water cooled unit
Water Cooled Unit: A Comprehensive Guide
Water cooled units are crucial components in a wide array of industrial and commercial applications, primarily designed to facilitate efficient heat transfer and maintain optimal operating temperatures. These units utilize water as the medium for heat dissipation, taking advantage of water’s high heat – carrying capacity to remove excess heat from various processes, equipment, or indoor environments. From large – scale manufacturing plants to commercial buildings and data centers, water cooled units play a vital role in ensuring the smooth and reliable operation of systems that generate significant amounts of heat.
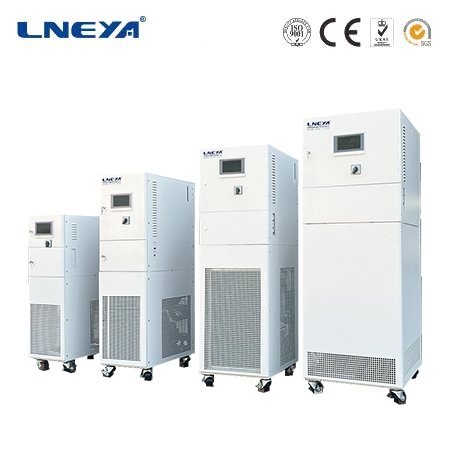
Working Principles of Water Cooled Units
The operation of water cooled units is based on a continuous cycle of heat absorption and rejection, involving several key components and processes.
Heat Absorption
In the initial stage, the water cooled unit comes into contact with the heat source. For example, in a water – cooled chiller system used for air conditioning in a building, the warm refrigerant (after absorbing heat from the indoor air) enters the water – cooled condenser. Here, the water flowing through the condenser tubes absorbs heat from the refrigerant. In industrial applications, water cooled units can be used to cool machinery, where the water directly absorbs heat generated by the equipment during operation. The heat transfer occurs through conduction, as the relatively cooler water comes into contact with the hotter surface of the component or refrigerant, causing heat to flow from the hotter to the cooler medium.
Water Circulation
A pump is a critical element in water cooled units, responsible for circulating the water throughout the system. The pump forces the heated water, which has absorbed heat from the source, to move towards the heat rejection component. This continuous circulation ensures that fresh, cooler water is constantly available to absorb heat, maintaining the efficiency of the cooling process. The flow rate of the water, determined by the pump’s capacity, is carefully designed to match the heat load of the system. A higher heat load typically requires a greater water flow rate to effectively remove the heat.
Heat Rejection
The heated water then reaches the heat rejection component, most commonly a cooling tower. In the cooling tower, the water is dispersed over fill materials, increasing its surface area. As air passes through the tower, a portion of the water evaporates. Evaporation is a cooling process as it requires energy, which is drawn from the remaining water, thus reducing its temperature. The cooled water is then collected at the bottom of the cooling tower and pumped back to the heat absorption component, restarting the cycle. In some cases, instead of a cooling tower, a heat exchanger may be used to transfer the heat from the water to another medium, such as ambient air or a secondary coolant loop.
Types of Water Cooled Units
Water – Cooled Chillers
Water – cooled chillers are one of the most common types of water cooled units. They are widely used in large – scale commercial buildings, industrial plants, and data centers. These chillers work by cooling a refrigerant through the heat – exchange process with water in the condenser. The cooled refrigerant then circulates through an evaporator, where it absorbs heat from the medium to be cooled, such as air in an air – conditioning system or process fluid in an industrial application.
Water – cooled chillers can be further classified into different subtypes based on their compressor technology, such as centrifugal chillers, screw chillers, and reciprocating chillers. Centrifugal chillers are known for their high – capacity cooling capabilities, making them suitable for large – scale applications where a significant amount of cooling is required. Screw chillers offer a good balance between capacity and efficiency and can operate effectively across a wide range of load conditions. Reciprocating chillers, on the other hand, are typically used for smaller – scale applications or where a lower cooling capacity is needed.
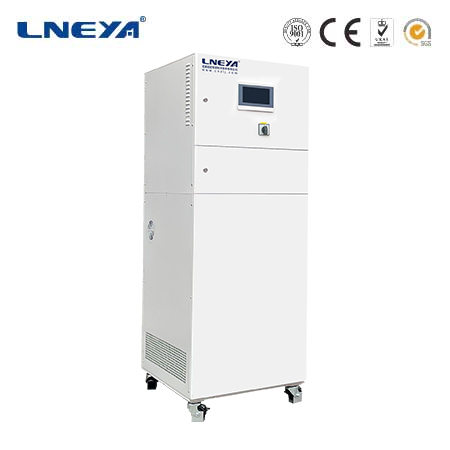
Water – Cooled Condensers
Water – cooled condensers are integral components of refrigeration and air – conditioning systems. Their main function is to condense the high – pressure, high – temperature refrigerant gas into a liquid by transferring heat to the water flowing through them. They consist of a series of tubes through which the water passes, while the refrigerant surrounds the tubes on the outside. The design of the condenser, including the tube material, tube arrangement, and surface area, significantly impacts its heat – transfer efficiency.
Copper tubes are commonly used in water – cooled condensers due to their excellent thermal conductivity and resistance to corrosion. The tubes may be arranged in a shell – and – tube configuration, where the water flows through the tubes and the refrigerant is in the shell, or in other specialized designs depending on the application requirements. Water – cooled condensers are more energy – efficient than air – cooled condensers in many cases, as water can absorb and carry away heat more effectively than air.
Water – Cooled Heat Exchangers
Water – cooled heat exchangers are used to transfer heat between two fluids, with water being one of the fluids. They can be used in various applications, such as pre – heating or cooling process fluids in industrial plants, or in HVAC systems for heat recovery purposes. There are different types of water – cooled heat exchangers, including shell – and – tube heat exchangers, plate – type heat exchangers, and coil – type heat exchangers.
Shell – and – tube heat exchangers consist of a large shell and a bundle of tubes inside it. One fluid flows through the tubes, while the other fluid (usually water) flows around the tubes within the shell, enabling heat transfer between the two. Plate – type heat exchangers are made up of a series of thin, corrugated metal plates stacked together, with gaskets sealing the edges to create separate channels for the two fluids. They offer a high heat – transfer efficiency in a compact size. Coil – type heat exchangers feature a coil through which one fluid flows, while the other fluid (water) passes over or around the coil, facilitating heat exchange.
Applications of Water Cooled Units
Industrial Applications
In the industrial sector, water cooled units are used in numerous processes. In manufacturing plants, they are essential for cooling machinery and equipment, such as injection molding machines, metal – working tools, and industrial furnaces. By maintaining the optimal operating temperature of these machines, water cooled units help prevent overheating, which can lead to equipment failure, reduced productivity, and poor product quality.
In the chemical industry, water cooled units play a crucial role in cooling chemical reactors, distillation columns, and other processing equipment. Many chemical reactions generate a significant amount of heat, and efficient cooling is required to control the reaction rate, prevent runaway reactions, and ensure the safety of the process. Additionally, water cooled units are used for cooling the electrical systems in industrial plants, such as transformers and motors, to maintain their performance and extend their lifespan.
Commercial Applications
In commercial buildings, water cooled units are widely used for air – conditioning systems. Large shopping malls, office buildings, hotels, and hospitals rely on water – cooled chillers to provide a comfortable indoor environment. These chillers cool the water, which is then circulated through air – handling units to cool and dehumidify the air before it is distributed throughout the building. Water – cooled condensers in these systems help reject the heat absorbed from the indoor air to the outside environment, ensuring the continuous operation of the air – conditioning system.
Data centers also heavily depend on water cooled units for cooling their servers and other IT equipment. The high heat load generated by the servers requires an efficient cooling solution to prevent overheating, which can lead to data loss and system failures. Water – cooled units in data centers are designed to remove heat from the servers and transfer it to a cooling tower or another heat rejection mechanism, maintaining the optimal temperature and humidity levels within the data center.
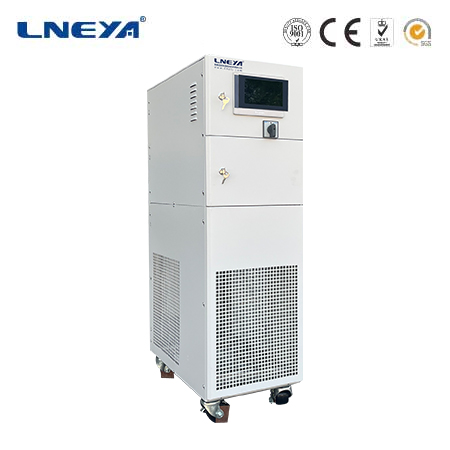
Selection Criteria for Water Cooled Units
Cooling Capacity
Determining the appropriate cooling capacity is the most critical factor when selecting a water cooled unit. It is essential to accurately calculate the total heat load of the system that needs to be cooled. Factors such as the size of the building or industrial facility, the number and type of heat – generating equipment, the ambient temperature, and the required temperature setpoint all contribute to the heat load calculation. An undersized water cooled unit will not be able to provide sufficient cooling, leading to overheating and potential system failures, while an oversized unit will result in higher initial costs, increased energy consumption, and unnecessary waste.
Energy Efficiency
Energy efficiency is a significant consideration, as water cooled units can consume a substantial amount of energy, especially in large – scale applications. Look for units with high – efficiency ratings, such as a high Coefficient of Performance (COP) or Energy Efficiency Ratio (EER). Energy – efficient water cooled units not only help reduce operating costs but also have a lower environmental impact by consuming less electricity. Features like variable – speed drives for pumps and compressors can adjust the operation of the unit based on the actual cooling demand, further enhancing energy savings.
Water Quality and Availability
The quality and availability of water are crucial factors. In regions with limited water resources, it may be necessary to consider water – conservation measures or alternative cooling technologies. Hard water, which contains high levels of minerals, can cause scaling and corrosion in the water – cooled unit’s components, reducing its efficiency and lifespan. Therefore, it is important to assess the water quality in the area and implement appropriate water treatment measures, such as filtration, softening, and chemical dosing, to prevent these issues. Additionally, the water supply should be reliable and have sufficient pressure and flow rate to meet the requirements of the water cooled unit.
Space Requirements
The available space for installing the water cooled unit is also an important consideration. Some units, such as large – scale water – cooled chillers with cooling towers, require significant floor space and may need to be installed outdoors. Others, like compact plate – type heat exchangers, can be installed in smaller spaces. The installation location should also allow for proper access for maintenance, ventilation, and connection to the water supply and drainage systems. When planning the installation, it is necessary to consider the dimensions of the unit, as well as any additional space required for pipes, valves, and other accessories.
Maintenance Requirements
Regular maintenance is necessary to keep water cooled units operating efficiently and reliably. Consider the ease of maintenance when choosing a unit. Units with easily accessible components, clear maintenance instructions, and a reliable supply of spare parts will be more convenient and cost – effective to maintain. Some manufacturers offer comprehensive maintenance services and training programs for operators, which can be beneficial for ensuring the proper operation and longevity of the unit. Additionally, the frequency of maintenance tasks, such as cleaning, inspection, and replacement of components, should be taken into account when making a selection.
Installation, Maintenance, and Environmental Considerations
Installation
Proper installation of water cooled units is essential for their optimal performance and longevity. The installation process should be carried out by trained professionals who are familiar with the specific requirements of the unit and local building codes. Key installation considerations include ensuring correct alignment and connection of pipes, proper electrical wiring (if applicable), and adequate ventilation for components such as cooling towers.
For water – cooled chillers, the refrigerant lines need to be properly connected and sealed to prevent leaks. The water pipes should be installed with the correct slope to ensure proper water flow and drainage. Cooling towers should be installed in a location with good air circulation to facilitate efficient heat rejection. Additionally, insulation should be applied to the water pipes and other components to minimize heat losses and prevent condensation, which can lead to corrosion and other problems.
Maintenance
Regular maintenance is crucial to keep water cooled units running smoothly. Maintenance tasks typically include cleaning the heat – transfer surfaces, such as the tubes in water – cooled condensers and heat exchangers, to remove dirt, scale, and other contaminants that can reduce heat – transfer efficiency. Monitoring the water quality and treating the water as needed to prevent scaling and corrosion is also an important part of maintenance.
Checking the refrigerant levels and pressures in water – cooled chillers, as well as the operation of pumps and fans, is necessary to ensure the proper functioning of the unit. Lubricating moving parts, replacing worn – out gaskets and seals, and calibrating control systems are other common maintenance activities. A well – planned maintenance schedule, based on the manufacturer’s recommendations and the operating conditions of the unit, can help prevent breakdowns, extend the unit’s lifespan, and maintain its energy efficiency.
Environmental Considerations
Water cooled units have environmental implications that need to be addressed. The water consumption of these units can be significant, especially in large – scale applications. Implementing water – conservation measures, such as using closed – loop systems or water – saving cooling tower designs, can help reduce water usage. Additionally, the proper disposal of wastewater from the water cooled unit is important to prevent environmental pollution.
The choice of refrigerant in water – cooled chillers also has an impact on the environment. Refrigerants with high global warming potential (GWP) can contribute to climate change. Therefore, it is advisable to select units that use more environmentally friendly refrigerants, such as those with low GWP or natural refrigerants. Ensuring proper refrigerant management to prevent leaks is also crucial for minimizing the environmental impact of water cooled units.
In conclusion, water cooled units are essential for efficient heat removal in a wide range of industrial and commercial applications. Understanding their working principles, types, applications, selection criteria, and aspects related to installation, maintenance, and environmental considerations is crucial for making informed decisions and ensuring the reliable and sustainable operation of these units. By carefully considering these factors, users can choose the right water cooled unit for their specific needs, optimize its performance, and contribute to energy – efficient and environmentally friendly cooling solutions.
Related recommendations
dc air conditioning
122DC (Direct Current) air conditioning represents a significant advancement in the field of climate control. Unlike traditional air - conditioning systems that primarily operate on alternating curre...
View detailswater heater coil
410Water Heater Coil: Enhancing Efficiency and Performance Water heater coils are critical components in both domestic and commercial water heating systems, providing efficient heat transfer to pr...
View detailswater cooled liquid chiller
192Water Cooled Liquid Chiller: Detailed Explanation Introduction to Water Cooled Liquid ChillersWater cooled liquid chillers are refrigeration machines designed to cool water or water-glycol mix...
View details200kw chiller
233200kW Chiller A 200kW chiller refers to a refrigeration unit with a cooling capacity of 200 kilowatts. This type of chiller is commonly used in a variety of settings where a moderate to relativ...
View details
HelloPlease log in