process cooling system
Process Cooling Systems: A Vital Component in Industrial Processes
Introduction to Process Cooling Systems
Process cooling systems are designed to control the temperature of processes in various industries, ensuring efficient operation and maintaining the quality of products. These systems can be classified into two main types: water-cooled and air-cooled, each with its own set of advantages and applications.
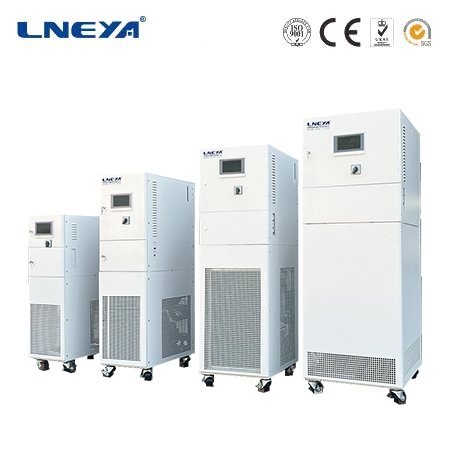
Components of a Process Cooling System
A typical process cooling system, especially a water-cooled system, consists of several key components:
Chiller Unit: The chiller unit houses the compressor, condenser, evaporator, and expansion valve. It is responsible for removing heat from the process or building and transferring it to the cooling medium, usually water.
Cooling Tower: The cooling tower acts as a heat rejection device, removing heat from the cooling water and dissipating it into the atmosphere through evaporation and heat transfer.
Water Pumps: Water pumps circulate the cooling water between the chiller unit, cooling tower, and the process or building being cooled, ensuring a continuous flow of coolant.
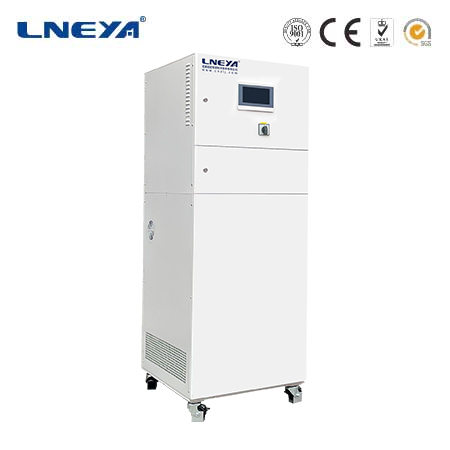
Water Treatment System: A water treatment system is often integrated to maintain the quality and cleanliness of the cooling water, preventing scaling, corrosion, and biological growth.
Controls and Instrumentation: These monitor and regulate the operation of the chiller system, including temperature, flow rates, and pressure, ensuring optimal performance.
Operation of Process Cooling Systems
The operation of a process cooling system involves a series of steps that form a closed-loop refrigeration cycle:
Refrigeration Cycle: The compressor pressurizes the refrigerant gas, raising its temperature and pressure. The high-pressure gas then flows to the condenser, where it releases heat to the cooling water and condenses into a high-pressure liquid.
Heat Rejection: The high-pressure liquid refrigerant flows through the expansion valve, which reduces its pressure, causing the refrigerant to evaporate in the evaporator and absorb heat from the process or building being cooled.
Cooling Water Circuit: The cooling water circuit involves the circulation of water between the chiller unit, cooling tower, and the process or building being cooled. The cooling tower removes heat from the cooling water, which is then circulated back to the chiller unit to absorb heat again.
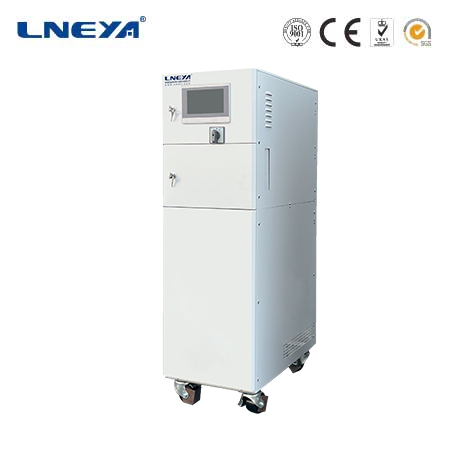
Advantages of Process Cooling Systems
Process cooling systems offer several advantages, particularly in industrial settings:
Efficiency: Water-cooled systems are generally more energy-efficient compared to air-cooled systems due to the superior heat transfer capabilities of water.
Space Saving: Water-cooled chiller systems require less space compared to air-cooled systems, as there is no need for large condenser fans, making them ideal for installations where space is limited.
Reliability: Process cooling systems, especially those from reputable manufacturers, are designed with a zero-defect policy, ensuring reliable operation for years to come.
Customizability: Process cooling solutions can be customized to meet the specific needs of different industries, whether it’s a plug-and-play solution or a completely customized system.
Applications of Process Cooling Systems
Process cooling systems are used in a variety of applications where precise temperature control is essential:
Manufacturing: In industries such as plastics, chemicals, and food processing, process cooling systems maintain optimal temperatures for processes and equipment.
Data Centers: They keep IT equipment running smoothly by accommodating large amounts of heat generation.
Food Processing & Storage: Reliable process cooling provides stable temperatures for food production, transport, and storage.
Pharmaceutical: Process cooling systems avoid air contamination in highly controlled environments with their precise temperature and humidity control technologies.
Conclusion
Process cooling systems are indispensable in maintaining the required temperature for various industrial processes. Their ability to provide precise temperature control and energy efficiency makes them a vital component in industries such as plastics, food processing, and data centers. As technology advances, process cooling systems continue to evolve, offering more efficient and sustainable solutions to meet the changing needs of industries worldwide.
Related recommendations
small industrial water chiller
356Small Industrial Water Chillers: Efficient Cooling for Manufacturing Processes Small industrial water chillers play a critical role in maintaining precise temperature control in a variety of ma...
View detailsthermal oil heaters
435Understanding Thermal Oil Heaters Thermal oil heaters are a type of heat transfer fluid electric boiler designed to heat process fluids in industrial applications. They operate by using electri...
View detailsindustrial glycol chiller system
128IntroductionIn the complex and energy - intensive landscape of industrial operations, maintaining precise temperature control is often the linchpin for ensuring product quality, equipment longevi...
View detailsWhat are the performance advantages of a 1 ton chiller?
856What are the performance advantages of a 1 ton chiller? 1. Simple construction and easy operation: with fewer spare parts, the simple and clear control panel in the 1-ton chiller is ver...
View details
HelloPlease log in