heater for oil tank
Introduction
Maintaining the right temperature of oil stored in tanks is crucial in numerous industries, including petrochemicals, transportation, and energy. Proper heating prevents oil from thickening or solidifying, which can impede its flow, affect its quality, and cause operational disruptions. Different types of heaters are available to meet the diverse needs of oil tank heating, each with its own characteristics and operational principles.
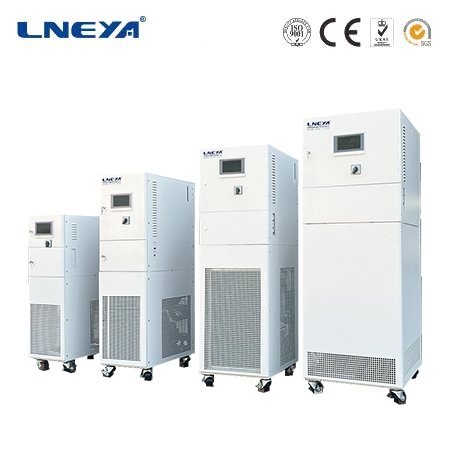
Types of Heaters for Oil Tanks and Their Working Principles
Sub – types and Applications
Immersion Heaters: These are directly inserted into the oil tank. They are highly effective as they transfer heat directly to the oil, providing rapid heating. Immersion heaters are commonly used in small – to medium – sized oil tanks, such as those used in industrial lubricant storage or in heating oil for residential boilers. Their compact design makes them suitable for tanks with limited space.
Jacketed Heaters: Jacketed heaters consist of a heating jacket that surrounds the outside of the oil tank. The jacket is filled with a heat – conducting fluid, which is heated by electric elements. Heat is then transferred from the fluid to the tank wall and subsequently to the oil inside. Jacketed heaters are ideal for larger tanks where uniform heating of the entire oil volume is required, as they distribute heat more evenly across the tank surface. They are often used in commercial fuel storage facilities and in industrial processes where consistent oil temperature is essential.
Steam Heaters
Working Principle: Steam heaters utilize steam, which is generated in a boiler, as the heat source. The steam, at high temperature and pressure, is piped into the oil tank or through a heat exchanger within the tank. As the steam comes into contact with the oil or the heat – exchanger surface, it releases its latent heat, condensing back into water. This heat transfer warms the oil. The condensed water, known as condensate, is then returned to the boiler to be reheated and turned back into steam, creating a continuous cycle. Steam heaters can provide high – intensity heat quickly, making them suitable for applications that require rapid heating of large volumes of oil.
Sub – types and Applications
Coil Heaters: Coil heaters consist of a series of metal coils placed inside the oil tank. Steam flows through these coils, and heat is transferred from the coils to the surrounding oil. Coil heaters are relatively simple in design and can be customized to fit different tank sizes and shapes. They are commonly used in refineries and chemical plants for heating crude oil and other petroleum products during storage and processing.
Steam – Jacketed Tanks: Similar to jacketed electric heaters, steam – jacketed tanks have an outer jacket through which steam circulates. The steam jacket provides even heating around the entire tank, ensuring that the oil inside is uniformly warmed. These are often used in industries where precise temperature control of large volumes of oil is necessary, such as in the food – grade oil storage or in the pharmaceutical industry for heating specialty oils.
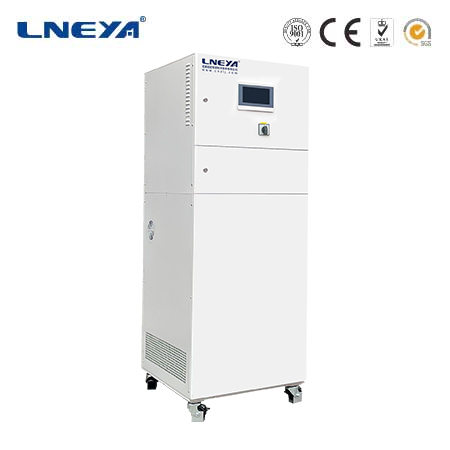
Hot Water Circulation Heaters
Working Principle: Hot water circulation heaters involve heating water in a separate boiler or water heater unit and then circulating it through pipes or coils inside or around the oil tank. Heat is transferred from the hot water to the oil via conduction and convection. The cooled water is then returned to the boiler to be reheated and recirculated. This type of heating system offers a more gentle and controlled heating process compared to steam heaters, as the temperature of the water can be more easily regulated.
Applications: Hot water circulation heaters are suitable for applications where a stable and moderate heating temperature is required. They are commonly used in agricultural settings for heating fuel oil in storage tanks for tractors and other farm equipment. In some commercial buildings with on – site oil – fired heating systems, hot water circulation heaters can be used to maintain the temperature of the heating oil, ensuring a consistent supply for the boilers.
Key Factors to Consider When Choosing an Oil Tank Heater
Tank Size and Capacity
Heating Requirements: Larger oil tanks require heaters with higher heating capacities to ensure that the entire volume of oil can be heated to the desired temperature within a reasonable time frame. The surface area of the tank also affects the heat transfer rate. For example, a cylindrical tank with a large surface – to – volume ratio may lose heat more quickly, necessitating a more powerful heater. When sizing a heater, calculations based on the tank’s dimensions, the specific heat capacity of the oil, and the desired temperature rise are essential.
Installation Space: The available space inside and around the oil tank also impacts the choice of heater. Immersion heaters may be limited by the tank’s internal space, while jacketed heaters require sufficient room around the tank for installation. Consideration must also be given to the placement of associated equipment such as pipes, valves, and control panels for steam and hot water circulation heaters.
Type of Oil
Viscosity and Temperature Sensitivity: Different types of oil have varying viscosity levels and temperature sensitivities. For instance, heavy crude oils have high viscosities and require significant heating to become fluid enough for pumping and processing. On the other hand, some refined oils may degrade if heated to excessively high temperatures. Understanding the properties of the oil being stored is crucial for selecting a heater that can maintain the appropriate temperature range without causing damage to the oil.
Corrosive Properties: Certain oils, especially those containing sulfur or other chemicals, can be corrosive to the materials used in heaters. In such cases, heaters made from corrosion – resistant materials like stainless steel or coated with protective layers are necessary. This ensures the longevity of the heater and prevents contamination of the oil.
Energy Efficiency
Heating Technology: Different heating technologies have varying levels of energy efficiency. Electric heaters may be more efficient for small – scale applications or where electricity is the most readily available energy source. Steam heaters can be highly efficient when there is an existing steam infrastructure, but they may require additional energy for steam generation. Hot water circulation heaters can offer good energy efficiency, especially when combined with energy – saving features such as variable – speed pumps and smart controls.
Insulation: Proper insulation of the oil tank and the heater system is essential for minimizing heat loss. Insulated tanks and pipes reduce the amount of energy required to maintain the oil temperature, thereby improving overall energy efficiency. Look for heaters that come with built – in insulation or consider adding insulation to the existing system to enhance its performance.
Safety Features
Overheat Protection: All oil tank heaters should be equipped with overheat protection mechanisms. This can include thermostats that automatically shut off the heater if the oil temperature exceeds a pre – set limit, preventing damage to the oil and potential safety hazards such as fires or explosions.
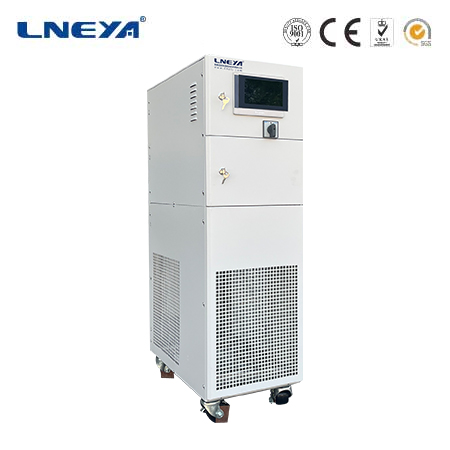
Leak Detection: For steam and hot water circulation heaters, leak detection systems are crucial. Leaks in the steam or water pipes can lead to water or steam ingress into the oil tank, contaminating the oil and causing operational problems. Some advanced heaters are integrated with sensors that can detect leaks and trigger alarms or shut – off mechanisms.
Electrical Safety (for Electric Heaters): Electric heaters must comply with strict electrical safety standards. Features such as grounded electrical connections, insulation of electrical components, and protection against electrical shorts are essential to prevent electrical accidents.
Installation, Operation, and Maintenance of Oil Tank Heaters
Installation
Professional Installation: Given the complexity and potential safety risks associated with oil tank heaters, professional installation is highly recommended. Technicians with experience in heating systems and knowledge of local safety codes can ensure that the heater is installed correctly. This includes proper placement of the heater within or around the tank, secure connection of pipes and electrical wires, and calibration of control systems.
Compliance with Regulations: Different regions have specific regulations regarding the installation of oil tank heaters. These regulations cover aspects such as the distance between the heater and flammable materials, the type of ventilation required, and the proper handling of fuel and electrical connections. Ensuring compliance with these regulations is not only a legal requirement but also essential for the safe operation of the heater.
Operation
Initial Startup: Follow the manufacturer’s instructions carefully during the initial startup of the heater. This may involve filling the system with the appropriate fluid (water for hot water heaters, oil for steam boilers if applicable), checking for leaks, and setting the desired temperature. For electric heaters, ensure that the electrical connections are secure and the power supply is turned on gradually.
Monitoring and Adjustment: Regularly monitor the temperature of the oil, the pressure in the system (for steam and hot water heaters), and the energy consumption of the heater. Based on the monitoring results, make adjustments to the heater settings as needed. For example, if the oil temperature is fluctuating too much, adjust the thermostat settings or the flow rate of the heating medium.
Maintenance
Regular Inspections: Conduct routine inspections of the heater, including checking for signs of wear and tear, corrosion, or leaks. For electric heaters, inspect the heating elements and electrical connections for any damage. In steam and hot water heaters, check the pipes, valves, and pumps for proper functioning. Replace any worn – out or damaged components promptly.
Cleaning: Keep the heater and its associated components clean. For steam and hot water heaters, descale the pipes and heat exchangers periodically to remove mineral deposits that can reduce heat transfer efficiency. In electric heaters, clean the surfaces of the heating elements to ensure optimal heat transfer.
Calibration: Periodically calibrate the temperature sensors and control systems of the heater to ensure accurate temperature control. This helps in maintaining the desired oil temperature and preventing over – or under – heating.
Conclusion
Selecting the right heater for an oil tank is a critical decision that depends on various factors, including tank size, oil type, energy efficiency, and safety requirements. Understanding the different types of heaters available, their working principles, and proper installation, operation, and maintenance procedures is essential for ensuring the efficient and safe heating of oil in storage tanks. By making informed choices and following best practices, industries can maintain the quality of their stored oil, prevent operational disruptions, and enhance overall productivity.
Related recommendations
chiller system operation
385Chiller System Operation: A Comprehensive Guide Chiller systems are indispensable for maintaining comfortable temperatures in commercial buildings, industrial processes, and data centers. These...
View detailswater to water chiller
178Introduction Water to water chillers are sophisticated systems designed to transfer heat from one water source (the warm water) to another (the cool water), thereby reducing the temperature of...
View detailschiller engineering
363Chiller Engineering: An In-Depth Analysis Chiller engineering is a specialized field within the broader domain of heating, ventilation, and air conditioning (HVAC) systems. Chillers are essenti...
View details40 ton air cooled chiller
82Working PrincipleThe 40 ton air cooled chiller operates on the vapor-compression refrigeration cycle, which involves four main stages:Compression: The compressor takes in low-pressure, low-tempe...
View details
HelloPlease log in