temperature control unit
Introduction
Temperature control is a crucial aspect in numerous fields, from industrial manufacturing and scientific research to everyday comfort in homes and commercial buildings. Temperature control units (TCUs) serve as the backbone of systems that require accurate and consistent temperature regulation. These units are designed to monitor, adjust, and maintain temperature within a specified range, ensuring optimal performance of processes, preservation of materials, and comfort for occupants. This article will offer a comprehensive overview of temperature control units, covering their basic concepts, working mechanisms, types, applications, and best practices for implementation.
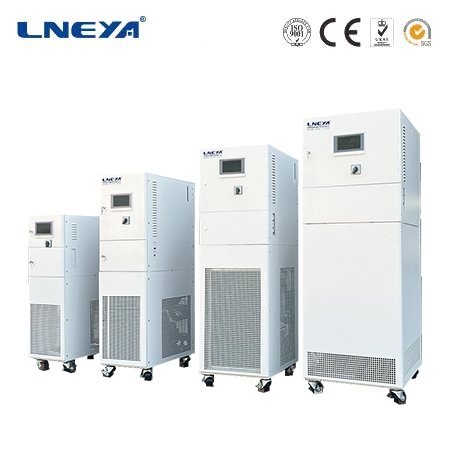
What is a Temperature Control Unit?
A temperature control unit is an automated system that measures the temperature of a specific environment, process, or object and adjusts it to a desired setpoint. It acts as the central nervous system for temperature – sensitive operations, continuously monitoring the temperature and making real – time adjustments as needed. TCUs can be stand – alone devices or integrated into larger control systems, and they vary in complexity, from simple units used for basic temperature regulation to highly sophisticated systems capable of handling complex thermal processes with extreme precision.
Working Principles of Temperature Control Units
The operation of a temperature control unit is based on a feedback control loop, which involves three main steps: sensing, processing, and actuation.
Sensing: The process starts with temperature sensors, which are the eyes of the TCU. These sensors, such as thermocouples, resistance temperature detectors (RTDs), or thermistors, are strategically placed in the area or on the object whose temperature needs to be controlled. They convert the thermal energy into an electrical signal, which is then transmitted to the controller. For example, in a chemical reactor, an RTD might be inserted into the reaction mixture to accurately measure its temperature.
Processing: The controller is the brain of the TCU. It receives the electrical signal from the temperature sensor, converts it into an actual temperature reading, and compares it with the pre – set desired temperature (setpoint). Based on the difference between the measured temperature and the setpoint (the error), the controller uses specific algorithms to calculate the appropriate control action. The most common control algorithm is the Proportional – Integral – Derivative (PID) control, which adjusts the output based on the current error, the accumulated error over time, and the rate of change of the error.
Actuation: Once the controller determines the necessary control action, it sends a signal to the actuator. Actuators can be heating elements, cooling devices (such as fans, chillers, or refrigeration units), or dampers in HVAC systems. For instance, if the measured temperature is lower than the setpoint, the controller will signal the heating element to turn on and increase the temperature. Conversely, if the temperature is too high, it will activate the cooling device to reduce the temperature. This continuous cycle of sensing, processing, and actuation ensures that the temperature remains as close as possible to the desired setpoint.
Components of a Temperature Control Unit
Temperature Sensors
Thermocouples: These are composed of two different metal wires joined at one end. When there is a temperature difference between the joined end (the hot junction) and the other end (the cold junction), a small voltage is generated, known as the Seebeck effect. Thermocouples are widely used due to their wide temperature range (from -200°C to over 2000°C), fast response time, and durability. They are commonly found in industrial furnaces, power plants, and automotive engines.
Resistance Temperature Detectors (RTDs): RTDs operate on the principle that the electrical resistance of a metal (usually platinum, nickel, or copper) changes with temperature. They offer high accuracy and stability, making them suitable for applications that require precise temperature measurement, such as in laboratories, pharmaceutical manufacturing, and semiconductor processing.
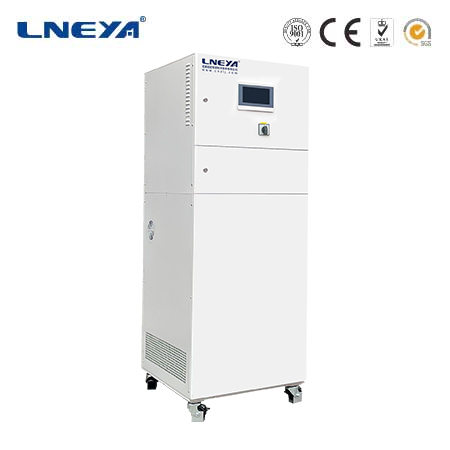
Thermistors: Thermistors are semiconductor – based temperature sensors with a high sensitivity to temperature changes. They have a large change in resistance for a small change in temperature, but their temperature range is generally more limited compared to thermocouples and RTDs. Thermistors are often used in consumer electronics, HVAC systems, and some automotive applications for quick and cost – effective temperature sensing.
Controllers
PID Controllers: As mentioned earlier, PID controllers are the most prevalent type in temperature control units. They calculate the control output by combining three components: the proportional term, which reacts to the current error; the integral term, which eliminates steady – state error over time; and the derivative term, which anticipates future errors based on the rate of change of the error. PID controllers can be tuned to achieve optimal performance for different applications, balancing factors like response time, stability, and accuracy.
Programmable Logic Controllers (PLCs): PLCs are more advanced controllers that can be programmed to perform a wide variety of control functions, including temperature control. They are often used in industrial automation settings where multiple processes need to be coordinated. PLC – based temperature control units can handle complex control strategies, communicate with other devices in the network, and store and analyze data for process optimization.
Microcontroller – Based Controllers: These controllers use microchips to execute control algorithms. They are highly flexible and can be customized for specific applications. Microcontroller – based TCUs are commonly found in consumer products, small – scale industrial processes, and research equipment, where cost – effectiveness and compact size are important factors.
Actuators
Heating Elements: Heating elements come in various forms, such as electric resistance heaters, infrared heaters, and gas – fired burners. Electric resistance heaters work by passing an electric current through a resistive material, which generates heat. They are widely used in applications like ovens, water heaters, and industrial drying processes. Infrared heaters emit infrared radiation, which directly heats objects without heating the intervening air, making them suitable for applications where rapid heating is required.
Cooling Devices: Cooling actuators include fans, air conditioners, chillers, and refrigeration units. Fans work by increasing air circulation, which helps dissipate heat. Air conditioners and chillers use the vapor – compression cycle to remove heat from the environment and transfer it elsewhere. Refrigeration units are commonly used in cold storage facilities, laboratories, and food processing plants to maintain low temperatures.
Dampers and Valves: In HVAC systems, dampers and valves are used to control the flow of air or coolant. Dampers adjust the amount of air flowing through ducts, while valves regulate the flow of liquids (such as water or coolant) in cooling or heating systems. By controlling the flow, these actuators help maintain the desired temperature in the building.
Types of Temperature Control Units
PID – Based Temperature Control Units
PID – based TCUs are the workhorses of temperature control. They are suitable for a wide range of applications, from simple home appliances to complex industrial processes. Their ability to fine – tune the control output based on the proportional, integral, and derivative terms makes them highly effective in achieving and maintaining a stable temperature. For example, in a plastic injection molding machine, a PID – based TCU can precisely control the temperature of the mold, ensuring consistent product quality.
Programmable Temperature Control Units
Programmable TCUs offer greater flexibility as they can be configured to follow specific temperature profiles over time. They are commonly used in processes that require a sequence of temperature changes, such as in heat treatment of metals, where the material needs to be heated, held at a certain temperature for a period, and then cooled in a controlled manner. These units can be programmed via a user interface, and they often have memory capabilities to store multiple temperature profiles for different applications.
Smart Temperature Control Units
With the advent of the Internet of Things (IoT) and advanced sensor technologies, smart TCUs have emerged. These units are equipped with connectivity features, allowing them to communicate with other devices and systems over a network. They can be remotely monitored and controlled, and they often incorporate artificial intelligence and machine learning algorithms to optimize temperature control. For instance, a smart TCU in a commercial building can analyze occupancy patterns, weather data, and energy consumption to adjust the temperature in an energy – efficient and comfortable manner.
Applications of Temperature Control Units
Industrial Applications
Pharmaceutical Industry: In pharmaceutical manufacturing, precise temperature control is critical for the production of drugs and vaccines. TCUs are used to control the temperature of reactors during chemical synthesis, drying ovens for powder processing, and cold storage facilities for storing temperature – sensitive products. Even a slight deviation from the required temperature can affect the chemical reactions, product quality, and stability of the medications.
Food Processing: The food industry relies on TCUs to ensure food safety and quality. Temperature control is essential during processes like cooking, baking, freezing, and refrigeration. For example, in a meat processing plant, TCUs control the temperature of refrigerated storage rooms to prevent spoilage, and they regulate the cooking temperature of ovens to achieve the desired texture and taste of the products.
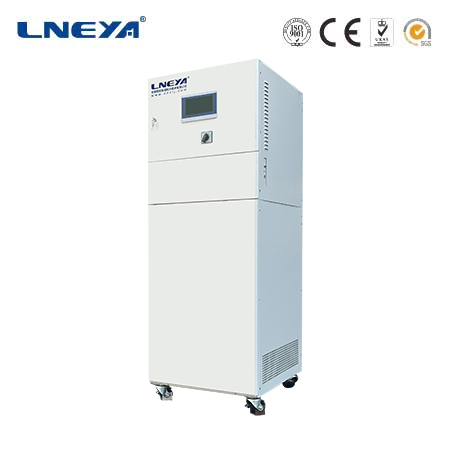
Electronics Manufacturing: In the production of electronic components, such as semiconductors, TCUs play a vital role. The manufacturing processes involve precise temperature control during operations like chip fabrication, soldering, and reflow soldering. Any temperature variation can lead to defects in the components, affecting their performance and reliability.
Scientific Research
In laboratories, TCUs are used in a variety of experiments. For example, in biological research, they maintain the temperature of incubators to support cell growth. In materials science, TCUs control the temperature during material synthesis and characterization, allowing researchers to study the properties of materials under different thermal conditions. They are also used in calorimetry experiments to accurately measure heat changes.
HVAC Systems
Heating, Ventilation, and Air Conditioning (HVAC) systems in residential, commercial, and industrial buildings rely on TCUs to provide comfortable indoor environments. TCUs control the temperature of heating and cooling equipment, adjust the airflow through ducts, and manage the overall climate control. They can be programmed to maintain different temperature settings at different times of the day, improving energy efficiency and occupant comfort.
Considerations When Selecting a Temperature Control Unit
Temperature Range and Accuracy Requirements
The first step in selecting a TCU is to determine the required temperature range and accuracy for the application. Different processes and applications have varying temperature needs. For example, a laboratory experiment may require a temperature control unit that can maintain a temperature within ±0.1°C, while a simple room heating system may tolerate a deviation of ±1°C. Ensure that the chosen TCU can operate within the required temperature range and meet the accuracy specifications.
Type of Sensor Compatibility
Since the temperature sensor is a crucial part of the TCU, it’s important to choose a unit that is compatible with the type of sensor you plan to use. Some TCUs are designed to work specifically with certain sensors, such as only accepting thermocouple inputs or only being compatible with RTDs. Make sure the TCU can interface with the sensor and accurately interpret the sensor’s output signal.
Control Algorithm and Flexibility
Consider the control algorithm of the TCU. PID controllers are suitable for many applications, but for more complex processes, you may need a programmable or smart TCU with advanced control capabilities. Also, look for a unit that offers flexibility in terms of programming, configuration, and the ability to adapt to changing process requirements.
Connectivity and Communication Features
If you need to integrate the TCU with other systems, such as a building management system or a process control network, choose a unit with appropriate connectivity options. Ethernet, Wi – Fi, and industrial communication protocols like Modbus or Profibus are common features in modern TCUs. These features enable remote monitoring, control, and data logging, which can be valuable for process optimization and troubleshooting.
Cost and Maintenance
Finally, consider the initial cost of the TCU, as well as the long – term maintenance costs. More advanced TCUs with additional features may be more expensive, but they could also offer better performance and efficiency. Look for units that are easy to maintain, with accessible components and clear user manuals. Some TCUs may require regular calibration of the sensors and controllers, so factor in the associated costs and effort.
Installation, Operation, and Maintenance of Temperature Control Units
Installation
Proper installation of a TCU is essential for its optimal performance. Follow the manufacturer’s installation instructions carefully, which typically include steps for wiring the sensors, controllers, and actuators. Ensure that the sensors are placed in the correct location to accurately measure the temperature. For example, in a large room, multiple sensors may be required to get an average temperature reading. Connect the controller to a stable power source and any necessary communication networks. For actuators, make sure they are properly installed and connected to the controller, and that they can operate freely without any obstructions.
Operation
Once installed, familiarize yourself with the TCU’s user interface and operating instructions. Set the desired temperature setpoint and configure any additional parameters, such as the control algorithm settings (if applicable). Regularly monitor the temperature readings and the performance of the TCU. Some TCUs may have diagnostic features that can alert you to any issues, such as sensor malfunctions or control errors. If adjustments are needed, make them carefully and monitor the system’s response to ensure that the temperature remains stable.
Maintenance
Regular maintenance is crucial to keep the TCU in good working condition. Periodically check the sensors for accuracy by comparing their readings with a calibrated reference thermometer. Clean or replace the sensors as recommended by the manufacturer to prevent dirt or debris from affecting their performance. For the controller, check the electrical connections, update the firmware if available, and ensure that the control algorithms are still providing optimal performance. Inspect the actuators for any signs of wear or damage, lubricate moving parts if necessary, and replace any faulty components promptly.
Future Trends in Temperature Control Units
Integration with IoT and Smart Systems
The integration of TCUs with the Internet of Things will continue to grow. This will enable more advanced features, such as real – time remote monitoring and control from mobile devices, predictive maintenance based on data analytics, and seamless integration with other smart building systems. For example, a TCU in a smart home could communicate with other smart devices, like smart thermostats, lights, and security systems, to create a more energy – efficient and comfortable living environment.
Enhanced Energy – Efficiency Features
As energy costs rise and environmental concerns increase, there will be a greater focus on developing TCUs with enhanced energy – efficiency features. This may include more efficient heating and cooling elements, intelligent control algorithms that optimize energy consumption based on real – time conditions, and the use of renewable energy sources for powering the TCUs. For instance, a TCU could be designed to use solar power during the day to reduce its reliance on the grid.
Miniaturization and Microfabrication
With the advancements in microfabrication technology, temperature control units are likely to become smaller and more compact. Miniature TCUs could be integrated directly into small devices, such as wearable electronics, medical implants, and microfluidic chips. These miniaturized units will require less power and space while still providing accurate temperature control.
Conclusion
Temperature control units are indispensable for maintaining precise thermal conditions in a vast array of applications. Understanding their working principles, components, types, and applications is crucial for selecting the right TCU for a specific task. By following proper installation, operation, and maintenance practices, users can ensure the reliable and efficient performance of these units. As technology continues to evolve, temperature control units will become more intelligent, energy – efficient, and versatile, further expanding their applications and impact in various industries and everyday life.
Related recommendations
usa labs chiller
257Introduction to USA Labs ChillersIn the United States, laboratory chillers play a crucial role in maintaining the optimal temperature conditions for a wide range of scientific experiments and proc...
View details40 ton water cooled chiller
128IntroductionIn the domain of cooling systems, 40 - ton water cooled chillers play a vital role in meeting the significant cooling demands of various mid - to - large - scale applications. With a ...
View detailswater source chiller
89Working Principles of Water Source ChillersThe fundamental operation of water source chillers is grounded in the vapor - compression refrigeration cycle, which involves four essential components:...
View detailsfactory chiller
117IntroductionIn the realm of industrial operations, factory chillers play a pivotal role in ensuring smooth production processes and maintaining the integrity of equipment and products. A factory ...
View details
HelloPlease log in