water chiller for injection molding machine
Water Chiller for Injection Molding Machine: Enhancing Productivity and Efficiency
Water chillers play a pivotal role in the injection molding industry, ensuring the precise temperature control necessary for the efficient operation of injection molding machines. This article delves into the importance of water chillers, their selection criteria, and their impact on the injection molding process.
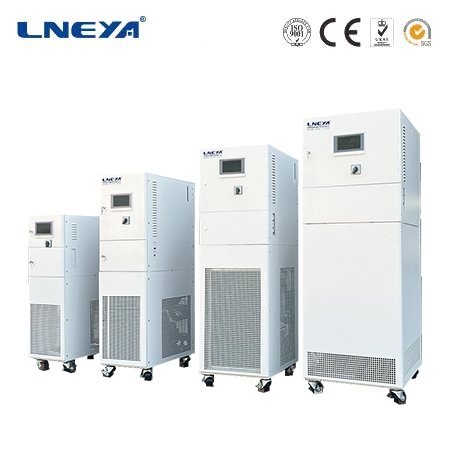
Importance of Water Chillers in Injection Molding
Water chillers are used to cool the molds in injection molding machines, which is crucial for controlling the temperature of the plastic being molded. By maintaining optimal temperatures, water chillers help in enhancing the surface quality of plastic parts, reducing cycle times, and increasing production efficiency.
Selection Criteria for Water Chillers
Selecting the appropriate water chiller for an injection molding machine involves considering several factors:
Melting Point of Plastic: Understanding the melting point of the plastic material is essential, as different plastics have different melting points. For instance, polypropylene has a melting point of 160°C, while polycarbonate can reach up to 287°C.
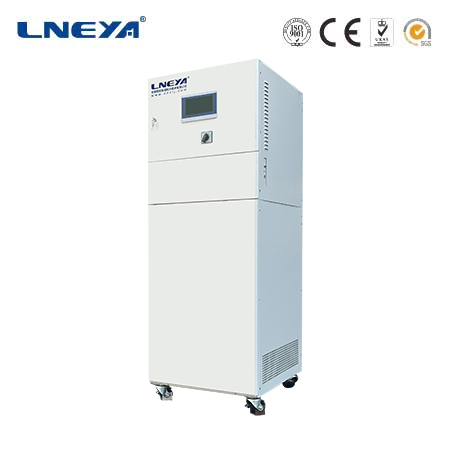
Heat Distortion Temperature (HDT): Knowing the HDT range for the plastic material helps in choosing the right water chiller, as it affects the cooling requirements.
Cooling Power: The cooling power of the chiller must match the cooling needs of the injection molding machine, ensuring efficient heat removal and optimal cooling.
Space Availability: The physical dimensions of the chiller should fit within the available space in the production facility.
Benefits of Using Water Chillers in Injection Molding
The use of water chillers in injection molding offers several benefits:
Reduced Cycle Times: Efficient cooling with water chillers can significantly reduce the amount of time spent for each batch, leading to faster production cycles.
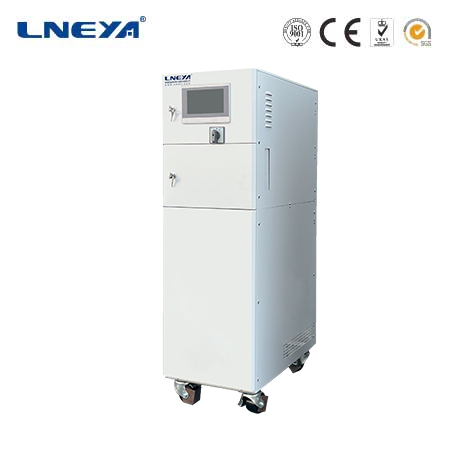
Improved Quality: Precise temperature control helps in reducing defects in the molded parts, resulting in higher quality products.
Energy Efficiency: Modern water chillers are designed to be energy-efficient, reducing operational costs and environmental impact. Chillers with FleXX technology, for example, can reduce energy requirements by up to 30%.
Customization and Flexibility: Water chillers can be customized to suit specific cooling needs, with features like digital synchronization with the mold cycle and the ability to memorize parameters for each mold.
Conclusion
Water chillers are an indispensable component in the injection molding process, providing precise temperature control that enhances productivity and quality. As the injection molding market continues to grow, the demand for efficient and sustainable water chiller solutions is expected to rise. The future of water chillers in injection molding lies in continued innovation, energy efficiency, and customization, ensuring that they remain a key driver in the industry’s progress.
Related recommendations
What factors are related to the cooling effect of a 50 ton chiller?
986What factors are related to the cooling effect of a 50 ton chiller? 1. Insufficient refrigerant Solution: It is necessary to supplement sufficient refrigerant and maintain a pres...
View detailstemperature control chamber
143Temperature Control Chamber: A Comprehensive Guide Temperature control chambers play a crucial role in numerous industries and scientific research endeavors by providing a controlled environme...
View detailslarge tonnage chillers
339Understanding Large Tonnage Chillers Large tonnage chillers are industrial-scale refrigeration systems designed to provide substantial cooling capacities, often ranging from hundreds to thousan...
View details30 ton air cooled chiller
26730 Ton Air-Cooled Chiller: Industrial Cooling Solutions Air-cooled chiller systems are essential in industries where precise temperature control is required. A 30-ton air-cooled chiller, in par...
View details
HelloPlease log in