chiller for injection molding machine
Chiller for Injection Molding Machine: Enhancing Efficiency and Quality
Industrial chillers are crucial components in the injection molding process, providing precise temperature control to ensure the quality and consistency of plastic parts. This article delves into the various aspects of chillers for injection molding machines, including their applications, benefits, and technological advancements.
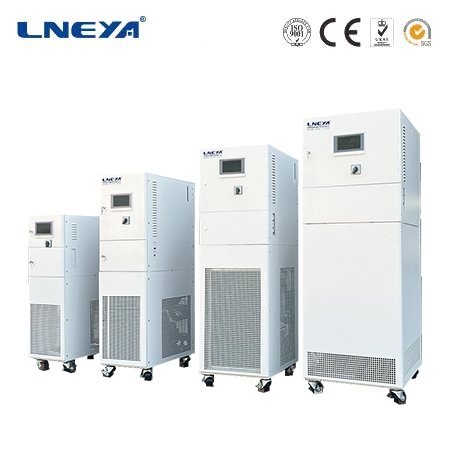
Applications and Benefits
Chillers for injection molding machines are used to cool the plastic molds, which is essential for controlling the temperature of the plastic being molded. This process enhances the surface quality of the plastic parts and can significantly reduce the cycle time, leading to increased production efficiency.
Types of Chillers
There are two main types of chillers used in injection molding: air-cooled and water-cooled chillers. Air-cooled chillers are simpler to install and do not require a water source, making them ideal for stationary cooling. Water-cooled chillers, on the other hand, offer more efficient heat removal and are long-lasting with high performance.
Selection Criteria
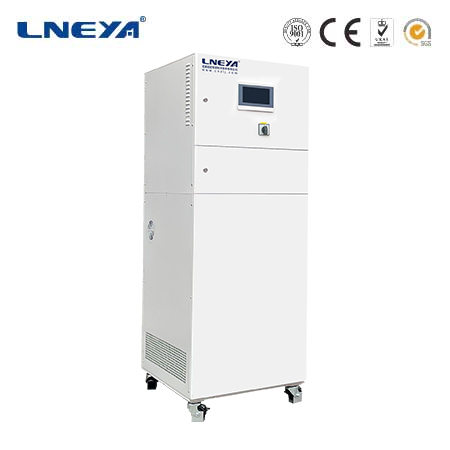
When selecting a chiller for an injection molding machine, several factors must be considered, including the melting point of the plastic, heat distortion temperature (HDT), desired mold temperature controller, cooling power, and available space. The melting point of the plastic is particularly important as it varies with different types of plastics, influencing the choice of the chiller system.
Technological Advancements
Modern chillers for injection molding machines are equipped with advanced features such as microprocessor control, which allows for precise temperature control and easy operation. Innovations like FleXX technology adapt the performance of components to the cooling requirements of the application, reducing energy requirements by up to 30% and leading to significant savings in refrigerant.
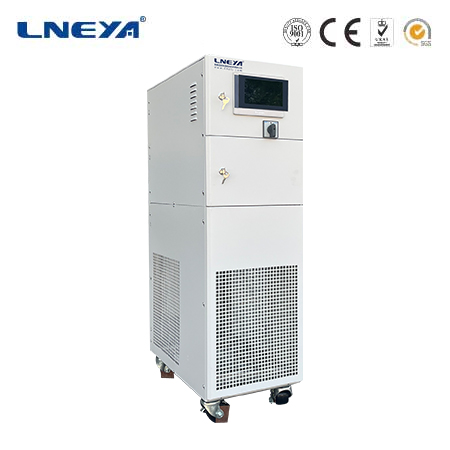
Impact on Injection Molding Process
The use of chillers in injection molding machines has a significant impact on the process. Chillers help in reducing cycle times and improving the quality of the molded parts. They also contribute to energy savings, with some drive systems achieving up to 66% energy-saving performance.
Conclusion
Chillers for injection molding machines play a critical role in the plastic manufacturing industry. They not only enhance the efficiency and quality of the injection molding process but also contribute to energy savings and environmental sustainability. As technology continues to advance, the capabilities of chillers are expected to improve, further optimizing the injection molding process and meeting the growing demands of the industry
Related recommendations
cooling jacket reactor
318Cooling Jacket Reactor: A Complete IntroductionA cooling jacket reactor is a crucial apparatus widely used in various industrial processes, especially in the chemical, pharmaceutical, and food ind...
View detailsexternal chiller
448Closed-Cycle Cooling Water System: Precision Temperature Control for Diverse Applications A closed-cycle cooling water system, often referred to as a recirculating water bath chiller, is an ess...
View detailsclosed water cooling system
309Closed Water Cooling Systems: Efficient and Sustainable Industrial Cooling Closed water cooling systems, also known as closed-loop cooling systems, are specialized setups used in various indust...
View detailsefficient chillers
166Introduction In an era where energy conservation and sustainability are at the forefront, the demand for efficient chillers has never been higher. Chillers are integral to numerous industries,...
View details
HelloPlease log in