closed loop chillers
Introduction
Closed loop chillers play a pivotal role in modern cooling applications. Unlike open loop systems, closed loop chillers operate with a coolant that circulates within a completely sealed circuit. This design feature offers several advantages, making them a preferred choice in various industries. By maintaining a closed system, the coolant is protected from external contaminants, and the overall efficiency and reliability of the chiller are enhanced.
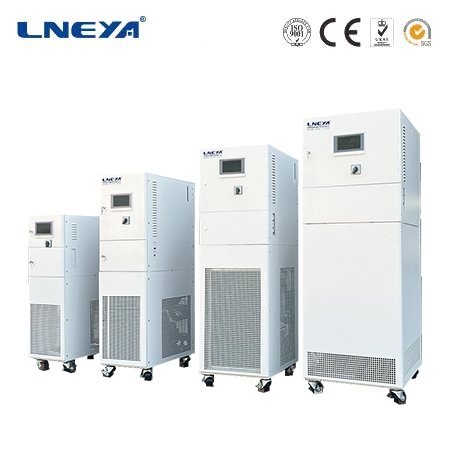
Working Principles of Closed Loop Chillers
Vapor – Compression Cycle
Compression Stage: In a vapor – compression closed loop chiller, the process starts with a low – pressure, low – temperature refrigerant vapor. A compressor is the heart of this cycle. It sucks in the refrigerant vapor and compresses it to a high – pressure, high – temperature state. As the refrigerant is compressed, work is done on it, increasing its internal energy. The compressor is sized according to the cooling capacity requirements of the chiller. For example, in a large – scale industrial closed loop chiller, a powerful compressor is needed to handle the high volume of refrigerant required to achieve the desired cooling effect.
Condensation Stage: The high – pressure, high – temperature refrigerant vapor then enters the condenser. In the condenser, the refrigerant releases heat to a cooling medium. In air – cooled closed loop chillers, ambient air is used as the cooling medium, and fans blow air over the condenser coils to dissipate the heat. In water – cooled closed loop chillers, water is the cooling medium. The heat is transferred to the water, which is then cooled in a cooling tower or a water – cooled heat exchanger. During this process, the refrigerant condenses back into a high – pressure liquid state.
Expansion Stage: The high – pressure liquid refrigerant passes through an expansion device, such as a thermostatic expansion valve or a capillary tube. The expansion device reduces the pressure of the refrigerant, causing it to expand rapidly. This sudden expansion leads to a drop in the refrigerant’s temperature, and it enters the evaporator as a low – pressure, low – temperature liquid – vapor mixture.
Evaporation Stage: In the evaporator, the low – pressure refrigerant absorbs heat from the process fluid or the air that needs to be cooled. As it absorbs heat, the refrigerant evaporates and turns back into a low – pressure vapor. The cooled process fluid or air can then be used for cooling purposes. In a closed loop system, the process fluid is typically a coolant mixture, such as a glycol – water solution, which circulates within the closed loop, transferring heat to the refrigerant in the evaporator.
Absorption Cycle
Absorption Process: In an absorption closed loop chiller, a refrigerant (usually water in water – lithium bromide systems or ammonia in ammonia – water systems) is absorbed by an absorbent solution in the absorber. This absorption process releases heat, which is removed by a cooling medium, typically water. The absorbent solution becomes rich in refrigerant as it absorbs the vapor.
Generation Process: The rich absorbent – refrigerant solution is then pumped to the generator. Heat is applied to the generator, which can come from a waste heat source, solar energy, or natural gas. The heat causes the refrigerant to vaporize from the absorbent solution. The high – pressure refrigerant vapor then moves to the condenser.
Condensation and Expansion: Similar to the vapor – compression cycle, in the condenser, the high – pressure refrigerant vapor releases heat and condenses into a liquid state. The high – pressure liquid refrigerant then passes through an expansion valve, reducing its pressure and temperature.
Evaporation: The low – pressure, low – temperature refrigerant enters the evaporator, where it absorbs heat from the process fluid within the closed loop. As the refrigerant evaporates, the process fluid is cooled. The weak absorbent – refrigerant solution from the generator returns to the absorber to complete the cycle. Absorption closed loop chillers are less common than vapor – compression ones but can be a cost – effective and energy – efficient option in facilities with access to suitable heat sources.
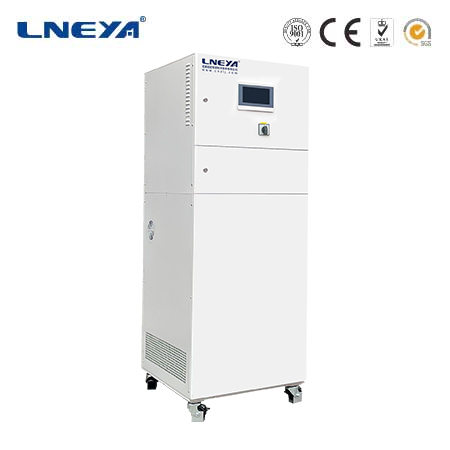
Components of Closed Loop Chillers
Compressor
Types of Compressors: There are different types of compressors used in closed loop chillers. Reciprocating compressors use a piston – cylinder arrangement to compress the refrigerant. They are suitable for small – to – medium – sized chillers and offer good efficiency at specific load conditions. Screw compressors, on the other hand, use two intermeshing helical screws to compress the refrigerant. They are more commonly used in medium – to – large – scale closed loop chillers due to their higher capacity and better part – load performance. Centrifugal compressors use a high – speed impeller to compress the refrigerant and are typically used in large – scale industrial and commercial applications where high cooling capacities are required.
Function in the System: The compressor’s main function is to increase the pressure of the refrigerant, which is essential for the heat – transfer process in the chiller. By compressing the refrigerant, the compressor raises its temperature, allowing it to release heat in the condenser. The efficiency of the compressor directly affects the overall energy consumption of the closed loop chiller. A well – maintained and properly sized compressor ensures smooth operation and optimal cooling performance.
Condenser
Air – Cooled Condensers: Air – cooled condensers in closed loop chillers use ambient air to cool the refrigerant. They consist of finned coils through which the hot refrigerant vapor flows. Fans are used to blow air over the coils, facilitating heat transfer from the refrigerant to the air. Air – cooled condensers are relatively simple in design and are suitable for applications where water availability is limited. However, they are generally less energy – efficient than water – cooled condensers, especially in hot ambient conditions.
Water – Cooled Condensers: Water – cooled condensers use water as the cooling medium. The hot refrigerant vapor flows through tubes in the condenser, and water flows around these tubes. The heat from the refrigerant is transferred to the water. Water – cooled condensers are more energy – efficient as water has a higher heat – carrying capacity than air. They are commonly used in large – scale commercial and industrial closed loop chiller systems. However, they require a water – cooling infrastructure, including a cooling tower or a water – cooled heat exchanger, and proper water treatment to prevent scale formation and corrosion.
Expansion Device
Thermostatic Expansion Valves: Thermostatic expansion valves (TXVs) are commonly used in closed loop chillers. They regulate the flow of the high – pressure liquid refrigerant into the evaporator. The TXV senses the temperature of the refrigerant at the outlet of the evaporator and adjusts the refrigerant flow rate accordingly. This helps to maintain a proper refrigerant charge in the evaporator and ensures efficient heat transfer. If the temperature at the evaporator outlet is too high, the TXV opens wider to allow more refrigerant to flow, and if it is too low, the TXV closes slightly to reduce the refrigerant flow.
Capillary Tubes: Capillary tubes are another type of expansion device. They are simple, inexpensive, and consist of a long, narrow tube. The high – pressure liquid refrigerant passes through the capillary tube, and the pressure drop across the tube causes the refrigerant to expand. Capillary tubes are often used in smaller closed loop chillers or in applications where a fixed – flow expansion device is sufficient. However, they do not provide the same level of control as TXVs and may not be as effective in maintaining optimal performance under varying load conditions.
Evaporator
Shell – and – Tube Evaporators: Shell – and – tube evaporators are commonly used in closed loop chillers. In a shell – and – tube evaporator, the refrigerant is typically in the tubes, and the process fluid (such as a glycol – water mixture) flows around the tubes in the shell. Heat is transferred from the process fluid to the refrigerant, causing the refrigerant to evaporate. Shell – and – tube evaporators offer high heat – transfer efficiency and are suitable for applications where large amounts of heat need to be removed from the process fluid.
Plate – Type Evaporators: Plate – type evaporators consist of a series of thin, corrugated metal plates. The refrigerant and the process fluid flow between alternate plates, and heat is transferred across the plates. Plate – type evaporators are more compact than shell – and – tube evaporators and can offer high heat – transfer coefficients. They are often used in applications where space is limited, such as in some commercial and industrial installations.
Applications of Closed Loop Chillers
Data Centers
Cooling of Servers: Data centers are filled with servers that generate a significant amount of heat during operation. Closed loop chillers are used to cool the air around the servers, preventing them from overheating. The chilled water or coolant from the closed loop chiller is circulated through air – handling units (AHUs) or computer room air – conditioners (CRACs). These units blow the cooled air over the servers, maintaining a stable temperature within the data center. Precise temperature control is crucial in data centers as even a slight increase in temperature can affect the performance and lifespan of the servers.
Ensuring Reliability: Closed loop chillers offer a high level of reliability in data center cooling. Since the coolant is in a closed system, there is a reduced risk of contamination, which could otherwise affect the performance of the cooling system. In addition, closed loop chillers can be equipped with backup power systems and redundant components to ensure continuous operation, minimizing the risk of server downtime due to cooling system failures.
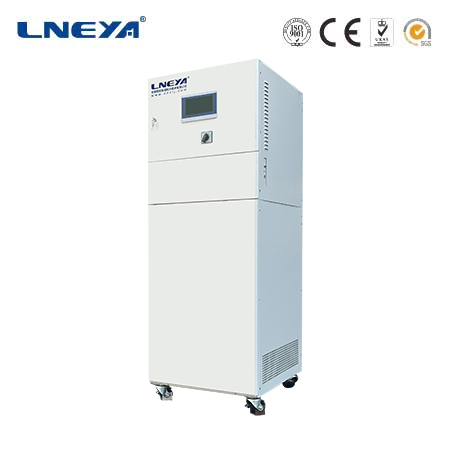
Medical Facilities
Operating Room Cooling: In operating rooms, maintaining a precise temperature and humidity level is essential for the well – being of patients and the success of surgical procedures. Closed loop chillers are used to cool the air in the operating room. The chilled water or coolant is used to cool the air – handling units that supply conditioned air to the operating room. The closed loop design helps to prevent the entry of contaminants into the cooling system, which could potentially affect the sterile environment of the operating room.
Medical Equipment Cooling: Many medical devices, such as MRI machines, CT scanners, and laser equipment, generate heat during operation and require cooling. Closed loop chillers provide a reliable cooling solution for these devices. The coolant in the closed loop system absorbs the heat from the medical equipment, ensuring their proper functioning and longevity.
Industrial Manufacturing
Plastic Injection Molding: In plastic injection molding, molds need to be cooled rapidly and precisely to ensure the proper shaping of plastic products. Closed loop chillers are used to cool the molds. The coolant in the closed loop system circulates through channels in the molds, removing heat and allowing the plastic to solidify evenly. The ability to control the cooling rate is crucial in plastic injection molding as it affects the quality and dimensional accuracy of the finished products.
Metalworking Processes: In metalworking processes such as machining, grinding, and welding, heat is generated, which can affect the quality of the finished product and the lifespan of the tools. Closed loop chillers are used to cool the cutting fluids or the workpieces themselves. The cooled coolant helps to reduce the temperature of the cutting tools, preventing overheating and extending their service life. It also improves the surface finish of the machined parts.
Advantages of Closed Loop Chillers
Reduced Risk of Contamination
Isolated Coolant System: In a closed loop chiller, the coolant is isolated from the external environment. This means that there is little to no risk of contaminants such as dirt, dust, or biological matter entering the coolant system. In contrast, open loop systems, which are exposed to the environment, are more prone to contamination. For example, in an industrial setting, open loop chillers may be exposed to airborne particles from the manufacturing process, which can clog filters, reduce heat – transfer efficiency, and cause corrosion in the cooling system. Closed loop chillers eliminate these risks, ensuring the purity of the coolant and the optimal performance of the chiller.
Protection of System Components: By preventing contamination, closed loop chillers help to protect the system components. Contaminants can cause wear and tear on components such as pumps, valves, and heat exchangers. In a closed loop system, the components are less likely to be damaged by contaminants, which extends their lifespan and reduces the need for frequent maintenance and replacement. This not only saves costs but also improves the overall reliability of the cooling system.
Better Temperature Control
Stable Coolant Temperature: Closed loop chillers can maintain a more stable coolant temperature compared to open loop systems. Since the coolant is not affected by external environmental factors such as changes in ambient temperature or humidity, the temperature of the coolant can be precisely controlled. In applications where precise temperature control is crucial, such as in data centers and medical facilities, this is a significant advantage. For example, in a data center, a stable coolant temperature ensures that the servers are cooled evenly, preventing hotspots and maintaining optimal performance.
Responsive to Load Changes: Closed loop chillers are also more responsive to changes in the cooling load. The control systems in closed loop chillers can quickly adjust the operation of components such as the compressor and the expansion valve to meet the changing cooling requirements. This allows the chiller to maintain a consistent temperature even when the heat load from the process or space being cooled varies. In an industrial manufacturing process where the heat load may change during different production stages, a closed loop chiller can adapt to these changes and provide efficient cooling.
Energy – Efficiency
Optimized Heat – Transfer: Closed loop chillers are designed to optimize heat – transfer processes. The closed system allows for better control of the coolant flow and temperature, which leads to more efficient heat transfer. In a well – designed closed loop chiller, the refrigerant and the coolant are carefully matched to ensure maximum heat transfer with minimal energy consumption. For example, in a water – cooled closed loop chiller, the water – cooling system can be optimized to operate at the most efficient temperature and flow rate, reducing the energy required to cool the refrigerant.
Variable – Speed Technologies: Many closed loop chillers are equipped with variable – speed technologies, such as variable – speed drives for the compressor and pumps. These technologies allow the chiller to adjust its operation according to the actual cooling load. When the cooling load is low, the compressor and pumps can operate at a lower speed, consuming less energy. This results in significant energy savings over the long term, especially in applications where the cooling load varies throughout the day.
Comparison with Open Loop Chillers
Water Consumption
Lower Water Consumption in Closed Loop: Open loop chillers typically require a continuous supply of fresh water to cool the refrigerant. This water is then discharged after use, resulting in high water consumption. In contrast, closed loop chillers use a closed – circuit coolant system, and the only water consumption is in the cooling of the condenser in water – cooled models. Even in water – cooled closed loop chillers, the water is recirculated and cooled in a cooling tower or a water – cooled heat exchanger, resulting in much lower water consumption compared to open loop systems. This makes closed loop chillers a more sustainable choice, especially in areas where water resources are scarce.
Water Conservation Benefits: The reduced water consumption of closed loop chillers has environmental and economic benefits. It helps to conserve water resources and reduces the cost of water intake and wastewater treatment. In addition, closed loop chillers can be used in applications where water conservation is a priority, such as in industries that are subject to strict water – use regulations.
System Complexity and Maintenance
Higher Complexity in Closed Loop: Closed loop chillers generally have a higher level of system complexity compared to open loop chillers. They require a closed – circuit coolant system, which includes components such as expansion tanks, pressure – relief valves, and coolant – monitoring devices. The closed system also needs to be carefully maintained to ensure proper operation. However, the higher complexity is offset by the advantages of reduced contamination and better temperature control.
Maintenance Requirements: The maintenance requirements for closed loop chillers are different from those of open loop chillers. In closed loop chillers, the focus is on maintaining the integrity of the closed – circuit coolant system. This includes checking the coolant level, concentration, and quality, as well as inspecting components such as the compressor, condenser, and evaporator for signs of wear and damage. In open loop chillers, in addition to component maintenance, there is a need to manage water treatment to prevent scale formation and corrosion in the water – cooling system.
Maintenance of Closed Loop Chillers
Coolant – Related Maintenance
Coolant Level and Concentration Checks: Regularly checking the coolant level in the closed loop system is essential. A low coolant level can reduce the cooling capacity of the chiller and may lead to overheating. The concentration of the coolant, especially in glycol – water mixtures, should also be monitored. The proper concentration is crucial for maintaining the antifreeze and heat – transfer properties of the coolant. A refractometer can be used to measure the concentration of glycol in the coolant. If the concentration deviates from the recommended range, additional coolant or water can be added to adjust it.
Coolant Quality Assessment: Inspecting the quality of the coolant is also important. The coolant should be clear and free of any visible particles, discoloration, or signs of biological growth. If the coolant appears contaminated, it may need to be filtered or replaced. Chemical analysis of the coolant can also be performed to check for the presence of contaminants, changes in pH, and the effectiveness of corrosion inhibitors. In a closed loop system, the coolant should be regularly tested to ensure its integrity and performance.
Related recommendations
3 ton water chiller
2303 Ton Water Chiller: A Detailed IntroductionA 3 - ton water chiller is a device designed to remove heat from water, providing a continuous supply of chilled water for various applications. The "3 ...
View detailsWhat environmental factors should be considered when using a 5 ton water chiller?
871What environmental factors should be considered when using a 5 ton water chiller? 1. If the environment in which a company uses a chiller is poor and the chiller needs to run for a rela...
View detailsmetal chiller
69IntroductionIn the realm of metalworking and industries related to metal processing, maintaining optimal temperatures is crucial for ensuring product quality, equipment longevity, and overall ope...
View detailsconstant temp water bath
83Constant Temperature Water Bath: Principles, Mechanisms, and ApplicationsIn the realm of scientific research, industrial processes, and various experimental setups, maintaining a stable temperatu...
View details
HelloPlease log in