digital temperature controllers
Introduction
In an era where precise temperature control is crucial for the optimal performance of various processes and systems, digital temperature controllers have emerged as indispensable tools. These devices offer enhanced accuracy, flexibility, and functionality compared to their analog counterparts. Whether it’s maintaining the ideal temperature in a manufacturing plant, ensuring the safety and quality of food products, or regulating the environment in a research laboratory, digital temperature controllers play a vital role. This article will provide a detailed overview of digital temperature controllers, covering their basic concepts, working mechanisms, types, applications, and key considerations for selection and use.
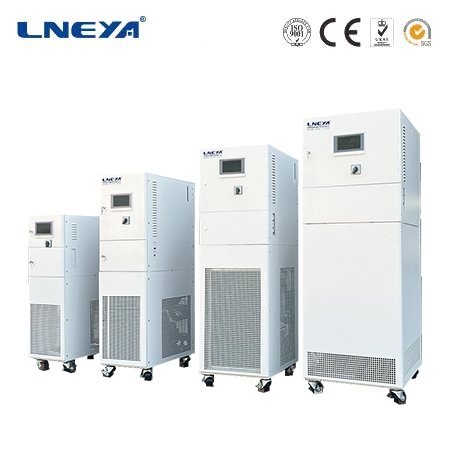
What are Digital Temperature Controllers?
A digital temperature controller is an electronic device that monitors and regulates the temperature of a system or process. It uses digital technology, typically a microprocessor or microcontroller, to receive input from temperature sensors, process the data, and generate control signals to adjust heating or cooling devices. Unlike analog controllers, which rely on physical components such as potentiometers and transistors for operation, digital temperature controllers offer higher precision, programmability, and the ability to interface with other digital devices and systems.
Digital temperature controllers usually have a digital display that shows the current temperature reading, the setpoint (the desired temperature), and other relevant information. They can be configured and programmed through buttons, keypads, or via a computer interface, allowing users to customize the control parameters according to their specific requirements.
Working Principles of Digital Temperature Controllers
Sensing
The operation of a digital temperature controller starts with the temperature sensor. There are various types of temperature sensors commonly used, including thermocouples, resistance temperature detectors (RTDs), and thermistors. These sensors convert the thermal energy into an electrical signal, which is then transmitted to the controller. For example, a thermocouple generates a small voltage based on the temperature difference between its two junctions, while an RTD changes its electrical resistance in proportion to the temperature. The controller reads this electrical signal and converts it into a digital temperature value for further processing.
Processing
Once the temperature value is received, the digital controller’s microprocessor or microcontroller processes the data. It compares the measured temperature with the pre – set setpoint. Based on the difference between the two (the error), the controller applies a specific control algorithm to determine the appropriate control action. The most widely used control algorithm in digital temperature controllers is the Proportional – Integral – Derivative (PID) algorithm.
The PID algorithm calculates the control output by combining three components:
Proportional (P): The proportional term reacts to the current error. It provides an output that is directly proportional to the magnitude of the error. For example, if the error is large, the proportional term will generate a larger control signal to make a more significant adjustment to the heating or cooling device.
Integral (I): The integral term accumulates the error over time. It helps to eliminate any steady – state error, ensuring that the temperature eventually reaches and stays at the setpoint. By continuously adjusting the control output based on the accumulated error, the integral term compensates for any constant disturbances or inaccuracies in the system.
Derivative (D): The derivative term predicts the future behavior of the error based on its rate of change. It helps to dampen the system’s response and prevent overshooting the setpoint. By taking into account how quickly the error is changing, the derivative term can make preemptive adjustments to the control output, resulting in a more stable and responsive control system.
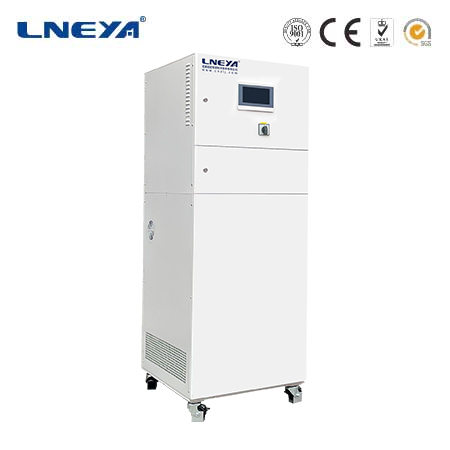
Actuation
After the controller determines the control action using the selected algorithm, it sends a control signal to the actuator. Actuators can be heating elements, cooling fans, valves in HVAC systems, or other devices that can adjust the temperature of the system. For example, if the measured temperature is lower than the setpoint, the controller will send a signal to increase the power to the heating element or turn on a heating device. Conversely, if the temperature is too high, it will activate the cooling device to reduce the temperature. This continuous cycle of sensing, processing, and actuation ensures that the temperature is maintained as close as possible to the desired setpoint.
Types of Digital Temperature Controllers
Programmable Digital Temperature Controllers
Programmable digital temperature controllers offer a high degree of flexibility. They allow users to set multiple temperature setpoints and control parameters for different time periods. These controllers are commonly used in applications where the temperature needs to follow a specific profile over time, such as in heat treatment processes for metals. For example, in a metal annealing process, the temperature may need to be gradually increased, held at a certain level for a specific duration, and then cooled down in a controlled manner. Programmable controllers can be easily programmed to follow such complex temperature profiles, ensuring consistent and accurate processing. They usually have a user – friendly interface, such as a liquid crystal display (LCD) and a keypad, for setting and modifying the program parameters.
PID Digital Temperature Controllers
PID digital temperature controllers are the most widely used type due to their effectiveness in achieving stable and precise temperature control. As mentioned earlier, they use the PID control algorithm to continuously adjust the control output based on the error between the measured temperature and the setpoint. These controllers can be tuned to optimize the performance for different applications by adjusting the proportional, integral, and derivative gains. PID controllers are suitable for a wide range of processes, from simple room temperature control in residential settings to complex industrial manufacturing processes. They are available in various configurations, including single – loop controllers for controlling a single temperature zone and multi – loop controllers for managing multiple temperature points simultaneously.
Smart Digital Temperature Controllers
With the advancement of technology, smart digital temperature controllers have emerged. These controllers are equipped with features such as built – in communication interfaces (e.g., Ethernet, Wi – Fi, Bluetooth), allowing them to connect to a network or other devices. This enables remote monitoring and control of the temperature, as well as data logging and analysis. Smart controllers can also integrate with other smart systems, such as building automation systems or industrial control networks. They often use advanced algorithms and machine learning techniques to optimize the temperature control process, adapt to changing conditions, and predict potential issues. For example, a smart temperature controller in a commercial building can analyze occupancy patterns, weather data, and energy consumption to adjust the temperature in an energy – efficient and comfortable manner.
Applications of Digital Temperature Controllers
Industrial Applications
Manufacturing: In manufacturing plants, digital temperature controllers are used in a variety of processes. For instance, in plastic injection molding, precise temperature control of the mold and the plastic material is essential for producing high – quality parts with consistent dimensions. Digital temperature controllers ensure that the temperature is maintained within a narrow range, preventing issues such as warping, shrinkage, or poor surface finish. In metalworking, they are used to control the temperature of furnaces, heat treatment equipment, and welding processes, ensuring the desired material properties and product quality.
Food Processing: The food industry relies on digital temperature controllers to maintain food safety and quality. In food storage facilities, such as cold rooms and freezers, these controllers monitor and regulate the temperature to prevent spoilage and the growth of harmful bacteria. During food processing operations, like cooking, baking, and pasteurization, digital temperature controllers ensure that the food is processed at the correct temperature for the appropriate duration, killing pathogens and preserving the nutritional value and taste of the food.
Pharmaceutical and Biotechnology: In the pharmaceutical and biotechnology sectors, digital temperature controllers are crucial for the production, storage, and transportation of drugs, vaccines, and biological samples. Even a slight deviation from the required temperature can affect the efficacy and stability of these products. Digital controllers are used to maintain the temperature of incubators, refrigerators, freezers, and bioreactors within strict limits, ensuring the integrity of the biological materials and the success of research and production processes.
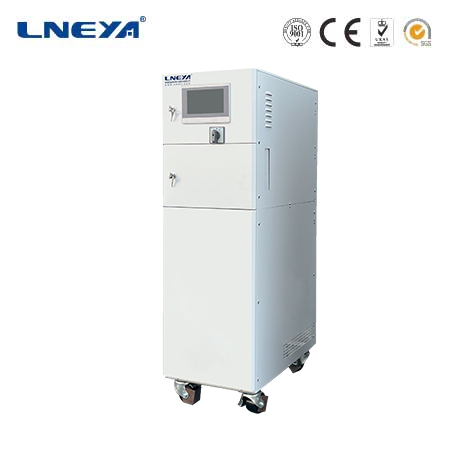
Scientific Research
In laboratories, digital temperature controllers are used in a wide range of experiments. For example, in biological research, they maintain the temperature of incubators to support cell growth and the development of organisms. In materials science, they control the temperature during material synthesis, characterization, and testing, allowing researchers to study the properties of materials under different thermal conditions. In chemical experiments, digital temperature controllers ensure that reactions occur at the desired temperature, enabling accurate and reproducible results.
HVAC Systems
In heating, ventilation, and air – conditioning (HVAC) systems, digital temperature controllers play a key role in providing comfortable indoor environments. They are used in residential, commercial, and industrial buildings to control the temperature of heating and cooling equipment, such as furnaces, air conditioners, and heat pumps. Digital thermostats, which are a type of digital temperature controller, can be programmed to adjust the temperature based on the time of day, occupancy, and user preferences. This not only improves comfort but also helps to optimize energy consumption, reducing heating and cooling costs.
Considerations When Selecting Digital Temperature Controllers
Temperature Range and Accuracy
The first consideration when choosing a digital temperature controller is the required temperature range and accuracy. Different applications have different temperature requirements, and the controller must be able to operate within the necessary range. For example, some industrial processes may require temperature control in the range of -200°C to 1500°C, while a simple room thermostat may only need to control temperatures between 10°C and 30°C. In addition to the range, accuracy is crucial. High – precision applications, such as in scientific research or pharmaceutical manufacturing, may require a controller with an accuracy of ±0.1°C or better, while less critical applications may tolerate a slightly lower accuracy.
Control Algorithm and Functionality
The choice of control algorithm depends on the nature of the process being controlled. PID controllers are suitable for most applications, but for processes with complex dynamics or specific requirements, other algorithms or additional features may be needed. Programmable controllers offer the flexibility to set custom temperature profiles, while smart controllers provide advanced features like remote monitoring and data analytics. Consider the specific control requirements of your application and choose a controller that offers the appropriate functionality.
Communication Interfaces
If you need to integrate the digital temperature controller with other devices or systems, such as a computer, a building management system, or an industrial control network, the availability of communication interfaces is important. Common interfaces include RS – 232, RS – 485, Ethernet, Wi – Fi, and Bluetooth. Make sure the controller has the necessary interface to enable seamless communication and data exchange with the other components in your system.
Input and Output Types
The controller’s input type should be compatible with the temperature sensor you plan to use. Different sensors have different output signals, and the controller must be able to read and process these signals correctly. Similarly, the output type of the controller should match the actuator or device that will be used to adjust the temperature. For example, if you are using a heating element that requires a relay – based control signal, the controller should have a relay output.
Cost and Budget
Digital temperature controllers vary in price depending on their features, functionality, and brand. While it’s important to choose a controller that meets your technical requirements, you also need to consider your budget. Compare different models and brands to find a controller that offers the best combination of performance and cost for your application. Keep in mind that higher – end controllers with advanced features may have a higher upfront cost but can also provide long – term savings through improved efficiency and reduced maintenance.
Installation, Operation, and Maintenance of Digital Temperature Controllers
Installation
Proper installation is essential for the optimal performance of digital temperature controllers. Follow the manufacturer’s installation instructions carefully, which typically include steps for wiring the controller to the temperature sensor and the actuator. Ensure that the wiring is done correctly to avoid electrical interference and inaccurate temperature readings. Mount the controller in a suitable location, preferably in an area that is easily accessible for programming and monitoring but protected from dust, moisture, and extreme temperatures. For controllers with communication interfaces, connect them to the network according to the specified procedures.
Operation
Once installed, familiarize yourself with the controller’s user interface and operating instructions. Set the initial temperature setpoint and other control parameters according to your application requirements. If the controller is programmable, create the desired temperature profile. Regularly monitor the temperature readings and the controller’s operation to ensure that the system is functioning properly. Some controllers may have diagnostic features that can alert you to any issues, such as sensor malfunctions or control errors. If any problems occur, refer to the user manual or contact the manufacturer’s technical support for assistance.
Maintenance
Regular maintenance can help prolong the lifespan of the digital temperature controller and ensure its accurate operation. Periodically check the wiring connections to make sure they are secure and free from damage. Clean the controller’s exterior and display to remove dust and debris. If the controller has a battery – backed memory (for storing program settings), replace the battery as recommended by the manufacturer to prevent data loss. Calibrate the controller and the temperature sensor periodically to ensure accurate temperature measurement. Follow the manufacturer’s maintenance schedule and guidelines for specific maintenance tasks, such as software updates (if applicable) and component inspections.
Future Trends in Digital Temperature Controllers
Integration with the Internet of Things (IoT)
The integration of digital temperature controllers with the IoT is a growing trend. This will enable more advanced features, such as real – time remote monitoring and control from mobile devices, cloud – based data storage and analysis, and seamless integration with other smart devices and systems. For example, in a smart home, a digital temperature controller could communicate with other smart appliances, like smart thermostats, lights, and security systems, to create a more energy – efficient and comfortable living environment. In an industrial setting, IoT – enabled temperature controllers could be part of a larger network of connected devices, allowing for centralized management and optimization of multiple temperature – controlled processes.
Enhanced Energy – Efficiency Features
As energy costs continue to rise and environmental concerns become more prominent, there will be a greater focus on developing digital temperature controllers with enhanced energy – efficiency features. These may include more intelligent control algorithms that optimize energy consumption based on real – time data, such as ambient temperature, occupancy, and energy prices. Controllers may also be designed to work more efficiently with energy – saving heating and cooling devices, such as variable – speed heat pumps and LED – based heating elements. Additionally, the use of renewable energy sources, such as solar – powered temperature sensors and controllers, is likely to become more common.
Miniaturization and Microfabrication
Advancements in microfabrication technology will lead to the development of smaller, more compact digital temperature controllers. Miniature controllers will be suitable for applications where space is limited, such as in portable devices, wearable electronics, and microfluidic chips. These small – scale controllers will still offer high precision and functionality, but with reduced power consumption and cost. The miniaturization trend will also enable the integration of multiple sensors and control functions into a single, tiny device, further enhancing the capabilities and versatility of digital temperature controllers.
Conclusion
Digital temperature controllers are essential devices for achieving precise and reliable temperature control in a wide variety of applications. Understanding their working principles, types, applications, and key considerations for selection, installation, operation, and maintenance is crucial for ensuring their optimal performance. As technology continues to evolve, digital temperature controllers will become even more advanced, offering enhanced features, improved energy efficiency, and greater integration with other systems. By staying informed about the latest trends and developments in this field, users can make the most of these devices and meet the growing demands for accurate temperature control in various industries and everyday life.
Related recommendations
chiller 12 kw
505Understanding 12 kW Chillers A 12 kW chiller is a versatile cooling system that provides 12 kilowatts of cooling power, suitable for a range of applications from commercial spaces to industrial...
View detailsglycol tank chiller
350Glycol Tank Chiller: Industrial Cooling Solutions Glycol tank chillers are an essential component in many industrial processes where consistent and reliable cooling is required. These chillers ...
View detailsmodular chiller system
445Modular Chiller Systems: Flexible and Efficient Cooling Solutions Modular chiller systems have become increasingly popular in the HVAC industry due to their versatility, efficiency, and scalabi...
View detailslarge tonnage chillers
63Working PrinciplesThe fundamental working principles of large tonnage chillers are based on either the vapour compression cycle or the absorption cycle, although the scale and complexity of compo...
View details
HelloPlease log in