process heating equipment
Introduction to Process Heating Equipment
Process heating is a critical aspect of many industrial operations, where maintaining precise temperatures is necessary for the efficiency and quality of the end product. Process heating equipment is designed to provide this necessary heat, ensuring that materials are processed under optimal conditions. This article explores the different types of process heating equipment, their operational mechanisms, benefits, and their applications in various industries.
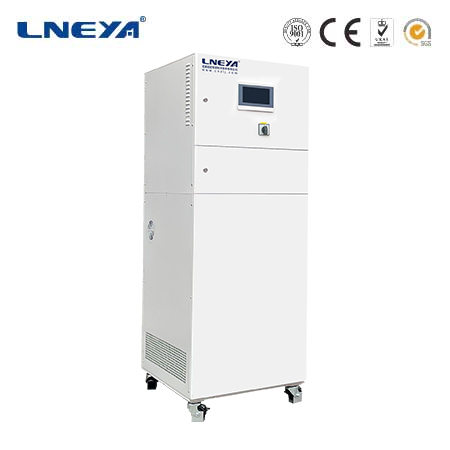
Types of Process Heating Equipment
Process heating equipment can be broadly categorized into the following types:
Direct Heating: In this method, the heat source comes into direct contact with the material being heated, such as in furnaces and ovens.
Indirect Heating: The heat is transferred to the material through a heat exchanger, which prevents direct contact between the heat source and the material. Examples include heat exchangers and thermal fluid systems.
Electric Heating: This involves the use of electric heaters, such as immersion heaters, band heaters, and cartridge heaters, which convert electrical energy into heat.
Fluid Heating: This type of equipment heats fluids, which are then circulated to the process. It includes steam boilers, hot oil heaters, and indirect water heaters.
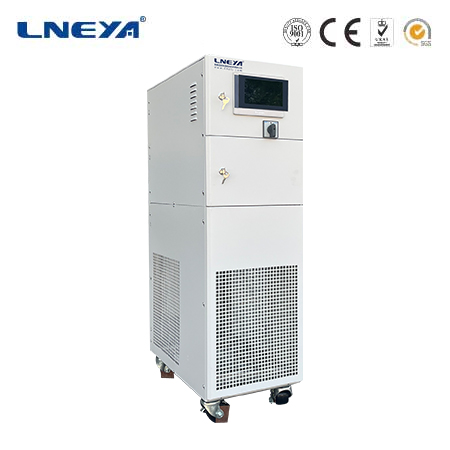
Infrared Heating: This uses infrared radiation to directly heat the surface of the material, providing quick and focused heat.
Working Principles
The working principles of process heating equipment vary depending on the type:
Conduction: Heat is transferred through direct contact between the material and the heat source or heating element.
Convection: Heat is transferred through the movement of heated fluids or gases.
Radiation: Heat is transferred through electromagnetic waves, directly heating the surface of the material without the need for a medium.
Advantages of Process Heating Equipment
The use of process heating equipment offers several advantages:
Efficiency: Modern process heating equipment is designed to minimize heat loss, ensuring efficient energy use.
Precision: These systems can maintain precise temperature control, which is crucial for many industrial processes.
Safety: Properly designed and maintained heating equipment reduces the risk of accidents and ensures a safe working environment.
Versatility: Process heating equipment can be adapted to a wide range of applications and can handle various materials and processes.
Applications of Process Heating Equipment
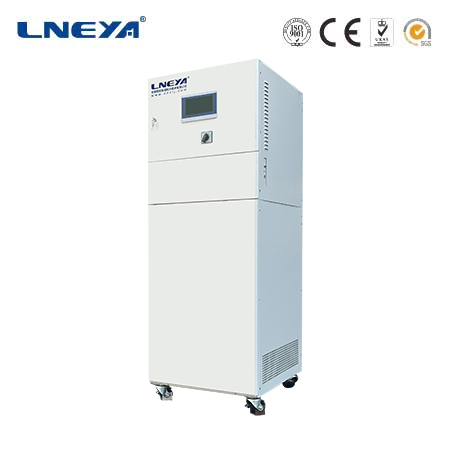
Process heating equipment is used across various industries, including:
Chemical Industry: For reactions that require precise temperature control.
Food and Beverage: For processes such as cooking, baking, and pasteurization.
Pharmaceutical: For the manufacturing of drugs and medical products that require specific temperature conditions.
Plastics and Rubber: For melting and molding processes.
Metal Processing: For heat treatment and annealing of metals.
Conclusion
Process heating equipment is indispensable in industries where temperature control is crucial for process efficiency and product quality. The selection of the appropriate heating equipment depends on the specific requirements of the process, including the type of material being heated, the required temperature range, and the desired level of temperature control. As technology advances, process heating equipment continues to evolve, offering improved efficiency, precision, and safety.
Note: This article is intended for informational purposes only and does not endorse or promote any specific products or services. It is designed to provide a comprehensive understanding of process heating equipment and its importance in various industrial applications.
Related recommendations
temperature of a chiller
432Introduction to Chiller Temperatures Chiller systems are designed to remove heat from an area or process and maintain a desired temperature for comfort, safety, or industrial requirements. The ...
View detailsthermostream price
75Thermostream Price: Factors, Ranges, and ConsiderationsThe cost of a thermostream system is a crucial aspect for anyone considering its implementation, whether for industrial, automotive, electro...
View detailsindustrial chiller machine
258Industrial Chiller Machine Industrial chiller machines are indispensable pieces of equipment in numerous industrial sectors. They are designed to remove heat from various industrial processes, ...
View detailsprocess heating and cooling
396Process Heating and Cooling: Technologies and Market Trends Process heating and cooling systems are critical in maintaining the desired temperature ranges in numerous industrial processes, from...
View details
HelloPlease log in