heater control system
Introduction
In modern heating applications, from industrial processes to residential heating systems, heater control systems play a pivotal role. They are designed to regulate the temperature output of heaters, ensuring that the desired temperature is maintained accurately and efficiently. A well – functioning control system not only enhances the performance of the heater but also contributes to energy savings, safety, and the longevity of the heating equipment.
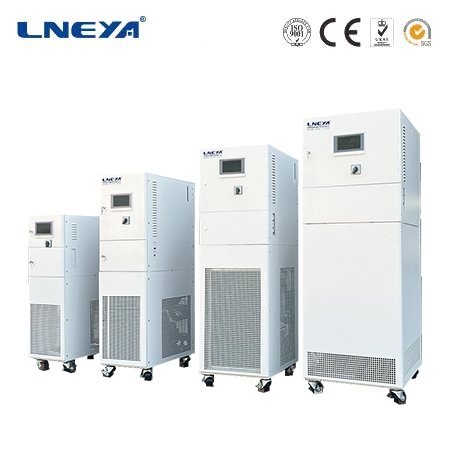
Components of Heater Control Systems
Sensors
Temperature Sensors: These are the most common sensors in heater control systems. They measure the temperature of the heated medium (such as air, water, or a process fluid) or the surface temperature of the heater itself. Common types include thermocouples, which generate a small voltage proportional to the temperature difference between two junctions; resistance temperature detectors (RTDs), whose electrical resistance changes with temperature; and thermistors, which are semiconductor devices with a high temperature – dependent resistance. Temperature sensors provide real – time temperature data to the controller, which uses this information to adjust the heater’s operation.
Other Sensors: Depending on the application, additional sensors may be used. For example, pressure sensors can be employed in systems where the pressure of the heated fluid affects the heating process, such as in steam – based heating systems. Flow sensors are useful in circulation – based heaters to monitor the flow rate of the fluid, ensuring that the heater is operating under the correct conditions. Humidity sensors may also be used in some applications where maintaining a specific humidity level in the heated environment is important.
Controllers
Function and Types: The controller is the brain of the heater control system. It receives input from the sensors, compares it with the setpoint (the desired temperature or other parameter), and generates control signals to adjust the heater’s operation. There are several types of controllers, including simple on – off controllers, which turn the heater on when the measured temperature is below the setpoint and off when it exceeds the setpoint; proportional – integral – derivative (PID) controllers, which offer more precise control by considering the current error, the accumulated error over time, and the rate of change of the error; and advanced digital controllers that can implement complex control algorithms such as fuzzy logic or adaptive control.
Programmability: Modern controllers often have programmable features. This allows users to set different temperature profiles for different times of the day or week, which is especially useful in commercial and industrial applications. For example, in an office building, the heating system can be programmed to lower the temperature during non – working hours and raise it before employees arrive, saving energy while maintaining comfort.
Actuators
Role in the System: Actuators are devices that receive control signals from the controller and physically adjust the heater’s operation. In electric heaters, actuators may control the power supply to the heating elements, for example, by adjusting the voltage or current. In gas – fired heaters, actuators can regulate the flow of gas to the burner, controlling the heat output. In some cases, actuators may also control other components such as fans in forced – air heaters or valves in fluid – based heating systems to optimize the heat transfer process.
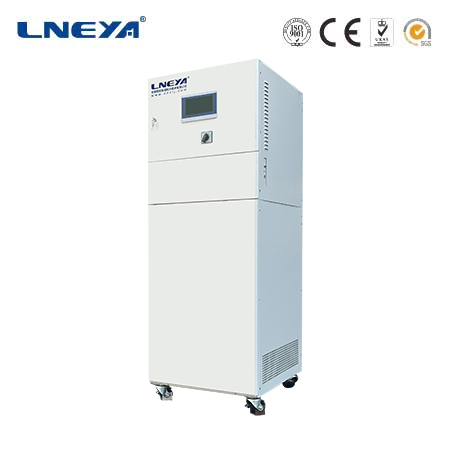
Types of Heater Control Systems
On – Off Control Systems
Working Principle: On – off control is the simplest form of heater control. When the measured temperature is below the setpoint, the controller activates the heater (turns it on), and when the temperature rises above the setpoint, the controller deactivates the heater (turns it off). This type of control creates a cycling effect, where the heater repeatedly turns on and off to maintain the temperature within a certain range around the setpoint.
Advantages and Disadvantages: On – off control systems are easy to implement and require minimal components, making them cost – effective. However, they are not very precise, as the temperature can overshoot or undershoot the setpoint significantly during the on – off cycles. This can lead to temperature fluctuations, which may not be suitable for applications that require a stable temperature, such as laboratory equipment or some industrial processes.
Proportional – Integral – Derivative (PID) Control Systems
Working Principle: PID controllers use a combination of three control actions: proportional, integral, and derivative. The proportional action reacts to the current error (the difference between the setpoint and the measured temperature), adjusting the control output in proportion to the error. The integral action accumulates the error over time and adjusts the control output to eliminate any steady – state error (the difference that remains even when the system has reached a stable state). The derivative action predicts the future trend of the error based on its rate of change and adjusts the control output to prevent overshooting.
Advantages and Applications: PID control systems offer much higher precision compared to on – off systems. They can quickly respond to changes in the setpoint or disturbances in the system and maintain the temperature very close to the desired value. PID controllers are widely used in a variety of applications, including industrial furnaces, water heaters, and HVAC systems in commercial buildings.
Fuzzy Logic Control Systems
Working Principle: Fuzzy logic control systems use a set of linguistic rules to make control decisions, rather than relying on precise mathematical models. These rules are based on human – like reasoning and can handle imprecise or uncertain data. For example, instead of using exact temperature values, fuzzy logic might use terms like “cold,” “warm,” and “hot.” The system evaluates the current state of the heater (such as the measured temperature and its rate of change) and applies the appropriate rules to determine the control action.
Advantages and Use Cases: Fuzzy logic control systems are very adaptable and can perform well in complex or nonlinear systems where traditional control methods may struggle. They are useful in applications where the heating process has variable characteristics or is difficult to model precisely, such as in some chemical processes or in heating systems with changing environmental conditions.
Adaptive Control Systems
Working Principle: Adaptive control systems continuously monitor the performance of the heater and the control system itself. They adjust the control parameters in real – time based on changes in the system’s characteristics or operating conditions. This can involve adapting to changes in the load on the heater, variations in the ambient temperature, or wear and tear of the heating equipment over time.
Advantages and Applications: Adaptive control systems offer high performance and reliability, as they can optimize the heater’s operation under a wide range of conditions. They are commonly used in industrial applications where precise temperature control and efficient operation are critical, such as in semiconductor manufacturing or in large – scale power generation plants.
Key Factors to Consider When Choosing a Heater Control System
Application Requirements
Temperature Range and Stability: Different applications have specific temperature requirements. Some processes may need to maintain a very narrow temperature range with high stability, while others can tolerate more fluctuations. For example, in pharmaceutical manufacturing, precise temperature control is essential to ensure the quality of the products, while in residential heating, a slightly wider temperature range may be acceptable. Choose a control system that can meet the temperature range and stability requirements of your application.
Heater Type and Size: The type and size of the heater also influence the choice of control system. A small electric space heater may only require a simple on – off or basic PID control system, while a large industrial furnace with complex heating requirements may need an advanced adaptive or fuzzy logic control system. Consider the power output, heating elements, and operating characteristics of the heater when selecting a control system.
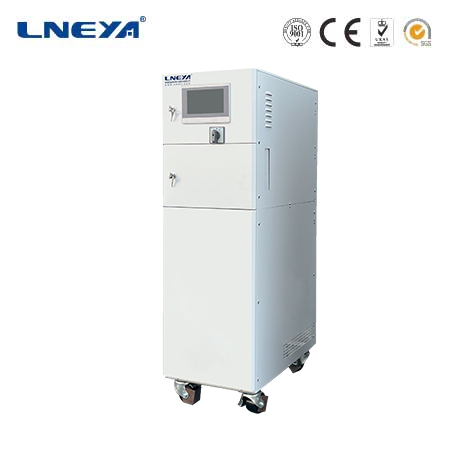
Accuracy and Precision
Measurement Accuracy: The accuracy of the sensors used in the control system is crucial for achieving precise temperature control. Higher – accuracy sensors can provide more reliable temperature data to the controller, enabling it to make more accurate control decisions. However, more accurate sensors also tend to be more expensive. Balance the required measurement accuracy with your budget and application needs.
Control Precision: The control system’s ability to maintain the temperature close to the setpoint is another important factor. As mentioned earlier, different control system types offer varying levels of precision. If your application demands high – precision temperature control, a PID, fuzzy logic, or adaptive control system may be more suitable than a simple on – off system.
Energy Efficiency
Control Strategies: Some control systems are designed to optimize energy consumption. For example, PID controllers can be tuned to minimize the energy used by the heater while still maintaining the desired temperature. Adaptive control systems can adjust the heater’s operation based on real – time energy costs or availability, reducing energy waste. Look for control systems that incorporate energy – saving features or algorithms.
Integration with Energy Management Systems: In some applications, it may be beneficial to integrate the heater control system with a larger energy management system. This allows for centralized control and monitoring of multiple heaters and other energy – consuming devices, enabling more effective energy optimization and cost savings.
Safety and Reliability
Fault Detection and Protection: A good heater control system should have built – in fault – detection mechanisms. This can include overheat protection, which shuts off the heater if the temperature exceeds a safe limit; sensor failure detection, which alerts the operator if a sensor malfunctions; and electrical safety features to prevent short circuits or other electrical hazards. Ensure that the control system you choose meets the necessary safety standards and regulations.
Redundancy and Backup: In critical applications, where the failure of the heater control system could have serious consequences, consider systems with redundancy or backup features. This can include redundant sensors, controllers, or power supplies, which can take over in case of a component failure, ensuring continuous and reliable operation of the heater.
Installation, Operation, and Maintenance of Heater Control Systems
Installation
Professional Installation: Installing a heater control system can be a complex task, especially for advanced systems. It is recommended to have a professional technician with experience in heating systems and control electronics perform the installation. This ensures that the system is installed correctly, with proper wiring, sensor placement, and calibration.
Compatibility Checks: Before installation, verify the compatibility of the control system with the existing heater and other components in the system. This includes checking the electrical ratings, communication protocols (if applicable), and physical dimensions to ensure a proper fit.
Operation
Initial Setup and Calibration: After installation, the control system needs to be set up and calibrated. This involves configuring the setpoint, adjusting the control parameters (for systems like PID controllers), and ensuring that the sensors are providing accurate readings. Follow the manufacturer’s instructions carefully during this process to ensure optimal performance.
Monitoring and Adjustment: Regularly monitor the operation of the heater control system. Check the temperature readings, control outputs, and any error messages or alerts. Based on the monitoring results, make adjustments to the system settings as needed. For example, if the temperature is consistently higher or lower than the setpoint, you may need to fine – tune the control parameters or check for any issues with the sensors or actuators.
Maintenance
Regular Inspections: Conduct routine inspections of the control system components, including sensors, controllers, and actuators. Look for signs of wear and tear, corrosion, or loose connections. Clean the sensors and other components as recommended by the manufacturer to ensure accurate operation.
Component Replacement: Over time, some components of the control system may need to be replaced. This can include batteries in wireless sensors, worn – out actuators, or malfunctioning controllers. Keep spare parts on hand and replace components promptly to prevent system failures.
Software Updates: For digital control systems, software updates may be available to improve performance, add new features, or fix bugs. Regularly check for software updates from the manufacturer and install them as necessary, following the proper procedures to avoid any disruptions to the system.
Conclusion
Heater control systems are integral to the efficient, safe, and precise operation of heaters in a wide range of applications. By understanding the components, types, key selection factors, and proper installation, operation, and maintenance procedures, users can choose the right control system for their specific needs and ensure optimal performance of their heating systems. Whether in industrial, commercial, or residential settings, a well – designed and well – maintained heater control system can significantly enhance the functionality and efficiency of heating equipment while reducing energy consumption and ensuring safety.
Related recommendations
process heating equipment
449Introduction to Process Heating Equipment Process heating is a critical aspect of many industrial operations, where maintaining precise temperatures is necessary for the efficiency and quality ...
View detailswater reservoir chiller
356Water Reservoir Chiller: A Key Component in Temperature Control Introduction to Water Reservoir Chillers Water reservoir chillers are refrigeration apparatuses designed to produce cold water...
View detailschiller control system
305Chiller Control System A chiller control system is an essential part of a refrigeration system that is responsible for maintaining the desired temperature by removing heat from a process or spa...
View detailsWhat are the common solutions to high pressure faults in liquid chiller?
977What are the common solutions to high pressure faults in liquid chiller? Due to insufficient cooling water output, the rated water output cannot be reached. The specific manifestation i...
View details
HelloPlease log in