thermonics temperature forcing system
Thermonics Temperature Forcing System: A Comprehensive Overview
In numerous scientific, industrial, and technological endeavors, the ability to precisely control and manipulate temperatures is essential. Thermonics temperature forcing systems have emerged as powerful tools to meet these temperature – control requirements. These systems are engineered to create and maintain specific temperature conditions, whether it’s for testing the performance of electronic components under extreme temperatures or simulating environmental conditions in scientific research.
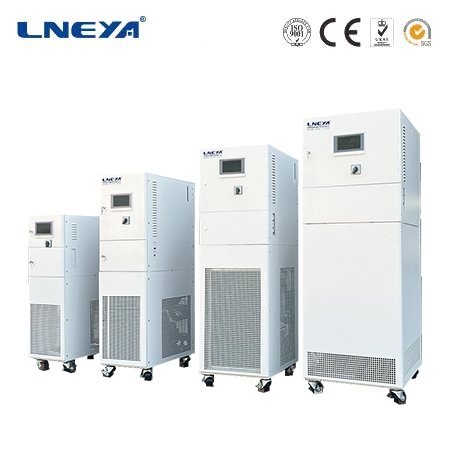
Working Principles
The fundamental operation of a thermonics temperature forcing system is based on the principles of heat transfer and thermal regulation. Heat transfer occurs through three main mechanisms: conduction, convection, and radiation. In a temperature forcing system, these mechanisms are harnessed and controlled to achieve the desired temperature changes.
Conduction involves the transfer of heat through direct contact between materials. For example, heating elements in the system can transfer heat to a test object or the surrounding environment via conduction. High – conductivity materials are often used to ensure efficient heat transfer. In some systems, a metal block may be heated by a heating element, and the test component is placed in contact with the block to receive the heat.
Convection is the transfer of heat through the movement of fluids (liquids or gases). Fans or pumps are used to circulate air or a coolant fluid within the system. As the fluid passes over the object being heated or cooled, it carries away or supplies heat. For instance, in a forced – air cooling setup, fans blow air over a heated component, and the air absorbs the heat, carrying it away to be dissipated elsewhere in the system.
Radiation is the transfer of heat through electromagnetic waves. While it may not be the primary mode of heat transfer in many thermonics temperature forcing systems, it still plays a role, especially in systems where objects are not in direct contact or when there is a need to account for heat loss or gain through radiation.
Thermal regulation in the system is achieved through a feedback loop mechanism. Temperature sensors continuously monitor the temperature within the system or of the object being tested. The sensor data is then sent to a controller, which compares the measured temperature with the setpoint (the desired temperature). Based on the difference, or error, between the actual and setpoint temperatures, the controller determines the appropriate action. If the temperature is below the setpoint, the controller may activate heating elements or reduce the cooling rate. Conversely, if the temperature is above the setpoint, it may increase the cooling capacity or turn off the heating elements. This continuous monitoring and adjustment ensure that the temperature remains as close as possible to the desired level.
Key Components
Heating Elements
Heating elements are crucial components in thermonics temperature forcing systems. One common type is the electrical resistance heating element. These elements work by passing an electric current through a resistive material, such as nichrome wire. As the current flows, the resistance of the material converts electrical energy into heat. The amount of heat generated can be controlled by adjusting the electrical current. For high – temperature applications, ceramic heating elements may be used. They can withstand higher temperatures and offer better durability compared to some other materials. In some systems, cartridge heaters, which are cylindrical heating elements inserted into holes in a metal block, are used to provide localized and efficient heating.
Cooling Devices
Cooling devices are essential for reducing the temperature within the system. Compressor – based refrigeration units are often employed for significant cooling requirements. These units work on the vapor – compression refrigeration cycle, similar to those in air conditioners and refrigerators. They compress a refrigerant gas, which then releases heat as it condenses. The cooled refrigerant is then expanded, absorbing heat from the environment or the object to be cooled.
For less demanding cooling applications or in combination with other cooling methods, thermoelectric coolers (TECs) can be used. TECs operate on the Peltier effect, where an electric current passing through a semiconductor module causes one side to heat up and the other side to cool down. They offer precise temperature control, compact size, and no moving parts, making them suitable for applications where space is limited or where rapid and accurate temperature changes are needed.
Sensors
Temperature sensors are the eyes of the thermonics temperature forcing system, providing real – time temperature data. Thermocouples are widely used due to their ability to measure a wide range of temperatures. They consist of two different metals joined together, and when there is a temperature difference between the junction and the reference point, a small voltage is generated, which is proportional to the temperature. Resistance Temperature Detectors (RTDs) are another common type. They rely on the change in electrical resistance of a material, usually platinum, with temperature. RTDs offer high accuracy and stability, making them ideal for applications where precise temperature measurement is crucial.
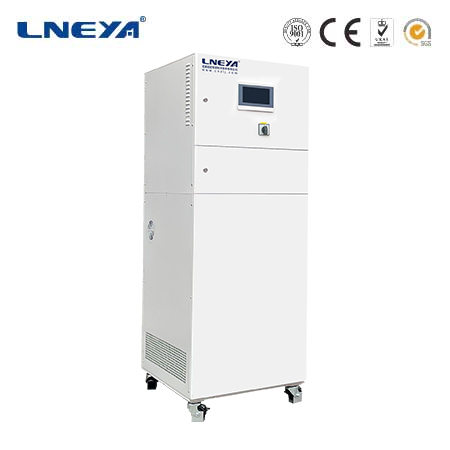
In addition to temperature sensors, other types of sensors may be included in the system. Humidity sensors can be used in applications where both temperature and humidity control are required, such as in environmental testing chambers. Pressure sensors may also be incorporated in systems that involve fluid circulation for cooling or heating, to monitor the pressure of the coolant or air, ensuring proper system operation.
Controllers
Controllers are the “brains” of the thermonics temperature forcing system. They analyze the data from the sensors and determine the appropriate control actions. Proportional – Integral – Derivative (PID) controllers are commonly used. The proportional component of the PID controller reacts to the current error between the measured temperature and the setpoint, adjusting the control output in proportion to the size of the error. The integral component accumulates past errors over time and helps eliminate steady – state errors, ensuring that the temperature eventually reaches and stays at the setpoint. The derivative component predicts future errors based on the rate of change of the error, allowing the controller to make preemptive adjustments and improve stability.
More advanced controllers, such as fuzzy logic controllers or model predictive controllers, are also being used in some systems. Fuzzy logic controllers can handle complex, nonlinear processes and uncertainties more effectively by using linguistic variables and rules. Model predictive controllers use a mathematical model of the system to predict future behavior and calculate the optimal control actions over a prediction horizon, taking into account constraints and multiple process variables.
Applications
Electronics Testing
In the electronics industry, thermonics temperature forcing systems are widely used for testing the performance and reliability of electronic components. Components such as integrated circuits (ICs), printed circuit boards (PCBs), and semiconductors need to be tested under various temperature conditions to ensure they can function properly in real – world scenarios. These systems can subject the components to extreme temperatures, from sub – zero cold to high heat, to simulate different environmental conditions. For example, during the development of a new microprocessor, it may be tested in a temperature forcing system to see how its performance, power consumption, and stability are affected by temperature variations. This helps manufacturers identify potential design flaws or weaknesses and make improvements before mass production.
Scientific Research
In scientific research, especially in fields like materials science, biology, and physics, temperature forcing systems are essential tools. In materials science, researchers use these systems to study how materials behave under different temperatures. For instance, they can investigate the phase transitions of materials, such as the change from solid to liquid or the transformation of crystal structures. By precisely controlling the temperature, scientists can observe and analyze these changes in detail.
In biology, temperature forcing systems can be used to study the effects of temperature on living organisms, cells, and biological processes. For example, in cryobiology research, cells or tissues may be cooled to very low temperatures using a temperature forcing system to study their viability and preservation. In ecological studies, these systems can be used to simulate climate change scenarios and observe how different organisms respond to temperature changes.
Aerospace and Defense
The aerospace and defense industries rely on thermonics temperature forcing systems for various purposes. In the development and testing of aircraft components, such as engines, avionics systems, and structural materials, these systems are used to simulate the extreme temperature conditions that the components will encounter during flight, from the cold temperatures at high altitudes to the heat generated by the engines. This ensures that the components are reliable and can withstand the harsh operating environments.
In the defense sector, temperature forcing systems are used for testing military equipment, including weapons systems, communication devices, and vehicles. They help ensure that the equipment functions properly in different climates, from the deserts to the arctic regions. This is crucial for the effectiveness and reliability of military operations.
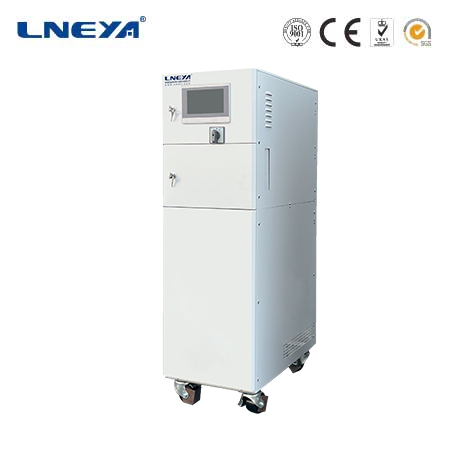
Automotive Industry
In the automotive industry, thermonics temperature forcing systems are used in the development and testing of vehicles. They are used to test engine components, such as cylinders, pistons, and cooling systems, under different temperature conditions to optimize engine performance, efficiency, and durability. Additionally, these systems are used to test the performance of automotive electronics, such as the battery management system, in – car entertainment systems, and electronic control units (ECUs). By subjecting these components to a range of temperatures, manufacturers can ensure that they function properly in various driving conditions, from hot summer days to cold winter nights.
Advantages
Precise Temperature Control
One of the primary advantages of thermonics temperature forcing systems is their ability to provide highly precise temperature control. They can maintain the temperature within a very narrow range, often within ±0.1°C or even better, depending on the system’s specifications. This precision is crucial in applications such as electronics testing, where even slight temperature variations can affect the performance and reliability of components. In scientific research, precise temperature control allows for accurate and reproducible experiments, enabling researchers to draw valid conclusions from their data.
Customizable Temperature Profiles
These systems offer the flexibility to create and implement customizable temperature profiles. Users can program the system to follow a specific temperature – time curve, such as a gradual increase in temperature, a rapid cooling phase followed by a hold at a certain temperature, or repeated cycles of heating and cooling. This feature is valuable in many applications, such as simulating the thermal cycling that electronic components may experience during their lifetime or replicating the temperature changes in different geographical regions for environmental testing.
Versatility
Thermonics temperature forcing systems can be used in a wide variety of applications across different industries. They can be adapted to handle different sizes and types of objects, from small electronic components to large industrial equipment. Additionally, they can operate over a broad temperature range, from extremely low cryogenic temperatures to high – temperature conditions, making them suitable for diverse testing and research requirements.
Reliability
Modern thermonics temperature forcing systems are designed with high – quality components and advanced control algorithms, ensuring reliable operation. They are built to withstand continuous use and can maintain stable performance over long periods. The use of redundant components in some systems further enhances their reliability, reducing the risk of system failures during critical testing or experimental processes.
Limitations
High Initial Cost
The purchase and installation of a thermonics temperature forcing system can be quite expensive. The cost includes the price of the heating and cooling components, sensors, controllers, and the enclosure or chamber where the temperature control takes place. Additionally, for complex systems, professional installation services may be required, adding to the overall cost. This high initial investment can be a barrier for some small – scale businesses or research laboratories with limited budgets.
Complexity
These systems are relatively complex, both in terms of their operation and maintenance. Operating a thermonics temperature forcing system requires a certain level of technical knowledge, especially when it comes to programming the temperature profiles and interpreting the data from the sensors. Maintenance tasks, such as calibrating the sensors, servicing the heating and cooling components, and updating the control software, also require specialized skills and tools. Any malfunction or incorrect operation of the system can lead to inaccurate temperature control, affecting the results of tests or experiments.
Energy Consumption
Thermonics temperature forcing systems can consume a significant amount of energy, especially when operating at extreme temperatures or for extended periods. Heating elements and refrigeration units require a substantial amount of electrical power to function. High energy consumption not only increases the operating costs but also has environmental implications. In some cases, additional measures may be needed to manage the energy consumption, such as using energy – efficient components or implementing power – management strategies.
Future Trends
Integration with Digital Technologies
As the trend towards digitalization continues, thermonics temperature forcing systems are likely to be integrated more closely with digital technologies. The integration of the Internet of Things (IoT) will enable real – time monitoring and remote control of the systems. This allows operators to access system data, adjust temperature settings, and receive alerts from anywhere in the world, improving operational efficiency and convenience. Additionally, the use of artificial intelligence (AI) and machine learning (ML) algorithms can analyze the large amounts of temperature – related data generated by the systems. These algorithms can be used to optimize temperature control, predict system failures, and improve the overall performance of the systems.
Miniaturization and Portability
There is a growing demand for smaller, more portable thermonics temperature forcing systems, especially in applications where mobility is required, such as field research or on – site product testing. Advances in microfabrication techniques and the development of compact, high – performance components will enable the creation of smaller – scale temperature forcing systems without sacrificing performance. These portable systems can be easily transported to different locations, providing flexibility and convenience for users.
Focus on Energy Efficiency and Sustainability
With increasing concerns about energy consumption and environmental sustainability, future thermonics temperature forcing systems will likely focus on improving energy efficiency. This may involve the development of more efficient heating and cooling technologies, such as advanced thermoelectric materials or improved refrigeration cycles. Additionally, the use of renewable energy sources, such as solar or wind power, to operate these systems may become more common. Systems may also be designed with features to recycle or reuse heat, further reducing their energy footprint.
In conclusion, thermonics temperature forcing systems are essential tools in many scientific, industrial, and technological fields. While they come with certain challenges, such as high cost and complexity, their advantages in providing precise temperature control, customizable profiles, versatility, and reliability make them indispensable. As technology continues to evolve, these systems are expected to become more advanced, integrated, and sustainable, further expanding their applications and capabilities.
Related recommendations
process chillers manufacturers
339Process Chillers Manufacturers: Driving Efficiency and Innovation Process chillers are indispensable in maintaining optimal temperatures in numerous industrial processes. Manufacturers of these...
View details20 ton chiller
206A 20 - ton chiller is a powerful cooling system used in various applications to remove heat from a space or process. The “20 - ton” rating is a measure of its cooling capacity. Specifically, it me...
View detailsglycol chiller systems
162Glycol Chiller Systems: A Comprehensive OverviewGlycol chiller systems are specialized cooling systems that utilize glycol - based solutions as secondary coolants to transfer heat and maintain de...
View detailsheating and cooling products
159Heating and Cooling Products: A Detailed OverviewMaintaining a comfortable indoor environment requires reliable heating and cooling solutions. This guide explores different types of HVAC (Heating,...
View details
HelloPlease log in