature – sensing circuit. In a lab water bath, a solid – state relay can be used to control the power to the heating element. These relays can switch very quickly, allowing for more precise control of the average power delivered to the heater and thus better temperature regulation. They are also more reliable than mechanical relays as they have no moving parts.
Advantages: Electronic controllers offer high precision, often within a fraction of a degree Celsius. They can respond quickly to changes in temperature, making them suitable for experiments where rapid temperature adjustments are needed. They can also be integrated with other laboratory equipment and data – acquisition systems.
Disadvantages: They are more complex and expensive compared to mechanical controllers. They require a stable power supply and may be sensitive to electrical noise, which can affect their performance.
Programmable Temperature Controllers
Function and Operation: Programmable temperature controllers allow users to set complex temperature – time profiles. They are equipped with microprocessors and memory to store multiple temperature set – points and the time intervals for each set – point. In a materials annealing process in a materials science laboratory, for example, the programmable controller can be set to gradually increase the temperature to a specific value, hold it for a certain period, and then slowly decrease the temperature. This precise control over the heating and cooling rates is essential for achieving the desired material properties.
Advantages: They offer a high degree of flexibility, which is crucial for experiments that require specific temperature ramping, holding, and cooling cycles. They can be programmed to repeat the same temperature profile for multiple samples, ensuring consistency in experimental results.
Disadvantages: They are the most expensive type of temperature controllers. Programming them requires a certain level of technical knowledge, and any programming errors can lead to incorrect temperature profiles and potentially ruin experiments.
Applications of Lab Temperature Controllers
Chemical Laboratories
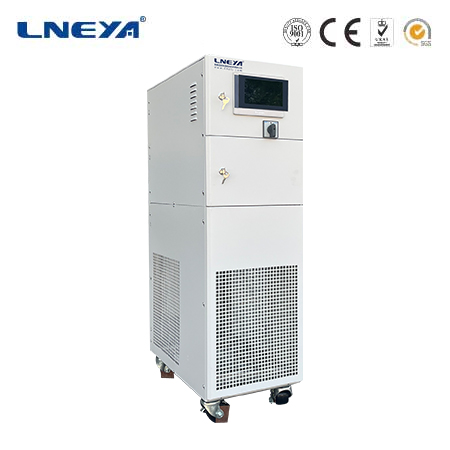
Organic Synthesis: In organic synthesis, many reactions are highly temperature – sensitive. For example, in the synthesis of pharmaceuticals, the reaction conditions need to be carefully controlled. A lab temperature controller can maintain the reaction mixture at the optimal temperature to promote the desired chemical reactions and minimize side reactions. If the temperature is too high, the reaction may proceed too quickly, leading to the formation of unwanted by – products. If the temperature is too low, the reaction may not occur at all or may be extremely slow.
Crystallization: Temperature control is crucial during crystallization processes. By carefully adjusting the temperature, chemists can control the rate of crystal growth. A lab temperature controller can be used to slowly lower the temperature of a supersaturated solution, allowing for the formation of high – quality crystals. These crystals can then be used for various purposes, such as X – ray diffraction studies to determine the molecular structure of compounds.
Biological Laboratories
Cell Culturing: In cell culture experiments, maintaining a constant temperature is essential for the survival and growth of cells. Most mammalian cells are cultured at around 37 °C, which is the normal body temperature of mammals. A lab temperature controller in a cell incubator ensures that the temperature remains within a very narrow range, typically ±0.1 °C. Any significant deviation from this temperature can affect cell metabolism, growth, and viability.
Enzyme Kinetics Studies: Enzymes are biological catalysts, and their activity is highly dependent on temperature. In enzyme kinetics experiments, a lab temperature controller is used to precisely control the temperature of the reaction mixture. By varying the temperature in a controlled manner, researchers can study how temperature affects the rate of enzyme – catalyzed reactions, which provides valuable insights into enzyme function and the underlying biochemical processes.
Materials Science Laboratories
Annealing and Tempering of Metals: In materials science, annealing and tempering are heat – treatment processes used to improve the mechanical properties of metals. A lab temperature controller is used to precisely control the heating and cooling rates during these processes. For example, during the annealing of steel, the temperature needs to be raised slowly to a specific value, held for a certain time, and then cooled at a controlled rate. This helps to relieve internal stresses, improve ductility, and refine the grain structure of the metal.
Polymer Processing: In the study of polymers, temperature control is important during processes such as polymerization and melt – processing. A lab temperature controller can be used to control the temperature of the polymerization reactor, ensuring that the polymerization reaction proceeds smoothly. During melt – processing, such as extrusion or injection molding of polymers, the temperature of the polymer melt needs to be precisely controlled to obtain the desired product properties.
Choosing the Right Lab Temperature Controller
Accuracy Requirements
The accuracy needed depends on the type of experiments. For example, in some high – precision biological experiments, such as studying the effects of minute temperature changes on cell signaling pathways, a temperature controller with an accuracy of ±0.01 °C may be required. In contrast, for basic chemical reactions where a general temperature range is sufficient, a controller with an accuracy of ±1 °C may be adequate.
Response Time
If the experiment involves rapid temperature changes, a temperature controller with a short response time is essential. For instance, in a flash – heating experiment where the temperature needs to be increased or decreased rapidly, a controller that can respond within seconds is required. PID – based electronic controllers generally have a faster response time compared to mechanical controllers.
Compatibility with Laboratory Equipment
The temperature controller should be compatible with the existing laboratory equipment. For example, if you are using a specific type of heating mantle or a custom – built reaction vessel, the controller should be able to interface with it properly. Some controllers may require specific types of sensors, so it’s important to ensure that the sensors are compatible with the equipment and the controller.
Budget Constraints
Mechanical temperature controllers are the most cost – effective, followed by electronic controllers, and programmable controllers are the most expensive. Depending on the frequency of use, the importance of precision, and the overall laboratory budget, a suitable controller needs to be selected. In some cases, a more expensive, high – precision controller may be a worthwhile investment if it is crucial for the success of important experiments.
Maintenance of Lab Temperature Controllers
Calibration
Regular calibration is essential to ensure the accuracy of the temperature controller. Calibration involves comparing the temperature readings of the controller with a known, accurate reference thermometer. If there is a deviation, the controller can be adjusted accordingly. The frequency of calibration depends on the usage of the controller and the accuracy requirements of the experiments. In general, it is recommended to calibrate the controller at least once every six months for high – precision applications.
Component Inspection
Periodically inspect the components of the temperature controller, such as the temperature sensors, relays, and wiring. Check for any signs of wear, corrosion, or damage. For example, if a temperature sensor is damaged, it may provide inaccurate temperature readings, leading to incorrect temperature control. Replace any faulty components immediately to ensure the proper functioning of the controller.
Software Updates (for Programmable Controllers)
If the temperature controller is programmable, it is important to keep the software up – to – date. Software updates may include bug fixes, improved control algorithms, and additional features. Manufacturers often release updates to improve the performance and reliability of their products. Check the manufacturer’s website regularly for available updates and follow the instructions for installation.
In conclusion, lab temperature controllers are indispensable tools in modern laboratories. By understanding the different types, applications, selection criteria, and maintenance requirements, laboratory personnel can choose and use the right temperature controller to ensure the success of their experiments.
Related recommendations
ethylene glycol for chillers
266Ethylene Glycol for Chillers: Enhancing Industrial Cooling Efficiency Ethylene glycol (EG) plays a vital role in chiller systems, especially in industrial processes and large-scale commercial b...
View detailsindustrial water chiller malaysia
236Industrial Water Chillers in Malaysia: An In - Depth ExplorationIndustrial water chillers are essential cooling equipment in Malaysia's industrial landscape, playing a significant role in maintain...
View detailswater recirculation cooler
381Introduction to Water Recirculation CoolersWater recirculation coolers are essential in maintaining a stable temperature in various industrial and laboratory processes. These systems work by circu...
View detailsdc air conditioning
299DC Air Conditioning: Technology, Efficiency, and Applications DC air conditioning systems are integral to maintaining comfortable and efficient environments in various applications, from reside...
View details
HelloPlease log in