line chiller
A Complete Guide to Line Chillers
Line chillers are an essential part of many industrial production lines. They are designed to cool a specific process fluid, usually water or a water – based solution, and maintain a stable temperature within the production line. This precise temperature control is crucial for ensuring the quality and efficiency of various manufacturing processes.
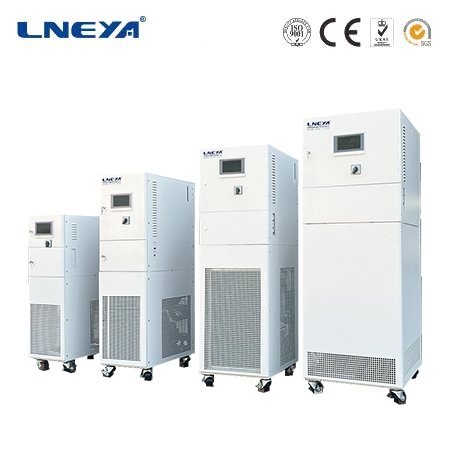
Definition and Function
A line chiller is a cooling device integrated into an industrial production line. Its primary function is to remove heat generated during the manufacturing process. By cooling the process fluid, it helps prevent overheating of equipment, which could lead to equipment failure, reduced product quality, or inefficiencies in the production process. For example, in a food and beverage production line, a line chiller can cool the product or the equipment used in processing, ensuring that the final product meets the required quality standards.
Working Principle
The working principle of a line chiller is based on the principles of heat transfer and refrigeration.
Heat Absorption: The warm process fluid from the production line enters the chiller. Inside the chiller, it passes through a heat exchanger. Here, the heat from the process fluid is transferred to a secondary fluid, which is usually a refrigerant in a closed – loop system.
Refrigeration Cycle: The refrigerant then goes through a vapor – compression refrigeration cycle. First, a compressor compresses the low – pressure refrigerant vapor into a high – pressure, high – temperature vapor. This increases the energy and temperature of the refrigerant. Next, the hot refrigerant vapor enters the condenser. In the condenser, heat is released to a cooling medium, which can be air (in air – cooled line chillers) or water (in water – cooled line chillers). As heat is removed, the refrigerant condenses back into a liquid. Then, the high – pressure liquid refrigerant passes through an expansion valve. The valve reduces the pressure of the refrigerant, causing it to expand rapidly and cool down to a low – pressure, low – temperature state. Finally, the cold refrigerant returns to the heat exchanger to absorb heat from the process fluid again, completing the cycle.
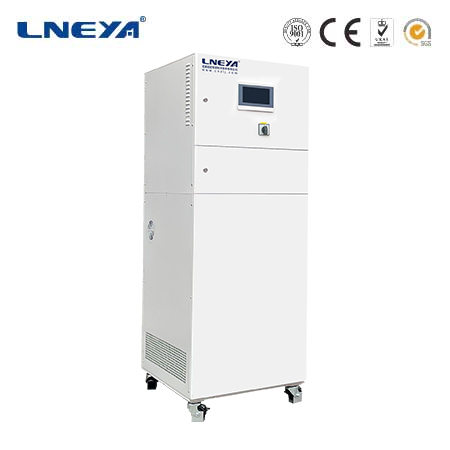
Types of Line Chillers
Air – Cooled Line Chillers
Advantages: Air – cooled line chillers are relatively easy to install as they do not require a complex water – cooling infrastructure. They are suitable for small – to – medium – sized production lines or areas where water is scarce. They are also more compact in design compared to some water – cooled counterparts.
Limitations: However, their cooling efficiency can be affected by high ambient temperatures. When the surrounding air is hot, the ability of the chiller to dissipate heat through air is reduced, which may lead to a decrease in the chiller’s performance. They also tend to be less energy – efficient than water – cooled line chillers in some cases.
Water – Cooled Line Chillers
Advantages: Water – cooled line chillers are highly energy – efficient due to the high heat – transfer capacity of water. They can handle larger cooling loads and are more suitable for large – scale production lines. Their performance is more stable and less affected by ambient temperature changes compared to air – cooled chillers.
Limitations: These chillers require a reliable source of water and a cooling tower or other water – cooling systems. The installation cost is higher due to the need for additional equipment and plumbing. Maintenance is also more complex, involving water treatment to prevent corrosion and scaling in the water – cooling system.
Advantages
Precise Temperature Control: Line chillers can maintain a very precise temperature for the process fluid. This is crucial in industries where even a slight temperature variation can affect product quality. For example, in the pharmaceutical industry, precise temperature control during drug manufacturing is essential to ensure the efficacy and stability of the final product.
Energy – Saving: Modern line chillers are designed with energy – saving features. For instance, some models are equipped with variable – speed drives on compressors and pumps. These drives can adjust the speed based on the actual cooling load, reducing energy consumption when the production line has a lower heat load.
Improved Product Quality: By preventing overheating of equipment and maintaining a stable temperature, line chillers contribute to improving the quality of the final product. In the plastics industry, for example, proper cooling during the molding process can prevent product defects such as warping and shrinkage.
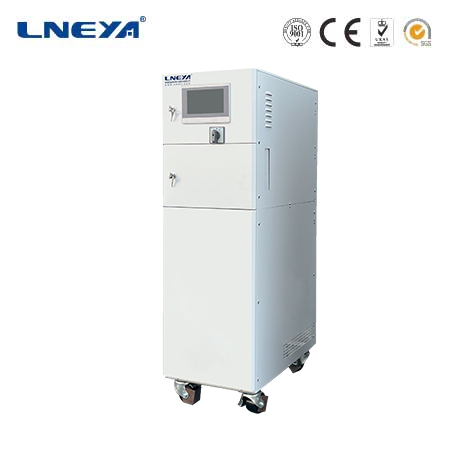
Applications
Food and Beverage Industry: In food processing plants, line chillers are used to cool products such as dairy products, beverages, and processed foods. They are also used to cool the equipment, like pasteurizers and filling machines, to ensure smooth operation and product quality. In breweries, line chillers cool the wort during fermentation and the beer during packaging.
Plastics Industry: In plastic manufacturing, line chillers play a vital role in cooling the molds during injection molding, blow molding, and extrusion processes. Precise cooling helps in achieving the desired shape, size, and quality of the plastic products.
Pharmaceutical Industry: As mentioned earlier, line chillers are used to maintain a stable temperature during drug manufacturing, including the production of tablets, capsules, and liquid medications. They are also used in the storage and transportation of temperature – sensitive pharmaceutical products.
Selection Considerations
Cooling Capacity: Calculate the exact cooling load required for your production line. This involves considering factors such as the heat generated by the equipment, the volume of the process fluid, and the production rate. Oversizing or undersizing the line chiller can lead to inefficiencies and higher operating costs.
Space Requirements: Consider the available space in your production facility. Air – cooled line chillers are more compact, while water – cooled line chillers require additional space for the cooling tower and associated plumbing.
Energy Efficiency: Look for line chillers with high Energy Efficiency Ratio (EER) or Coefficient of Performance (COP) ratings. Energy – efficient chillers can save a significant amount of energy and reduce operating costs over the long term.
Maintenance Requirements: Evaluate the ease of maintenance. Some line chillers may require more frequent maintenance, such as regular cleaning of air – cooled condensers or water treatment for water – cooled systems. The availability of local service providers and spare parts should also be considered.
Maintenance
Regular Inspections: Regularly inspect the line chiller for any signs of leaks, unusual noises, or vibrations. Check the refrigerant levels, oil levels in the compressor, and the condition of the process fluid. Monitor the temperature and pressure readings to ensure the chiller is operating within normal parameters.
Cleaning: Clean the heat exchangers, condensers, and filters regularly. In air – cooled line chillers, clean the air – cooled condensers to remove dust and debris. In water – cooled line chillers, clean the water – cooled condensers and ensure proper water treatment to prevent scaling and corrosion.
Fluid Replacement: Over time, the process fluid or the refrigerant may degrade or become contaminated. Replace the fluids according to the manufacturer’s recommendations to maintain the chiller’s performance.
Professional Servicing: Periodically, have a professional technician perform a comprehensive servicing of the line chiller. This includes checking the electrical components, calibrating the controls, and performing any necessary repairs or adjustments. Professional servicing can help extend the lifespan of the chiller and ensure its reliable operation.
In conclusion, line chillers are an integral part of many industrial production lines. Understanding their working principle, types, advantages, applications, selection criteria, and maintenance requirements is essential for industries to ensure efficient production, high – quality products, and cost – effective operations.
Related recommendations
What temperature sensors are commonly used for lab water chiller?
1082What temperature sensors are commonly used for lab water chiller? Generally speaking, the temperature sensors used in laboratory chillers mainly include the following types: 1. T...
View detailsWhat is the maintenance and inspection of a 200 ton chiller?
1016What is the maintenance and inspection of a 200 ton chiller? 1. Check the stability of voltage and current 2. Regularly inspect the compressor The necessary acceptance tes...
View detailscooling chiller machine
154Introduction to Cooling Chiller MachinesCooling chiller machines are designed to remove heat from a process fluid, usually water or a water - glycol mixture, and transfer it to a secondary fluid ...
View detailscirculating bath chiller
292Circulating Bath Chillers: Consistent Temperature Control for Laboratories Introduction Circulating bath chillers are essential in laboratory settings for their ability to provide precise te...
View details
HelloPlease log in