glycol chiller systems
Glycol Chiller Systems: A Comprehensive Overview
Glycol chiller systems are specialized cooling systems that utilize glycol – based solutions as secondary coolants to transfer heat and maintain desired temperature levels. These systems have become increasingly popular in a wide range of industrial and commercial applications due to their ability to operate efficiently in low – temperature environments and provide effective freeze protection. Whether it’s for cooling sensitive pharmaceutical products, maintaining optimal temperatures in data centers, or preserving the quality of food and beverages, glycol chiller systems play a crucial role in ensuring reliable and consistent cooling performance.
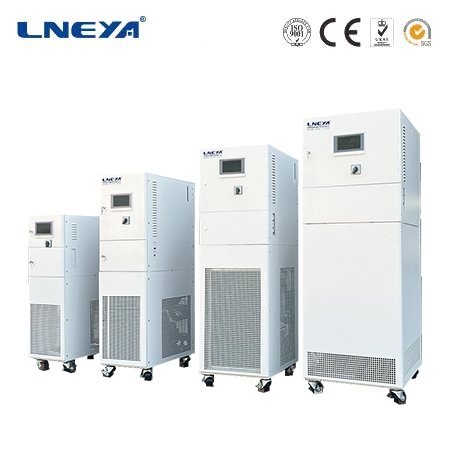
Working Principles of Glycol Chiller Systems
The Refrigeration Cycle
At the core of glycol chiller systems is the refrigeration cycle, which involves several key components and processes. The cycle begins with the compressor, which raises the pressure and temperature of the refrigerant gas. The high – pressure, high – temperature refrigerant then enters the condenser, where it releases heat to the surrounding environment or a cooling medium (such as air in air – cooled systems or water in water – cooled systems). As the refrigerant gives off heat, it condenses into a high – pressure liquid.
The high – pressure liquid refrigerant then passes through an expansion valve or device. This causes a sudden drop in pressure, resulting in the refrigerant evaporating and cooling down significantly. The low – temperature, low – pressure refrigerant then enters the evaporator. In the evaporator, instead of directly cooling the medium to be cooled, the refrigerant transfers its coldness to a glycol – water solution. The glycol solution, acting as a secondary coolant, absorbs heat from the refrigerant and becomes cooled. This cooled glycol solution is then pumped through a closed – loop system to the areas or processes that require cooling, where it absorbs heat from the target medium and returns to the evaporator to repeat the cycle.
Role of Glycol
Glycol, typically ethylene glycol or propylene glycol, is added to water to create a coolant solution with enhanced properties. One of the primary advantages of glycol is its ability to lower the freezing point of water. This is crucial in applications where the coolant needs to operate at sub – zero temperatures without freezing, preventing damage to the chiller system and the associated pipes and equipment. Additionally, glycol has good heat – transfer properties, allowing it to efficiently absorb and transfer heat between the evaporator and the cooling load. The concentration of glycol in the solution can be adjusted based on the required operating temperature range, with higher concentrations providing greater freeze protection but also affecting the solution’s viscosity and heat – transfer efficiency.
Types of Glycol Chiller Systems
Air – Cooled Glycol Chiller Systems
Air – cooled glycol chiller systems use ambient air as the medium for heat rejection. These systems are relatively easy to install as they do not require a separate water supply for heat dissipation. The condenser in an air – cooled chiller is equipped with fans that blow air over the condenser coils. As the high – pressure, high – temperature refrigerant from the compressor enters the condenser, heat is transferred from the refrigerant to the air passing over the coils, causing the refrigerant to condense.
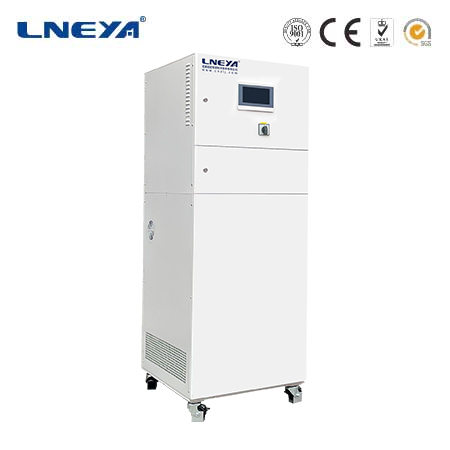
Air – cooled glycol chillers are suitable for locations where water is scarce or where the installation of a water – cooling system is impractical. However, they tend to be less energy – efficient compared to water – cooled systems, especially in hot and humid climates, as the efficiency of heat transfer to air depends on the ambient air temperature. They are commonly used in small – to medium – sized industrial facilities, commercial buildings, and some outdoor applications where access to a water source is limited.
Water – Cooled Glycol Chiller Systems
Water – cooled glycol chiller systems rely on water as the heat – rejection medium. In these systems, the condenser transfers heat from the refrigerant to a separate water loop. The heated water from the condenser is then typically sent to a cooling tower, where heat is dissipated into the atmosphere through evaporation. Water – cooled glycol chillers are more energy – efficient than air – cooled ones because water has a higher heat – carrying capacity than air, allowing for more effective heat transfer.
They are often used in large – scale industrial applications, data centers, and facilities where a consistent and high – capacity cooling solution is required. However, water – cooled systems require more complex installation and maintenance, including the management of the water – cooling system, such as ensuring proper water quality to prevent scaling and corrosion in the pipes and condenser.
Components of Glycol Chiller Systems
Compressor
The compressor is a vital component that drives the refrigeration cycle. It compresses the low – pressure, low – temperature refrigerant gas, increasing its pressure and temperature. Compressors can be of different types, such as reciprocating, screw, or centrifugal. Reciprocating compressors use pistons to compress the refrigerant and are suitable for smaller – scale chiller systems. Screw compressors, with their intermeshing rotors, offer a good balance between capacity and efficiency and are commonly used in medium – to large – sized systems. Centrifugal compressors are known for their high – capacity cooling capabilities and are often employed in large industrial and commercial applications.
Condenser
The condenser is responsible for converting the high – pressure, high – temperature refrigerant gas into a liquid by removing heat. In air – cooled condensers, the heat is transferred to the ambient air through the condenser coils and fans. In water – cooled condensers, heat is transferred to the water, which then carries the heat away to a cooling tower or other heat – rejection device. The design of the condenser, including the type of tubes, fin configuration (in air – cooled condensers), and surface area, significantly impacts the efficiency of heat transfer and the overall performance of the chiller system.
Evaporator
The evaporator is where the heat exchange between the refrigerant and the glycol solution occurs. The low – temperature, low – pressure refrigerant absorbs heat from the glycol solution, causing the glycol to cool down. The design of the evaporator, similar to the condenser, affects the rate and efficiency of heat transfer. Shell – and – tube evaporators, plate evaporators, and finned – tube evaporators are common types used in glycol chiller systems, each with its own advantages in terms of heat – transfer performance, compactness, and ease of maintenance.
Expansion Valve
The expansion valve plays a crucial role in regulating the flow of the refrigerant and reducing its pressure. It controls the amount of refrigerant that enters the evaporator, ensuring that the refrigerant evaporates completely and efficiently absorbs heat from the glycol solution. Different types of expansion valves, such as thermal expansion valves and electronic expansion valves, are used depending on the specific requirements of the chiller system. Electronic expansion valves offer more precise control and better performance in variable – load applications.
Glycol Pump
The glycol pump is responsible for circulating the glycol solution through the closed – loop system. It ensures that the cooled glycol reaches the areas that need cooling and that the heated glycol is returned to the evaporator for re – cooling. The size and capacity of the glycol pump need to be carefully selected based on the flow rate and pressure requirements of the system to ensure efficient heat transfer and proper operation of the cooling process.
Applications of Glycol Chiller Systems
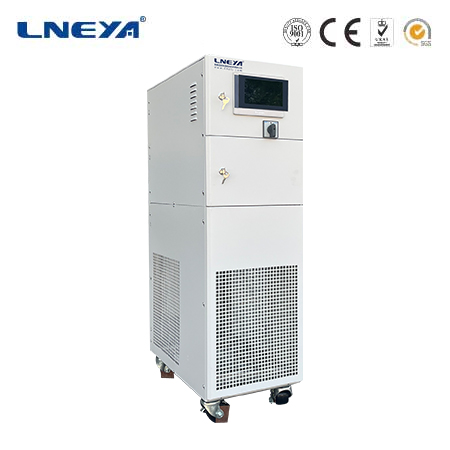
Food and Beverage Industry
In the food and beverage industry, glycol chiller systems are used for various purposes. They are essential for cooling and freezing food products during processing, storage, and transportation. For example, in meat processing plants, glycol – cooled systems are used to rapidly chill freshly slaughtered meat to prevent the growth of bacteria and maintain its quality. In breweries, glycol chillers cool the wort during the brewing process and maintain the cold temperatures required for storing and dispensing beer. They also play a crucial role in the production of ice cream and other frozen desserts, ensuring the proper freezing and texture of the products.
Pharmaceutical Industry
The pharmaceutical industry relies on glycol chiller systems to maintain the stability and integrity of drugs and biological products. Many pharmaceutical compounds are sensitive to temperature changes, and precise temperature control is required during manufacturing, storage, and distribution. Glycol chillers are used to cool reactors during chemical synthesis, maintain the cold storage temperatures of vaccines and other temperature – sensitive medications, and ensure the proper functioning of equipment such as centrifuges and freezers.
Data Centers
Data centers generate a significant amount of heat from servers and other IT equipment. Glycol chiller systems are increasingly being used in data centers as an efficient and reliable cooling solution. The glycol – based coolant can be circulated through heat exchangers to cool the air or directly cool the servers, helping to maintain the optimal temperature and humidity levels required for the proper operation of the equipment. This not only prevents overheating and potential data loss but also extends the lifespan of the IT infrastructure.
Industrial Processes
In various industrial processes, glycol chiller systems are used to cool machinery, equipment, and process fluids. For example, in metalworking industries, they cool cutting tools and lubricants to prevent overheating and improve the quality of the machining process. In the plastics industry, glycol chillers are used to cool molds during injection molding and blow molding operations, ensuring the proper shaping and quality of the plastic products. They are also used in chemical plants to cool reactors, condensers, and other process equipment to maintain the desired reaction temperatures and prevent hazardous situations.
Selection Criteria for Glycol Chiller Systems
Cooling Capacity
Determining the appropriate cooling capacity is the first and most critical step in selecting a glycol chiller system. It is essential to accurately calculate the total heat load of the processes or equipment that need to be cooled. Factors such as the size of the facility, the number and type of heat – generating equipment, the ambient temperature, and the required temperature setpoint all contribute to the heat load calculation. An undersized chiller system will not be able to provide sufficient cooling, leading to overheating and potential system failures, while an oversized system will result in higher initial costs, increased energy consumption, and unnecessary waste.
Temperature Requirements
Different applications have specific temperature requirements for the glycol solution. Some processes may require extremely low temperatures, while others need only moderate cooling. It is important to choose a glycol chiller system that can maintain the required temperature within a narrow tolerance range. Additionally, the system should be able to handle temperature fluctuations and maintain stability under varying load conditions to ensure consistent performance and product quality.
Glycol Concentration and Compatibility
The choice of glycol type (ethylene glycol or propylene glycol) and its concentration in the solution depends on the operating temperature range and the specific requirements of the application. Higher glycol concentrations provide greater freeze protection but can also increase the solution’s viscosity, affecting heat – transfer efficiency and pump performance. It is also crucial to ensure that the glycol solution is compatible with the materials used in the chiller system, such as pipes, valves, and seals, to prevent corrosion and degradation over time.
Energy Efficiency
Energy efficiency is a significant consideration, as glycol chiller systems can consume a substantial amount of energy, especially in large – scale applications. Look for systems with high – efficiency components, such as variable – speed compressors and pumps, which can adjust their operation based on the actual cooling demand, reducing energy consumption during periods of low load. Energy – efficiency ratings, such as the Coefficient of Performance (COP) or the Energy Efficiency Ratio (EER), can be used to compare the energy efficiency of different chiller systems. Selecting an energy – efficient system not only helps reduce operating costs but also has a lower environmental impact by consuming less electricity.
Installation and Space Requirements
The available space for installing the glycol chiller system is an important factor. Some systems, especially large – scale water – cooled chillers with cooling towers, require significant floor space and may need to be installed outdoors. Air – cooled chillers are generally more compact and can be installed indoors in some cases. The installation process should also comply with local building codes, safety regulations, and environmental standards. Consideration should be given to factors such as access for maintenance, ventilation, and the connection of pipes and electrical wiring.
Maintenance Requirements
Regular maintenance is necessary to keep glycol chiller systems operating efficiently and reliably. Consider the ease of maintenance when choosing a system. Systems with easily accessible components, clear maintenance instructions, and a reliable supply of spare parts will be more convenient and cost – effective to maintain. Some manufacturers offer comprehensive maintenance services and training programs for operators, which can be beneficial for ensuring the proper operation and longevity of the system. Additionally, the frequency of maintenance tasks, such as cleaning, inspection, and replacement of components, should be taken into account when making a selection.
Installation, Maintenance, and Safety Considerations
Installation
Proper installation of a glycol chiller system is essential for its optimal performance and longevity. The installation process should be carried out by trained professionals who are familiar with the specific requirements of the system and local installation codes. Key installation considerations include ensuring correct alignment and connection of pipes, proper electrical wiring, and adequate ventilation for air – cooled systems.
For water – cooled systems, the installation of cooling towers, pumps, and water – treatment equipment should be carefully coordinated. The glycol pipes should be properly insulated to prevent heat losses and condensation, which can lead to corrosion and other problems. The chiller unit should be installed on a stable foundation to minimize vibration and noise. Additionally, the system should be filled with the appropriate glycol – water solution at the correct concentration, and all components should be checked for leaks before startup.
Maintenance
Regular maintenance is crucial to keep glycol chiller systems running smoothly. Maintenance tasks typically include checking and adjusting the refrigerant levels and pressures, inspecting and cleaning the condenser and evaporator coils, monitoring the glycol solution for concentration, pH, and contaminants, and lubricating moving parts such as pumps and fans. The glycol solution should be tested and replenished or replaced periodically to ensure proper freeze protection and heat – transfer performance.
The compressor, expansion valve, and other critical components should also be inspected regularly for signs of wear or malfunction. A well – planned maintenance schedule, based on the manufacturer’s recommendations and the operating conditions of the system, can help prevent breakdowns, extend the system’s lifespan, and maintain its energy efficiency.
Safety Considerations
Safety is of utmost importance when using glycol chiller systems. Glycol solutions, especially ethylene glycol, can be toxic if ingested or inhaled in large quantities. Appropriate safety measures should be taken during handling, such as wearing protective gloves and goggles, and ensuring proper ventilation. In case of a spill, the glycol should be cleaned up promptly using appropriate absorbent materials, and the area should be thoroughly rinsed.
The chiller system itself also poses potential hazards, such as high – voltage electrical components and high – pressure refrigerant lines. All electrical work should be carried out by qualified electricians, and proper grounding should be ensured. Pressure relief valves and other safety devices should be regularly inspected and tested to ensure they are functioning properly. In case of any malfunction or abnormal operation, the system should be shut down immediately, and a qualified technician should be called for inspection and repair.
In conclusion, glycol chiller systems are essential for efficient and reliable cooling in a wide range of applications. Understanding their working principles, types, components, applications, selection criteria, and aspects related to installation, maintenance, and safety is crucial for making informed decisions and ensuring the optimal performance of these systems. By carefully considering these factors, industries and businesses can choose the right glycol chiller system for their specific needs, optimize its operation, and contribute to energy – efficient and sustainable cooling solutions.
Related recommendations
Why does the lab water chiller compressor burn out?
1050Why does the lab water chiller compressor burn out? 1. One of the reasons is that due to a lack of phase, prolonged use can lead to burnout. The refrigeration compressor has correspondi...
View detailssmall chiller plant
513Small Chiller Plant: Selection and Efficiency A small chiller plant is an essential component of heating, ventilation, and air conditioning (HVAC) systems, particularly where precise temperatur...
View detailsheating and cooling cooler
498Heating and Cooling Coolers: Versatile Temperature Control Solutions Heating and cooling coolers are engineered systems designed to maintain precise temperature control in a variety of settings...
View detailsWhat is the refrigeration capacity of a small water chiller related to?
962What is the refrigeration capacity of a small water chiller related to? The cooling capacity of small chillers is mainly related to the following factors: 1. Equipment cooling po...
View details
HelloPlease log in