compressor heater
Compressor Heater
In mechanical systems where compressors play a crucial role, the performance and longevity of these devices can be significantly influenced by temperature conditions. Compressor heaters are specialized equipment designed to maintain the optimal operating temperature of compressors, ensuring smooth and efficient operation across a wide range of applications.
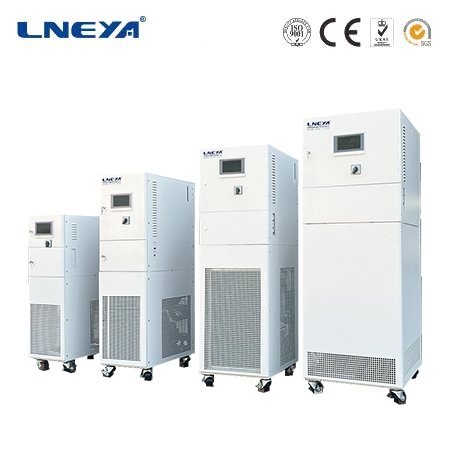
Working Principle
The primary function of a compressor heater is to warm up the compressor’s lubricating oil and other critical components. In cold environments or during startup after a long period of inactivity, the lubricating oil can become highly viscous. High – viscosity oil restricts the free movement of the compressor’s internal parts, leading to increased friction, higher energy consumption, and potential mechanical failures.
Compressor heaters work by transferring heat to the oil and components. When the heater is activated, it raises the temperature of the lubricant, reducing its viscosity and allowing it to flow freely. This ensures that all moving parts within the compressor are properly lubricated, minimizing wear and tear and enabling the compressor to start and run smoothly. Additionally, maintaining the right temperature helps prevent condensation inside the compressor, which can cause corrosion and damage to sensitive components over time.
Types of Compressor Heaters
Electrical Resistance Heaters: These are one of the most common types of compressor heaters. They operate on the principle of generating heat when an electric current passes through a resistive element. The resistive material, often made of nichrome wire or similar alloys, converts electrical energy into heat energy. Electrical resistance heaters can be installed in various ways, such as wrapping them around the compressor housing or placing them near the oil sump. They are relatively simple in design, cost – effective, and can provide a consistent heat output. However, they may have limitations in terms of heat distribution uniformity, especially for larger compressors.
Silicone Rubber Heaters: Silicone rubber heaters are flexible and can be customized to fit the shape of the compressor. They consist of a heating element embedded within a silicone rubber matrix. This type of heater offers excellent heat transfer properties and can conform closely to the surface of the compressor, ensuring even heat distribution. Silicone rubber heaters are often used in applications where space is limited or where a more precise fit is required. They are also resistant to moisture, chemicals, and mechanical stress, making them suitable for harsh operating environments. However, they may be more expensive compared to electrical resistance heaters.
Immersion Heaters: Immersion heaters are designed to be directly submerged in the lubricating oil of the compressor. They transfer heat directly to the oil, providing rapid and efficient heating. These heaters are typically made of a metal sheath with a heating element inside, and they are equipped with safety features such as temperature sensors to prevent overheating. Immersion heaters are highly effective in quickly reducing the viscosity of the oil, but their installation may require more complex procedures as they need to be properly sealed to prevent oil leakage.
Applications
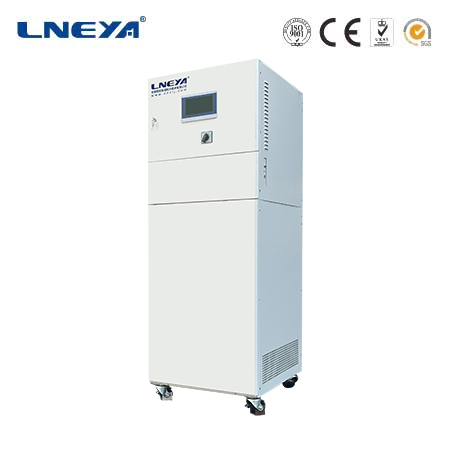
Refrigeration and Air – Conditioning Systems: In refrigeration and air – conditioning units, compressors are the heart of the system. During cold weather or when the unit has been idle for a while, compressor heaters are used to ensure that the compressor can start smoothly. For example, in commercial refrigeration systems used in supermarkets, compressor heaters prevent the oil from thickening in the cold storage environment, allowing the compressors to operate efficiently and maintain the required low temperatures for food preservation.
Oil and Gas Industry: In the oil and gas sector, compressors are used for various purposes, such as gas compression and pipeline transportation. Compressor heaters are essential in regions with low ambient temperatures. They help maintain the temperature of the compressor lubricants, enabling the compressors to function properly even in freezing conditions. This is crucial for ensuring the continuous operation of oil and gas production facilities and transportation systems.
Manufacturing Plants: In manufacturing plants, compressors are widely used to power pneumatic tools, operate robotic systems, and perform other industrial processes. Compressor heaters are employed to keep the compressors running efficiently, especially in facilities where temperature fluctuations occur. By maintaining the optimal temperature, the heaters help reduce maintenance costs associated with compressor failures and ensure the smooth flow of production operations.
Marine Applications: On ships and other marine vessels, compressors are used for functions like air conditioning, engine starting, and cargo handling. Compressor heaters are necessary to prevent the negative effects of cold seawater and low – temperature marine environments on compressor performance. They ensure that the compressors can operate reliably, which is vital for the safety and functionality of the entire vessel.
Advantages
Improved Compressor Performance: By maintaining the proper temperature of the lubricants and components, compressor heaters enhance the overall performance of the compressor. Reduced friction leads to lower energy consumption, increased efficiency, and improved compression ratios. This results in better system performance and can contribute to cost savings in the long run.
Extended Compressor Lifespan: Proper lubrication due to the action of the compressor heater minimizes wear and tear on the compressor’s internal parts. Reducing mechanical stress and preventing damage from factors like high – viscosity oil or condensation helps extend the lifespan of the compressor. This reduces the frequency of replacements and associated maintenance costs.
Reliable Operation in Harsh Conditions: Compressor heaters enable compressors to operate reliably in extreme temperatures, whether it’s the cold of winter or the heat of summer. In cold environments, they ensure easy startup, while in hot conditions, they can help prevent overheating – related issues. This reliability is crucial for industries where continuous operation is essential.
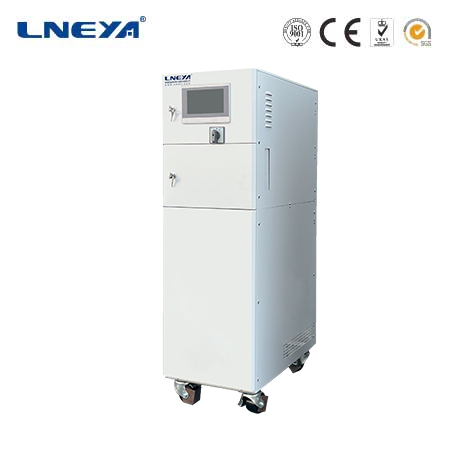
Limitations and Considerations
Energy Consumption: Compressor heaters consume electrical energy, and in some cases, this can add to the overall operating costs of the system. For large – scale applications with multiple compressors, the cumulative energy consumption of the heaters can be significant. Therefore, it’s important to select heaters with energy – efficient designs and consider their usage patterns to optimize energy usage.
Installation Complexity: Depending on the type of compressor heater, installation can range from relatively simple to quite complex. Immersion heaters, for example, require careful installation to prevent oil leakage and ensure proper sealing. Additionally, some heaters may need to be integrated with the compressor’s control system, which can add to the installation and setup requirements.
Maintenance Requirements: Regular maintenance is necessary to ensure the proper functioning of compressor heaters. This includes checking for electrical faults, inspecting the heater elements for wear and tear, and ensuring that the temperature sensors are working correctly. Failure to perform maintenance can lead to heater malfunctions, which in turn can affect the performance of the compressor.
In conclusion, compressor heaters are an integral part of maintaining the optimal performance and reliability of compressors in diverse applications. Understanding their working principles, types, applications, advantages, and limitations is essential for making informed decisions regarding their selection, installation, and maintenance. By properly utilizing compressor heaters, industries can ensure the smooth operation of their compressor – based systems, reduce costs, and extend the lifespan of their valuable equipment.
Related recommendations
temperature control chamber
145Temperature Control Chamber: A Comprehensive Guide Temperature control chambers play a crucial role in numerous industries and scientific research endeavors by providing a controlled environme...
View detailsWhat is the maintenance method for non circulating cold water in chiller for laboratory?
925What is the maintenance method for non circulating cold water in chiller for laboratory? The water level in the water tank is lower than the water inlet of the water pump Solutio...
View detailsclosed loop chilled water cooling system
392Closed-Loop Chilled Water Cooling Systems: A Comprehensive Guide Closed-loop chilled water cooling systems are an essential technology for controlling and maintaining temperatures in a variety ...
View detailsindustrial circulation heaters
237Industrial circulation heaters play a critical role in a wide array of industrial applications where temperature control of fluids is necessary. These heaters are designed to heat moving or circul...
View details
HelloPlease log in