thermal oil heating system
Thermal Oil Heating Systems: A Comprehensive Overview
I. Introduction
A thermal oil heating system is a closed – loop system that utilizes thermal oil (also known as heat – transfer oil) as the medium to transfer heat from a heat source to various processes. This type of heating system has become increasingly popular in industrial applications due to its ability to provide efficient and reliable heat transfer over a wide temperature range.
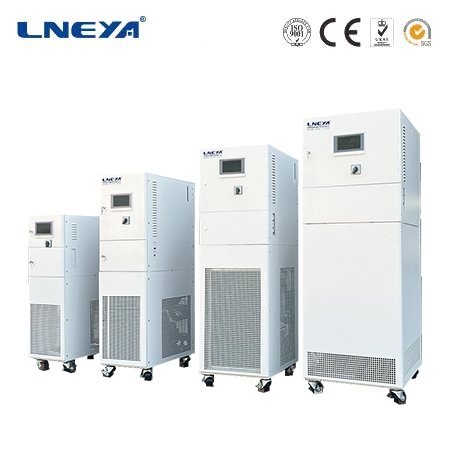
II. Components of a Thermal Oil Heating System
Heater
The heater is the heart of the thermal oil heating system. There are different types of heaters, such as electric heaters and fired heaters. Electric heaters use resistance elements to convert electrical energy into heat. They are relatively easy to control and are suitable for applications where precise temperature control is required. Fired heaters, on the other hand, burn fuels like natural gas, oil, or coal. They can generate large amounts of heat and are often used in large – scale industrial processes. The heater heats the thermal oil to the desired temperature, which is then circulated throughout the system.
Pump
A pump is used to circulate the thermal oil within the closed – loop system. The pump ensures a continuous flow of the heated oil from the heater to the process equipment and then back to the heater for reheating. The selection of the pump depends on factors such as the required flow rate, the viscosity of the thermal oil, and the pressure drop in the system. Centrifugal pumps are commonly used in thermal oil heating systems due to their ability to handle high – volume flows and their relatively simple design.
Expansion Tank
An expansion tank is an essential component of the thermal oil heating system. As the thermal oil is heated, it expands. The expansion tank provides a space for the oil to expand without causing excessive pressure in the system. It also helps to maintain a constant pressure in the system and can be used to top – up the oil level when necessary. The expansion tank is typically connected to the system at a low – pressure point and is designed to withstand the maximum operating temperature and pressure of the system.
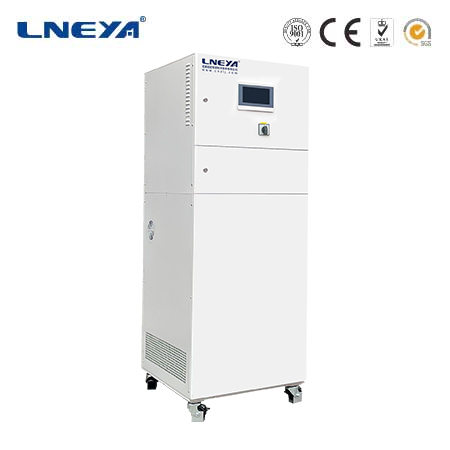
Heat Exchangers
Heat exchangers are used to transfer the heat from the thermal oil to the process fluid or equipment. There are various types of heat exchangers, such as shell – and – tube heat exchangers and plate – type heat exchangers. In a shell – and – tube heat exchanger, the thermal oil flows through the tubes, while the process fluid flows around the tubes in the shell. The heat is transferred through the tube walls. Plate – type heat exchangers consist of a series of plates with channels for the thermal oil and the process fluid. The close proximity of the plates allows for efficient heat transfer.
III. Working Principle
The working principle of a thermal oil heating system is based on the circulation of the thermal oil. First, the thermal oil is heated in the heater to the desired temperature. The heated oil then enters the pump, which forces it through the pipelines and into the heat exchangers. In the heat exchangers, the heat from the thermal oil is transferred to the process fluid or equipment. As the thermal oil gives up its heat, its temperature drops. The cooled oil then returns to the heater, where it is reheated, and the cycle continues. The entire system is designed to be a closed – loop, which helps to prevent contamination of the thermal oil and ensures efficient heat transfer.
IV. Applications
Chemical Industry
In the chemical industry, thermal oil heating systems are widely used. For example, in polymerization processes, a consistent and precise temperature is required to ensure the proper formation of polymers. Thermal oil heating systems can provide the necessary heat to maintain the reaction temperature within a narrow range. They are also used in distillation processes, where they heat the mixture to be distilled, separating the different components based on their boiling points.
Food Industry
In the food industry, thermal oil heating systems are used in various applications. In baking processes, they can provide a uniform heat source for ovens, ensuring that the food is baked evenly. They are also used in food processing equipment such as kettles for cooking, where the thermal oil heats the kettle walls, transferring heat to the food inside. In the production of chocolate, thermal oil heating systems are used to maintain the correct temperature for melting and tempering the chocolate.
Textile Industry
In the textile industry, thermal oil heating systems play a crucial role. They are used in dyeing processes, where they heat the dye bath to the required temperature. The accurate temperature control provided by these systems ensures consistent coloration of the textiles. Thermal oil heating systems are also used in the drying of textiles, where they provide the heat needed to evaporate the moisture from the fabric.
Plastics Industry
In the plastics industry, thermal oil heating systems are used for heating plastic molds. The uniform heat distribution provided by the thermal oil helps to ensure that the plastic melts evenly and fills the mold properly. This results in high – quality plastic products with consistent dimensions and properties. They are also used in plastic extrusion processes, where the thermal oil heats the plastic material to the appropriate temperature for extrusion through a die.
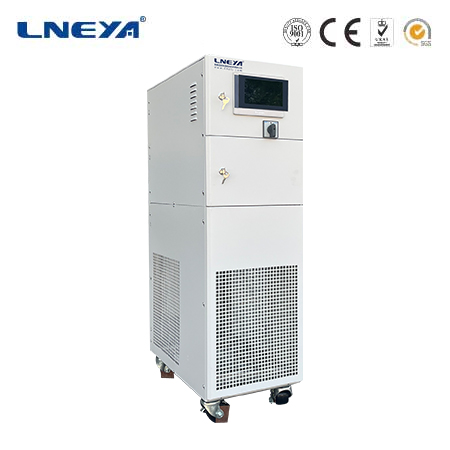
V. Advantages of Thermal Oil Heating Systems
High – Temperature Capability
Thermal oil heating systems can operate at high temperatures, often up to 300 – 400°C. This makes them suitable for applications that require high – temperature processing, such as in some chemical reactions and high – temperature drying processes. Unlike steam heating systems, which are limited by the saturation temperature of steam at a given pressure, thermal oil can be heated to much higher temperatures without the need for extremely high pressures.
Energy – Efficiency
These systems are relatively energy – efficient. The closed – loop design reduces heat losses, and the high heat – carrying capacity of thermal oil allows for the transfer of large amounts of heat with a relatively small volume of the medium. Also, the ability to operate at lower pressures compared to some other heating systems means that less energy is required to maintain the system’s operation.
Precise Temperature Control
Thermal oil heating systems can provide very precise temperature control. The use of advanced control systems, such as proportional – integral – derivative (PID) controllers, allows for accurate regulation of the heater’s output, ensuring that the temperature of the thermal oil and, consequently, the process temperature remains within a tight tolerance. This is crucial for applications where even a slight temperature variation can affect the quality of the product.
Versatility
They are highly versatile and can be used in a wide range of industries and applications. The same basic system can be adapted to different temperature requirements, flow rates, and process needs by adjusting the components such as the heater size, pump capacity, and heat exchanger design.
VI. Maintenance and Safety Considerations
Maintenance
Regular maintenance is essential for the proper operation of a thermal oil heating system. This includes checking the oil level in the expansion tank and topping it up if necessary. The oil should also be periodically tested for its quality, such as its viscosity and acid number. If the oil has degraded, it may need to be replaced. The heaters, pumps, and heat exchangers should be inspected for any signs of wear, leaks, or blockages. Filters in the system should be cleaned or replaced regularly to prevent contaminants from entering the system.
Safety Considerations
Thermal oil is flammable, so safety is a major concern. The system should be installed in a well – ventilated area away from sources of ignition. Overheating protection devices should be installed to prevent the thermal oil from reaching dangerous temperatures. Pressure relief valves are also crucial to prevent over – pressurization of the system. Operators should be trained on the proper operation and safety procedures of the system to minimize the risk of accidents.
VII. Factors to Consider When Choosing a Thermal Oil Heating System
Temperature Range
The required temperature range for the application is a primary consideration. Different processes have different temperature requirements, and the thermal oil heating system should be able to meet these requirements accurately. If the process requires a high – temperature operation, the system should be designed to handle the maximum temperature without degradation of the components or the thermal oil.
Capacity
The capacity of the system, which is related to the amount of heat it can deliver, should be sufficient for the process. This depends on factors such as the size of the process equipment, the heat – load requirements, and the desired heating rate. An undersized system may not be able to provide enough heat, while an oversized system may be inefficient and costly.
Type of Thermal Oil
There are different types of thermal oils available, each with its own properties such as thermal stability, viscosity, and flash point. The choice of thermal oil should be based on the operating temperature range, the compatibility with the system components, and the specific requirements of the application. For example, in high – temperature applications, a thermal oil with high thermal stability is required.
Cost
The initial cost of the system, including the purchase of the heater, pump, expansion tank, heat exchangers, and installation, as well as the ongoing operating and maintenance costs, should be considered. Energy – efficient systems may have a higher initial cost but can result in lower operating costs over time.
In conclusion, thermal oil heating systems are an important and versatile heating solution in many industries. Their proper understanding, selection, operation, and maintenance are crucial for ensuring efficient and safe heat transfer in various industrial processes.
Related recommendations
efficient chillers
462The Importance of Efficient Chiller Operation Efficient chiller operation is critical in the context of increasing energy costs and environmental concerns. Chillers are responsible for a signif...
View detailsWhat should I do if the temperature difference between the inlet and outlet of the water cooled industrial chiller is small?
938What should I do if the temperature difference between the inlet and outlet of the water cooled industrial chiller is small? Technicians stated that when users use water-cooled chillers...
View detailsWhat details should be paid attention to in the daily maintenance and upkeep of industrial air cooled chiller?
933What details should be paid attention to in the daily maintenance and upkeep of industrial air cooled chiller? 1. When starting an air-cooled industrial chiller unit, it should be check...
View detailsHow to select pipelines in industrial chiller systems?
879How to select pipelines in industrial chiller systems? The development of a refrigeration system includes selecting the sizes of various pipelines and valves in the system, and developi...
View details
HelloPlease log in