unit of chiller capacity
Common Units of Chiller Capacity
British Thermal Units per Hour (BTU/h)
The British Thermal Unit (BTU) is a traditional unit of energy widely used in the United States and some other regions. One BTU is defined as the amount of heat required to raise the temperature of one pound of water by one degree Fahrenheit. When expressed as BTU per hour (BTU/h), it measures the rate at which a chiller can remove heat. For example, a small – scale chiller used in a residential air – conditioning system might have a capacity of 12,000 BTU/h. This indicates that the chiller can remove 12,000 BTUs of heat from the cooled space or medium every hour.
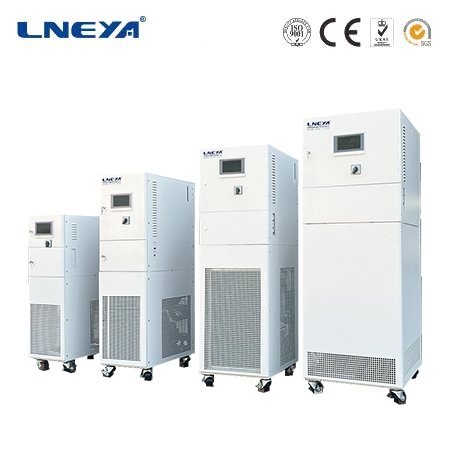
BTU/h is a versatile unit that can be used to describe the capacity of various types of chillers, from small portable units to large industrial systems. It provides a straightforward way to compare the cooling capabilities of different chillers, especially when dealing with applications where the heat load is calculated in BTUs. However, due to its relatively small magnitude for large – scale applications, larger multiples such as MBtu/h (million BTUs per hour) are sometimes used.
Tons of Refrigeration (TR)
The ton of refrigeration is another commonly used unit, particularly in the HVAC (Heating, Ventilation, and Air – Conditioning) industry. One ton of refrigeration is defined as the amount of heat required to melt one ton (2000 pounds) of ice at 32°F (0°C) in 24 hours. This is equivalent to 12,000 BTU/h. The origin of this unit dates back to the days when ice was used for cooling, and it represents the cooling effect equivalent to melting a certain amount of ice over a specific period.
In commercial and industrial settings, chillers with capacities ranging from a few tons to several thousand tons are common. For instance, a medium – sized commercial building might use a chiller with a capacity of 50 TR to meet its cooling requirements. The use of tons of refrigeration simplifies the specification and comparison of chillers in the HVAC industry, as it provides a more intuitive measure of cooling capacity for large – scale applications compared to BTU/h.
Kilowatts (kW)
Kilowatts (kW) is the SI (International System of Units) unit for power and is widely used globally to measure the cooling capacity of chillers. One kilowatt is equal to 1000 watts, and in the context of chiller capacity, it represents the rate at which the chiller can remove heat in terms of electrical power equivalent. To convert between BTU/h and kW, the conversion factor is that 1 kW is approximately equal to 3412.14 BTU/h.
The use of kW as a capacity unit is beneficial in international contexts and in applications where energy consumption and efficiency calculations are based on the metric system. It allows for easy integration with other electrical and energy – related measurements. In modern industrial and commercial chiller systems, kW is frequently used, especially when communicating with international partners or when analyzing the overall energy performance of a facility’s cooling infrastructure.
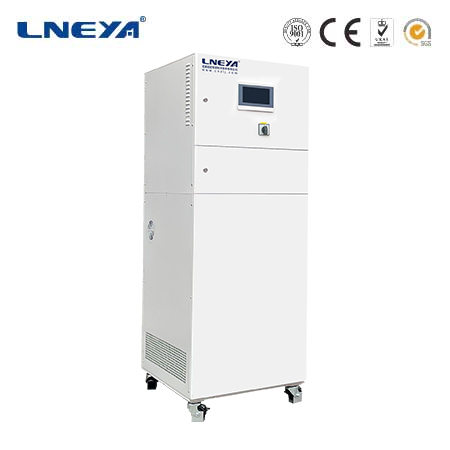
Conversion Between Capacity Units
Converting between different chiller capacity units is essential for accurate communication and system design. The following are the key conversion factors:
BTU/h to TR: Since 1 TR is equal to 12,000 BTU/h, to convert from BTU/h to TR, divide the value in BTU/h by 12,000. For example, a chiller with a capacity of 60,000 BTU/h has a capacity of 60,000 / 12,000 = 5 TR.
TR to BTU/h: To convert from TR to BTU/h, multiply the value in TR by 12,000. So, a 10 – TR chiller has a capacity of 10 * 12,000 = 120,000 BTU/h.
BTU/h to kW: As mentioned earlier, 1 kW is approximately 3412.14 BTU/h. To convert from BTU/h to kW, divide the value in BTU/h by 3412.14. For instance, a chiller with a capacity of 34,121.4 BTU/h has a capacity of 34,121.4 / 3412.14 = 10 kW.
kW to BTU/h: To convert from kW to BTU/h, multiply the value in kW by 3412.14. Thus, a 20 – kW chiller has a capacity of 20 * 3412.14 = 68,242.8 BTU/h.
TR to kW: First convert TR to BTU/h (by multiplying by 12,000) and then convert the resulting BTU/h value to kW by dividing by 3412.14. For example, a 25 – TR chiller has a capacity of (25 * 12,000) / 3412.14 ≈ 87.92 kW.
Application Scenarios of Different Capacity Units
Residential Applications
In residential air – conditioning systems, BTU/h is commonly used to specify the capacity of chillers and air conditioners. Homeowners and HVAC contractors are often more familiar with this unit as it provides a detailed measure of the cooling capacity required for a specific room or house. For example, when sizing an air conditioner for a small bedroom, the capacity might be specified as 5000 – 8000 BTU/h, depending on factors such as the room size, insulation, and number of occupants. This detailed measurement helps in selecting the right – sized unit to ensure comfort while avoiding over – or under – sizing, which can lead to inefficiency or poor performance.
Commercial and Industrial HVAC Applications
In commercial buildings such as offices, malls, and hotels, as well as in industrial facilities, both tons of refrigeration (TR) and kilowatts (kW) are widely used. Tons of refrigeration is a preferred unit in the HVAC industry in the United States and some other regions for its simplicity in communicating large – scale cooling requirements. Facility managers and engineers can quickly understand the cooling capacity of a chiller in terms of TR and compare it with the building’s cooling load. For example, a large shopping mall might require a chiller with a capacity of several hundred tons of refrigeration to maintain comfortable indoor temperatures for shoppers.
Kilowatts (kW), on the other hand, is more commonly used in international settings and in applications where energy efficiency calculations are a priority. Many modern building energy management systems and international building codes use kW as the standard unit for measuring cooling capacity. This allows for seamless integration with other energy – related measurements and enables accurate analysis of a building’s overall energy consumption and performance. For instance, in an industrial manufacturing plant, when evaluating the energy efficiency of a chiller system, using kW as the capacity unit helps in comparing the chiller’s performance with industry benchmarks and in implementing energy – saving measures.
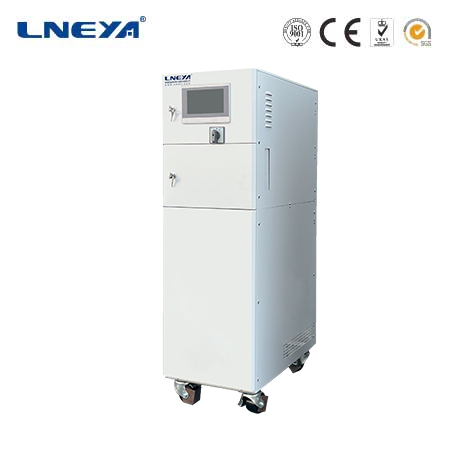
Data Centers
Data centers have specific cooling requirements due to the high heat loads generated by servers and other IT equipment. Kilowatts (kW) is the predominant unit used to measure chiller capacity in data centers. This is because data center operators are highly focused on energy consumption and efficiency, and using kW allows for easy integration with the data center’s power management systems. By specifying chiller capacity in kW, operators can accurately calculate the cooling load and energy requirements of the data center, optimize the operation of the chiller system, and implement energy – saving strategies such as free – cooling when ambient conditions permit.
Factors Influencing Chiller Capacity Requirements
Cooling Load
The cooling load is the most significant factor determining the required chiller capacity. It represents the amount of heat that needs to be removed from the space or process to maintain the desired temperature. In a commercial building, the cooling load is influenced by factors such as the building’s size, insulation quality, number of occupants, solar gain through windows, and the heat generated by equipment and lighting. In an industrial setting, the cooling load is determined by the heat generated during manufacturing processes, the temperature requirements of machinery, and the heat from stored materials. A larger cooling load requires a chiller with a higher capacity to effectively remove the heat and maintain the desired temperature.
Ambient Conditions
Ambient temperature and humidity have a direct impact on chiller capacity requirements. In hot and humid climates, chillers have to work harder to dissipate heat, which may require a higher – capacity chiller to achieve the same cooling effect as in a cooler climate. For example, an air – cooled chiller operating in a tropical region will face more challenges in rejecting heat to the ambient air compared to the same chiller in a temperate climate. Similarly, high humidity can affect the performance of evaporative chillers, reducing their cooling capacity and potentially increasing the required chiller capacity to meet the cooling demand.
Desired Temperature and Temperature Control Precision
The desired temperature of the cooled space or process and the required precision of temperature control also influence chiller capacity. In applications where extremely low temperatures are required, such as in pharmaceutical cold storage or semiconductor manufacturing, chillers with higher capacities may be needed to achieve and maintain the low temperatures. Additionally, if precise temperature control is essential, a chiller with a more accurate capacity matching and control system may be required. For example, in a research laboratory where experiments are sensitive to small temperature fluctuations, a chiller with a capacity that can be finely adjusted to maintain a stable temperature within a narrow range is necessary.
Selecting the Appropriate Capacity Unit
Based on Regional Practices
Consider the common practices and standards in the region where the chiller will be installed and operated. In the United States, BTU/h and tons of refrigeration are widely used in the HVAC industry, so specifying chiller capacity in these units may be more appropriate for local contractors, engineers, and facility managers. In international projects or regions that follow the metric system, using kilowatts (kW) as the capacity unit is often more convenient and in line with industry standards, facilitating communication and integration with other building systems and energy management practices.
According to Application Requirements
For applications where detailed heat load calculations are based on BTUs, such as in some residential and small – scale commercial projects, using BTU/h as the capacity unit can provide a more intuitive understanding of the cooling requirements. In large – scale commercial and industrial applications where the focus is on the overall cooling capacity and ease of communication within the HVAC industry, tons of refrigeration may be a better choice. When energy efficiency and integration with electrical and energy – related systems are priorities, especially in data centers and international projects, kilowatts (kW) is the most suitable unit.
For Compatibility with Existing Systems and Equipment
If the chiller is being installed as part of an existing cooling system or facility, it is important to select a capacity unit that is compatible with the existing equipment and control systems. For example, if the facility’s energy management system already uses kW as the standard unit for measuring power and energy, choosing a chiller specified in kW will ensure seamless integration and accurate monitoring of the chiller’s performance within the overall system.
In conclusion, the unit of chiller capacity is a fundamental aspect of chiller specification, selection, and operation. Understanding the different units, their conversion relationships, application scenarios, and the factors influencing capacity requirements is essential for ensuring that chillers are properly sized, operate efficiently, and meet the cooling needs of various applications. By carefully considering these aspects and selecting the appropriate capacity unit, users can optimize the performance of their chiller systems, reduce energy consumption, and achieve cost – effective and reliable cooling solutions.
Related recommendations
How to deal with the installation of water pumps in air cooled water chillers that do not produce water?
1059How to deal with the installation of water pumps in air cooled water chillers that do not produce water? To address the issue of the water pump in the air-cooled chiller being unable to...
View detailsthe chiller cooler
512The Chiller Cooler: A Vital Component of HVAC Systems The chiller cooler, often simply referred to as a chiller, is an integral part of Heating, Ventilation, and Air Conditioning (HVAC) systems...
View details500 ton water cooled chiller
430500 Ton Water-Cooled Chiller: Large-Scale Cooling Solutions for Industrial Applications A 500-ton water-cooled chiller is a significant piece of HVAC equipment capable of managing substantial t...
View detailswater source chiller
87Working Principles of Water Source ChillersThe fundamental operation of water source chillers is grounded in the vapor - compression refrigeration cycle, which involves four essential components:...
View details
HelloPlease log in