process heating
Process heating is a fundamental and widely – used concept in the industrial and manufacturing sectors. It involves the use of thermal energy to heat materials to specific temperatures for various manufacturing procedures such as melting, curing, drying, and more. This process is essential for enhancing productivity and efficiency in industrial operations, and it plays a crucial role in determining the quality of the final products.
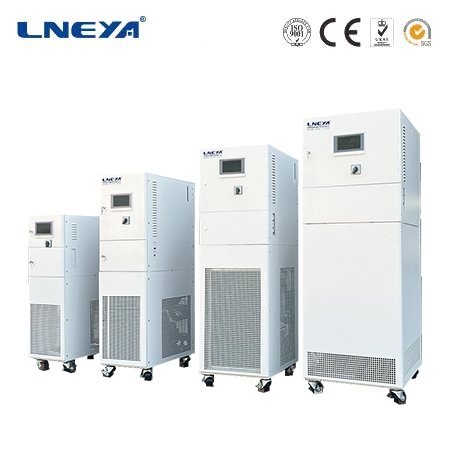
Definition and Basics
Process heating can be defined as the transfer of thermal energy to a substance with the aim of achieving a desired temperature. This thermal energy transfer can occur through three main mechanisms: conduction, convection, and radiation.
Conduction: This is the transfer of heat between two objects in direct contact. For example, when a metal rod is placed in a fire, heat travels along the length of the rod from the hot end (in contact with the fire) to the cooler end through conduction. In industrial settings, conduction is often used in heating elements that are in direct contact with the materials to be heated, such as in electric resistance heaters.
Convection: Convection involves the transfer of heat through a fluid (liquid or gas). There are two types of convection: natural convection, which occurs due to density differences in the fluid caused by temperature variations (for example, hot air rising in a room), and forced convection, which is aided by external means like fans or pumps. In process heating, forced – convection ovens are commonly used, where hot air is blown over the materials to be heated, ensuring more uniform heating.
Radiation: Radiation is the transfer of thermal energy through electromagnetic waves. Infrared heaters are a common example of radiation – based process heating. They emit infrared radiation, which is absorbed by the materials, causing them to heat up. This method is useful for applications where direct contact heating is not feasible or when rapid heating is required.
Applications in Different Industries
Process heating has a wide range of applications across various industries:
Metals Industry:
Melting: In steel production, electric arc furnaces are used to melt scrap metal. The high temperatures (well over 1000 °C) required for melting are achieved through process heating. This allows for the production of new steel products from recycled materials.
Forging and Heat Treatment: Metals are heated to specific temperatures to make them more malleable for forging into desired shapes. Heat treatment processes such as annealing, quenching, and tempering are also carried out using process heating. These processes change the mechanical properties of the metals, enhancing their strength, toughness, or hardness.
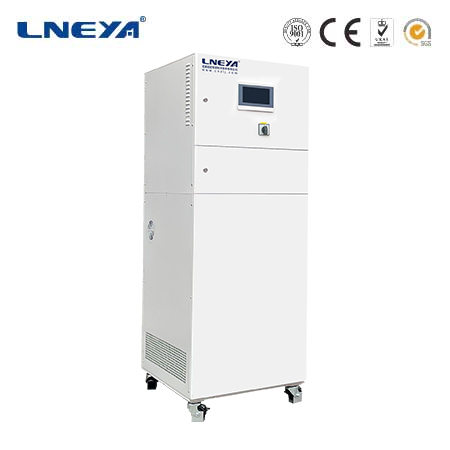
Food and Beverage Industry:
Cooking and Baking: Process heating is used in commercial ovens, cookers, and fryers. For example, in a bakery, ovens heat the dough to the right temperature for baking bread, cakes, and pastries. In a food processing plant, cookers are used to heat and cook ingredients for products like soups, sauces, and ready – meals.
Pasteurization: To ensure the safety of milk, juice, and other beverages, pasteurization is carried out. This involves heating the liquid to a specific temperature (usually around 70 – 80 °C for milk) for a set period to kill harmful bacteria while maintaining the quality and taste of the product.
Drying: In the production of dried fruits, nuts, and grains, process heating is used to remove moisture. Hot air is blown over the food products in drying chambers, evaporating the water content and extending the shelf – life of the products.
Petroleum and Chemical Industry:
Distillation: In petroleum refining, crude oil is separated into its various components (such as gasoline, diesel, and kerosene) through a distillation process. This process involves heating the crude oil in a distillation column to different temperatures, as each component has a different boiling point.
Chemical Reactions: Many chemical reactions require specific temperatures to occur. Process heating is used to provide the necessary heat for reactions such as polymerization (used in the production of plastics), esterification (in the production of esters for fragrances and plastics), and many others.
Automotive Industry:
Painting and Coating: After the body of a car is assembled, it goes through a painting process. The paint is first applied and then cured using process heating. This can be done in a convection oven or through infrared heating. The curing process ensures that the paint forms a durable and smooth finish.
Plastic Molding: In the production of plastic parts for cars, such as dashboards and bumpers, plastic pellets are melted using process heating and then injected into molds to take the desired shape.
Process Heating Systems
A typical process heating system consists of several components:
Heat Source:
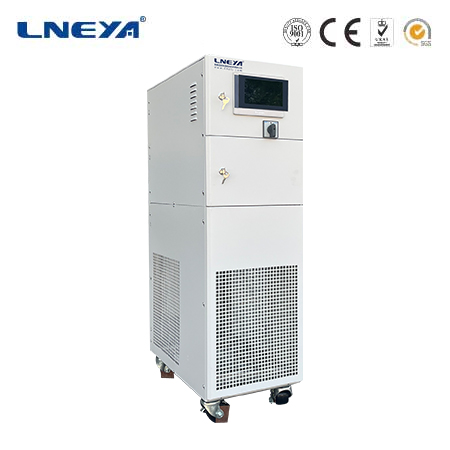
Fuel – fired Burners: These use fuels such as natural gas, oil, or coal to produce heat through combustion. For example, in a large industrial furnace, natural gas burners are often used. The combustion of natural gas releases a large amount of heat, which is then used to heat the materials or the environment within the furnace.
Electric Heaters: Electric heaters work on the principle of Joule heating. When an electric current passes through a resistive element (such as a wire made of nichrome), heat is generated. Electric heaters are known for their precise temperature control and are used in applications where accuracy is crucial, like in some laboratory heating equipment or in certain electronics manufacturing processes.
Steam Generators: Steam can be used as a heat source. Boilers are used to generate steam by heating water. The steam can then be used directly for heating applications (such as in some food processing or textile industries) or to drive turbines for power generation in combined – heat – and – power systems.
Material Handling System: This system is responsible for transporting the materials through the heating system. In a continuous production line, conveyors may be used to move products through an oven or a heating chamber. In a batch – type process, cranes or forklifts may be used to load and unload materials into and out of the heating equipment.
Enclosure: An enclosure is used to isolate the material from the external environment and to contain the heat. Furnaces, ovens, and kilns are examples of enclosures. They are often insulated to minimize heat loss, which helps in improving the energy efficiency of the process heating system. The design of the enclosure also affects the distribution of heat within it, ensuring uniform heating of the materials.
Types of Process Heating Technologies
Direct Heating: In direct heating, the heat source is in direct contact with the material to be heated. For example, in a simple gas – fired furnace used for melting metals, the flames from the gas burners directly impinge on the metal, transferring heat to it. This method is relatively simple and can be very efficient for some applications, but it may not be suitable for materials that are sensitive to contaminants from the combustion process.
Indirect Heating: Indirect heating involves the use of a heat exchanger. A heat – transfer fluid (such as thermal oil, water, or steam) is heated in a separate chamber by the heat source and then circulated through the heat exchanger, where it transfers heat to the material to be heated without direct contact. This method is useful when the material to be heated cannot tolerate direct exposure to the heat source, such as in the food industry or in some pharmaceutical processes.
Electric Heating Technologies:
Resistance Heating: As mentioned earlier, resistance heating uses the resistance of a material to an electric current to generate heat. It is widely used in small – scale heating applications and in situations where precise temperature control is required.
Induction Heating: Induction heating works on the principle of electromagnetic induction. When an alternating current is passed through a coil, it creates a changing magnetic field. If a metal object is placed within this magnetic field, eddy currents are induced in the metal, which in turn generate heat due to the electrical resistance of the metal. Induction heating is used in applications such as metal forging, heat treatment, and in some cooking appliances.
Energy Efficiency in Process Heating
Energy efficiency in process heating is crucial for reducing operating costs and minimizing environmental impact. Here are some ways to improve energy efficiency:
Insulation: Proper insulation of the heating equipment and pipelines can significantly reduce heat loss. High – quality insulation materials with low thermal conductivity, such as fiberglass, mineral wool, or polyurethane foam, can be used to line the walls of furnaces, ovens, and to wrap pipes. This helps in keeping the heat within the system where it is needed, rather than losing it to the surrounding environment.
Waste Heat Recovery: Many process heating systems produce waste heat that can be recovered and reused. For example, in a fuel – fired furnace, the hot flue gases can be used to pre – heat the incoming air for combustion or to pre – heat the materials to be processed. Heat exchangers can be installed to transfer the heat from the waste stream (such as flue gases) to a useful stream (such as incoming air or water).
Optimizing Burner Operations: Adjusting the air – to – fuel ratio in burners is important for efficient combustion. If there is too much air, it can lead to excess heat being carried away in the flue gases, reducing efficiency. On the other hand, if there is too little air, incomplete combustion occurs, resulting in wasted fuel and increased emissions. Modern burners are often equipped with sensors and control systems to optimize the air – to – fuel ratio.
Upgrading Heating Equipment: Using more energy – efficient heating equipment can lead to significant energy savings. For example, replacing old – fashioned electric resistance heaters with more advanced induction heating systems can reduce energy consumption in some applications. Newer models of furnaces and ovens are also designed with better insulation and more efficient heat distribution systems.
Implementing Energy Management Systems: Energy management systems can monitor and control the energy usage of process heating systems. These systems can collect data on energy consumption, temperature, and other parameters, and then use this data to optimize the operation of the system. For example, they can adjust the heating schedule based on the production requirements, turning off or reducing the heat when it is not needed.
Future Trends in Process Heating
Sustainable and Renewable Energy Sources: There is a growing trend towards using renewable energy sources for process heating. Solar – powered process heating systems are being developed, where solar collectors are used to capture solar energy and convert it into heat. Biomass – fired boilers are also becoming more popular as a sustainable alternative to fossil – fuel – fired boilers, especially in industries where biomass feedstocks are readily available, such as in the forestry or agricultural sectors.
Advanced Control Systems and Automation: Future process heating systems will likely rely more on advanced control systems and automation. Smart sensors and controllers will be able to monitor and adjust the heating process in real – time, based on various factors such as the quality of the incoming materials, the desired final product characteristics, and the energy availability. This will lead to more precise temperature control, better product quality, and increased energy efficiency.
Nanotechnology – enabled Heating Materials: Nanotechnology may play a role in developing new heating materials. Nanocomposites with enhanced thermal conductivity could be used in heating elements or heat exchangers, improving the performance of process heating systems. These materials may also have other advantages such as better durability and resistance to corrosion.
In conclusion, process heating is a complex and essential aspect of modern industrial and manufacturing processes. Understanding its principles, applications, systems, and energy – efficiency measures is crucial for industries to operate efficiently, produce high – quality products, and meet the challenges of sustainability in the future.
Related recommendations
How important is insulation treatment for laboratory chiller?
896How important is insulation treatment for laboratory chiller? For chillers, if operated at high temperatures, a large amount of cold air from industrial chillers may be severely lost. A...
View details1.5 ton water chiller
319Introduction to 1.5 Ton Water ChillersA 1.5 ton water chiller is an industrial cooling system designed to remove heat from various processes, providing a cooling capacity of 18,000 BTU/HR. These c...
View detailsportable industrial chiller
412Portable Industrial Chiller: Versatile Cooling Solutions for Industrial Applications Portable industrial chillers, also known as portable cooling units, are essential in providing flexible and ...
View detailschiller machine manufacturers
399Chiller Machine Manufacturers: A Global Perspective Chiller machine manufacturers play a crucial role in providing efficient cooling solutions for industries such as plastics, food and beverage...
View details
HelloPlease log in