process heaters
The Role and Importance of Process Heaters in Industrial Processes
Process heaters play a critical role in a wide range of industries, from petrochemical to food processing. They are used to maintain the necessary temperatures for chemical reactions, to heat materials for processing, and to maintain the temperature of liquids in pipelines. The efficiency and reliability of process heaters can significantly impact the productivity and safety of industrial operations.
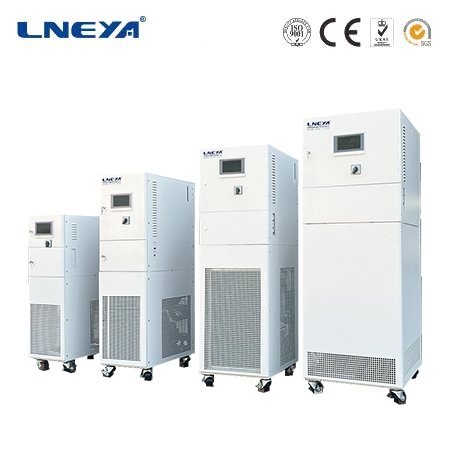
Types of Process Heaters
There are several types of process heaters, each designed for specific applications:
Direct Fired Heaters: These heaters use a direct flame to heat the process medium. They are simple in design and can achieve high temperatures quickly. However, they may not be suitable for processes that require precise temperature control or where the flame could contaminate the process medium.
Indirect Fired Heaters: In these heaters, the flame is separated from the process medium by a heat exchanger. This design allows for better temperature control and is suitable for processes where the flame must not come into direct contact with the medium.
Electric Heaters: Electric heaters use electric resistance to generate heat. They offer precise temperature control and are suitable for applications where there is a need for a clean heat source. However, they can be less energy-efficient than fired heaters for large-scale heating.
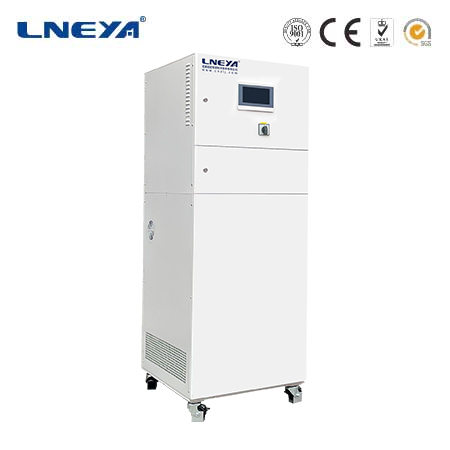
Heat Exchangers: These are used to transfer heat from one fluid to another without mixing the fluids. They can be shell and tube, plate, or spiral types, and are used when there is a need to heat or cool a process fluid without direct contact with the heat source.
Applications of Process Heaters
Process heaters are used in various applications across different industries:
Petrochemical Industry: They are used to heat hydrocarbons for refining and to maintain the temperature of pipelines to prevent wax buildup.
Chemical Processing: In chemical plants, heaters are used to provide the necessary heat for reactions and to control the temperature of processes to ensure optimal yield and product quality.
Food Processing: Heaters are used to pasteurize and sterilize products, as well as to cook and dry ingredients.
Pharmaceutical Industry: They are essential for heating and cooling processes in the manufacture of drugs and medicines.
Power Generation: In power plants, heaters are used to preheat boiler feedwater and to maintain the temperature of various process fluids.
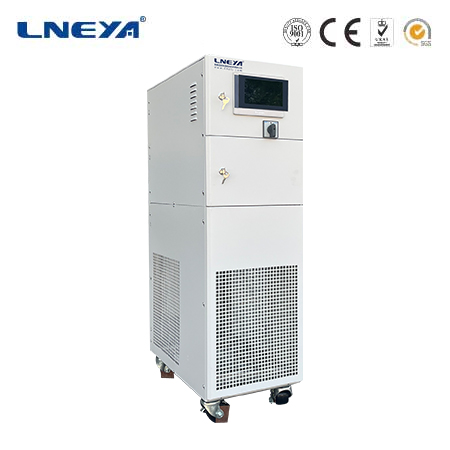
Benefits of Process Heaters
The benefits of using process heaters include:
Efficiency: Modern process heaters are designed to minimize heat loss and maximize energy efficiency.
Control: They offer precise temperature control, which is crucial for maintaining the quality and consistency of products in various industries.
Reliability: Process heaters are built to withstand harsh industrial conditions, ensuring reliable operation over extended periods.
Safety: With proper design and maintenance, process heaters can operate safely, reducing the risk of accidents and downtime.
Safety Considerations
When using process heaters, safety is a paramount concern. Some safety considerations include:
Flame Arrestors: These are used to prevent flashback fires in direct fired heaters.
Pressure Relief Valves: These valves release pressure if it exceeds safe levels, preventing explosions.
Temperature Monitoring: Continuous monitoring of temperatures ensures that processes do not exceed safe operating limits.
Regular Maintenance: Regular inspection and maintenance of process heaters can prevent accidents and extend the life of the equipment.
Selecting the Right Process Heater
When selecting a process heater, several factors should be considered:
Thermal Load: The heater must be capable of providing the necessary heat to meet the process requirements.
Temperature Range: The heater should be able to operate within the required temperature range for the process.
Energy Source: The availability and cost of the energy source (e.g., natural gas, electricity) should be considered.
Process Medium: The type of fluid or material being heated will determine the type of heater required.
Control Requirements: The level of temperature control needed will influence the choice of heater.
Safety and Environmental Regulations: Compliance with local safety and environmental regulations is essential.
In conclusion, process heaters are indispensable in maintaining the efficiency and safety of industrial processes. By understanding the different types, applications, benefits, and safety considerations, industries can select the most suitable process heaters for their specific needs. Regular maintenance and adherence to safety standards ensure that these heaters operate reliably and efficiently, contributing to the overall productivity of the process.
Related recommendations
sistem chiller
420Understanding Chiller Systems: Technology and Applications Chiller systems are essential in maintaining optimal temperatures in a variety of industrial and commercial applications. These system...
View detailsportable chiller units
238The Operation and Significance of Portable Chiller Units Portable chiller units are self-contained, temporary cooling solutions that provide precise temperature control for a variety of industr...
View detailswater bath in the laboratory
72Water Bath in the Laboratory: Functions, Types, and ApplicationsIn the bustling environment of a laboratory, where precision and control are paramount, the water bath stands as an indispensable p...
View detailswater cooling system for industry
268Water Cooling System for Industry: Operational Efficiency and Best Practices Industrial processes often generate significant amounts of heat that, if left unchecked, can damage equipment and di...
View details
HelloPlease log in