lab chiller
Lab Chiller: A Comprehensive Guide
In the intricate world of scientific research, maintaining precise temperature conditions is often the key to obtaining accurate and reliable results. Lab chillers, also known as laboratory cooling systems, play an indispensable role in this regard. These specialized devices are designed to remove heat from various laboratory processes, equipment, and samples, ensuring that experiments proceed under optimal thermal environments. This article will provide a comprehensive exploration of lab chillers, covering their working principles, types, components, applications, selection criteria, and maintenance considerations.
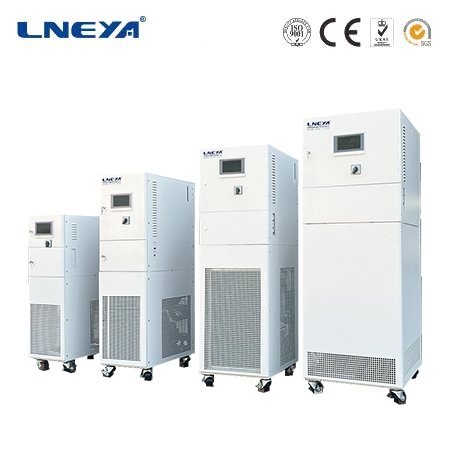
Working Principles of Lab Chillers
Lab chillers operate based on well – established refrigeration principles, with the two most common cycles being the vapor – compression cycle and, to a lesser extent, the absorption cycle.
Vapor – Compression Cycle
The vapor – compression cycle is the foundation for the majority of lab chillers. It involves four main stages:
Compression: The cycle initiates with the compressor, which draws in low – pressure, low – temperature refrigerant vapor from the evaporator. Through mechanical work, the compressor increases the pressure and temperature of the vapor. For instance, in a reciprocating compressor, a piston moves back and forth within a cylinder to compress the refrigerant, converting it into a high – pressure, high – temperature state. This energy – intensive process is essential for the subsequent heat – transfer stages.
Condensation: The high – pressure, high – temperature refrigerant vapor then enters the condenser. Here, it releases heat to a cooling medium, which can be air or water. As the refrigerant loses heat, it undergoes a phase change from a vapor to a liquid. In air – cooled condensers, fins are used to enhance the surface area for heat dissipation to the surrounding air, while water – cooled condensers transfer heat to a flowing water stream, offering more efficient heat removal.
Expansion: The high – pressure liquid refrigerant next passes through an expansion device, such as a thermostatic expansion valve (TXV) or a capillary tube. This device reduces the pressure of the refrigerant abruptly, causing it to expand and cool down significantly. The result is a low – pressure, low – temperature mixture of liquid and vapor, ready for the final stage of the cycle.
Evaporation: The low – pressure, low – temperature refrigerant mixture enters the evaporator. In the evaporator, the refrigerant absorbs heat from the process fluid or the equipment that requires cooling, such as a reaction vessel or a spectroscopy instrument. As the refrigerant absorbs heat, it evaporates back into a low – pressure vapor, completing the cycle and providing the necessary cooling effect.
Absorption Cycle
Although less common than the vapor – compression cycle in lab chillers, the absorption cycle is utilized in specific scenarios, especially where waste heat or low – grade heat sources are available. In this cycle:
Absorption: The refrigerant, often water in lithium – bromide absorption chillers, is absorbed by a strong solution of an absorbent, such as lithium – bromide. This absorption process releases heat, and the resulting weak solution of absorbent and refrigerant is pumped to a generator.
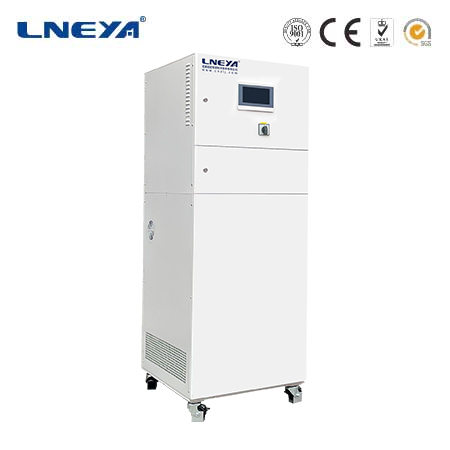
Generation: Heat is applied to the weak solution in the generator, causing the refrigerant to vaporize and separate from the absorbent. The high – pressure refrigerant vapor then proceeds to the condenser, where it condenses and releases heat, similar to the vapor – compression cycle.
Expansion and Evaporation: The condensed refrigerant passes through an expansion valve and enters the evaporator. Here, it absorbs heat from the target cooling source, evaporates, and becomes a low – pressure vapor, which is then absorbed by the strong absorbent solution in the absorber, restarting the cycle. The advantage of the absorption cycle lies in its ability to utilize heat sources that would otherwise be wasted, making it an energy – efficient option in certain applications.
Types of Lab Chillers
Lab chillers come in various types, each designed to meet specific cooling requirements and laboratory setups.
Benchtop Chillers
Features: Benchtop chillers are compact, space – saving devices ideal for small – scale laboratory applications. They are designed to fit on a laboratory bench or within a cabinet, making them suitable for laboratories with limited floor space. These chillers typically have lower cooling capacities, ranging from a few hundred watts to a couple of kilowatts.
Applications: They are commonly used for cooling small – scale equipment, such as rotary evaporators, circulators, and some types of analytical instruments. For example, in a chemistry lab conducting solvent evaporation using a rotary evaporator, a benchtop chiller can efficiently cool the condenser to recover the solvent.
Floor – Standing Chillers
Features: Floor – standing chillers are larger and more powerful than benchtop models. They have higher cooling capacities, often ranging from several kilowatts to tens of kilowatts. These chillers are more robust and can handle continuous operation under heavy loads. They usually come with additional features such as built – in pumps, storage tanks, and advanced control systems.
Applications: They are suitable for larger laboratories or industrial research facilities where multiple pieces of equipment or large – scale processes require cooling. In a pharmaceutical research lab, a floor – standing chiller might be used to cool multiple fermentation tanks simultaneously, ensuring consistent temperature control for the production of biological drugs.
Recirculating Chillers
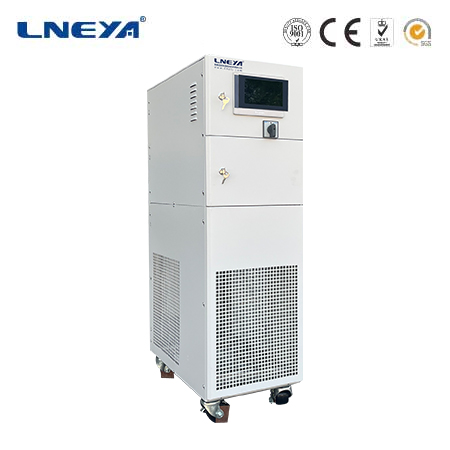
Features: Recirculating chillers are designed to circulate a coolant, usually water or a water – glycol mixture, through the equipment to be cooled and then back to the chiller for re – cooling. They often have high – flow pumps to ensure efficient heat transfer and can maintain a stable temperature over extended periods. Some recirculating chillers are equipped with temperature – control systems that can be adjusted to meet specific experimental requirements.
Applications: These chillers are widely used in applications where a continuous supply of cooled fluid is needed, such as cooling lasers, X – ray tubes, and high – performance computing systems in research labs. In a physics lab using a high – power laser for material processing experiments, a recirculating chiller can prevent the laser from overheating by continuously cooling its components.
Components of Lab Chillers
Compressor
Function: As mentioned earlier, the compressor is the heart of the vapor – compression – based lab chiller. It is responsible for compressing the refrigerant vapor, increasing its pressure and temperature, which enables the refrigerant to release heat in the condenser.
Types: Different types of compressors are used in lab chillers, including reciprocating, rotary screw, and centrifugal compressors. Reciprocating compressors are suitable for small – to – medium – sized chillers due to their relatively simple design and lower cost. Rotary screw compressors offer higher efficiency and reliability, making them a popular choice for medium – to – large – capacity chillers. Centrifugal compressors are typically used in large – scale industrial – grade chillers but can also be found in some high – capacity laboratory cooling systems.
Condenser
Function: The condenser’s primary role is to remove heat from the high – pressure, high – temperature refrigerant vapor and convert it into a liquid. It transfers the heat to the cooling medium, whether it is air or water.
Types: Lab chillers can have either air – cooled or water – cooled condensers. Air – cooled condensers are simpler in design and do not require a separate water – supply system, making them more convenient for installations where water availability is limited. However, they may be less efficient in high – temperature environments. Water – cooled condensers, on the other hand, offer better heat – transfer performance and are often used in applications where higher cooling capacities and more stable operation are required, but they necessitate a reliable water – supply and treatment system.
Evaporator
Function: The evaporator is where the refrigerant absorbs heat from the process or equipment to be cooled, causing it to evaporate from a liquid – vapor mixture to a vapor state. This heat absorption provides the cooling effect necessary for laboratory operations.
Types: Evaporators can be of the shell – and – tube type, where the refrigerant flows through the tubes and the process fluid flows around the shell, or plate – type, which uses thin metal plates for enhanced heat – transfer efficiency. Plate – type evaporators are known for their compact size and high heat – transfer rates, making them suitable for space – constrained laboratory setups.
Expansion Device
Function: The expansion device, such as a thermostatic expansion valve (TXV) or a capillary tube, reduces the pressure of the high – pressure liquid refrigerant, allowing it to expand and cool down as it enters the evaporator.
Operation: A TXV controls the flow of refrigerant based on the superheat of the refrigerant vapor leaving the evaporator. It adjusts the opening of the valve to maintain an optimal refrigerant flow rate, ensuring efficient operation of the evaporator. In contrast, a capillary tube is a simple, fixed – orifice device that provides a constant pressure drop and is often used in smaller, less – complex chiller systems.
Control System
Function: The control system of a lab chiller monitors and regulates various parameters, including temperature, pressure, and refrigerant flow rate, to ensure the chiller operates efficiently and safely. It also allows users to set and adjust the desired cooling temperature according to experimental requirements.
Components: Modern lab chiller control systems typically include sensors (such as temperature sensors, pressure sensors, and flow sensors), controllers (which can be programmable logic controllers – PLCs or microprocessor – based controllers), and user interfaces (such as touchscreens or digital displays). Some advanced control systems can be integrated with laboratory information management systems (LIMS) for remote monitoring and data logging.
Applications of Lab Chillers
Biology Labs
Cell Culture: In cell – culture experiments, maintaining a precise temperature is crucial for cell growth and viability. Lab chillers are used to cool incubators, water baths, and refrigerated centrifuges. For example, some cell lines require incubation at temperatures slightly below room temperature, and a chiller – cooled incubator can provide the stable thermal environment needed for successful cell cultivation.
Protein Purification: During protein – purification processes, such as chromatography, maintaining the temperature of the buffer solutions and column is essential to preserve protein integrity. Lab chillers can cool the storage tanks for buffer solutions and the equipment used in the purification process, ensuring that the proteins remain in their native state.
Chemistry Labs
Reaction Control: Many chemical reactions are highly sensitive to temperature. Lab chillers are used to cool reaction vessels, especially for exothermic reactions, to prevent overheating and control the reaction rate. In organic synthesis, for instance, reactions involving the addition of reactive reagents may generate a significant amount of heat, and a chiller – cooled water jacket around the reaction flask can help maintain the desired reaction temperature.
Distillation and Evaporation: In distillation and evaporation processes, such as those using rotary evaporators, lab chillers are employed to cool the condensers. This allows for the efficient recovery of solvents and the separation of components in a mixture, ensuring the purity of the final products.
Physics Labs
Cryogenic Experiments: In some physics experiments, extremely low temperatures are required. Lab chillers can be used in conjunction with cryogenic systems to achieve and maintain these low temperatures. For example, in experiments involving the study of superconductivity, where materials need to be cooled to near – absolute – zero temperatures, a chiller can help with the pre – cooling stages and the overall temperature control of the cryogenic setup.
Cooling of High – Energy Equipment: High – energy physics experiments often involve equipment such as particle accelerators, which generate a large amount of heat during operation. Lab chillers are used to cool the magnets, power supplies, and other components of these systems to prevent overheating and ensure their proper functioning.
Selection Criteria for Lab Chillers
Cooling Capacity
Calculation: The cooling capacity of a lab chiller is measured in watts (W) or British Thermal Units per hour (BTU/h). It is essential to accurately calculate the cooling load required for the laboratory equipment and processes. This includes considering the heat generated by the equipment, the ambient temperature, and the heat transfer requirements. For example, if cooling a rotary evaporator with a known heat – generation rate and accounting for heat losses to the environment, the appropriate chiller with sufficient cooling capacity can be selected.
Margin for Growth: It is advisable to choose a chiller with a slightly higher cooling capacity than the current requirement to accommodate future equipment additions or changes in experimental procedures. This provides flexibility and ensures that the chiller can handle increased loads without compromising performance.
Temperature Range
Required Temperature: Different laboratory applications demand specific temperature ranges. Some processes may require cooling down to sub – zero temperatures, while others need only mild cooling. Ensure that the selected lab chiller can operate within the required temperature range with the necessary precision. For instance, in a pharmaceutical lab conducting freezing – point depression experiments, a chiller capable of reaching low sub – zero temperatures with high accuracy is essential.
Temperature Stability: In addition to the temperature range, temperature stability is crucial. A chiller with good temperature – control capabilities can maintain a consistent temperature, which is vital for experiments that are sensitive to temperature fluctuations. Look for chillers with advanced control systems and high – quality sensors to ensure stable temperature operation.
Coolant Type
Water vs. Water – Glycol Mixtures: The choice of coolant depends on the application. Water is a common coolant for applications where freezing is not a concern. However, in applications where the temperature may drop below the freezing point of water, a water – glycol mixture is preferred. Glycol acts as an antifreeze, preventing the coolant from freezing and potentially damaging the chiller and connected equipment.
Corrosion Resistance: If using a water – based coolant, consider the potential for corrosion in the chiller and the connected piping. Some chillers are designed with corrosion – resistant materials or come with built – in corrosion – prevention measures to ensure the longevity of the system when using water or water – glycol mixtures.
Noise Level
Laboratory Environment: In a laboratory setting, noise can be a significant distraction, especially in areas where concentration is required. When selecting a lab chiller, pay attention to its noise level, especially if it will be installed in an area close to workstations or sensitive equipment. Benchtop chillers are generally quieter than floor – standing models, but even among floor – standing chillers, there can be variations in noise output.
Noise – Reduction Features: Some chillers are equipped with noise – reduction features, such as sound – insulated enclosures, vibration – dampening mounts, and quieter fan designs. These features can help minimize the impact of the chiller’s noise on the laboratory environment.
Maintenance of Lab Chillers
Regular Cleaning
Condenser Cleaning: For air – cooled condensers, regular cleaning is essential to remove dust, dirt, and debris that can accumulate on the fins, reducing the heat – transfer efficiency. Use a soft brush or compressed air to clean the condenser fins gently. For water – cooled condensers, it is important to ensure that the water – inlet filters are clean and that the water – flow rate is optimal. Periodic descaling may also be required to remove mineral deposits that can form on the condenser tubes over time.
Evaporator and Coolant System Cleaning: The evaporator and the coolant – circulation system should also be kept clean. Sediments and contaminants in the coolant can affect heat transfer and potentially clog the system. Follow the manufacturer’s recommendations for draining, flushing, and refilling the coolant system at the appropriate intervals.
Refrigerant Checks
Level and Pressure Monitoring: Regularly monitor the refrigerant level and pressure in the chiller. Low refrigerant levels can indicate a leak in the system, which should be promptly detected and repaired. Use the pressure gauges and refrigerant – level indicators provided by the manufacturer to check these parameters. If a refrigerant leak is suspected, professional technicians should be called in to locate and repair the leak and recharge the system with the appropriate refrigerant.
Refrigerant Replacement: Over time, refrigerants may degrade or become contaminated. Follow the manufacturer’s guidelines for refrigerant replacement intervals to ensure optimal performance and compliance with environmental regulations. Some older refrigerants have been phased out due to their ozone – depletion potential or high global – warming potential, and it is important to use environmentally friendly alternatives.
Component Inspection
Compressor and Pump Inspection: Regularly inspect the compressor and pumps for signs of wear, such as unusual noises, vibrations, or leaks. Check the lubrication levels of the compressor and pumps and replace the lubricant as recommended. Faulty compressors or pumps can lead to reduced cooling performance and potentially cause system failures if not addressed promptly.
Sensor and Control System Checks: Test the sensors and control system regularly to ensure accurate temperature and pressure readings and proper operation of the chiller. Calibrate the sensors as needed to maintain the precision of the temperature – control system. Malfunctioning sensors or control systems can result in incorrect temperature settings and inefficient operation of the chiller.
In conclusion, lab chillers are indispensable tools in modern scientific research, enabling precise temperature control across a wide range of laboratory applications. Understanding their working principles, types, components, applications, selection criteria, and maintenance requirements is essential for researchers, laboratory managers, and technicians. By making informed decisions when selecting and properly maintaining lab chillers, laboratories can ensure reliable, efficient, and accurate experimental results, contributing to the advancement of scientific knowledge and innovation.
Related recommendations
propylene glycol for chiller
142In chiller systems, maintaining an efficient and reliable cooling process is of utmost importance. Propylene glycol has emerged as a popular choice for use in chiller coolants. It is a clear, colo...
View detailsunit of chiller capacity
117Common Units of Chiller CapacityBritish Thermal Units per Hour (BTU/h)The British Thermal Unit (BTU) is a traditional unit of energy widely used in the United States and some other regions. One ...
View detailschiller range
301Understanding the Chiller Range The chiller range encompasses a variety of cooling systems that are crucial for temperature control in numerous industrial applications. Chillers, also known as ...
View detailspropylene glycol for chiller
430Propylene Glycol for Chiller Systems: An In-Depth Analysis Understanding Propylene Glycol in Chillers Propylene glycol is a popular fluid used in chiller systems, particularly for its effect...
View details
HelloPlease log in