air cooled water chillers
Air Cooled Water Chillers: A Comprehensive Guide
Air cooled water chillers are essential cooling systems widely utilized across various industries and applications. These chillers operate by using ambient air as the medium for heat rejection, eliminating the need for a separate water source for cooling, unlike their water – cooled counterparts. They play a pivotal role in maintaining optimal temperatures in buildings, industrial processes, and data centers by efficiently cooling water, which is then circulated to absorb heat from the spaces or equipment that require temperature control.
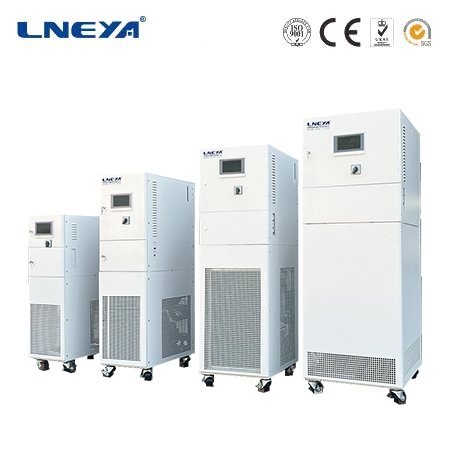
Working Principles of Air Cooled Water Chillers
The operation of air cooled water chillers is based on the refrigeration cycle, which involves several key stages and components working in harmony to achieve the desired cooling effect.
Refrigerant Compression
The cycle commences with the compressor, which is the heart of the chiller. The compressor draws in low – pressure, low – temperature refrigerant gas and compresses it, significantly increasing its pressure and temperature. This high – energy state of the refrigerant is crucial for the subsequent heat – rejection process. As the compressor forces the refrigerant through its mechanism, it converts mechanical energy into thermal energy, making the refrigerant suitable for heat transfer in the next stage of the cycle.
Condensation
After compression, the high – pressure, high – temperature refrigerant gas flows into the condenser. In air cooled water chillers, the condenser consists of a series of coils with a large surface area. Fans are strategically placed to blow ambient air over these condenser coils. As the warm refrigerant gas comes into contact with the cooler surface of the coils, heat is transferred from the refrigerant to the air. This heat transfer causes the refrigerant to condense from a gas into a high – pressure liquid. The efficiency of this condensation process depends on factors such as the airflow rate over the coils, the surface area of the coils, and the temperature difference between the refrigerant and the ambient air.
Expansion
The high – pressure liquid refrigerant then passes through an expansion valve or device. The expansion valve creates a significant pressure drop, reducing the pressure and temperature of the refrigerant suddenly. This drop in pressure causes the refrigerant to partially evaporate, turning into a mixture of liquid and vapor. The now low – pressure, low – temperature refrigerant mixture is ready to absorb heat in the evaporator.
Evaporation
In the evaporator, the low – pressure refrigerant mixture comes into contact with the water that needs to be cooled. The water, which is typically circulated from the areas requiring cooling (such as air – handling units in a building or industrial machinery), transfers its heat to the refrigerant. As the refrigerant absorbs heat from the water, it fully evaporates back into a gas. The cooled water is then pumped out of the evaporator and distributed to the relevant cooling loads, while the gaseous refrigerant is drawn back into the compressor to start the cycle anew.
Key Components of Air Cooled Water Chillers
Compressor
As mentioned, the compressor is a vital component responsible for initiating the refrigeration cycle. Compressors in air cooled water chillers can be of different types, each with its own characteristics and applications.
Reciprocating Compressors: These compressors use pistons that move back and forth within cylinders to compress the refrigerant. They are commonly used in smaller – scale chillers and are known for their relatively simple design and cost – effectiveness. However, they may have lower efficiency compared to some other types at higher capacities and can produce more noise and vibration.
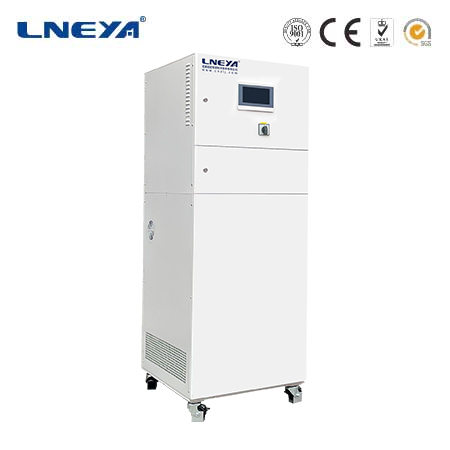
Screw Compressors: Screw compressors feature two intermeshing helical rotors that compress the refrigerant. They offer a good balance between efficiency and capacity, capable of handling a wide range of cooling loads. Screw compressors are more energy – efficient than reciprocating compressors at partial loads and are often used in medium – to large – sized air cooled water chillers.
Centrifugal Compressors: Centrifugal compressors utilize centrifugal force to increase the pressure of the refrigerant. They are designed for high – capacity applications and are highly efficient at full load. Centrifugal compressors are typically found in large commercial and industrial air cooled water chiller systems where a significant amount of cooling is required.
Condenser
The condenser in an air cooled water chiller is where the heat transfer from the refrigerant to the ambient air occurs. The condenser coils are usually made of materials with high thermal conductivity, such as copper, to facilitate efficient heat exchange. The design of the condenser, including the number of coil rows, fin spacing, and coil configuration, affects its performance. A well – designed condenser maximizes the surface area available for heat transfer while minimizing air resistance to ensure optimal airflow over the coils. Additionally, the fans used to blow air over the condenser coils are carefully selected based on factors like airflow volume, static pressure, and noise level to ensure effective heat dissipation.
Evaporator
The evaporator is responsible for cooling the water by absorbing heat from it using the refrigerant. Similar to condensers, evaporators can come in various designs, such as shell – and – tube evaporators, plate evaporators, and finned – tube evaporators.
Shell – and – Tube Evaporators: In a shell – and – tube evaporator, the water flows through the tubes, while the refrigerant surrounds the tubes within the shell. This design allows for a large heat – transfer surface area and is suitable for handling high – volume water flows, making it common in many industrial and commercial applications.
Plate Evaporators: Plate evaporators consist of a series of thin, corrugated metal plates stacked together. The water and refrigerant flow through alternate channels between the plates, enabling efficient heat transfer in a compact space. They are often used in applications where space is limited and high heat – transfer efficiency is required.
Finned – Tube Evaporators: Finned – tube evaporators have tubes with fins attached to increase the surface area for heat exchange. They are commonly used when cooling air in addition to water, such as in integrated HVAC – chiller systems, where the fins help transfer heat from the refrigerant to the air passing over them.
Expansion Valve
The expansion valve regulates the flow of the refrigerant into the evaporator and controls the pressure drop. There are different types of expansion valves, including thermal expansion valves and electronic expansion valves.
Thermal Expansion Valves: Thermal expansion valves use a temperature – sensitive bulb that senses the temperature of the refrigerant leaving the evaporator. Based on this temperature, the valve adjusts the flow of refrigerant to ensure that the refrigerant fully evaporates in the evaporator and that the superheat (the temperature of the refrigerant gas above its boiling point) is maintained at an optimal level.
Electronic Expansion Valves: Electronic expansion valves offer more precise control over the refrigerant flow. They are controlled by electronic controllers that can receive input from various sensors, such as temperature and pressure sensors, and adjust the valve opening in real – time. This allows for better performance in variable – load applications and improved energy efficiency.
Types of Air Cooled Water Chillers
Reciprocating Air Cooled Water Chillers
Reciprocating air cooled water chillers are often chosen for smaller – scale applications where the cooling demand is relatively low. They are suitable for small commercial buildings like small offices, restaurants, and retail stores. These chillers are relatively inexpensive compared to larger, more complex models. However, they may have higher energy consumption at partial loads and require more frequent maintenance due to the mechanical nature of the reciprocating compressor, which has more moving parts that can wear over time.
Screw Air Cooled Water Chillers
Screw air cooled water chillers are widely used in medium – to large – sized commercial and industrial applications. They can handle a broader range of cooling loads, making them suitable for shopping malls, hospitals, and industrial plants. Their ability to operate efficiently at partial loads makes them a popular choice in applications where the cooling demand fluctuates throughout the day. Screw chillers also generally have a longer lifespan and require less maintenance compared to reciprocating chillers, contributing to their overall cost – effectiveness over the long term.
Centrifugal Air Cooled Water Chillers
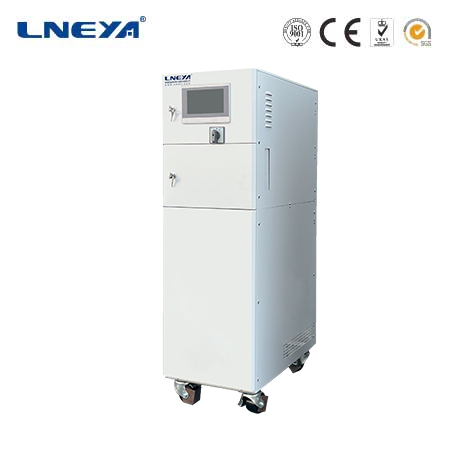
Centrifugal air cooled water chillers are designed for large – scale applications with high cooling requirements, such as large data centers, skyscrapers, and major industrial facilities. These chillers can deliver extremely high cooling capacities. They are highly efficient at full load, which is ideal for applications where a consistent and large amount of cooling is needed continuously. However, centrifugal chillers may experience a significant drop in efficiency at low – load conditions, and their initial cost is relatively high. They also require more sophisticated installation, operation, and maintenance due to their complex design and high – capacity nature.
Applications of Air Cooled Water Chillers
Commercial Buildings
In commercial buildings, air cooled water chillers are a key component of heating, ventilation, and air – conditioning (HVAC) systems. They cool the water that is circulated through air – handling units, which then distribute cooled air throughout the building to maintain a comfortable indoor environment. Whether it’s an office building, a hotel, or a shopping mall, air cooled water chillers ensure that occupants enjoy a pleasant temperature, regardless of the outdoor weather conditions. Additionally, they can be integrated with other building systems, such as heating systems and energy – management systems, to optimize energy usage and enhance overall building performance.
Industrial Processes
Many industrial processes generate a significant amount of heat that needs to be removed to ensure the proper operation of equipment and the quality of products. Air cooled water chillers are used to cool machinery, such as injection molding machines in the plastics industry, where maintaining the correct temperature of the molds is crucial for producing high – quality plastic parts. In the food and beverage industry, they cool processing equipment, storage areas, and refrigeration units to preserve the freshness and safety of products. They also play a role in cooling electrical equipment, such as transformers and motors, in industrial plants to prevent overheating and extend their lifespan.
Data Centers
Data centers house a large number of servers and other IT equipment that generate substantial amounts of heat. Air cooled water chillers are used to cool the air – conditioning systems in data centers, ensuring that the servers operate within their optimal temperature range. By maintaining the right temperature, these chillers help prevent server failures, data loss, and costly downtime. With the increasing demand for data storage and processing, the role of air cooled water chillers in data centers continues to grow in importance, and there is a growing focus on developing more energy – efficient chiller solutions to meet the high – energy demands of these facilities.
Selection Criteria for Air Cooled Water Chillers
Cooling Capacity
Determining the appropriate cooling capacity is the most critical factor when selecting an air cooled water chiller. It is essential to accurately calculate the total heat load of the space or processes that need to be cooled. This involves considering factors such as the size of the building, the number of occupants, the type and quantity of heat – generating equipment (such as computers, lights, and machinery), and the ambient temperature. An undersized chiller will not be able to provide sufficient cooling, leading to discomfort in buildings or equipment overheating in industrial applications. On the other hand, an oversized chiller will result in higher initial costs, increased energy consumption, and wasted resources.
Energy Efficiency
Energy efficiency is a major consideration, as air cooled water chillers can consume a significant amount of electricity. Look for chillers with high – efficiency ratings, such as a high Coefficient of Performance (COP) or Energy Efficiency Ratio (EER). A higher COP or EER indicates that the chiller can produce more cooling output for each unit of electrical energy input, resulting in lower operating costs over time. Features like variable – speed drives for compressors and fans can adjust the chiller’s operation based on the actual cooling demand, further enhancing energy savings. Energy – efficient chillers also contribute to environmental sustainability by reducing greenhouse gas emissions associated with electricity generation.
Noise Level
In applications where noise can be a concern, such as in commercial buildings located in residential areas or in laboratories, the noise level of the air cooled water chiller is an important factor. Manufacturers typically provide noise level specifications for their chillers. Look for chillers that operate quietly, or consider implementing noise – reduction measures such as installing the chiller in a sound – insulated enclosure or choosing models with low – noise fans and compressors. Excessive noise can be a nuisance to occupants and may also violate local noise regulations.
Space Requirements
The available space for installing the air cooled water chiller is another key consideration. These chillers come in various sizes, and some larger models may require a significant amount of outdoor or rooftop space. It is important to measure the available installation area carefully and ensure that there is enough room for the chiller, as well as for proper air circulation around it. Additionally, consider the access requirements for maintenance and service. The chiller should be installed in a location that allows technicians easy access to components for inspection, cleaning, and repair.
Compatibility with Existing Systems
If the air cooled water chiller is being installed as part of an existing HVAC or industrial cooling system, compatibility is crucial. Ensure that the chiller’s cooling capacity, refrigerant type, and control system are compatible with the other components of the system. For example, if the existing system uses a specific type of refrigerant, the new chiller should also be compatible with that refrigerant to avoid the need for costly refrigerant changes or system modifications. Similarly, the control system of the chiller should be able to integrate seamlessly with the building’s overall energy – management or HVAC control system for efficient operation.
Installation, Maintenance, and Environmental Considerations
Installation
Proper installation of air cooled water chillers is essential for their optimal performance and longevity. The installation process should be carried out by trained professionals who are familiar with the specific requirements of the chiller and local building codes and regulations. Key installation considerations include ensuring proper placement of the chiller to allow for adequate air circulation. The chiller should be installed on a flat, stable surface, and there should be sufficient clearance around it to ensure that air can flow freely over the condenser coils.
Electrical connections should be made in accordance with electrical codes, and the chiller should be properly grounded to prevent electrical hazards. For larger chillers, the refrigerant lines need to be carefully sized, installed, and leak – tested to ensure that there are no refrigerant leaks, which can be harmful to the environment and reduce the chiller’s performance. Additionally, if the chiller is connected to a water – circulation system, the pipes should be installed correctly to ensure proper water flow and prevent issues such as water hammer or leaks.
Maintenance
Regular maintenance is crucial to keep air cooled water chillers operating efficiently and reliably. Maintenance tasks include cleaning the condenser coils regularly to remove dirt, dust, and debris that can accumulate over time and reduce the efficiency of heat transfer. The coils can be cleaned using compressed air, brushes, or specialized coil – cleaning chemicals. Additionally, check and clean the air filters (if present) to ensure proper airflow through the chiller.
Monitor the refrigerant levels and pressures regularly and recharge the refrigerant if necessary. Check the condition of the compressor, fans, and other moving parts, and lubricate them as per the manufacturer’s recommendations to reduce friction and prevent wear. Inspect the electrical components for any signs of damage or loose connections. A well – planned maintenance schedule, based on the manufacturer’s guidelines and the operating conditions of the chiller, can help prevent breakdowns, extend the chiller’s lifespan, and maintain its energy efficiency.
Environmental Considerations
Air cooled water chillers have several environmental implications that need to be addressed. The refrigerant used in chillers can have a significant impact on the environment. Some refrigerants, such as chlorofluorocarbons (CFCs) and hydrochlorofluorocarbons (HCFCs), have been phased out due to their ozone – depleting properties. Today, more environmentally friendly refrigerants, such as hydrofluorocarbons (HFCs) with low global warming potential (GWP) or natural refrigerants like ammonia and carbon dioxide, are being used. It is important to ensure that the chiller uses a refrigerant that complies with environmental regulations and has a minimal impact on the ozone layer and climate change.
In addition, the energy consumption of air cooled water chillers contributes to greenhouse gas emissions associated with electricity generation. By selecting energy – efficient chillers and implementing energy – management strategies, such as optimizing the chiller’s operation based on load demand and integrating it with renewable energy sources, the environmental impact can be minimized. Proper disposal of old or damaged chillers and their components is also important to prevent the release of harmful substances into the environment.
In conclusion, air cooled water chillers are versatile and essential cooling systems with a wide range of applications. Understanding their working principles, components, types, applications, selection criteria, and aspects related to installation, maintenance, and the environment is crucial for making informed decisions when choosing and operating these chillers. By carefully considering these factors, users can ensure the efficient, reliable, and sustainable operation of air cooled water chillers, meeting their cooling needs while minimizing costs and environmental impact.
Related recommendations
chilled water cooling water
308Chilled Water Cooling Systems: An Overview Chilled water systems are a cornerstone of modern cooling technology, offering efficient and reliable solutions for temperature control across diverse...
View detailsindustrial process cooling
335Industrial Process Cooling: A Comprehensive GuideI. IntroductionIndustrial process cooling refers to the set of techniques and systems employed to remove heat generated during various industrial m...
View detailswater cooled chiller installation
393Water-Cooled Chiller Installation: A Comprehensive Guide The installation of a water-cooled chiller is a complex process that requires careful planning and execution to ensure the system operat...
View details20 ton chiller
206A 20 - ton chiller is a powerful cooling system used in various applications to remove heat from a space or process. The “20 - ton” rating is a measure of its cooling capacity. Specifically, it me...
View details
HelloPlease log in