laboratory cooling equipment
Laboratory cooling equipment is a category of specialized devices engineered to create and maintain controlled low-temperature environments, essential for preserving samples, enabling chemical reactions, and ensuring the proper functioning of analytical instruments. Unlike commercial or residential cooling appliances, these tools prioritize precision, reliability, and stability, often operating within temperature ranges as broad as -270°C to 20°C, with tolerances as tight as ±0.1°C. This level of control is vital in scientific research, where even minor temperature fluctuations can invalidate experimental results, compromise sample integrity, or damage sensitive equipment. From basic refrigerators for reagent storage to advanced cryogenic systems for ultra-low temperature applications, laboratory cooling equipment forms the backbone of countless scientific and industrial processes.
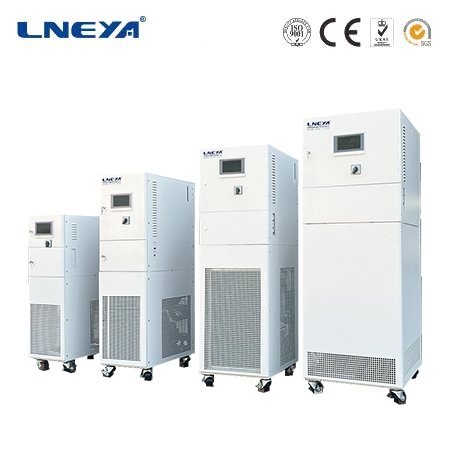
Laboratory cooling equipment comprises several distinct types, each tailored to specific temperature ranges and applications. Laboratory refrigerators are the most common, designed to maintain temperatures between 2°C and 8°C—ideal for storing pharmaceuticals, biological samples, and chemical reagents that degrade at room temperature. These differ from household refrigerators in their precise temperature control (±1°C) and features like forced-air circulation to eliminate temperature gradients within the unit, ensuring uniform cooling. Many models include alarms that trigger if temperatures exceed the safe range, protecting valuable samples from spoilage.
Laboratory freezers operate at lower temperatures, with low-temperature freezers (-20°C to -40°C) used for storing enzymes, vaccines, and biological materials requiring longer-term preservation. Ultra-low temperature (ULT) freezers extend this range to -86°C, capable of preserving samples for years, such as cell lines, DNA, and viruses. These freezers use advanced compressors with multiple cooling stages—some employing cascade systems, where two compressors work in series to achieve extremely low temperatures. Insulation is critical in ULT freezers, often using vacuum-sealed panels or high-density foam to minimize heat infiltration and reduce energy consumption.
Recirculating chillers are designed to cool external equipment, such as spectrometers, rotary evaporators, or laser systems, by circulating chilled fluid (usually water or a water-glycol mixture) through the equipment’s cooling coils. They maintain temperatures between -40°C and 30°C, with precise control (±0.1°C) to prevent overheating of instruments during operation. Recirculating chillers feature a reservoir, a refrigeration system, and a pump to circulate the fluid, with many models allowing users to adjust flow rates to match the equipment’s cooling needs.
Cryogenic equipment handles the lowest temperatures, using cryogens (substances that exist as liquids at extremely low temperatures) like liquid nitrogen (-196°C) or liquid helium (-269°C). Cryogenic freezers and dewars (insulated containers) store samples at these ultra-low temperatures, essential for preserving tissues, stem cells, and other biological materials with long-term viability requirements. Cryostats are specialized devices that maintain frozen samples at specific temperatures (typically -20°C to -50°C) while allowing sectioning for microscopy, a common technique in histology and pathology.
Cooling baths (or chillers baths) provide a stable low-temperature environment for small-scale reactions or sample preparation. They consist of a container filled with a cooling medium (e.g., ethanol or dry ice mixtures) and a temperature controller that circulates the medium to maintain the desired temperature, often between -80°C and 100°C. These are widely used in chemistry labs for processes like distillation, crystallization, and enzyme activity studies, where precise temperature control is critical.
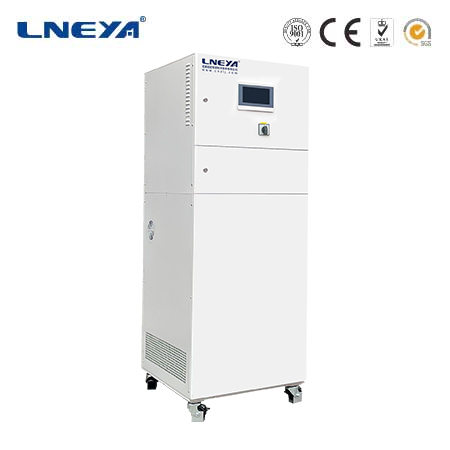
The operation of laboratory cooling equipment relies on principles of thermodynamics, using various mechanisms to remove heat from the target environment. Vapor-compression refrigeration is the most common technology, employed in refrigerators, freezers, and recirculating chillers. This process involves four key components: a compressor, condenser, expansion valve, and evaporator. The compressor pressurizes a refrigerant (e.g., HFC-134a, a non-toxic, low-global-warming-potential gas), raising its temperature. The hot, high-pressure refrigerant flows to the condenser, where it releases heat to the surrounding environment and condenses into a liquid. The liquid refrigerant then passes through an expansion valve, which reduces its pressure, causing it to evaporate in the evaporator. During evaporation, the refrigerant absorbs heat from the internal environment (e.g., the freezer compartment or circulating fluid), lowering its temperature. The low-pressure vapor returns to the compressor, completing the cycle.
Cryogenic equipment operates on a different principle, leveraging the latent heat of vaporization of cryogens. When liquid nitrogen is exposed to a warmer environment, it boils and vaporizes, absorbing large amounts of heat in the process, rapidly cooling the surrounding area. Dewars and cryogenic freezers use vacuum insulation to minimize heat transfer, slowing the evaporation of the cryogen and extending its cooling capacity.
For applications requiring precise temperature control, such as recirculating chillers and cooling baths, proportional-integral-derivative (PID) controllers are integrated into the system. These controllers continuously monitor the temperature via sensors (RTDs or thermocouples) and adjust the refrigeration output—by varying compressor speed or regulating the flow of cryogens—to maintain the setpoint, minimizing fluctuations and ensuring stability.
Laboratory cooling equipment is indispensable across a range of scientific and industrial fields, playing a critical role in preserving samples, enabling experiments, and supporting instrument operation. In biological and life sciences, refrigerators and freezers store cell cultures, blood samples, and antibodies at 2–8°C and -20°C to -80°C, respectively, preventing degradation and maintaining viability for research or clinical use. Cryogenic freezers (-150°C to -196°C) are essential for long-term storage of stem cells and genetic materials, with some samples preserved for decades for future studies.
Pharmaceutical and medical research relies on precise cooling to develop and test drugs. Stability testing of pharmaceuticals—assessing how drugs degrade over time—requires controlled low temperatures (e.g., 5°C, 25°C) to simulate storage conditions, using specialized refrigerators with data logging to track temperature over months or years. Vaccine storage, particularly for mRNA vaccines like those for COVID-19, demands ultra-low temperature freezers (-70°C) to maintain efficacy.
Chemistry and materials science laboratories use cooling equipment for reactions that generate heat or require low temperatures to proceed. Recirculating chillers cool rotary evaporators, which remove solvents from solutions by evaporation, ensuring the condenser remains cold enough to trap the solvent vapor. Cooling baths maintain reaction vessels at specific temperatures—for example, 0°C for reactions involving ice baths or -78°C using dry ice and acetone—controlling reaction rates and preventing unwanted side reactions.
Analytical laboratories depend on cooling equipment to ensure instrument accuracy. Spectrophotometers, which measure light absorption in samples, use cooling systems to stabilize the temperature of detectors, as heat can cause electronic noise and distort readings. Chromatography systems, such as HPLC (High-Performance Liquid Chromatography), require cooled autosamplers to keep samples at low temperatures, preventing chemical degradation before analysis.
Environmental and food science applications use laboratory cooling equipment to preserve samples collected in the field. Soil, water, and air samples are stored in refrigerators or freezers to prevent microbial growth or chemical changes until analysis, ensuring data accuracy. Food testing labs use similar equipment to assess shelf-life and safety, storing food samples at various temperatures to simulate consumer storage conditions.
Selecting the right laboratory cooling equipment requires careful consideration of several key factors to match the device to the application’s specific needs. Temperature range is the primary consideration: a lab storing routine reagents will need a refrigerator (2–8°C), while one working with cryopreserved cells requires an ultra-low temperature freezer (-80°C or lower). It is critical to choose a device with a range that exceeds the required temperature to account for minor fluctuations.
Temperature precision and uniformity are essential for experiments or storage where consistency is critical. Look for equipment with a tolerance of ±0.5°C or better, and forced-air circulation to ensure uniform cooling throughout the chamber. For example, a freezer used for storing biological samples must maintain the same temperature in all corners to prevent some samples from thawing while others remain frozen.
Capacity and storage configuration depend on the volume and type of samples or equipment. Benchtop models are suitable for small labs with limited space, while floor-standing units offer larger capacities (up to 1,000 liters for freezers). Consider shelf configuration—adjustable or removable shelves allow flexibility for storing various container sizes, from small vials to large bottles.
Energy efficiency is a practical concern, especially for ultra-low temperature freezers, which consume significant energy. Look for models with energy-saving features like variable-speed compressors, high-efficiency insulation, and standby modes for periods of low use. Energy Star-certified equipment meets strict efficiency standards, reducing operating costs over time.
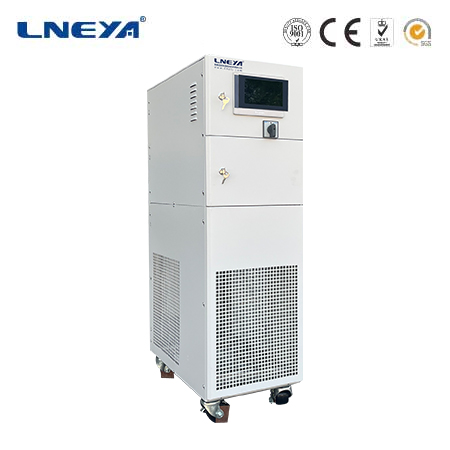
Safety and monitoring features are critical for protecting valuable samples. Temperature alarms (audible, visual, or remote via email/SMS) alert users to deviations from the set range, while backup power options (e.g., battery or generator compatibility) prevent temperature spikes during power outages. Data logging capabilities, which record temperature history, are essential for regulatory compliance in fields like pharmaceuticals, where documentation of storage conditions is required.
Material compatibility ensures the equipment can handle the samples or chemicals stored. Stainless steel interiors are resistant to corrosion from chemicals, making them suitable for chemistry labs, while glass-lined or plastic interiors may be preferred for biological samples to minimize contamination risks.
Regulatory compliance is necessary for labs subject to standards like Good Laboratory Practice (GLP) or Good Manufacturing Practice (GMP). Choose equipment that meets these standards, with features like tamper-proof settings, audit trails, and calibration certificates to facilitate compliance.
Proper maintenance of laboratory cooling equipment is essential to ensure accuracy, reliability, and longevity, as well as to protect valuable samples. Regular cleaning prevents contamination and maintains efficiency. Wipe down interior surfaces with a mild disinfectant (e.g., 70% ethanol) monthly, removing spills and debris. For freezers, defrost manually or use auto-defrost features (if available) to prevent ice buildup, which reduces cooling efficiency and increases energy use.
Temperature calibration verifies accuracy. Annually, compare the equipment’s displayed temperature to a calibrated thermometer placed inside the unit, at the same level as stored samples. If discrepancies exceed the tolerance range, contact a technician to recalibrate the sensors or controller. Keep calibration records for regulatory compliance.
Inspecting and maintaining cooling systems ensures optimal performance. For compressor-based equipment, clean condenser coils every 3–6 months to remove dust and debris, which can block airflow and cause the compressor to overwork. Check door gaskets for wear or damage, replacing them if they no longer seal tightly—leaks allow warm air to enter, increasing energy consumption and temperature fluctuations.
Monitoring and addressing alarms promptly prevents sample loss. Test alarm systems monthly to ensure they function correctly, and respond immediately to alerts by checking for power outages, door ajar issues, or compressor failures. Have a contingency plan, such as backup storage, for critical samples in case of equipment failure.
Cryogenic equipment maintenance requires special care. Handle cryogens like liquid nitrogen with proper PPE (gloves, goggles) to prevent cold burns. Inspect dewars and cryogenic freezers for signs of insulation degradation, which can increase evaporation rates. Monitor cryogen levels regularly, refilling before they drop too low to avoid sample thawing.
Emerging trends in laboratory cooling equipment focus on enhancing precision, sustainability, and connectivity, driven by advances in technology and growing demands for efficiency and compliance. Smart monitoring and IoT integration allow remote tracking of temperature, energy use, and equipment status via cloud-based platforms. Users can receive real-time alerts on smartphones or computers, enabling proactive maintenance and reducing the risk of sample loss. Some systems integrate with laboratory information management systems (LIMS), automating data logging and compliance reporting.
Energy-efficient designs are a priority, with manufacturers developing compressors that adjust cooling output based on demand, reducing energy consumption. Ultra-low temperature freezers now feature better insulation materials, such as aerogels, which provide superior thermal resistance while reducing weight and size. Solar-powered or hybrid systems are emerging for off-grid labs or regions with unreliable power, ensuring continuous operation.
Miniaturization is enabling more compact equipment without sacrificing performance. Benchtop chillers and freezers with small footprints are ideal for crowded labs, while microfluidic cooling systems provide precise temperature control for tiny samples or microscale reactions, advancing fields like point-of-care diagnostics.
Sustainability initiatives are driving the development of environmentally friendly refrigerants. Traditional refrigerants with high global warming potential (GWP) are being replaced with low-GWP alternatives, such as hydrofluoroolefins (HFOs), reducing the environmental impact of equipment. Manufacturers are also designing equipment for easier recycling at the end of its lifecycle, minimizing waste.
Advanced temperature control algorithms are improving stability, with adaptive PID controllers that learn from temperature fluctuations and adjust cooling output in real time. This reduces overshoot and undershoot, maintaining tighter tolerances and improving energy efficiency. Some systems use artificial intelligence to predict temperature changes based on usage patterns, optimizing performance.
In conclusion, laboratory cooling equipment is an essential component of scientific research and industrial processes, providing the precise, stable low-temperature environments needed to preserve samples, enable experiments, and operate instruments. With a range of types designed for specific temperature ranges and applications, these tools are critical to ensuring the accuracy and reliability of scientific data. By understanding their functions, selection criteria, and maintenance requirements, researchers and lab managers can choose the right equipment to meet their needs, ensuring optimal performance and sample protection. As technology advances, laboratory cooling equipment will continue to evolve, offering greater efficiency, connectivity, and sustainability, supporting the next generation of scientific discoveries.
Related recommendations
thermal test systems
111Introduction to Thermal Test SystemsThermal test systems are specialized setups designed to subject products, components, or materials to controlled thermal conditions, simulating the environment...
View detailsgerman chiller manufacturer
480German Chiller Manufacturer: Innovation, Quality, and Sustainability Germany's engineering prowess extends to the chiller manufacturing industry, with several companies leading the way in innov...
View detailsprocess heater manufacturers
268Process Heater Manufacturers Process heaters are essential equipment in many industrial sectors as they are used to heat fluids, gases, or other materials to specific temperatures required for ...
View details5 tr water chiller
2325 TR Water Chiller: A Comprehensive GuideWhat is a 5 TR Water Chiller?A 5 TR water chiller is a cooling device with a cooling capacity of 5 tons of refrigeration. One ton of refrigeration is equiv...
View details
HelloPlease log in