high pressure steam system
Introduction to High Pressure Steam System
A high pressure steam system is a specialized setup that generates, distributes, and utilizes steam at pressures significantly above atmospheric levels, typically ranging from 100 psi (pounds per square inch) to over 2000 psi. Steam, as a versatile medium, excels at storing and transferring thermal energy efficiently. High pressure steam systems capitalize on this property, enabling processes that demand high – intensity heat transfer, mechanical power, or precise temperature control. These systems are widely employed across various industries, from power plants generating electricity to factories manufacturing goods and facilities processing food. The ability to operate at high pressures allows for increased energy density in steam, facilitating more efficient energy transfer and enabling a broader range of applications compared to low – pressure steam systems.
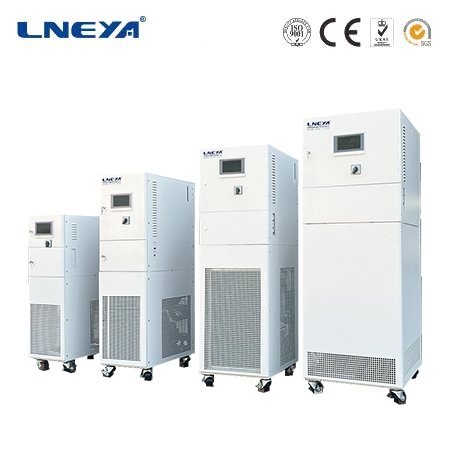
Key Components of High Pressure Steam System
Boilers
Boilers are the heart of high pressure steam systems, responsible for converting water into steam. They come in various types, each with distinct features suitable for different applications.
Water – Tube Boilers: In water – tube boilers, water circulates through tubes while hot combustion gases flow around them. This design allows for higher pressure and temperature operation compared to fire – tube boilers. The tubes are typically arranged in a drum or multiple drums, and the system can be designed as a once – through or a recirculating type. Once – through boilers are often used in large – scale power plants, where water is converted to steam in a single pass through the tubes without the need for a large drum for water storage. Recirculating boilers, on the other hand, continuously circulate a portion of the water back to the tubes for reheating, providing more stable steam output.
Fire – Tube Boilers: Fire – tube boilers feature hot gases passing through tubes submerged in water. They are generally more suitable for lower to moderate pressure applications and smaller – scale operations. Fire – tube boilers are known for their simplicity and relatively lower initial cost. However, their maximum operating pressure and steam output capacity are typically more limited compared to water – tube boilers. The design consists of a cylindrical shell with multiple tubes running through it, and the combustion chamber is often located either at one end or integrated within the shell.
Turbines
Steam turbines are crucial components in high pressure steam systems, especially in power generation. They convert the thermal energy of high pressure steam into mechanical energy.
Impulse Turbines: Impulse turbines operate on the principle of impulse force. High pressure steam is directed onto the blades of the turbine through nozzles, causing the blades to rotate due to the change in momentum of the steam. The steam expands primarily in the nozzles, and the pressure drop occurs mainly in these nozzles rather than across the turbine blades. Impulse turbines are typically used for high – speed applications and can be designed as single – stage or multi – stage, with multi – stage designs providing higher efficiency and power output by utilizing the steam’s energy more effectively through successive stages.
Reaction Turbines: Reaction turbines work based on the principle of both impulse and reaction forces. In these turbines, steam expands both in the nozzles and as it passes over the turbine blades. The blades are shaped such that the steam not only impinges on them but also causes a reaction force as it changes direction and pressure while flowing through the blade passages. Reaction turbines are more efficient than impulse turbines in many applications, especially for large – scale power generation, as they can extract more energy from the steam over a wider range of operating conditions.
Valves
Valves play a vital role in controlling the flow, pressure, and direction of steam within high pressure steam systems.
Safety Valves: Safety valves are critical components designed to protect the system from overpressure situations. When the pressure within the system exceeds the preset safety limit, the safety valve automatically opens, releasing steam to reduce the pressure. They are typically spring – loaded, with the spring force set to a specific pressure value corresponding to the maximum allowable pressure of the system. Safety valves are required by regulations in all high pressure steam systems to prevent catastrophic failures due to excessive pressure.
Control Valves: Control valves are used to regulate the flow rate of steam, allowing operators to adjust the steam supply to different processes or equipment. These valves can be operated manually or automatically, with automated control valves often integrated into a control system that monitors and adjusts the steam flow based on parameters such as temperature, pressure, or process demand. Different types of control valves, such as globe valves, gate valves, and butterfly valves, are selected based on the specific requirements of the system, including the desired flow characteristics, pressure drop, and degree of control precision.
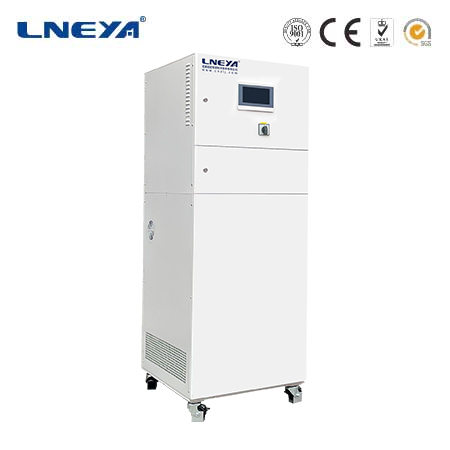
Pipes and Fittings
Pipes and fittings are used to transport high pressure steam from the boiler to various points of use within the system.
Pipe Materials: High pressure steam pipes are typically made from materials that can withstand high temperatures and pressures, such as carbon steel, stainless steel, and alloy steel. Carbon steel is commonly used for lower – temperature and lower – pressure applications due to its relatively low cost and good mechanical properties. Stainless steel is preferred in applications where corrosion resistance is crucial, such as in food processing or chemical plants. Alloy steel, which contains elements like chromium, molybdenum, and vanadium, offers enhanced strength and heat resistance, making it suitable for high – temperature and high – pressure applications in power plants and refineries.
Fittings: Fittings, including elbows, tees, reducers, and couplings, are used to connect pipes, change the direction of steam flow, or adapt to different pipe sizes. They are designed to maintain the structural integrity and pressure – holding capacity of the piping system. Welded fittings are often used in high pressure steam systems for their strength and leak – tightness, while flanged fittings provide ease of assembly and disassembly for maintenance and repair purposes.
Working Principles of High Pressure Steam System
Steam Generation
In the boiler, heat is transferred to water to convert it into steam. The heat source can be various fuels, such as natural gas, oil, coal, or biomass, or it can be from other sources like waste heat recovery systems or nuclear reactions. In a fuel – fired boiler, the fuel is burned in the combustion chamber, and the resulting hot gases transfer heat to the water in the boiler tubes through conduction, convection, and radiation. As the water absorbs heat, it undergoes a phase change from liquid to vapor, forming steam. The temperature and pressure of the steam generated depend on factors such as the type of boiler, the heat input rate, and the design of the boiler’s steam – generating components.
Steam Distribution
Once generated, high pressure steam is distributed through a network of pipes to different parts of the system where it is needed. The steam’s high pressure provides the driving force for its flow through the pipes. Pressure – reducing valves may be used along the distribution network to lower the steam pressure to the appropriate level required by different processes or equipment. Insulation is applied to the pipes to minimize heat losses during distribution, ensuring that the steam retains its high temperature and energy content as it reaches the point of use. The layout of the piping system is carefully designed to optimize steam flow, minimize pressure drops, and ensure even distribution of steam to all connected equipment.
Steam Utilization
High pressure steam can be utilized in multiple ways depending on the application. In power generation, steam is directed into steam turbines, where its thermal energy is converted into mechanical energy as the steam expands and drives the turbine blades. The turbine is connected to a generator, which converts the mechanical energy into electrical energy. In industrial processes, high pressure steam can be used for heating, such as in heat exchangers to warm up process fluids or in drying applications to remove moisture from materials. It can also be used for mechanical power, for example, in steam – powered pumps or compressors. Additionally, in some cases, high pressure steam is used for cleaning purposes, where its high temperature and pressure help to remove dirt, grease, and other contaminants from surfaces.
Applications of High Pressure Steam System
Power Generation
High pressure steam systems are the backbone of most thermal power plants. In a coal – fired power plant, for example, coal is burned in a boiler to generate high pressure steam. This steam is then fed into a steam turbine, which drives a generator to produce electricity. The high pressure and temperature of the steam allow for a more efficient conversion of thermal energy into electrical energy compared to lower – pressure systems. Similarly, in natural gas – fired combined – cycle power plants, high pressure steam is generated in a heat recovery steam generator (HRSG) using the exhaust heat from a gas turbine. The steam then powers a steam turbine, further enhancing the overall efficiency of the power – generation process.
Manufacturing Industry
In the manufacturing sector, high pressure steam systems are used in a wide range of processes. In the chemical industry, high pressure steam is used to heat reactors, facilitating chemical reactions that require high temperatures and pressures. For example, in the production of fertilizers, steam is used to heat the reaction vessels where raw materials are combined to form the final products. In the textile industry, high pressure steam is employed for processes such as dyeing, printing, and drying of fabrics. The steam provides the necessary heat to activate dyes, set prints, and remove moisture from the fabrics quickly and efficiently. Additionally, in the paper manufacturing industry, high pressure steam is used to cook wood chips into pulp, as well as for drying and pressing the paper sheets during the production process.
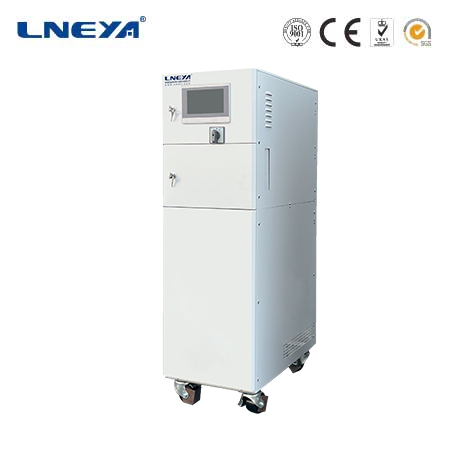
Food Processing Industry
The food processing industry relies on high pressure steam systems for various operations. Steam is used for cooking, sterilizing, and pasteurizing food products. In large – scale food production facilities, high pressure steam cookers are used to prepare large quantities of food quickly and uniformly. Steam sterilization is crucial for ensuring the safety of food products by killing harmful bacteria, viruses, and other pathogens. For example, canned foods are often sterilized using high pressure steam to extend their shelf life. In the dairy industry, high pressure steam is used for pasteurizing milk and other dairy products, maintaining their nutritional value while eliminating potential contaminants.
Other Applications
High pressure steam systems also find applications in other areas. In the oil and gas industry, steam is injected into oil wells to reduce the viscosity of heavy oil, making it easier to extract. This process, known as steam flooding or steam injection, helps to increase oil recovery rates. In the healthcare sector, high pressure steam is used in autoclaves for sterilizing medical equipment, surgical instruments, and laboratory supplies. The high temperature and pressure of the steam ensure complete elimination of all microorganisms, ensuring the safety and sterility of the equipment used in medical procedures.
Design and Installation of High Pressure Steam System
Design
Designing a high pressure steam system requires a detailed understanding of the application’s requirements, including the steam demand, operating pressure and temperature, and the layout of the facility. The type and size of the boiler are selected based on the required steam output and the available fuel source. The piping system is designed to handle the high pressure and temperature of the steam, with proper sizing of pipes to ensure adequate steam flow and minimize pressure drops. The placement of valves, including safety valves and control valves, is carefully planned to ensure effective control of the steam flow and safety of the system. Additionally, the design should incorporate measures for heat recovery and energy efficiency, such as using waste heat from the steam system to preheat water or other process fluids.
Installation
Installation of a high pressure steam system must be carried out by qualified professionals following strict safety and regulatory standards. Boilers need to be installed in a well – ventilated area, with proper connections to the fuel supply, water supply, and flue gas exhaust systems. Piping should be installed with proper supports, slopes, and insulation to ensure safe and efficient steam distribution. Valves and fittings are installed according to the design specifications, with careful attention to ensuring leak – tight connections. Electrical connections for control systems and monitoring devices are made by licensed electricians. After installation, the system undergoes a series of tests, including pressure testing, leak testing, and functional testing, to ensure that it operates safely and meets the design requirements.
Maintenance and Safety of High Pressure Steam System
Maintenance
Regular maintenance is essential to keep a high pressure steam system in optimal working condition. This includes routine inspections of the boiler, checking for signs of corrosion, scale buildup, or leaks. The water treatment system, which is crucial for preventing scale formation and maintaining the quality of the boiler water, needs to be monitored and maintained regularly. Valves should be inspected for proper operation, and any sticking or leaking valves should be repaired or replaced promptly. Piping should be checked for signs of wear, corrosion, or damage, and insulation should be repaired if it is damaged to minimize heat losses. Additionally, the control system, including temperature and pressure sensors, should be calibrated regularly to ensure accurate monitoring and control of the system.
Safety
Safety is of utmost importance in high pressure steam systems due to the potential hazards associated with high pressure and high temperature steam. The system should be equipped with proper safety devices, including safety valves, pressure gauges, and temperature sensors, which are regularly inspected and calibrated to ensure their reliability. Regular safety training should be provided to all personnel involved in the operation and maintenance of the system to ensure they are aware of the potential hazards and know how to respond in case of an emergency. Safety protocols, such as lockout – tagout procedures for maintenance work, should be strictly followed to prevent accidental release of steam or injury to personnel. Additionally, the system should be designed and operated in compliance with all relevant safety codes and regulations to minimize the risk of accidents and ensure the safety of the facility and its occupants.
Future Developments in High Pressure Steam Systems
As industries strive for greater energy efficiency and sustainability, high pressure steam systems are also evolving. Research and development efforts are focused on improving boiler efficiency, reducing emissions from fuel – fired boilers, and enhancing the integration of renewable energy sources into steam – generation processes. For example, the use of biomass fuels in boilers is increasing as a more sustainable alternative to fossil fuels. Additionally, advancements in materials science are leading to the development of pipes and components that can withstand even higher pressures and temperatures, enabling more efficient steam generation and utilization. Smart control systems are also being integrated into high pressure steam systems, allowing for real – time monitoring and optimization of the system’s operation, further improving energy efficiency and reducing operating costs.
In conclusion, high pressure steam systems are complex yet essential systems that play a vital role in numerous industries. Understanding their components, working principles, applications, design, installation, maintenance, and safety aspects is crucial for ensuring their efficient and safe operation. With continuous technological advancements, high pressure steam systems are set to become even more efficient, sustainable, and integral to various industrial and commercial operations in the future.
Related recommendations
What is the maintenance method for non circulating cold water in chiller for laboratory?
925What is the maintenance method for non circulating cold water in chiller for laboratory? The water level in the water tank is lower than the water inlet of the water pump Solutio...
View detailschiller kw
246Chiller kw In the world of refrigeration, the term "chiller kw" is of great importance. Kilowatts (kw) are a unit of measurement used to express both the power consumption of a chiller and its ...
View detailschiller items
330Understanding Chiller Items Chiller items encompass the range of components, technologies, and systems that facilitate cooling in various applications. Chillers are essential in maintaining opt...
View detailswater cooled package unit
296Water-Cooled Package Unit: Efficient and Compact HVAC Solution Water-cooled package units are a type of HVAC equipment that provides cooling through a water-cooled condenser, offering an effici...
View details
HelloPlease log in