industrial process cooling
Industrial Process Cooling: A Comprehensive Guide
I. Introduction
Industrial process cooling refers to the set of techniques and systems employed to remove heat generated during various industrial manufacturing and production processes. Heat is an inevitable by – product in many industrial operations, and if not properly managed, it can lead to a range of problems, from equipment malfunction to a decline in product quality. Therefore, effective industrial process cooling is essential for the smooth and efficient running of industrial facilities.
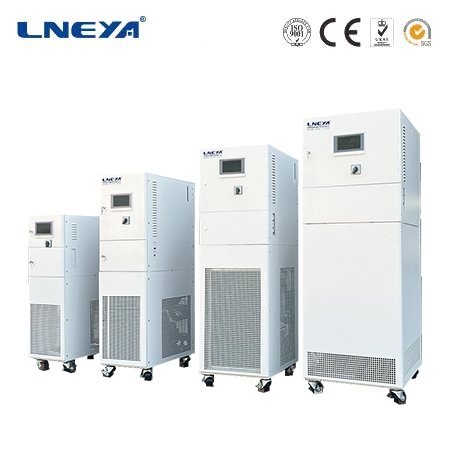
II. Importance of Industrial Process Cooling
Preventing Equipment Overheating
Industrial machinery and equipment often generate a significant amount of heat during operation. For example, in metalworking processes like machining, the friction between the cutting tool and the workpiece can cause the tool and the workpiece to heat up rapidly. If the temperature exceeds the equipment’s rated operating temperature, it can lead to premature wear, deformation, or even failure of the components. Cooling systems help to maintain the equipment at an optimal temperature, extending its lifespan and reducing the frequency of costly repairs and replacements.
Ensuring Product Quality
In many industries, temperature control is critical for product quality. In the food and beverage industry, for instance, the temperature during processing, storage, and transportation of products can affect their taste, texture, and shelf – life. In the pharmaceutical industry, precise temperature control is necessary to ensure the stability and efficacy of drugs. Industrial process cooling systems enable manufacturers to maintain the required temperature conditions throughout the production process, resulting in high – quality products that meet industry standards.
Enhancing Process Efficiency
When equipment operates at an optimal temperature, the overall process efficiency can be improved. For example, in chemical reactions, maintaining the right temperature can enhance the reaction rate and selectivity, leading to higher yields. Cooling systems also help to prevent thermal stress on equipment, which can cause inefficiencies due to component expansion and contraction. By providing a stable thermal environment, industrial process cooling contributes to more consistent and efficient production.
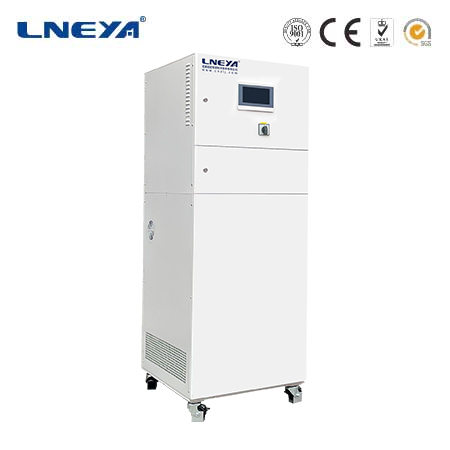
III. Cooling Methods in Industrial Processes
Air – Cooling
Air – cooling is a relatively simple and cost – effective method of industrial process cooling. In this method, ambient air is used to remove heat from the equipment or process. For small – scale operations or in areas with low heat loads, natural air convection may be sufficient. In such cases, heat is transferred from the hot surface of the equipment to the surrounding air due to the temperature difference. For larger heat loads, forced – air cooling is often employed. Fans or blowers are used to direct air over the hot surfaces, increasing the rate of heat transfer. Air – cooling is commonly used in applications such as cooling of electrical enclosures, where the heat generated by electronic components needs to be dissipated.
Water – Cooling
Water – cooling is a more efficient method compared to air – cooling due to water’s higher specific heat capacity. Water can absorb a large amount of heat without a significant increase in its own temperature. In industrial water – cooling systems, water is circulated through pipes or channels in close proximity to the heat – generating equipment. Heat is transferred from the equipment to the water, and the heated water is then either cooled in a cooling tower or a heat exchanger before being recirculated. Water – cooling is widely used in applications such as power generation, where large – scale cooling of engines and turbines is required.
Refrigerant – Based Cooling
Refrigerant – based cooling systems, such as industrial chillers, are used when a lower temperature is required for cooling. These systems operate on the principle of the refrigeration cycle. A compressor increases the pressure and temperature of a refrigerant gas. The hot, high – pressure gas then passes through a condenser, where it releases heat to the surrounding environment and condenses into a liquid. The liquid refrigerant is then expanded through an expansion valve, causing it to cool down. This cold refrigerant is used in an evaporator to absorb heat from the process fluid or equipment that needs to be cooled. Refrigerant – based cooling is commonly used in industries like food and beverage, pharmaceuticals, and plastics, where precise temperature control at low temperatures is essential.
IV. Components of Industrial Process Cooling Systems
Chillers
Chillers are a key component of refrigerant – based cooling systems. As mentioned earlier, they cool a fluid (usually water or a glycol – water mixture) to a specific temperature. There are different types of chillers, including mechanical vapor – compression chillers and absorption chillers. Mechanical vapor – compression chillers use a compressor to drive the refrigeration cycle, while absorption chillers use a heat source (such as waste heat from industrial processes) to separate the refrigerant from an absorbent, eliminating the need for a compressor in some cases.
Heat Exchangers
Heat exchangers play a crucial role in industrial process cooling by facilitating the transfer of heat between two fluids. In water – cooling systems, shell – and – tube heat exchangers are commonly used. In this type of heat exchanger, the hot process fluid flows through the tubes, while the cooling water flows around the tubes in the shell. Heat is transferred through the tube walls. Plate – type heat exchangers are also popular, especially in applications where a high heat transfer efficiency and a compact design are required. They consist of a series of plates with channels for the hot and cold fluids, and the close proximity of the plates allows for efficient heat transfer.
Pumps
Pumps are used to circulate the cooling fluid (water, refrigerant, or air) through the cooling system. In water – cooling systems, centrifugal pumps are commonly used to move the water from the chiller or cooling tower to the heat – consuming equipment and back. The pump’s capacity is sized according to the required flow rate of the cooling fluid, which depends on the heat load of the industrial process. In refrigerant – based systems, refrigerant pumps may be used to circulate the refrigerant within the system.
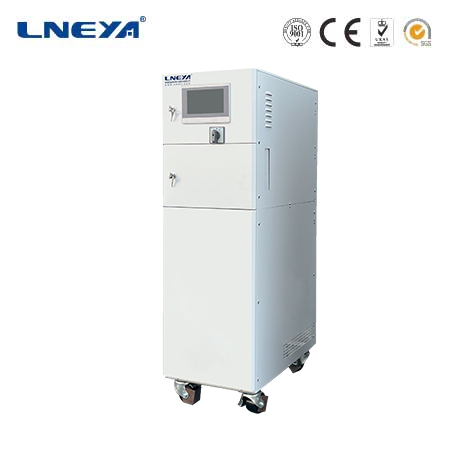
Cooling Towers
Cooling towers are an important part of water – cooling systems. Their main function is to cool the warm water that has absorbed heat from the industrial process. In a cooling tower, the warm water is sprayed or distributed over a large surface area, and as it comes into contact with air (either through natural or forced convection), some of the water evaporates. The latent heat of vaporization is taken from the remaining water, cooling it down. The cooled water is then collected and recirculated back to the process.
V. Applications in Different Industries
Manufacturing Industry
In the manufacturing industry, industrial process cooling is used in a wide range of processes. In plastic injection molding, cooling channels are incorporated into the molds to rapidly cool the molten plastic, allowing it to solidify into the desired shape. In metal casting, cooling is necessary to control the solidification rate of the molten metal, which affects the microstructure and mechanical properties of the cast part. In electronics manufacturing, cooling is crucial for maintaining the performance and reliability of electronic components, such as cooling the CPU in computers.
Food and Beverage Industry
In the food and beverage industry, industrial process cooling is essential at every stage of production. During food processing, chilled water is used to cool cooked products, prevent spoilage, and maintain product quality. In beverage production, cooling is required for fermentation, carbonation, and bottling processes. For example, in the production of beer, the fermentation process needs to be carried out at a specific temperature, and cooling systems are used to maintain this temperature.
Chemical Industry
In the chemical industry, many reactions are exothermic, meaning they generate heat. Industrial process cooling is used to control the temperature of these reactions, ensuring their safe and efficient operation. Cooling is also important for storing and transporting chemical products, as some chemicals may degrade or become unstable at high temperatures. For example, in the production of polymers, precise temperature control during the polymerization reaction is necessary to obtain the desired polymer properties.
Power Generation Industry
In power generation, whether it is from fossil fuels, nuclear energy, or renewable sources like solar and geothermal, industrial process cooling is vital. In fossil – fuel – powered power plants, cooling systems are used to condense the steam after it has passed through the turbine, converting it back into water for reuse in the boiler. In nuclear power plants, large – scale cooling systems are required to remove the heat generated by the nuclear reactor. In solar thermal power plants, cooling is needed to maintain the efficiency of the power – generating equipment.
VI. Maintenance and Management of Industrial Process Cooling Systems
Regular Checks and Inspections
Regular maintenance of industrial process cooling systems is essential to ensure their proper operation. This includes checking the refrigerant levels in chillers, inspecting the pumps for any signs of wear or leakage, and examining the heat exchangers for fouling or corrosion. The cooling towers should also be inspected regularly for proper water distribution, the presence of biological growth, and the condition of the fan motors. Regular visual inspections and performance monitoring can help detect potential problems early, preventing unexpected breakdowns.
Water Treatment
In water – cooling systems, water treatment is crucial to prevent issues such as corrosion, scaling, and biological growth. Corrosion can damage the pipes, heat exchangers, and other components of the cooling system, reducing its efficiency and lifespan. Scaling, caused by the deposition of minerals in the water, can also impede heat transfer. Biological growth, such as algae and bacteria, can clog the pipes and cooling towers. Water treatment methods may include the addition of corrosion inhibitors, scale – control chemicals, and biocides to maintain the quality of the cooling water.
Energy Management
With the increasing focus on energy efficiency and cost – reduction, energy management in industrial process cooling systems is becoming more important. This can involve the use of variable – speed drives for pumps and fans, which can adjust the flow rate and speed based on the actual cooling load. Energy – efficient chillers and heat exchangers can also be installed to reduce energy consumption. Monitoring and optimizing the operation of the cooling system can help identify opportunities for energy savings without sacrificing cooling performance.
VII. Future Trends in Industrial Process Cooling
Energy – Efficiency Improvements
As energy costs continue to rise and environmental concerns become more prominent, there is a growing trend towards developing more energy – efficient industrial process cooling systems. This includes the use of advanced refrigeration technologies, such as magnetic refrigeration and absorption heat pumps, which have the potential to reduce energy consumption significantly. Additionally, the integration of energy – recovery systems, where waste heat from one process is used for heating or cooling in another, is becoming more common.
Sustainable Cooling Solutions
There is a shift towards more sustainable cooling solutions in the industrial sector. This involves the use of environmentally friendly refrigerants with low global warming potential (GWP) and ozone – depletion potential (ODP). For example, the adoption of natural refrigerants like carbon dioxide (CO₂), ammonia (NH₃), and hydrocarbons is increasing. Sustainable cooling also includes the use of renewable energy sources, such as solar and wind power, to operate cooling systems.
Smart and Automated Cooling Systems
The future of industrial process cooling lies in the development of smart and automated systems. These systems use sensors and control algorithms to monitor and adjust the cooling process in real – time based on the actual heat load and operating conditions. Smart cooling systems can optimize energy usage, improve cooling performance, and provide early warnings of potential equipment failures. The integration of cooling systems with the overall industrial Internet of Things (IIoT) infrastructure allows for better connectivity and control, enabling more efficient operation of industrial facilities.
In conclusion, industrial process cooling is a complex and vital aspect of modern industrial operations. Understanding its methods, components, applications, maintenance, and future trends is essential for industries to operate efficiently, produce high – quality products, and meet environmental and economic goals.
Related recommendations
How to handle the malfunction of the evaporator chiller?
985How to handle the malfunction of the evaporator chiller? 1. Exhaust when the pressure is high. There may be a problem with heat dissipation. When the high and low pressure of the...
View detailsindustrial heater company
315The Role of Industrial Heater Companies in Modern Industry Industrial heater companies are essential providers of heating solutions that enable numerous industries to maintain optimal operating...
View detailslarge environmental chamber
389Introduction to Large Environmental Chambers Large environmental chambers are engineered to simulate various environmental conditions for testing the performance, reliability, and durability of...
View detailswater cooled chiller installation
393Water-Cooled Chiller Installation: A Comprehensive Guide The installation of a water-cooled chiller is a complex process that requires careful planning and execution to ensure the system operat...
View details
HelloPlease log in