industrial process heating systems
What are Industrial Process Heating Systems?
Industrial process heating systems are specialized systems designed to provide controlled heat for various industrial processes. They are essential in maintaining the temperature stability required for manufacturing, processing, and other industrial operations, ensuring product quality, and optimizing production efficiency. These systems can use various heat sources, including electricity, gas, steam, and thermal fluids, to deliver precise and consistent heat.
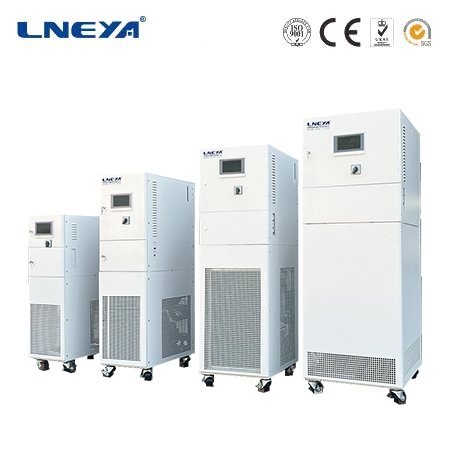
Types of Industrial Process Heating Systems
Electric Heating Systems: These systems use electric resistance, induction, or infrared heating to generate heat. They are known for their precision and ease of control.
Gas Heating Systems: These systems use natural gas or propane as the heat source. They are cost-effective and widely used in applications requiring high temperatures.
Steam Heating Systems: These systems use steam generated from boilers to provide heat. They are commonly used in industries where steam is already available as a byproduct.
Thermal Fluid Heating Systems: These systems use a heat transfer fluid (e.g., thermal oil) to circulate heat through the system. They are ideal for applications requiring uniform heat distribution.
Combustion Heating Systems: These systems burn fuels (e.g., oil, coal) to generate heat. They are used in applications requiring very high temperatures.
Working Principles of Industrial Process Heating Systems
Industrial process heating systems operate on the basic principle of heat generation and transfer. The process involves the following steps:
Heat Generation: The heat source (e.g., electric element, gas burner) generates heat.
Heat Transfer: The heat is transferred to the process or material through conduction, convection, or radiation.
Temperature Control: The system maintains the desired temperature using sensors, controllers, and feedback mechanisms.
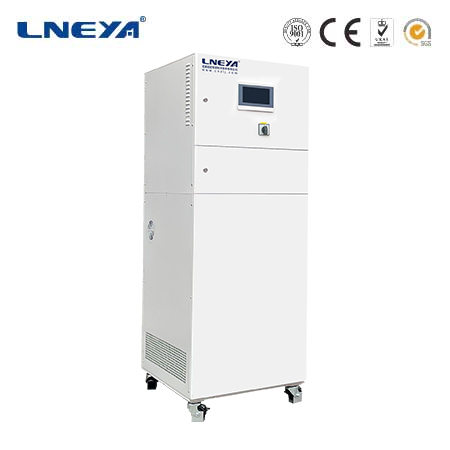
Applications of Industrial Process Heating Systems
Industrial process heating systems are used in a wide range of industries and applications, including:
Chemical Processing: Heating is essential in chemical reactions, distillation, and drying processes to ensure product quality and optimize reaction rates.
Food Production: Heating is used in cooking, pasteurization, and sterilization processes to ensure food safety and quality.
Metalworking: Heating is required in processes such as forging, annealing, and heat treatment to alter material properties and improve product performance.
Pharmaceuticals: Precise temperature control is critical in drug formulation, drying, and sterilization processes to maintain product efficacy and compliance with regulatory standards.
Plastics and Rubber: Heating is used in molding, extrusion, and vulcanization processes to shape and cure materials.
Benefits of Industrial Process Heating Systems
Precise Temperature Control: Industrial process heating systems offer excellent temperature stability, which is crucial for processes that require consistent heat.
Energy Efficiency: Modern heating systems are designed to be energy-efficient, reducing operational costs and environmental impact.
Versatility: These systems can be used in a wide range of applications, making them a versatile heating solution.
Durability: High-quality heating systems are built to withstand harsh industrial environments, ensuring long-term reliability.
Environmental Impact: Many heating systems use environmentally friendly technologies, reducing their impact on the environment.
Factors to Consider When Selecting an Industrial Process Heating System
Heat Source: Choose the appropriate heat source (e.g., electric, gas, steam) based on the specific requirements of your application.
Energy Efficiency: Design the system to minimize energy consumption, considering factors such as heat loss, insulation, and system design.
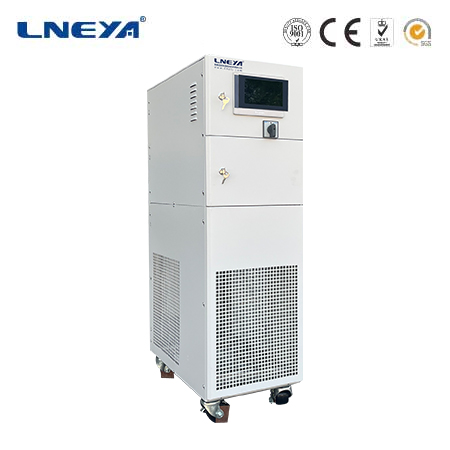
Temperature Range: Ensure the system can achieve and maintain the required temperature range for your process.
System Design: Consider the layout and design of the system, including heat distribution, control mechanisms, and safety features.
Maintenance Requirements: Design the system for ease of maintenance, including access to components, availability of spare parts, and the use of durable materials.
Cost: Consider the initial investment cost as well as long-term operational and maintenance costs.
Maintenance Tips for Industrial Process Heating Systems
Regular Inspections: Conduct regular inspections of the system’s components to identify and address any issues early.
Clean Heat Exchangers: Regularly clean heat exchangers to ensure efficient heat transfer.
Monitor System Performance: Continuously monitor system performance, including temperature, pressure, and flow rate, to detect any deviations from normal operation.
Lubricate Moving Parts: Regularly lubricate the system’s moving parts to reduce wear and tear.
Check Insulation: Ensure that insulation is intact and effective to minimize heat loss.
Schedule Professional Maintenance: Have a professional technician perform routine maintenance to ensure optimal performance.
Conclusion
Industrial process heating systems are indispensable in maintaining the temperature stability required for various industrial processes. By understanding their types, working principles, applications, and benefits, businesses can make informed decisions when selecting a heating system for their specific needs. Regular maintenance and proper operation are essential to ensure the system’s long-term reliability and performance. Whether you’re in chemical processing, food production, metalworking, or pharmaceuticals, a well-designed and maintained industrial process heating system can provide the precise and consistent heat you need to enhance operational efficiency, reduce costs, and ensure sustainability.
Related recommendations
small heating and cooling units
141Small Heating and Cooling Units: A Complete GuideIn modern living and working environments, the demand for compact and efficient thermal management solutions has grown significantly. Small heatin...
View detailschilling unit operation
79Chilling Unit Operation: A Definitive GuideIn the domain of thermal management, chilling units serve as the cornerstone for maintaining optimal temperatures in a plethora of settings, ranging fro...
View detailscompact cooling system
169Compact Cooling System: A Comprehensive ExplorationIn today's world, where space is at a premium in many applications, compact cooling systems have emerged as a crucial solution for maintaining op...
View detailsheating and cooling controller
366Heating and Cooling Controllers: Regulating Temperature for Comfort and Efficiency Heating and cooling controllers are integral components of heating, ventilation, and air conditioning (HVAC) s...
View details
HelloPlease log in