cooling chillers
Cooling chillers are mechanical systems designed to extract heat from a substance, typically water or a refrigerant, and transfer it to another medium, thereby reducing the temperature of the initial substance. They are widely used in a multitude of settings, from large – scale industrial processes to maintaining comfortable temperatures in commercial buildings and ensuring precise conditions in scientific laboratories. Understanding the functionality, types, and applications of cooling chillers is key for professionals and enthusiasts alike who are involved in temperature – sensitive operations or interested in efficient cooling solutions.
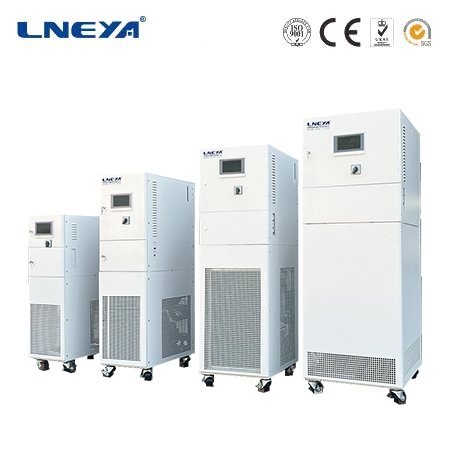
Working Principles
The Refrigeration Cycle
The foundation of a cooling chiller’s operation is the refrigeration cycle, which consists of four main components: the compressor, condenser, expansion valve, and evaporator.
Compressor: The compressor plays a pivotal role by increasing the pressure and temperature of the refrigerant gas. Through compression, it elevates the energy level of the gas, making it easier to release heat later in the cycle. The high – pressure, high – temperature refrigerant then proceeds to the condenser.
Condenser: In the condenser, the refrigerant gas releases its heat to a cooling medium. For air – cooled chillers, this medium is the ambient air, and fans are used to enhance heat dissipation. In water – cooled chillers, the heat is transferred to a water loop, often connected to a cooling tower. As the refrigerant loses heat, it condenses back into a liquid state.
Expansion Valve: The expansion valve reduces the pressure of the liquid refrigerant. When the liquid refrigerant passes through this valve, its pressure drops significantly, causing it to expand and cool down rapidly.
Evaporator: In the evaporator, the cold, low – pressure refrigerant absorbs heat from the substance that needs to be cooled, such as water in a water – cooling chiller. As the refrigerant absorbs heat, it vaporizes back into a gas, and the now – cooled substance is ready for circulation. The refrigerant gas then returns to the compressor, restarting the cycle.
Heat Transfer Process
Heat transfer is the core mechanism that enables cooling chillers to function. In the evaporator, heat naturally moves from the warmer substance (the load) to the colder refrigerant due to the temperature difference. The greater this temperature differential, the more efficient the heat transfer. In the condenser, the process is reversed, with heat being transferred from the hot refrigerant to the cooling medium, effectively removing heat from the system and allowing for continuous cooling.
Types of Cooling Chillers
Air – Cooled Chillers
Design and Operation: Air – cooled chillers utilize ambient air as the cooling medium for the condenser. They are equipped with fans that blow air over the condenser coils, facilitating the transfer of heat from the refrigerant to the air. These chillers are relatively straightforward in design and do not require a separate water – cooling infrastructure, making them a popular choice in areas where water is scarce or costly.
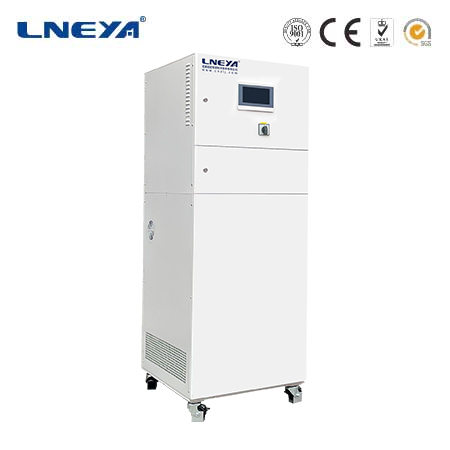
Advantages: Installation of air – cooled chillers is usually uncomplicated, often only needing a well – ventilated outdoor location. They are also more mobile and can be relocated with relative ease if necessary. Additionally, their initial investment costs are generally lower compared to water – cooled alternatives.
Disadvantages: However, air – cooled chillers are less energy – efficient, especially in hot and humid climates. High ambient temperatures can impede their heat – dissipating ability, leading to decreased performance and potentially higher energy consumption. They also tend to produce more noise due to the operation of the fans.
Water – Cooled Chillers
Design and Operation: Water – cooled chillers use water as the cooling medium in the condenser. The hot refrigerant transfers its heat to the water flowing through the condenser coils. This warm water is then directed to a cooling tower, where it releases heat to the atmosphere and is cooled down before being recirculated back to the chiller.
Advantages: These chillers are highly energy – efficient, particularly for large – scale applications. Water has a higher heat – carrying capacity than air, allowing for more effective heat transfer. They can maintain consistent performance even in high – temperature environments, making them suitable for industries with substantial cooling demands.
Disadvantages: Water – cooled chillers require a more complex installation, including the setup of a cooling tower and a water – treatment system to prevent scaling, corrosion, and microbial growth in the water loop. The initial investment, including the cost of the chiller, cooling tower, and associated plumbing, is significantly higher. Moreover, they consume a large amount of water, which can be a concern in water – scarce regions.
Absorption Chillers
Design and Operation: Absorption chillers operate on a different principle compared to compression – type chillers (air – cooled and water – cooled). They rely on the absorption of a refrigerant (usually ammonia) by an absorbent (commonly lithium bromide solution). Instead of using a compressor, heat is used as the driving force for the refrigeration process. The heat source can be steam, hot water, or waste heat from industrial processes.
Advantages: Absorption chillers are ideal for settings where there is a readily available waste – heat source, such as power plants or manufacturing facilities with excess heat. They operate quietly, produce less vibration, and can contribute to overall energy savings by utilizing otherwise wasted heat.
Disadvantages: They are generally larger and more complex in design, requiring more space for installation. Absorption chillers also have a lower coefficient of performance (COP) compared to compression – type chillers, meaning they consume more heat energy to produce the same amount of cooling. Additionally, the absorbent and refrigerant solutions require careful handling and maintenance to ensure optimal operation.
Scroll Chillers
Design and Operation: Scroll chillers use scroll compressors, which consist of two interleaving spiral – shaped scrolls, one fixed and one orbiting. As the orbiting scroll moves, it creates a series of chambers that change in size, compressing the refrigerant gas. These chillers are known for their smooth operation, low noise levels, and high reliability.
Advantages: Scroll chillers offer good energy efficiency, especially at part – load conditions, which are common in many applications. They have fewer moving parts compared to reciprocating compressors, reducing the likelihood of mechanical failures and maintenance requirements. Their compact size also makes them suitable for installations where space is limited.
Disadvantages: They are typically less suitable for very large – scale applications that require extremely high cooling capacities. Additionally, the initial cost of scroll chillers can be relatively high, although this may be offset by their long – term energy savings and reliability.
Applications of Cooling Chillers
Industrial Applications
Manufacturing Processes: In industries such as food and beverage, pharmaceutical, and chemical manufacturing, precise temperature control is essential. Cooling chillers are used to cool reactors during chemical synthesis to maintain the desired reaction rates and prevent overheating, which could lead to unwanted side reactions or even hazardous situations. In the food industry, they help preserve the quality of products by controlling the temperature during pasteurization, freezing, and storage processes. In pharmaceuticals, accurate temperature control during the synthesis of active ingredients ensures product quality and consistency.
Plastic and Metalworking Industries: In plastic manufacturing, cooling chillers are crucial for cooling injection molds. Rapid and uniform cooling of the molds helps in producing high – quality plastic parts with precise dimensions. In metalworking, such as machining and metal casting, chillers are used to cool cutting tools, workpieces, and lubricants to prevent overheating, which can lead to tool wear, reduced machining accuracy, and damage to the metal’s properties.
Commercial Applications
Data Centers: Data centers generate a massive amount of heat due to the continuous operation of servers and other electronic equipment. Cooling chillers are used to remove this heat, maintaining a stable and cool environment. This is crucial for the proper functioning and longevity of the data – center equipment, as overheating can lead to system failures and data loss.
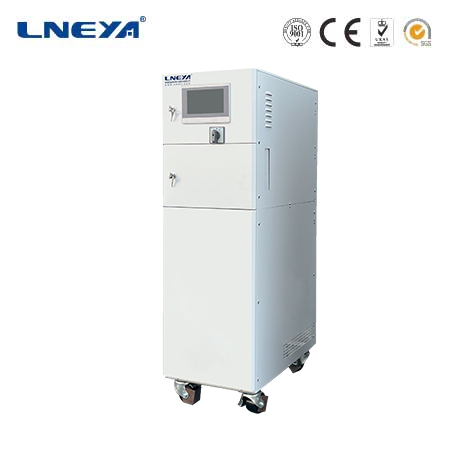
HVAC Systems in Buildings: In commercial buildings like offices, shopping malls, and hotels, cooling chillers are integral to the heating, ventilation, and air – conditioning (HVAC) systems. They provide chilled water to air – handling units, which cool the air and distribute it throughout the building, ensuring a comfortable indoor environment for occupants.
Scientific and Research Applications
Laboratory Equipment: In research laboratories, many scientific instruments, such as centrifuges, spectrometers, and electron microscopes, require precise temperature control. Cooling chillers are used to cool these devices, ensuring accurate and reliable experimental results. They also help protect the sensitive components of the equipment from damage due to overheating.
Medical Facilities: In hospitals and medical research centers, cooling chillers are used to maintain the temperature of refrigeration units storing vaccines, blood products, and other biological samples. They are also used in some medical imaging equipment and surgical devices that generate heat during operation.
Selection and Installation Considerations
Sizing
Selecting the appropriate size of a cooling chiller is crucial for optimal performance. An undersized chiller will struggle to meet the cooling demand, leading to increased operating times, higher energy consumption, and potential damage to the processes or equipment it serves. Conversely, an oversized chiller will cycle on and off frequently, reducing its efficiency and lifespan. Factors such as the cooling load of the application, ambient temperature, and the specific requirements of the equipment being cooled need to be carefully calculated. Professional engineers often use load – calculation methods and software to determine the accurate chiller size.
Location
The location of the cooling chiller can impact its performance and maintenance. For air – cooled chillers, they should be installed in an area with good ventilation to ensure efficient heat dissipation. Outdoor installation is common, but they need to be protected from direct sunlight, rain, and debris. Water – cooled chillers, along with their associated cooling towers, require sufficient space for installation and maintenance. The location should also provide easy access to water supply and drainage systems. Additionally, noise and vibration considerations may influence the location, especially in facilities where these factors could affect other operations or nearby environments.
Integration with Existing Systems
When installing a cooling chiller, seamless integration with existing systems is essential. This includes ensuring compatibility with the process fluid (such as water or coolant), the piping and plumbing systems, and the control systems of the facility. Proper integration ensures that the chiller can effectively cool the targeted equipment and processes while also allowing for easy monitoring and control of its operation.
Maintenance and Troubleshooting
Regular Maintenance
Component Inspection: Regularly inspecting the components of the cooling chiller, such as the compressor, condenser, evaporator, and expansion valve, is vital. Check for signs of wear, leaks, or damage. Monitor the refrigerant levels and the condition of the refrigerant lines to ensure proper operation.
Cleaning: Clean the condenser coils (for both air – cooled and water – cooled chillers) regularly to remove dirt, dust, and debris. In water – cooled chillers, also clean the cooling tower and the water – side of the condenser to prevent scaling and fouling, which can significantly reduce the chiller’s efficiency.
Water Treatment (for water – cooled chillers): Implement a proper water – treatment program to prevent corrosion, scaling, and the growth of algae and bacteria in the water loop. Regularly test the water quality and adjust the treatment chemicals as needed.
Lubrication: Lubricate the moving parts of the chiller, such as the compressor motor bearings and fan motors, according to the manufacturer’s recommendations. Proper lubrication ensures smooth operation and reduces wear and tear on the components.
Common Troubleshooting Issues
Low Refrigerant Charge: A low refrigerant charge can cause the chiller to operate inefficiently or fail to cool properly. Signs include warm suction lines, high – pressure differentials, and reduced cooling capacity. A leak in the refrigerant system is often the cause, and it needs to be located and repaired.
Compressor Problems: Compressor failures can occur due to various reasons, such as overheating, lack of lubrication, or electrical issues. Symptoms may include abnormal noises, high – current draw, or the compressor failing to start. Regular maintenance and monitoring can help prevent compressor problems.
Water – Flow Issues (in water – cooled chillers): Low water flow or water – pressure problems can be caused by clogged filters, faulty pumps, or valve malfunctions. Insufficient water flow can lead to overheating of the chiller and reduced cooling performance.
Scaling and Fouling: In water – cooled chillers, scaling and fouling on the water – side components can impede heat transfer. Regular water treatment and cleaning are essential to prevent these issues. If scaling or fouling occurs, chemical cleaning or mechanical descaling may be necessary.
Energy Efficiency and Environmental Considerations
Energy – Saving Features
Variable – Speed Drives: Many modern cooling chillers are equipped with variable – speed drives for the compressor and fans. These drives adjust the speed of the components based on the cooling load, reducing energy consumption during periods of low demand. For example, when the cooling load decreases, the compressor speed can be reduced, saving electricity.
Heat Recovery Systems: Some cooling chillers feature heat recovery systems that capture the waste heat from the condenser. This recovered heat can be used for other purposes within the facility, such as pre – heating water, space heating, or supporting other processes that require heat, thereby increasing the overall energy efficiency of the operation.
Advanced Control Systems: Intelligent control systems can optimize the operation of cooling chillers. These systems can monitor and adjust various parameters in real – time, such as temperature, pressure, and flow rates, to ensure the chiller operates at its most efficient point under different operating conditions.
Environmental Impact
Refrigerant Selection: The choice of refrigerant in a cooling chiller has significant environmental implications. Older refrigerants, such as chlorofluorocarbons (CFCs) and hydrochlorofluorocarbons (HCFCs), have been phased out due to their ozone – depleting properties. Modern chillers use more environmentally friendly refrigerants, such as hydrofluorocarbons (HFCs) or natural refrigerants like ammonia and carbon dioxide. However, some HFCs still have a high global warming potential, prompting the industry to explore even more sustainable refrigerant options, such as hydrofluoroolefins (HFOs) and blends, to reduce the environmental impact of cooling systems.
Energy Consumption: Cooling chillers consume a significant amount of energy. By improving their energy efficiency, not only can operating costs be reduced, but also the overall carbon footprint associated with their operation can be minimized. This is important in the context of global efforts to reduce greenhouse gas emissions.
Future Trends in Cooling Chillers
Smart and Connected Chillers
The future of cooling chillers lies in increased connectivity and intelligence. Chillers will be equipped with sensors and communication technologies that allow for remote monitoring, control, and predictive maintenance. Operators will be able to access real – time data on the chiller’s performance, energy consumption, and health status through mobile devices or cloud – based platforms. Predictive maintenance algorithms will analyze the data to identify potential issues before they occur, enabling proactive repairs and minimizing downtime.
Improved Energy Efficiency
Ongoing research and development efforts will focus on further enhancing the energy efficiency of cooling chillers. This may involve the development of new refrigeration cycles, more efficient heat – transfer materials, and advanced compressor technologies. Additionally, the integration of renewable energy sources, such as solar or geothermal energy, with cooling chiller systems will become more prevalent, reducing the reliance on traditional energy sources and lowering the carbon footprint of cooling operations.
Miniaturization and Compact Design
As facilities seek to optimize space utilization, there will be a growing demand for smaller, more compact cooling chillers. Manufacturers will continue to develop innovative designs that offer high cooling capacities in a reduced footprint, making them suitable for a wider range of applications, including those in confined spaces or modular setups.
Conclusion
Cooling chillers are indispensable components in a vast array of applications, from industrial processes to commercial buildings and scientific research. Understanding their working principles, types, applications, selection criteria, installation requirements, maintenance needs, and the latest trends in energy – efficiency and environmental sustainability is essential for professionals across various industries. By making informed decisions regarding cooling chiller selection, installation, and operation, organizations can ensure optimal temperature control, enhance productivity, reduce energy consumption, and contribute to a more sustainable future. As technology continues to evolve, cooling chillers will become even more advanced, intelligent, and environmentally friendly, meeting the ever – changing demands of modern society.
Related recommendations
thermal cycling equipment
78Introduction to Thermal Cycling EquipmentThermal cycling equipment is an essential tool across multiple industries for evaluating the performance, reliability, and durability of products under fl...
View detailsportable temperature control unit
333Introduction to Portable Temperature Control Units Portable temperature control units (PCUs) are self-contained systems designed for thermal control and data acquisition in temperature-sensitiv...
View detailsair cooled chiller design
70Core Components and Their Design ConsiderationsAn air cooled chiller’s performance hinges on the design of its key components, each tailored to facilitate heat transfer and refrigerant flow. ...
View detailsair cooled water chillers
155Air Cooled Water Chillers: A Comprehensive GuideAir cooled water chillers are essential cooling systems widely utilized across various industries and applications. These chillers operate by using...
View details
HelloPlease log in