closed loop water chiller system
A Comprehensive Guide to Closed Loop Water Chiller Systems
Closed loop water chiller systems are widely used in numerous industrial and commercial applications for efficient heat removal and temperature control. These systems play a crucial role in maintaining optimal operating conditions for a variety of equipment and processes.
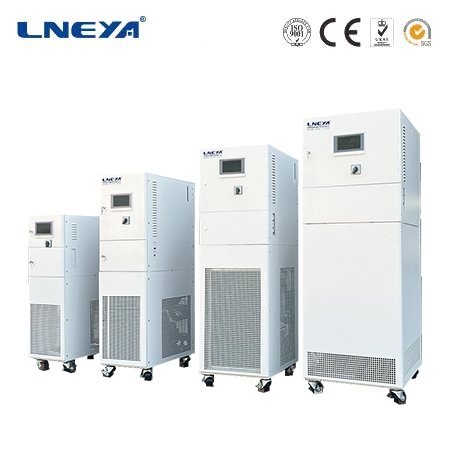
Working Principle
At the core of a closed loop water chiller system is the principle of heat transfer. A closed loop of water is continuously circulated through the system. The process begins when the warm water, which has absorbed heat from the equipment or process needing cooling, returns to the chiller unit. Inside the chiller, the water passes through an evaporator. Here, a refrigerant, operating on the vapor – compression refrigeration cycle, absorbs the heat from the water. The refrigerant vaporizes as it absorbs heat, and the now – cooled water is then pumped back into the loop to repeat the heat – absorption process.
The vapor – compression refrigeration cycle within the chiller consists of four main steps:
Compression: A compressor takes in low – pressure refrigerant vapor and compresses it to a high – pressure, high – temperature state. This increases the energy of the refrigerant and raises its temperature.
Condensation: The hot, high – pressure refrigerant vapor enters the condenser. In the condenser, heat is transferred to a cooling medium, which can be air (in air – cooled chillers) or water (in water – cooled chillers). As heat is removed, the refrigerant condenses back into a liquid.
Expansion: The high – pressure liquid refrigerant passes through an expansion valve. This valve reduces the pressure of the refrigerant, causing it to expand rapidly and cool down to a low – pressure, low – temperature state.
Evaporation: The cold refrigerant enters the evaporator and absorbs heat from the water in the closed loop, as mentioned earlier, thus cooling the water.
System Components
Chiller Unit: This is the central component responsible for cooling the water. It contains the compressor, condenser, expansion valve, and evaporator. The chiller unit can be either air – cooled or water – cooled, with each type having its own advantages and considerations.
Pumps: Pumps are used to circulate the water within the closed loop. They ensure a consistent flow rate of water through the system, which is essential for efficient heat transfer. The pump’s capacity should be carefully selected based on the size of the loop and the required flow rate.
Heat Exchangers: Heat exchangers are used to transfer heat between the water in the closed loop and other fluids or equipment. They can be plate – type, shell – and – tube type, or other specialized designs. Heat exchangers help in maximizing the heat transfer efficiency and can be used in applications where direct contact between the process fluid and the chiller water is not desired.
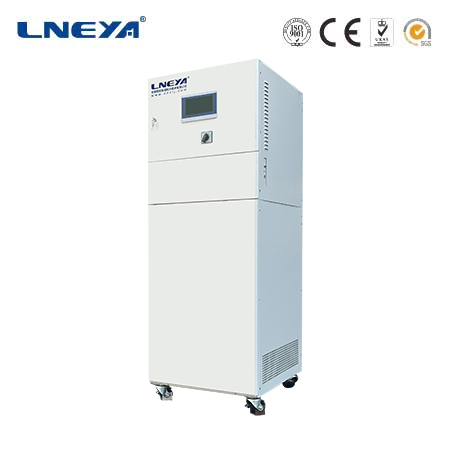
Advantages
Energy Efficiency: Closed loop water chiller systems can be highly energy – efficient. By recirculating the same water, they eliminate the need for continuous water replacement as in open – loop systems. Additionally, modern chiller units are designed with advanced features such as variable – speed drives on pumps and compressors, which can adjust the energy consumption based on the actual cooling load.
Precise Temperature Control: These systems are capable of providing very precise temperature control. The closed loop design allows for better monitoring and regulation of the water temperature, ensuring that the equipment or process being cooled is maintained at a consistent temperature. This is crucial in applications such as pharmaceutical manufacturing and data centers.
Reduced Contamination Risk: Since the water is contained within a closed loop, there is a lower risk of contamination from external sources. This is beneficial in applications where clean water is required, such as in semiconductor manufacturing or in some medical equipment cooling applications.
Applications
Manufacturing Industry: In manufacturing plants, closed loop water chiller systems are used to cool a wide range of equipment. For example, in metal – working processes, they cool high – speed cutting tools to prevent overheating and ensure accurate machining. In plastic injection molding, the systems cool the molds to ensure proper product formation.
Data Centers: Data centers generate a large amount of heat from servers and other electronic equipment. Closed loop water chiller systems are used to maintain the optimal temperature for the servers, preventing overheating and ensuring reliable operation. The precise temperature control provided by these systems is essential for the efficient operation of data center equipment.
Healthcare Facilities: In hospitals and clinics, closed loop water chiller systems are used to cool medical equipment such as MRI machines, CT scanners, and laser surgical devices. These systems help maintain the equipment’s performance and accuracy, which is crucial for patient diagnosis and treatment.
Selection Considerations
Cooling Capacity: Accurately calculate the cooling load required for your application. This involves considering factors such as the heat generated by the equipment, the size of the space or process being cooled, and any external heat sources. Choosing a chiller system with the right cooling capacity is essential to ensure efficient operation.
Water Quality: Since the water is recirculated in a closed loop, water quality is important. Consider the source of water and any potential contaminants. In some cases, water treatment may be necessary to prevent scaling, corrosion, and biological growth in the system.
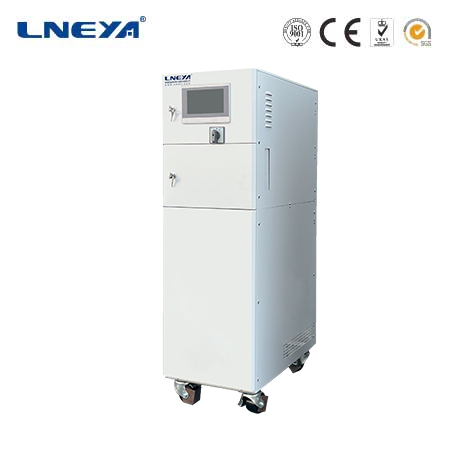
Energy Efficiency: Look for chiller systems with high Energy Efficiency Ratio (EER) or Coefficient of Performance (COP) ratings. Energy – efficient systems can significantly reduce operating costs over time, especially in applications with high – demand cooling requirements.
Maintenance Requirements: Consider the ease of maintenance when selecting a closed loop water chiller system. Some systems may require more frequent maintenance, such as regular cleaning of heat exchangers or replacement of filters. The availability of local service providers and spare parts should also be taken into account.
Maintenance
Regular Inspections: Regularly inspect the system for any signs of leaks, unusual noises, or vibrations. Check the water levels, pump operation, and the condition of the chiller unit. Monitor the temperature and pressure readings to ensure the system is operating within normal parameters.
Water Treatment: If necessary, perform regular water treatment to maintain water quality. This may include adding corrosion inhibitors, biocides, or other chemicals to prevent scaling, corrosion, and biological growth. Regularly test the water quality to ensure the effectiveness of the treatment.
Filter Replacement: Replace the filters in the system as recommended by the manufacturer. Clogged filters can reduce the system’s performance and increase energy consumption. Filters help remove impurities from the water, protecting the system components from damage.
Professional Servicing: Periodically, have a professional technician perform a comprehensive servicing of the chiller system. This includes checking the electrical components, calibrating the controls, and performing any necessary repairs or adjustments. Professional servicing can help identify and address potential issues before they cause major problems.
In conclusion, closed loop water chiller systems are a reliable and efficient solution for heat removal and temperature control in a wide range of applications. Understanding their working principle, components, advantages, applications, selection criteria, and maintenance requirements is essential for making informed decisions and ensuring their long – term, reliable operation.
Related recommendations
temperature control machine
91IntroductionA temperature control machine, also known as a thermostat, is a device designed to maintain a specific temperature within a given environment. It plays a crucial role in various indus...
View detailssingle fluid heating cooling system
131Introduction to Single Fluid Heating Cooling SystemA single fluid heating cooling system is an innovative thermal management approach that relies on a single fluid, such as water, glycol - water ...
View detailsthermal oil heaters
435Understanding Thermal Oil Heaters Thermal oil heaters are a type of heat transfer fluid electric boiler designed to heat process fluids in industrial applications. They operate by using electri...
View detailsflow chiller
71IntroductionIn the realm of modern industrial and commercial operations, maintaining accurate temperature control of flowing media is essential for the smooth running of numerous processes. Flow ...
View details
HelloPlease log in