40 ton chiller
A 40 – ton chiller is a substantial cooling system designed to remove a significant amount of heat from a space or process. The “40 – ton” rating refers to its cooling capacity, where 1 ton of cooling is equivalent to 12,000 British Thermal Units per hour (BTU/h). So, a 40 – ton chiller has a cooling capacity of 480,000 BTU/h. These chillers are widely used in various applications where a large – scale cooling solution is required.
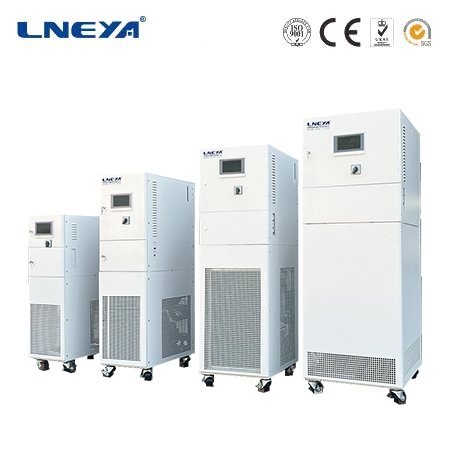
Working Principles of 40 – Ton Chillers
2.1 Vapor – Compression Chillers
Compression: In a vapor – compression 40 – ton chiller, the process begins with a low – pressure, low – temperature refrigerant vapor. A compressor sucks in this vapor and compresses it, increasing its pressure and temperature. As the refrigerant is compressed, work is done on it, and its internal energy rises. For a 40 – ton chiller, the compressor is sized appropriately to handle the large volume of refrigerant required to achieve the 480,000 BTU/h cooling capacity.
Condensation: The high – pressure, high – temperature refrigerant vapor then enters the condenser. In the condenser, the refrigerant releases heat to a cooling medium. In air – cooled models, ambient air is used, and fans blow air over the condenser coils to dissipate the heat. In water – cooled models, water is the cooling medium, and the heat is transferred to the water, which is then cooled in a cooling tower or a water – cooled heat exchanger. The refrigerant condenses back into a high – pressure liquid state during this process.
Expansion: The high – pressure liquid refrigerant passes through an expansion valve. The expansion valve reduces the pressure of the refrigerant, causing it to expand rapidly. This expansion leads to a drop in the refrigerant’s temperature, and it enters the evaporator as a low – pressure, low – temperature liquid – vapor mixture.
Evaporation: In the evaporator, the low – pressure refrigerant absorbs heat from the process fluid or the air that needs to be cooled. As it absorbs heat, the refrigerant evaporates and turns back into a low – pressure vapor. This cooled process fluid or air can then be used for cooling purposes, such as in air – conditioning systems for large buildings or in industrial cooling processes.
2.2 Absorption Chillers
Absorption: Absorption 40 – ton chillers operate on a different principle. In the absorber, a refrigerant (usually water in water – lithium bromide systems or ammonia in ammonia – water systems) is absorbed by an absorbent solution. This absorption process releases heat, which is removed by a cooling medium, typically water.
Generation: The rich absorbent – refrigerant solution is then pumped to the generator. Heat is applied to the generator, which can come from a waste heat source, solar energy, or natural gas. The heat causes the refrigerant to vaporize from the absorbent solution. The high – pressure refrigerant vapor then moves to the condenser.
Condensation: Similar to vapor – compression chillers, in the condenser, the high – pressure refrigerant vapor releases heat and condenses into a liquid state.
Expansion: The high – pressure liquid refrigerant passes through an expansion valve, reducing its pressure and temperature.
Evaporation: The low – pressure, low – temperature refrigerant enters the evaporator, where it absorbs heat from the process fluid or air to be cooled, evaporating back into a vapor. The weak absorbent – refrigerant solution from the generator returns to the absorber to complete the cycle. Absorption 40 – ton chillers are less common than vapor – compression ones but can be a viable option in facilities with access to suitable heat sources.
Applications of 40 – Ton Chillers
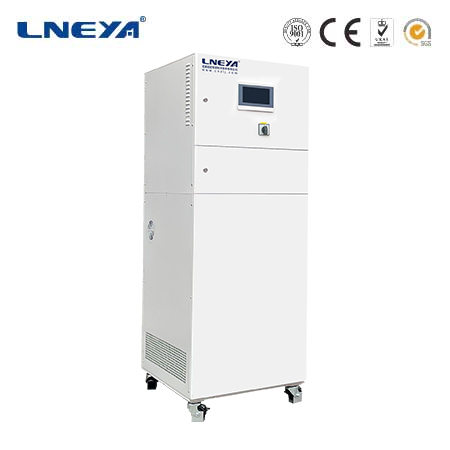
3.1 Commercial Buildings
Hotels: In hotels, a 40 – ton chiller is often used to provide cooling for the entire building, including guest rooms, lobbies, restaurants, and conference halls. The large cooling capacity ensures that all areas are maintained at a comfortable temperature, regardless of the outdoor conditions. The chiller can be integrated with the building’s air – handling units to distribute the cooled air evenly throughout the hotel.
Multi – story Office Buildings: Multi – story office buildings with a large number of occupants and heat – generating equipment, such as computers and servers, require a significant amount of cooling. A 40 – ton chiller can meet the cooling demands of such buildings. It can be used in a central air – conditioning system, with ducts distributing the cooled air to different floors and individual offices.
3.2 Industrial Applications
Food and Beverage Industry: In the food and beverage industry, 40 – ton chillers are used for various purposes. For example, in a large – scale dairy processing plant, the chiller can be used to cool the milk during processing to prevent spoilage. In a brewery, it can be used to cool the fermentation tanks, ensuring the proper temperature for yeast activity. The precise temperature control provided by the chiller is crucial for maintaining the quality of food and beverage products.
Manufacturing Plants: Manufacturing plants often have equipment that generates a lot of heat during operation. A 40 – ton chiller can be used to cool this equipment, preventing overheating and ensuring smooth operation. In a plastic injection – molding factory, for instance, the chiller can cool the molds, which helps in the proper shaping of plastic products.
Types of 40 – Ton Chillers
4.1 Air – Cooled 40 – Ton Chillers
Cooling Medium: Air – cooled 40 – ton chillers use ambient air as the cooling medium in the condenser. Fans are used to blow air over the condenser coils to dissipate the heat from the refrigerant.
Advantages: They are relatively easy to install as they do not require a complex water – cooling infrastructure. They are suitable for applications where water availability is limited. They can be placed outdoors, saving indoor space. In some cases, they may have a lower initial cost compared to water – cooled chillers.
Disadvantages: They are generally less energy – efficient compared to water – cooled chillers. Air has a lower heat – carrying capacity than water, so more air needs to be circulated to remove the same amount of heat. This results in higher fan power consumption. Their performance can be affected by high ambient temperatures, as the cooling efficiency decreases when the outdoor air is hot.
4.2 Water – Cooled 40 – Ton Chillers
Cooling Medium: Water – cooled 40 – ton chillers use water as the cooling medium in the condenser. The warm water from the condenser is then cooled in a cooling tower or a water – cooled heat exchanger and recirculated.
Advantages: They are more energy – efficient as water can carry more heat per unit volume than air. This leads to lower operating costs over time. They can operate at a lower condenser pressure, which can extend the lifespan of the compressor and other components. They are also less noisy compared to air – cooled chillers.
Disadvantages: They require a water – cooling system, which includes a cooling tower, pumps, and associated plumbing. This makes the installation more complex and expensive. Water treatment is necessary to prevent scale formation and corrosion in the water – cooling system.
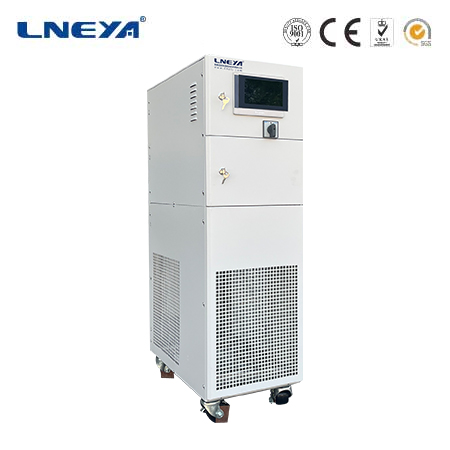
4.3 Absorption 40 – Ton Chillers
Heat – Driven Process: As mentioned earlier, absorption 40 – ton chillers use a heat – driven process. They are suitable for facilities that have access to waste heat sources, such as industrial plants with exhaust gases or power plants with excess heat.
Advantages: They can be an energy – efficient option when there is a suitable waste heat source available. They typically use refrigerants with low ozone – depletion potential and global – warming potential, making them more environmentally friendly in some cases. They operate quietly as they do not use a mechanical compressor.
Disadvantages: They have a higher initial cost compared to some vapor – compression chillers. Their efficiency can be lower at partial load conditions. They require a reliable heat source, and if the heat source is not available or is interrupted, the chiller’s operation may be affected.
Considerations When Choosing a 40 – Ton Chiller
5.1 Cooling Requirements
Accurate Load Calculation: It is essential to accurately calculate the cooling load of the space or process that the 40 – ton chiller will serve. Factors such as the size of the building, the number of occupants, the amount of heat – generating equipment, and the insulation of the space need to be considered. An inaccurate load calculation can lead to either an undersized chiller that cannot meet the cooling needs or an oversized chiller that is inefficient and costly to operate.
Future Expansion: If there is a possibility of future expansion in the building or an increase in the cooling requirements of the industrial process, it may be advisable to choose a 40 – ton chiller with some capacity for future growth. This could involve selecting a chiller with a slightly higher cooling capacity or one that can be easily upgraded.
5.2 Energy Efficiency
Energy – Star Ratings and Efficiency Standards: Look for 40 – ton chillers with high energy – efficiency ratings. Energy – Star ratings and other industry – recognized efficiency standards can be used as a guide. Chillers with features like variable – speed drives, which adjust the compressor speed according to the load, are generally more energy – efficient. Choosing an energy – efficient chiller can result in significant cost savings on energy bills over the long term.
Part – Load Performance: In many applications, the cooling load varies throughout the day. A 40 – ton chiller’s part – load performance is an important factor to consider. Chillers that are designed to operate efficiently under part – load conditions can save a substantial amount of energy. Some chillers use advanced control algorithms to optimize their performance at different load levels.
5.3 Installation and Space Requirements
Installation Complexity: Consider the installation complexity of the 40 – ton chiller. Air – cooled chillers are generally easier to install as they do not require a complex water – cooling infrastructure. Water – cooled chillers, on the other hand, need a cooling tower, pumps, and plumbing, which can make the installation more involved. The availability of skilled installers in the area and the cost of installation should also be taken into account.
Space Availability: The physical space available for the chiller is a crucial factor. Air – cooled chillers can be placed outdoors, but they still require a certain amount of space for proper air circulation. Water – cooled chillers need space for the chiller unit, the cooling tower, and the associated plumbing. In a building with limited space, the size and layout of the 40 – ton chiller and its components need to be carefully planned.
Maintenance of 40 – Ton Chillers
6.1 Regular Inspections
Refrigerant Level Checks: Regularly check the refrigerant level in the 40 – ton chiller. A low refrigerant level can reduce the cooling capacity and efficiency of the chiller. If there is a refrigerant leak, it should be detected and repaired promptly. Specialized equipment is used to measure the refrigerant level accurately.
Component Inspections: Inspect all the components of the chiller, including the compressor, expansion valve, condenser, and evaporator. Look for signs of wear, leaks, or damage. For example, the compressor should be checked for abnormal noises or vibrations, which could indicate mechanical problems. The heat exchanger surfaces should be inspected for fouling or corrosion.
6.2 Cleaning and Servicing
Heat Exchanger Cleaning: Clean the heat exchangers (condenser and evaporator) regularly. Fouling on the heat exchanger surfaces can reduce the heat transfer efficiency of the chiller. In air – cooled chillers, the condenser coils can be cleaned using compressed air or a coil – cleaning solution. In water – cooled chillers, the water – side of the heat exchangers may need to be chemically cleaned to remove scale and deposits.
Filter Replacements: Replace the filters in the chiller system as recommended by the manufacturer. Filters are used to remove debris and particles from the refrigerant and the cooling medium. Clogged filters can restrict the flow of refrigerant or cooling water, reducing the chiller’s performance.
6.3 Preventive Maintenance
Lubrication of Moving Parts: Lubricate all the moving parts of the 40 – ton chiller, such as the compressor bearings and the fan motors. Proper lubrication reduces friction and wear, extending the lifespan of the components. Use the recommended lubricants and follow the manufacturer’s guidelines for lubrication intervals.
Control System Calibration: Calibrate the control system of the chiller regularly. The control system is responsible for regulating the temperature, pressure, and other operating parameters of the chiller. A properly calibrated control system ensures that the chiller operates efficiently and safely.
In conclusion, a 40 – ton chiller is a powerful cooling solution with a wide range of applications. Understanding its working principles, types, applications, and maintenance requirements is crucial for making an informed decision when choosing and operating such a chiller.
Related recommendations
40 ton air cooled chiller
82Working PrincipleThe 40 ton air cooled chiller operates on the vapor-compression refrigeration cycle, which involves four main stages:Compression: The compressor takes in low-pressure, low-tempe...
View detailsWhat is the reason why the cryogenic chiller does not cool?
892What is the reason why the cryogenic chiller does not cool? During the operation of the chiller, the liquid refrigerant in the evaporator continuously absorbs heat from the water and be...
View detailssmall chiller price
297Small Chiller Price Overview Small chillers are essential in various applications, from commercial to industrial settings, providing precise temperature control. The price of these chillers is ...
View detailsefficient portable heater
155Efficient Portable HeaterIn a world where flexibility and convenience in heating solutions are highly valued, efficient portable heaters have emerged as essential devices. Whether it's for warmin...
View details
HelloPlease log in