industrial oil heating system
Industrial Oil Heating System: An In – Depth Explanation
Industrial oil heating systems are fundamental in a wide range of industrial processes. These systems are designed to heat oil, which then serves as a heat – transfer medium to provide thermal energy for various industrial operations.
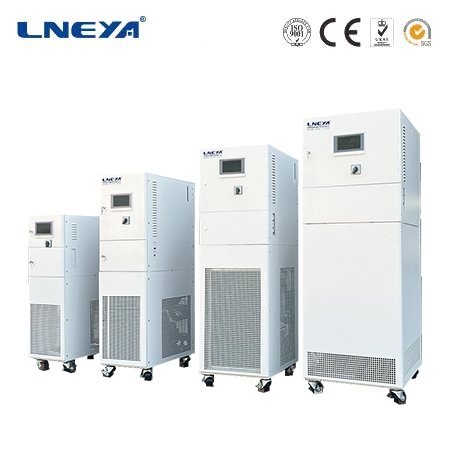
Working Mechanism
At the core of an industrial oil heating system is the process of heat transfer to the oil. In a fuel – fired system, a burner mixes fuel (such as natural gas, oil, or coal) with air in the correct ratio and ignites the mixture. The resulting combustion generates heat, which is transferred to the oil in a heat – exchanger or a directly – fired heater. In an electric – heated system, electric heating elements convert electrical energy into heat, which is then absorbed by the oil. The heated oil is circulated through a network of pipes to the areas where heat is required. As the oil releases its heat to the industrial process, it cools down and returns to the heater to be reheated, forming a continuous cycle.
Key Components
Heater: This is the central component where the oil is heated. It can be a direct – fired heater, where the oil is in direct contact with the heat source, or an indirect – fired heater, which uses a heat exchanger to transfer heat to the oil. Heaters are designed to withstand high temperatures and pressures and are typically made of high – quality materials such as stainless steel or alloy steel.
Pump: The pump is responsible for circulating the oil within the system. It ensures a continuous flow of oil from the heater to the heat – consuming equipment and back. Pumps are selected based on the required flow rate, pressure, and the viscosity of the oil.
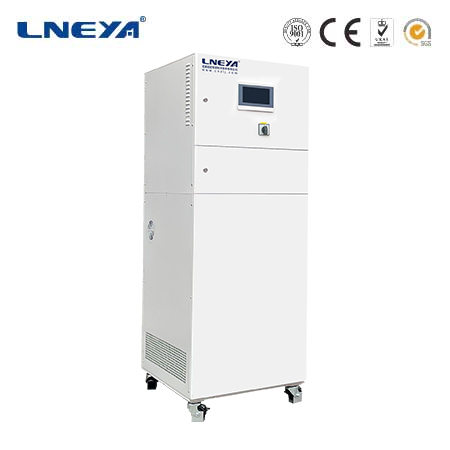
Heat Exchanger: In indirect – fired systems, the heat exchanger plays a crucial role. It allows the transfer of heat from the combustion gases or another heat source to the oil without direct contact. Heat exchangers are designed to maximize the heat – transfer efficiency and are available in various types, such as shell – and – tube, plate – type, and finned – tube heat exchangers.
Types of Industrial Oil Heating Systems
Direct – Fired Systems: In these systems, the oil is directly heated by the combustion of fuel. The heat is transferred directly to the oil in a combustion chamber. Direct – fired systems are known for their high heating efficiency and fast response times. However, they require careful safety measures due to the direct contact between the oil and the heat source.
Indirect – Fired Systems: Indirect – fired systems use a heat exchanger to transfer heat from the combustion gases or another heat source to the oil. This separation of the heat source and the oil provides an extra layer of safety. These systems are often used in applications where a higher level of safety is required, such as in the food and pharmaceutical industries.
Applications
Manufacturing Industry: Industrial oil heating systems are used in manufacturing processes such as plastic molding, metal casting, and drying. In plastic molding, the heated oil is used to maintain the temperature of the molds, ensuring the proper formation of plastic products.
Petrochemical Industry: In petrochemical plants, oil heating systems are used for processes like distillation, cracking, and polymerization. The precise temperature control provided by these systems is crucial for the production of high – quality petrochemical products.
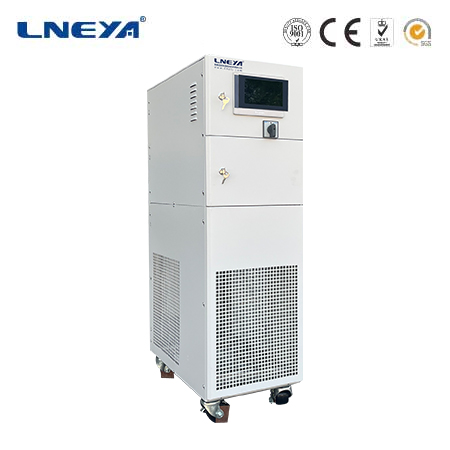
Power Generation: In some power – generation processes, such as in certain types of boilers, industrial oil heating systems are used to pre – heat the oil before combustion, improving the efficiency of the power – generation process.
Advantages
High – Temperature Operation: Industrial oil heating systems can operate at high temperatures, making them suitable for applications that require high – temperature heat sources. The heat – transfer oil can reach temperatures well above the boiling point of water, providing a more efficient way to transfer heat in high – temperature processes.
Energy – Efficiency: These systems are generally energy – efficient. The heat – transfer oil has good heat – storage and heat – transfer properties, allowing for efficient transfer of heat from the heater to the industrial process. This results in lower energy consumption compared to some other heating methods.
Flexibility: Industrial oil heating systems can be customized to meet the specific requirements of different industrial processes. They can be designed to operate with different types of fuels, and the heating capacity and temperature range can be adjusted according to the needs of the application.
Factors to Consider When Selecting an Industrial Oil Heating System
Heating Capacity: The system should have sufficient heating capacity to meet the heat requirements of the industrial process. This depends on factors such as the size of the equipment to be heated, the heat – consuming rate of the process, and the desired operating temperature.
Temperature Range: Different industrial processes require different temperature ranges. The oil heating system should be able to operate within the required temperature range accurately. Some processes may require precise temperature control within a narrow range, while others can tolerate a wider temperature variation.
Safety Requirements: Safety is a crucial factor when selecting an industrial oil heating system. Direct – fired systems may require more stringent safety measures due to the direct contact between the oil and the heat source. Indirect – fired systems, on the other hand, offer a higher level of safety. The system should also comply with relevant safety standards and regulations.
Cost – Effectiveness: This includes the initial investment cost, the operating cost (such as fuel or electricity cost), and the maintenance cost. A cost – effective system should have a reasonable initial investment and low operating and maintenance costs over its lifespan.
In conclusion, industrial oil heating systems are essential in modern industrial processes. Understanding their working mechanism, components, types, applications, advantages, and selection criteria is crucial for industries to make informed decisions when choosing a heating solution.
Related recommendations
heating and cooling products
399Heating and Cooling Products: A Comprehensive Overview Introduction to Heating and Cooling ProductsHeating and cooling products are integral to the comfort and functionality of residential, com...
View detailsWhat is the reason why the cryogenic chiller does not cool?
892What is the reason why the cryogenic chiller does not cool? During the operation of the chiller, the liquid refrigerant in the evaporator continuously absorbs heat from the water and be...
View detailsworking of air cooled chiller
44The Refrigeration Cycle: Core Working ProcessThe working of an air cooled chiller is centered on the refrigeration cycle, which consists of four sequential stages, each facilitated by key compone...
View detailsrecirculating chiller india
64Introduction to Recirculating Chillers in IndiaRecirculating chillers have emerged as a vital component in India's industrial and scientific infrastructure. These devices, which continuously circ...
View details
HelloPlease log in