temperature in chiller
Introduction to Temperature in Chiller Systems
Chiller systems are essential in maintaining specific temperature ranges for a variety of applications, from HVAC in buildings to industrial processes such as plastic injection and food processing. The term “temperature in chiller” denotes the set temperatures that these systems regulate to ensure optimal performance and efficiency.
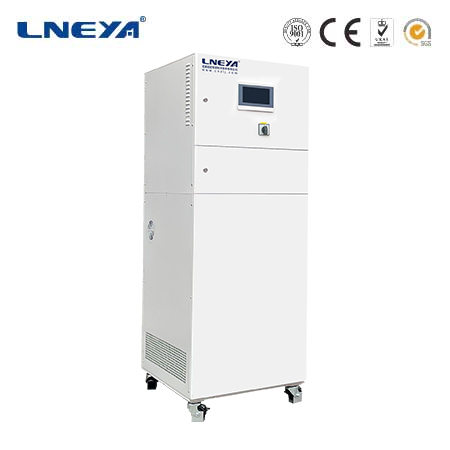
Significance of Temperature Control in Chillers
Process Efficiency: Precise temperature control is crucial for the efficiency of processes that rely on chillers, as it can affect the quality and consistency of products.
Equipment Protection: Maintaining the correct temperature helps protect equipment from damage due to overheating or thermal stress.
Factors Influencing Optimal Chiller Temperatures
Type of Process: Different processes require different temperature ranges. For instance, a chiller used in a data center will operate at a higher temperature than one used for food processing.
Equipment Design: The design and capacity of the chiller determine the temperature range it can effectively manage.
Environmental Conditions: Ambient temperature and humidity can influence the chiller’s set points and performance.
Impact of Chiller Temperatures on Energy Efficiency
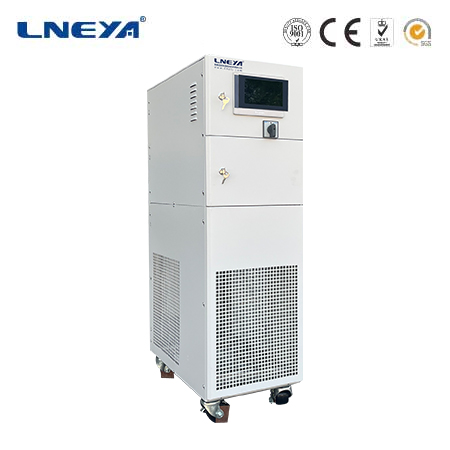
Energy Consumption: Chillers that operate at optimal temperatures consume less energy, reducing operational costs.
System Lifespan: Proper temperature management can extend the lifespan of chiller components, reducing maintenance and replacement costs.
Guidelines for Maintaining Chiller Temperatures
Regular Maintenance: Routine checks and maintenance ensure that chillers operate within their designed temperature ranges.
Calibration: Periodic calibration of temperature sensors and controls helps maintain accuracy.
Preventive Measures: Implementing preventive measures, such as monitoring for leaks and wear, can prevent temperature control issues.
Conclusion
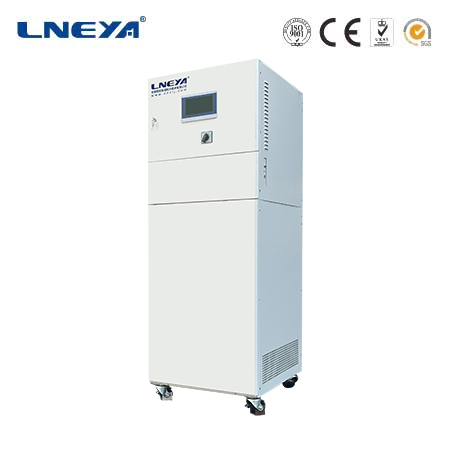
The “temperature in chiller” is a critical parameter that affects process efficiency, product quality, and energy consumption. Understanding the factors that influence optimal chiller temperatures and following best practices for maintenance and operation are essential for ensuring the effectiveness of these systems.
Note: This article is for informational purposes only and does not endorse any specific product or service. It is essential to consult with a qualified professional when designing, installing, or maintaining a chiller system to ensure it meets the specific requirements of the application and complies with industry standards.
Related recommendations
air cooled process chiller
327Air-Cooled Process Chillers: Operation and Advantages Air-cooled process chillers utilize ambient air to remove heat from the refrigerant, making them a preferred choice for smaller to medium-s...
View detailsheating water bath
131Heating Water Bath: A Comprehensive GuideA heating water bath is a versatile piece of equipment designed to provide a stable and controlled heat source by heating water within a contained vessel....
View detailssmardt water cooled chiller
70Key Technological FeaturesPatented Flooded Evaporator TechnologyOne of the most distinctive features of Smardt water cooled chillers is their patented flooded evaporator design. In a traditional...
View detailssmall industrial water chiller
437Small Industrial Water Chillers: Market Trends and Applications Small industrial water chillers are essential in maintaining optimal temperatures in various industrial processes. These chillers...
View details
HelloPlease log in