electric heaters for liquid
Electric Heaters for Liquid
Electric heaters for liquid are essential equipment in many industries and applications where there is a need to increase the temperature of various liquids. They operate based on the principle of converting electrical energy into heat energy, which is then transferred to the liquid to raise its temperature.
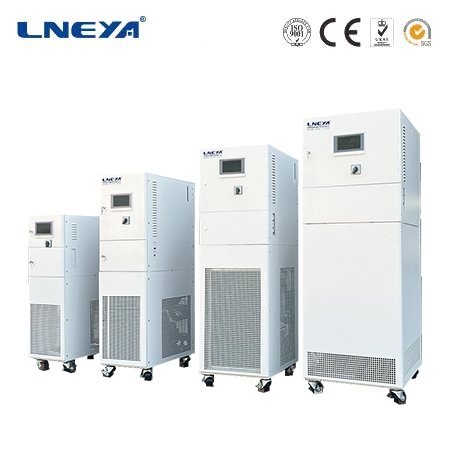
Working Principle
The fundamental working principle of electric heaters for liquid is based on the resistance of the heating element. When an electric current passes through a resistive element, such as a wire made of materials like nichrome, the resistance causes the element to heat up. This heat is then transferred to the surrounding liquid through conduction. The rate of heat transfer depends on factors such as the surface area of the heating element in contact with the liquid, the thermal conductivity of the liquid, and the temperature difference between the heating element and the liquid.
Types of Electric Heaters for Liquid
Immersion Heaters: Immersion heaters are one of the most common types. They consist of a heating element encased in a protective sheath, such as stainless steel or Incoloy. The heater is directly immersed in the liquid that needs to be heated. The heating element is connected to an electrical power source, and when energized, it generates heat, which warms the liquid around it. Immersion heaters are suitable for heating relatively small volumes of liquid in containers like tanks or drums. They are often used in laboratories, small-scale industrial processes, and even in some domestic applications for heating water in storage tanks. Their compact design and ease of installation make them a popular choice. However, they need to be properly sized for the volume of liquid to ensure efficient heating and to prevent overheating or damage to the heater.
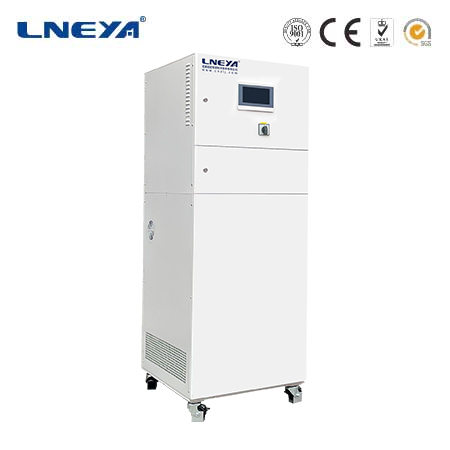
Circulation Heaters: Circulation heaters are designed for applications where a continuous flow of liquid needs to be heated. They typically have a housing with a heating element inside. The liquid is pumped through the housing, and as it passes over the heating element, it absorbs the heat. These heaters are commonly used in industrial processes such as chemical manufacturing, food processing, and oil and gas industries. In a chemical plant, for example, a circulation heater can be used to heat a chemical solution as it circulates through a pipeline system. They offer precise temperature control and can handle high flow rates and large volumes of liquid. But they require a proper pumping system to ensure the continuous flow of the liquid through the heater.
Cartridge Heaters: Cartridge heaters are cylindrical heating elements that can be inserted into drilled holes in a metal block or a liquid container. They are often used in applications where localized heating of a liquid is required. For instance, in injection molding machines, cartridge heaters can be used to heat the liquid plastic in specific areas to ensure proper molding. The heating element is enclosed in a metal sheath, and electrical leads are connected to supply power. Cartridge heaters can provide high heat output in a relatively small space, but their installation requires careful consideration of the hole size and the thermal contact between the heater and the surrounding material to ensure efficient heat transfer to the liquid.
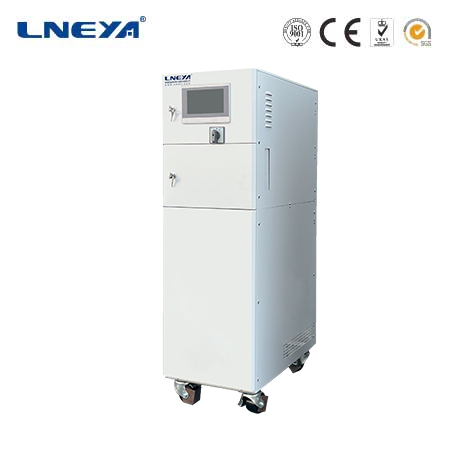
Considerations When Choosing Electric Heaters for Liquid
Power Requirements: Determining the appropriate power of the heater is crucial. It depends on factors such as the volume of the liquid, the desired temperature rise, and the time in which the heating needs to be accomplished. A larger volume of liquid or a greater temperature rise will require a higher power heater. Additionally, the thermal properties of the liquid, such as its specific heat capacity, also affect the power requirement.
Liquid Properties: Different liquids have different properties, such as viscosity, corrosiveness, and thermal conductivity. For corrosive liquids, heaters with suitable materials of construction, like stainless steel or other corrosion-resistant alloys, should be chosen to prevent damage to the heater. High viscosity liquids may require more power to heat and may also affect the heat transfer rate, so the design of the heater needs to take this into account.
Safety: Safety is a top priority when using electric heaters for liquid. Overheating can lead to dangerous situations, such as boiling over or even explosions in some cases. Heaters should be equipped with proper safety features, such as thermostats to control the temperature and overheat protection devices that will cut off the power in case of an abnormal temperature rise. Additionally, the electrical connections should be properly insulated and grounded to prevent electrical hazards.
Maintenance and Efficiency
Regular maintenance of electric heaters for liquid is essential to ensure their efficient operation and longevity. This includes checking the electrical connections for any signs of damage or loose connections, inspecting the heating elements for wear and tear, and cleaning the heaters to remove any deposits or scale that may form on the surface, which can reduce the heat transfer efficiency.
To improve the efficiency of electric heaters for liquid, proper insulation of the liquid containers or pipelines can be beneficial. This helps to minimize heat loss to the surroundings and ensures that more of the heat generated by the heater is transferred to the liquid. Additionally, using heaters with advanced control systems that can precisely regulate the power output based on the temperature requirements can also enhance energy efficiency.
In conclusion, electric heaters for liquid are versatile and important devices in various applications. Understanding their working principles, types, selection criteria, and maintenance requirements is essential for making the most of these heaters and ensuring safe and efficient heating of liquids. Whether in industrial processes or domestic applications, choosing the right electric heater for the specific liquid and application needs can lead to optimal performance and energy savings.
Related recommendations
How does the evaporator chiller reduce vibration and noise?
910How does the evaporator chiller reduce vibration and noise? Evaporator cooler is a device used to cool air or liquid, which can dissipate heat through evaporation. When using evaporator...
View detailshigh temp controller
402High Temp Controller: Regulating Extreme Temperatures in Industrial Processes Introduction High temp controllers are specialized temperature control devices engineered to operate and maintai...
View detailslab temperature controller
236Lab Temperature Controllers: A Complete GuideIn a laboratory setting, maintaining a precise and stable temperature is often critical for the success of experiments. Lab temperature controllers ar...
View detailslab water chiller
198Introduction to Lab Water ChillersLab water chillers are specialized cooling systems designed to maintain a stable and low temperature for water used in laboratory applications. They play a cruci...
View details
HelloPlease log in