chiller factory
Chiller Factory: An In-depth Look
Importance of Chillers
Chillers play a vital role in numerous sectors. In the HVAC industry, they are used to cool buildings, providing comfortable indoor environments. In manufacturing, they are essential for processes like plastic molding and metalworking, where precise temperature control is crucial to ensure product quality. In the pharmaceutical industry, chillers are utilized to maintain the required temperature for drug production and storage. Data centers also rely on chillers to keep servers and other equipment from overheating, ensuring their stable operation.
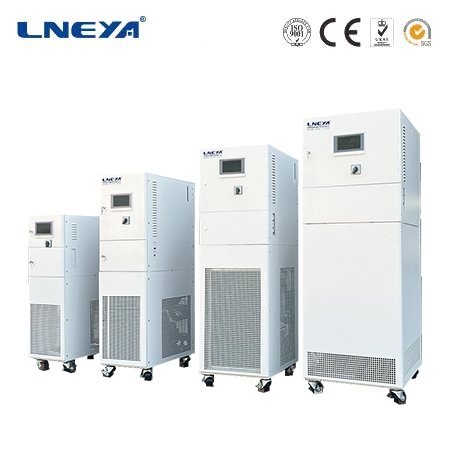
Manufacturing Process
Design and Planning
Needs Assessment: Understanding the specific cooling needs of the intended application, including thermal load, temperature range, flow rates, and environmental conditions.
Conceptual Design: Selecting the chiller type (air-cooled or water-cooled) and refrigeration cycle (vapor-compression or absorption), and defining key components.
Detailed Engineering: Creating detailed engineering drawings and 3D models using CAD, and conducting thermal analysis, fluid dynamics simulations, and structural integrity assessments.
Material Selection
Refrigerants: Choosing refrigerants like R-134a, R-410a, or ammonia based on cooling capacity, efficiency, environmental regulations, and safety.
Structural Materials: Using stainless steel, aluminum, or galvanized steel for the chiller’s frame and housing for durability and corrosion resistance.
Heat Exchanger Materials: Selecting copper, aluminum, titanium, or stainless steel for heat exchangers due to their high thermal conductivity and corrosion resistance.
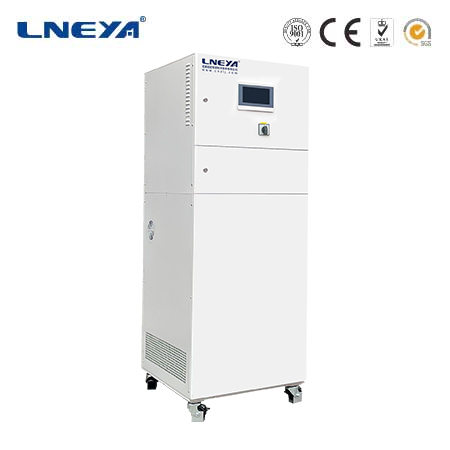
Component Manufacturing
Compressors: Precision manufacturing of reciprocating, screw, or centrifugal compressors, involving machining, assembly, and quality control.
Heat Exchangers: Manufacturing evaporators and condensers through brazing, welding, and finning, or using microchannel fabrication for better efficiency.
Expansion Valves: Producing expansion valves with high precision for accurate refrigerant flow control, including machining, assembly, and testing.
Assembly
Frame and Housing Assembly: Assembling the frame and housing first, and then mounting components like the compressor and heat exchangers.
Piping and Refrigerant Circuit: Connecting components with pipes, forming the refrigerant circuit, and conducting leak testing and insulation.
Electrical and Control Systems: Installing the electrical system, including control panels, sensors, and wiring, and integrating PLCs for automation and monitoring.
Testing and Quality Assurance
Initial Testing: Verifying component installation and refrigerant circuit integrity through pressure, leak, and electrical tests.
Performance Testing: Ensuring the chiller meets specified cooling capacity and efficiency by running it under various load conditions.
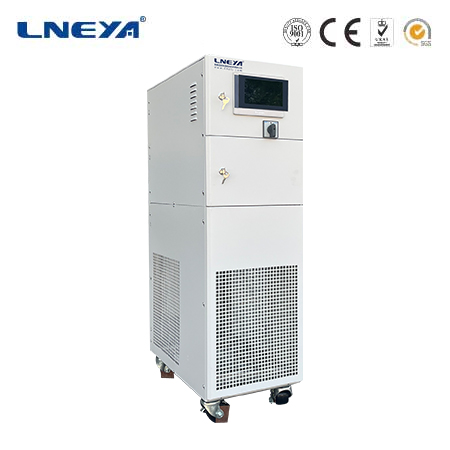
Final Inspection and Certification: Checking all aspects of the chiller and certifying it for compliance with industry standards.
Types of Chillers Produced
Air-Cooled Chillers: These use ambient air to dissipate heat from the refrigerant. They are convenient for smaller installations or where water is scarce, require less maintenance and no cooling towers, and are easier to install.
Water-Cooled Chillers: They utilize water from an external source, like a cooling tower, to release heat. They are more energy-efficient but need additional infrastructure.
Vapor Absorption Type Chillers: Often used in applications where there is a large supply of low-grade heat energy, such as in some industrial processes or in areas with access to waste heat. They are relatively quiet and have lower maintenance requirements compared to vapor compression chillers.
Vapor Compression Type Chillers: This is the most common type, which includes reciprocating, screw, and centrifugal compressors. They offer high cooling capacity and efficiency and are widely used in various industries.
Quality Control in Chiller Factories
Quality control is of utmost importance in chiller factories. Manufacturers need to use high-quality accessories and ensure that each component meets the preset service environment requirements. Strict adherence to industry standards such as ASME, CE, and UL is necessary. Regular inspections and tests should be carried out throughout the manufacturing process to identify and correct any potential issues promptly, ensuring that the final products are reliable and efficient.
Related recommendations
40 ton water cooled chiller
126IntroductionIn the domain of cooling systems, 40 - ton water cooled chillers play a vital role in meeting the significant cooling demands of various mid - to - large - scale applications. With a ...
View detailstemperature process control system
321Temperature Process Control Systems: Ensuring Precision in Industrial Processes Temperature process control systems are essential in maintaining the precise temperature conditions required for ...
View detailsexternal chiller
447Closed-Cycle Cooling Water System: Precision Temperature Control for Diverse Applications A closed-cycle cooling water system, often referred to as a recirculating water bath chiller, is an ess...
View detailslab chillers
129Lab Chillers: A Comprehensive GuideLab chillers are specialized cooling systems designed to provide accurate and stable temperature control in laboratory environments. These chillers play a vital...
View details
HelloPlease log in