glycol unit cooler
Glycol Unit Coolers: Efficient Cooling for Glycol Mixtures
Introduction
Glycol unit coolers are specialized refrigeration units designed to cool glycol mixtures, which are commonly used in industrial processes due to their freeze protection and heat transfer properties. These coolers are crucial in maintaining desired temperatures in various applications such as storage coolers, freezers in restaurants, convenience stores, warehouses, and supermarkets.
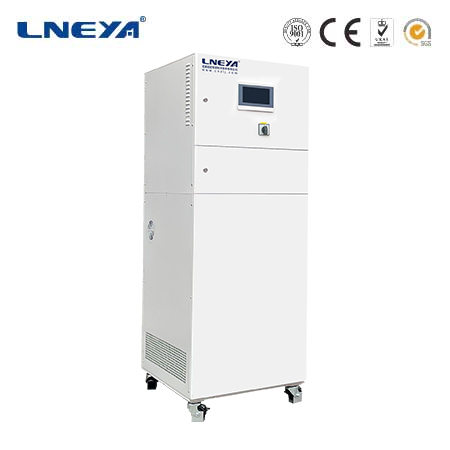
Design and Components
Glycol unit coolers are composed of several key components:
Evaporator: Where the glycol mixture absorbs heat, cooling the fluid.
Condenser: Where the heat absorbed by the glycol is released to the ambient environment.
Fans: Facilitate the heat rejection process by enhancing air circulation across the condenser.
Defrost System: Removes frost buildup from the evaporator, ensuring efficient heat transfer.
Applications
Glycol unit coolers are used in a variety of applications where precise temperature control is required:
Food Processing: Maintaining consistent temperatures in processing areas and cold storage.
Pharmaceutical: Cooling equipment and processes that require stable temperatures.
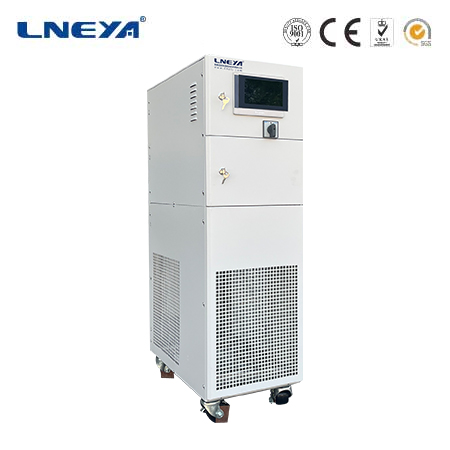
Ice Rinks: Keeping the ice surface frozen in a controlled environment.
Industrial Manufacturing: Cooling machinery and processes to ensure optimal performance.
Performance Factors
The performance of glycol unit coolers is determined by several factors:
Entering Air Temperature: The temperature of the air entering the cooler affects the cooling capacity.
Fluid Temperature: The temperature of the glycol mixture being cooled.
GPM Flow Rate: The rate at which the glycol mixture flows through the system.
Glycol Type and Mixture Percentage: The type of glycol and its concentration in the mixture impact the cooling efficiency.
Maintenance
Proper maintenance is essential for the optimal performance and longevity of glycol unit coolers:
Cleaning: Regularly cleaning the evaporator and condenser coils ensures efficient heat transfer.
Inspecting: Periodic inspections help identify potential issues such as leaks or worn components.
Testing Glycol: Regularly testing the glycol for contamination and adjusting the concentration as needed.
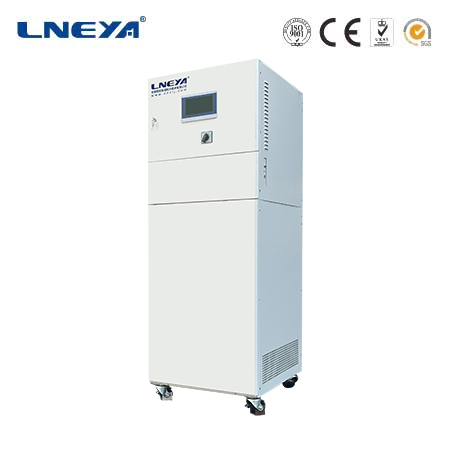
Efficiency and Considerations
The efficiency of glycol unit coolers can be optimized by:
Proper Sizing: Ensuring the cooler is appropriately sized for the heat load.
Regular Servicing: Scheduling regular servicing to keep the unit operating at peak efficiency.
Energy Management: Implementing energy management practices, such as variable speed drives on fans, to reduce energy consumption.
Conclusion
Glycol unit coolers are vital for applications requiring glycol mixture cooling. By understanding their design, applications, performance factors, and maintenance requirements, operators can ensure efficient and reliable cooling. Regular maintenance and proper sizing contribute to the longevity and optimal efficiency of glycol unit coolers.
Related recommendations
How to reduce vibration and noise in air cooled water chiller system?
952How to reduce vibration and noise in air cooled water chiller system? 1. The on-site rotor dynamic balance method for air-cooled chiller compressors reduces direct current vibration. ...
View detailstypes of water chiller
469Types of Water Chillers Water chillers are refrigeration systems that use water as a secondary coolant to provide cooling for various applications. They are categorized based on the type of com...
View detailschillers uk
157Chillers in the UK: A Comprehensive GuideChillers play a vital role in the United Kingdom across a wide range of industries and applications. They are used to remove heat from a process or space,...
View detailsheating and cooling systems
311Introduction to Heating and Cooling Systems Heating and cooling systems play a vital role in ensuring the comfort and well-being of occupants in residential, commercial, and industrial building...
View details
HelloPlease log in