small chiller
Introduction
Small chillers have carved out a niche in the cooling technology landscape, offering targeted solutions for applications that demand efficient cooling within a limited scale. These compact cooling units are designed to handle low – to – medium cooling loads, making them suitable for a variety of settings where large, traditional chillers would be oversized and inefficient. Whether it’s maintaining the ideal temperature in a small office, cooling specialized equipment in a laboratory, or supporting small – scale industrial processes, small chillers play a crucial role. This article will provide a comprehensive overview of small chillers, exploring their characteristics, working mechanisms, types, applications, and more.
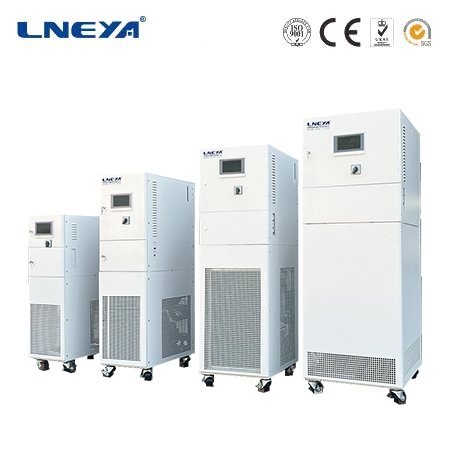
Definition and Key Characteristics
A small chiller is a refrigeration system that is designed with a relatively low cooling capacity, typically ranging from a fraction of a ton to around 20 – 30 tons of refrigeration (where 1 ton of refrigeration is equivalent to 12,000 BTU per hour). These chillers are characterized by their compact size, which allows them to fit into spaces with limited room, such as utility closets, small mechanical rooms, or even under benches in some cases.
One of the main features of small chillers is their energy – efficient operation. Many models are equipped with advanced components and control systems that optimize energy consumption based on the actual cooling demand. They often have variable – speed compressors or fans, enabling them to adjust their output and reduce energy waste when the cooling load is lower. Additionally, small chillers are generally easier to install and maintain compared to their larger counterparts, as they require less complex infrastructure and fewer specialized skills for routine upkeep.
Working Principles
The working principles of small chillers are based on the same fundamental refrigeration cycles as larger chillers, primarily the vapor – compression cycle. Here’s a detailed look at how it functions in the context of a small chiller:
Compression: The cycle initiates with the compressor. In a small chiller, the compressor draws in low – pressure, low – temperature refrigerant vapor. It then compresses this vapor, increasing its pressure and temperature significantly. This high – pressure, high – temperature refrigerant gas is then pushed towards the condenser. The compressor in small chillers is often designed to be compact yet efficient, using technologies like scroll compressors or small reciprocating compressors to achieve the necessary compression ratios.
Condensation: The compressed refrigerant gas enters the condenser. In air – cooled small chillers, fans blow air over the condenser coils, facilitating the transfer of heat from the refrigerant to the surrounding air. As the refrigerant releases heat, it condenses into a high – pressure liquid. In water – cooled small chillers, the refrigerant transfers its heat to a flowing water stream, which carries the heat away to a cooling tower or other heat rejection device. The condenser in small chillers is engineered to maximize heat transfer in a limited space, often with finned – tube designs or compact plate – type heat exchangers.
Expansion: The high – pressure liquid refrigerant then passes through an expansion valve. This valve restricts the flow of the refrigerant, causing a sudden drop in pressure. As the pressure decreases, the refrigerant expands and cools down, transforming into a low – pressure, low – temperature mixture of liquid and vapor. The expansion valve in small chillers is precisely calibrated to ensure the right amount of refrigerant flow and pressure drop for optimal cooling performance.
Evaporation: The low – pressure, low – temperature refrigerant mixture enters the evaporator. Inside the evaporator, the refrigerant absorbs heat from the fluid (usually water or a coolant) that needs to be cooled. This heat absorption causes the refrigerant to vaporize. The now – cooled fluid is then pumped out of the chiller and circulated to the equipment or space requiring cooling. The refrigerant vapor returns to the compressor to repeat the cycle, maintaining a continuous cooling effect.
Types of Small Chillers
Air – Cooled Small Chillers
Air – cooled small chillers are among the most popular types due to their simplicity and ease of installation. They rely on air as the medium for heat rejection, eliminating the need for a separate water supply system. These chillers are equipped with fans that force air over the condenser coils, dissipating the heat absorbed by the refrigerant into the surrounding environment.
Advantages: They are highly portable and can be used in a wide range of locations, even where access to a water source is limited. Installation is straightforward, typically only requiring electrical connections and proper ventilation around the unit. Air – cooled small chillers are also generally more cost – effective in terms of initial purchase and do not involve the additional costs associated with water treatment and plumbing for water – cooled systems.
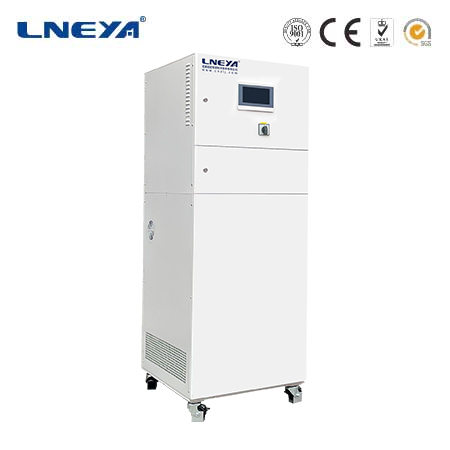
Limitations: However, their performance can be affected by high ambient temperatures. In hot environments, the air’s ability to absorb heat is reduced, which may lead to decreased cooling efficiency. They can also be noisier due to the operation of the fans, and their cooling capacity is often somewhat limited compared to water – cooled models of similar size.
Water – Cooled Small Chillers
Water – cooled small chillers use water as the heat – transfer medium to remove heat from the refrigerant. They require a connection to a water source, such as a municipal water supply, a well, or a dedicated cooling tower system. The heated water from the chiller is then either discharged or recirculated after being cooled in a cooling tower.
Advantages: These chillers offer higher cooling capacities and better energy efficiency compared to air – cooled models, especially in warmer climates or applications with consistent high cooling loads. They operate more quietly since they do not rely on large fans for heat dissipation. Water – cooled small chillers are well – suited for applications that demand continuous and reliable cooling, such as in some industrial processes or in data centers where precise temperature control is critical.
Limitations: On the downside, they are more complex to install, as they require proper plumbing connections for both the water intake and discharge. There are also additional costs associated with water treatment to prevent scaling, corrosion, and the growth of microorganisms in the water system. Maintenance can be more involved due to the need to monitor and manage the water – related components.
Refrigerant – Based Small Chillers
Some small chillers use refrigerant – based direct – expansion systems. In these units, the refrigerant is directly circulated through coils in the area or equipment to be cooled, absorbing heat directly without the need for an intermediate fluid like water. This type of small chiller is often used in applications where quick and targeted cooling is required, such as in small refrigeration cabinets or specialized cooling for electronic components.
Advantages: Refrigerant – based small chillers can provide rapid cooling and precise temperature control. They are compact and can be integrated closely with the equipment they are cooling, reducing heat transfer losses. They also eliminate the need for a secondary fluid circulation system, simplifying the overall setup in some cases.
Limitations: However, they require careful handling of the refrigerant due to its potential environmental impact and safety concerns. Maintenance may involve specialized skills for refrigerant handling, and any leaks in the refrigerant lines can be difficult to detect and repair.
Advantages and Limitations
Advantages
Cost – Effectiveness: Small chillers are generally more affordable to purchase and install compared to large – scale chiller systems. Their lower initial investment makes them accessible for small businesses, laboratories, and residential applications where a full – sized chiller would be prohibitively expensive. Additionally, their energy – efficient operation helps keep long – term operating costs down, especially when equipped with features like variable – speed drives.
Space – Saving: Their compact size allows them to fit into tight spaces, making them ideal for buildings with limited mechanical room space or for applications where space is at a premium. For example, in a small office building, a small chiller can be installed in a closet or a corner of the basement without taking up excessive floor area.
Ease of Installation and Maintenance: Small chillers often come with pre – assembled components and user – friendly interfaces, making installation relatively quick and straightforward. Maintenance tasks are also less complex, usually involving regular checks of components like filters, refrigerant levels, and electrical connections. Many models have modular designs that allow for easy replacement of individual parts if needed.
Flexibility: They can be easily adapted to different cooling requirements. Whether it’s cooling a single room, a specific piece of equipment, or a small industrial process, small chillers can be customized or adjusted to meet the specific needs of the application. Some models also offer the option to connect multiple small chillers in parallel to increase the overall cooling capacity when required.
Limitations
Limited Cooling Capacity: As the name suggests, small chillers have a restricted cooling capacity compared to large commercial or industrial chillers. They may not be suitable for applications with extremely high cooling loads, such as large manufacturing plants or sprawling commercial complexes. In such cases, multiple small chillers or a large – scale chiller system would be necessary.
Shorter Lifespan in Some Cases: Due to their compact design and potentially lower – quality components in some budget models, small chillers may have a shorter lifespan compared to more robust, larger chillers. However, with proper maintenance and the use of high – quality models, this limitation can be mitigated to some extent.
Environmental Considerations: Some small chillers use refrigerants that have a high global warming potential (GWP). As environmental regulations become stricter, users may need to upgrade to models using more environmentally friendly refrigerants, which can add to the overall cost and complexity of operation.
Applications
Residential Applications
In residential settings, small chillers can be used for various purposes. They are suitable for cooling individual rooms or small apartments, especially in regions with hot summers. For example, a small air – cooled chiller can be installed in a bedroom or a living room to provide targeted cooling without the need for a whole – house central air – conditioning system. Small chillers can also be used in combination with radiant floor heating systems for year – round comfort, providing chilled water for cooling in the summer and warm water for heating in the winter.
Commercial Applications
Small Offices and Retail Stores: Small chillers are an excellent choice for cooling small office spaces and retail stores. They can be easily installed in the ceiling or a closet, providing a comfortable environment for employees and customers without the high costs and complexity of large – scale HVAC systems. Some small chillers also come with built – in air – handling units, which can improve indoor air quality by filtering and circulating the air.
Restaurants and Cafes: In the food service industry, small chillers are used to cool kitchen equipment, such as refrigerators, freezers, and ice machines. They can also provide cooling for the dining area, ensuring a pleasant atmosphere for patrons. Water – cooled small chillers may be preferred in some restaurants to handle the higher heat loads generated by cooking equipment and to maintain more stable cooling performance.
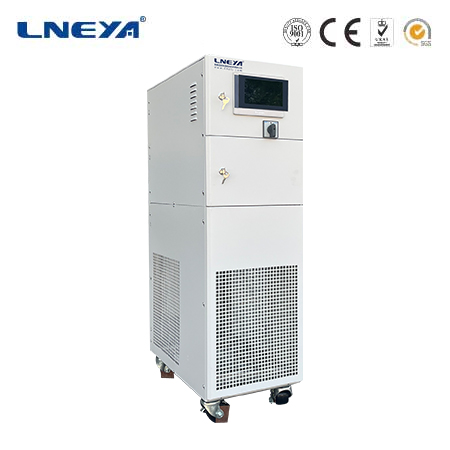
Laboratories and Research Facilities: Laboratories often require precise temperature control for various experiments and equipment. Small chillers can be customized to meet the specific cooling needs of different laboratory applications, such as cooling analytical instruments, incubators, or cold storage units. Their compact size allows them to be installed in the limited space available in many laboratories, and their ability to provide stable cooling is crucial for accurate research results.
Industrial Applications
Small – Scale Manufacturing: In small – scale manufacturing operations, small chillers are used to cool machinery, such as injection molding machines, CNC machines, and laser cutting equipment. These machines generate heat during operation, and proper cooling is essential to maintain their accuracy and longevity. Small chillers can be easily integrated into the manufacturing process, providing a reliable source of chilled water or coolant to keep the equipment running smoothly.
Pharmaceutical and Biotechnology: In the pharmaceutical and biotechnology industries, small chillers are used for temperature – sensitive processes, such as the storage and production of drugs, vaccines, and biological samples. They ensure that these products are kept within the required temperature range to maintain their efficacy and safety. Small chillers in these applications often need to meet strict regulatory requirements for temperature control and reliability.
Selection Considerations
Cooling Capacity: The most critical factor when selecting a small chiller is determining the appropriate cooling capacity. This requires calculating the heat load of the space or equipment to be cooled, taking into account factors such as the size of the area, the number of heat – generating devices, and the ambient temperature. It’s important to choose a chiller with a capacity that can meet the peak cooling demand while also operating efficiently under partial load conditions.
Type of Chiller: As discussed earlier, the choice between air – cooled, water – cooled, and refrigerant – based small chillers depends on various factors. Consider the availability of a water source, the ambient temperature of the installation location, noise requirements, and the specific cooling needs of the application. For example, if there is no easy access to a water source, an air – cooled chiller may be the best option, while a water – cooled chiller may be more suitable for applications with high and consistent cooling loads in a controlled environment.
Energy Efficiency: Look for small chillers with high energy – efficiency ratings, such as a high coefficient of performance (COP) or energy efficiency ratio (EER). Energy – efficient chillers not only reduce operating costs but also have a lower environmental impact. Features like variable – speed drives, intelligent controls, and high – efficiency heat exchangers can significantly enhance a chiller’s energy efficiency.
Size and Space Requirements: Ensure that the chosen small chiller will fit into the available installation space. Consider the dimensions of the unit, as well as the space required for ventilation (in the case of air – cooled chillers) and access for maintenance. Some small chillers are designed to be wall – mounted or under – counter, which can be useful in space – constrained environments.
Noise Level: If the chiller will be installed in an area where noise is a concern, such as near living spaces or in an office environment, pay attention to the noise level specification of the unit. Water – cooled chillers generally operate more quietly than air – cooled ones, but some air – cooled models are designed with noise – reducing features, such as sound – insulated enclosures or low – noise fans.
Installation, Operation, and Maintenance
Installation
Proper installation is essential for the optimal performance and longevity of a small chiller. Follow the manufacturer’s installation instructions carefully, which typically include steps for electrical wiring, plumbing connections (for water – cooled chillers), and positioning the unit. Ensure that the installation location provides adequate ventilation for air – cooled chillers and proper access for maintenance. For water – cooled chillers, install appropriate water treatment equipment if required to maintain water quality and prevent scaling and corrosion.
Operation
Once installed, familiarize yourself with the chiller’s control panel and operating instructions. Set the desired temperature and other parameters according to the cooling requirements. Regularly monitor the chiller’s performance, including refrigerant pressure, temperature of the chilled fluid, and electrical consumption. Some small chillers come with remote monitoring capabilities, allowing you to check the unit’s status and make adjustments from a remote location.
Maintenance
Regular maintenance is crucial to keep a small chiller running smoothly. Common maintenance tasks include:
Filter Cleaning/Replacement: Clean or replace air filters (in air – cooled chillers) and strainers (in water – cooled chillers) regularly to ensure proper airflow and water flow. Clogged filters can reduce the chiller’s efficiency and cause it to work harder, increasing energy consumption.
Refrigerant Level Check: Periodically check the refrigerant level and pressure. Low refrigerant levels can indicate a leak, which should be repaired promptly by a qualified technician.
Electrical Component Inspection: Inspect electrical connections, wires, and controls for signs of wear, loose connections, or damage. Tighten any loose connections and replace any faulty components as needed.
Heat Exchanger Cleaning: For water – cooled chillers, clean the condenser and evaporator heat exchangers periodically to remove dirt, debris, and scale buildup. This helps maintain optimal heat transfer efficiency.
Lubrication: Lubricate moving parts, such as fans and pumps, according to the manufacturer’s recommendations to reduce friction and extend their lifespan.
Future Trends
Smart and Connected Technologies: The future of small chillers is likely to see increased integration of smart technologies. Small chillers may be equipped with sensors and wireless communication capabilities, allowing them to be remotely monitored and controlled. Smart controls can optimize the chiller’s operation based on real – time data, such as ambient temperature, occupancy, and cooling demand, further enhancing energy efficiency. Additionally, predictive maintenance features can be incorporated, using data analytics to predict potential component failures and schedule maintenance before breakdowns occur.
Sustainable Refrigerants and Energy Sources: With growing environmental concerns, there will be a greater emphasis on using sustainable refrigerants with low global warming potential in small chillers. Additionally, the integration of renewable energy sources, such as solar – powered chillers or chillers that can be powered by waste heat from other processes, is expected to become more common. This will not only reduce the environmental impact of small chillers but also help users achieve their sustainability goals.
Miniaturization and High – Efficiency Design: As technology advances, small chillers are likely to become even more compact and efficient. New materials and manufacturing techniques will enable the development of smaller, yet more powerful compressors, heat exchangers, and other components. This will allow small chillers to provide higher cooling capacities in an even smaller footprint, making them suitable for an even wider range of applications.
Conclusion
Small chillers offer a practical and efficient cooling solution for a diverse range of applications, from residential comfort to industrial process cooling. Understanding their characteristics, working principles, types, advantages, and limitations is essential for making informed decisions when selecting, installing, and operating these units. By following proper maintenance practices and keeping an eye on emerging trends, users can ensure that their small chillers provide reliable, energy – efficient cooling for years to come. As technology continues
Related recommendations
40 ton air cooled chiller
82Working PrincipleThe 40 ton air cooled chiller operates on the vapor-compression refrigeration cycle, which involves four main stages:Compression: The compressor takes in low-pressure, low-tempe...
View detailsexternal chiller
383External Chillers: Types and Operation External chillers are refrigeration units used to cool fluids, typically water or glycol, which are then circulated through heat exchangers to provide coo...
View detailsunit of chiller capacity
117Common Units of Chiller CapacityBritish Thermal Units per Hour (BTU/h)The British Thermal Unit (BTU) is a traditional unit of energy widely used in the United States and some other regions. One ...
View detailslow pressure chiller
149Low Pressure Chillers: A Comprehensive Guide Introduction Low pressure chillers play a crucial role in modern cooling applications. They are designed to provide efficient cooling solutions...
View details
HelloPlease log in