process cooler
Introduction
In the complex landscape of industrial activities, maintaining appropriate temperature levels is often a determining factor for the success and efficiency of various processes. Process coolers are specialized equipment designed to remove excess heat from industrial systems, substances, or environments, ensuring that operations proceed smoothly and that products meet the required quality standards. Whether it’s cooling machinery in a manufacturing plant, preserving perishable goods in the food industry, or maintaining the stability of sensitive equipment in data centers, process coolers play an indispensable role.
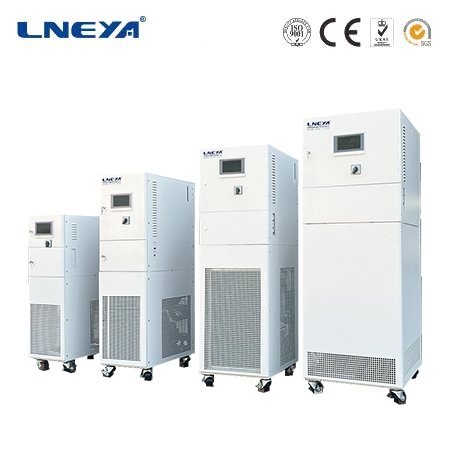
Types of Process Coolers
Mechanical Vapor Compression Coolers
Working Principle
Mechanical vapor compression coolers operate based on the vapor – compression refrigeration cycle, which is a fundamental mechanism for heat transfer. This cycle comprises four main components: the compressor, condenser, expansion valve, and evaporator.
Compression: The cycle commences with the compressor. It draws in low – pressure, low – temperature refrigerant vapor and compresses it, significantly increasing both its pressure and temperature. This compression process requires mechanical energy, usually provided by an electric motor. As the refrigerant is compressed, its state transforms from a low – energy vapor to a high – pressure, high – energy state, making it ready to release heat.
Condensation: The high – pressure, high – temperature refrigerant vapor then moves to the condenser. Here, the refrigerant transfers its heat to a cooling medium, which can be either air or water. In air – cooled condensers, fans blow ambient air over the condenser coils, facilitating the heat dissipation process. In water – cooled condensers, the refrigerant releases heat to a water loop, which may then be cooled further using a cooling tower. As heat is removed, the refrigerant condenses back into a liquid.
Expansion: After condensation, the high – pressure liquid refrigerant passes through an expansion valve. The expansion valve rapidly reduces the pressure of the refrigerant, causing it to expand and cool down significantly. This results in the formation of a low – pressure, low – temperature two – phase mixture of liquid and vapor.
Evaporation: The low – pressure, low – temperature refrigerant mixture enters the evaporator. Inside the evaporator, the refrigerant absorbs heat from the substance or process that needs to be cooled, such as a fluid in an industrial process or the air in a cooling system. As the refrigerant absorbs heat, it evaporates back into a vapor, effectively cooling the target medium. The now low – pressure refrigerant vapor is then drawn back into the compressor, restarting the cycle.
Sub – types
Reciprocating Compressor Coolers: These coolers utilize reciprocating compressors, where pistons move back and forth within cylinders. Reciprocating compressor coolers are suitable for smaller – to medium – sized cooling applications. They offer a relatively simple design and can provide good efficiency for their size, making them a common choice in many industrial settings with moderate cooling demands.
Centrifugal Compressor Coolers: Centrifugal compressors use centrifugal force to increase the pressure of the refrigerant. They are typically employed for large – scale cooling applications, such as in industrial plants with high – volume cooling requirements or large commercial buildings. Centrifugal compressors can handle high volumes of refrigerant and operate with high efficiency at full load, making them ideal for scenarios where substantial cooling capacity is needed.
Scroll Compressor Coolers: Scroll compressors consist of two interlocking spiral – shaped scrolls, with one scroll fixed and the other orbiting around it. Scroll compressor coolers are known for their quiet operation, high efficiency, and reliability. They are commonly used in medium – sized commercial and industrial applications where a balance between performance and noise reduction is desired.
Absorption Coolers
Working Mechanism
Absorption coolers operate on a principle distinct from mechanical vapor compression coolers. Instead of relying on mechanical energy to drive the cooling process, they use a heat source, such as steam, hot water, or natural gas. The key components of an absorption cooler include the absorber, generator, condenser, evaporator, and a pump.
Absorption and Generation: The process begins in the absorber, where a weak solution of a refrigerant (commonly water) and an absorbent (such as lithium bromide in water – based systems) absorbs the refrigerant vapor. This absorption is an exothermic process, releasing heat. The strong solution, rich in refrigerant, is then pumped to the generator. In the generator, heat from the external source is applied to the strong solution. As the solution is heated, the refrigerant vaporizes, leaving behind a weak solution. The refrigerant vapor then proceeds to the condenser.
Condensation, Expansion, and Evaporation: Similar to mechanical vapor compression coolers, in the condenser, the refrigerant vapor releases heat and condenses into a liquid. The liquid refrigerant then passes through an expansion valve, where its pressure drops, and it enters the evaporator. In the evaporator, the refrigerant absorbs heat from the process fluid, evaporating back into a vapor. The refrigerant vapor then returns to the absorber, completing the cycle.
Advantages
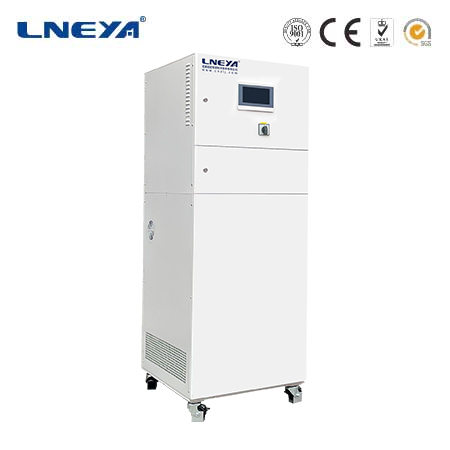
Absorption coolers offer several advantages, especially in situations where there is an abundant supply of low – cost heat. For example, in industrial plants that generate waste heat as a by – product of other processes, absorption coolers can utilize this waste heat to produce cooling, effectively recycling energy and reducing overall energy costs. Additionally, they can be more environmentally friendly as they do not rely on electrically – driven compressors, potentially reducing electricity consumption and associated carbon emissions.
Evaporative Coolers
Cooling Process
Evaporative coolers leverage the natural cooling effect of water evaporation to lower the temperature of the target medium. They typically consist of a water basin, spray nozzles, a heat exchanger, and fans.
Water Distribution and Evaporation: The warm substance or fluid that needs to be cooled enters the heat exchanger. Meanwhile, water from the basin is pumped and sprayed over the heat exchanger surfaces. As the water droplets are exposed to the air, a portion of the water evaporates. Since evaporation is an endothermic process, it absorbs heat from the surrounding environment, including the heat exchanger and the fluid inside it.
Airflow and Heat Transfer: Fans in the evaporative cooler draw in ambient air, which passes over the wet heat exchanger surfaces. The moving air enhances the evaporation process, increasing the rate of heat transfer. The cooled fluid then exits the cooler, ready to be circulated back into the industrial process. The evaporated water is replenished from a water supply, and the warm, humid air is exhausted outside.
Limitations
Evaporative coolers are most effective in dry climates, as the rate of evaporation is higher in low – humidity environments. In humid climates, the evaporation rate is reduced, limiting their cooling capacity. Additionally, they require a continuous water supply, and proper water treatment may be necessary to prevent issues such as scale formation and the growth of microorganisms in the water system.
Applications of Process Coolers
Manufacturing Industry
Plastic Manufacturing: In plastic injection molding and extrusion processes, maintaining precise temperature control is crucial for product quality. Process coolers are used to cool the molds and barrels, ensuring that the plastic material solidifies correctly and maintains the desired shape and dimensions. By controlling the cooling rate, manufacturers can reduce defects such as warping, shrinkage, and surface imperfections, improving overall production efficiency and product quality.
Metalworking: Metal machining operations, such as milling, turning, and grinding, generate a significant amount of heat. Process coolers are employed to cool cutting fluids, which not only lubricate the cutting tools but also remove heat from the machining area. This helps prevent tool wear, improves the surface finish of the metal parts, and allows for higher machining speeds, enhancing the productivity of the metalworking process.
Electronics Manufacturing: In the production of electronic components, even small temperature variations can affect the quality and performance of the products. Process coolers are used to cool the equipment used in manufacturing processes, such as reflow ovens, plasma etching machines, and lithography tools. By maintaining stable temperatures, process coolers ensure the accurate functioning of these critical pieces of equipment, reducing the likelihood of production errors and improving the yield of high – quality electronic components.
Food and Beverage Industry
Food Processing: In food processing plants, process coolers play a vital role in maintaining the freshness and quality of food products. They are used for cooling and freezing food items, such as meats, fruits, and vegetables, to inhibit the growth of bacteria and extend their shelf life. In the production of dairy products, coolers are used to maintain the cold chain during processing, storage, and transportation, ensuring the safety and integrity of the products.
Beverage Production: In the beverage industry, process coolers are essential for cooling and carbonating beverages. They cool the water used in the production process, as well as the beverages themselves during storage and dispensing. In beer brewing, for example, coolers are used to cool the wort after boiling, a critical step for proper fermentation. Additionally, they help maintain the desired temperature for carbonated beverages, ensuring the right level of carbonation and taste.
Pharmaceutical Industry
Drug Manufacturing: The pharmaceutical industry has strict temperature requirements for the production, storage, and transportation of drugs. Process coolers are used to maintain the cold chain throughout the manufacturing process, cooling reactors, storage tanks, and other equipment to ensure that chemical reactions occur at the correct temperatures and that drugs remain stable and effective. They also cool the air in cleanrooms, which are essential for preventing contamination during drug production, safeguarding the quality and safety of pharmaceutical products.
Biotechnology: In biotechnology applications, such as the production of vaccines, enzymes, and other biological products, precise temperature control is vital. Process coolers are used to cool bioreactors, centrifuges, and other equipment to maintain the optimal growth conditions for cells and microorganisms. They also help preserve the integrity of biological samples during storage and transportation, ensuring the success of biotechnological research and production processes.
Data Centers
Data centers house a large number of servers that generate a significant amount of heat during operation. Process coolers are used to cool the air or water that circulates through the data center to maintain the optimal operating temperature for the servers. By removing the heat, coolers prevent server overheating, which can lead to system failures, data loss, and reduced server lifespan. Advanced data centers may use sophisticated cooling systems, such as liquid – cooled servers, where process coolers directly cool the coolant fluid that cools the server components, enabling high – density server installations and efficient heat management.
Factors to Consider When Choosing a Process Cooler
Cooling Capacity
Determining the appropriate cooling capacity is the first and most critical step in selecting a process cooler. The cooling capacity needed depends on the heat load generated by the industrial process or the equipment to be cooled. This heat load is calculated based on factors such as the power consumption of the equipment, the rate of heat generation during chemical reactions, or the amount of heat to be removed from a specific space. It is essential to choose a cooler with a cooling capacity that can handle the maximum heat load of the system, with some additional margin to account for future growth, unexpected heat surges, or changes in operating conditions. Oversizing the cooler can lead to higher initial costs, increased energy consumption, and unnecessary equipment complexity, while undersizing it will result in inadequate cooling, potential equipment damage, and process inefficiencies.
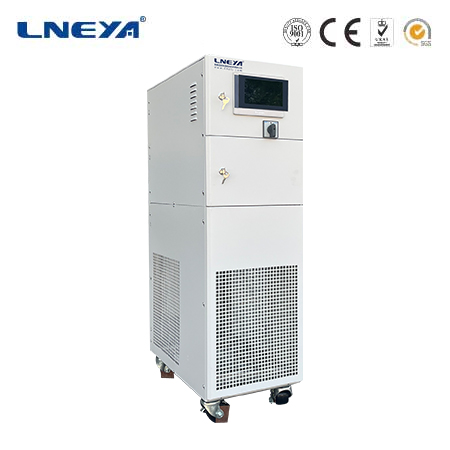
Energy Efficiency
Energy efficiency is a crucial consideration, as it directly impacts the operating costs of the process cooler over its lifespan and also has environmental implications. Different types of process coolers have varying levels of energy efficiency. For example, mechanical vapor compression coolers with high – efficiency compressors and advanced control systems can offer better energy performance. Absorption coolers can be highly efficient when paired with appropriate waste heat sources, effectively utilizing otherwise wasted energy. Evaporative coolers are generally more energy – efficient in terms of electrical consumption compared to mechanical refrigeration systems, as they primarily rely on the natural process of evaporation and the use of fans. When evaluating energy efficiency, look for coolers with high – efficiency ratings, such as those certified by energy – saving programs in your region, and consider features like variable – speed drives that can adjust the cooler’s operation based on the actual cooling demand, reducing energy consumption during periods of low load.
Refrigerant Type
The choice of refrigerant in a process cooler, especially for mechanical vapor compression systems, has both environmental and safety implications. Older refrigerants, such as chlorofluorocarbons (CFCs) and hydrochlorofluorocarbons (HCFCs), have been phased out due to their ozone – depleting properties. Hydrofluorocarbons (HFCs) are commonly used as replacements, but they also contribute to global warming. In recent years, there has been a growing trend towards using more environmentally friendly refrigerants, such as natural refrigerants like ammonia, carbon dioxide, and hydrocarbons. These natural refrigerants have lower global warming potentials and, in some cases, offer better thermodynamic properties. However, each refrigerant has its own safety characteristics. For example, ammonia is highly efficient but toxic and flammable in certain concentrations, requiring strict safety measures for handling and storage. When choosing a refrigerant, it is essential to consider the safety requirements of the facility, local environmental regulations, and the overall lifecycle impact of the refrigerant on the environment.
Maintenance Requirements
Regular maintenance is necessary to keep a process cooler operating efficiently and reliably. When choosing a cooler, consider the accessibility of its components for maintenance and repair. Coolers with easily removable parts, such as filters, condensers, and compressors, are easier to service, reducing maintenance time and costs. Also, check the availability of spare parts and the expertise of local service providers. Some coolers may require specialized training for maintenance personnel, and this should be factored into the decision – making process. Additionally, coolers with built – in monitoring and diagnostic systems can help detect potential problems early, allowing for timely maintenance and minimizing downtime. These systems can monitor parameters such as refrigerant pressure, temperature, and flow rates, providing valuable insights into the cooler’s performance and enabling proactive maintenance strategies.
Environmental Impact
In today’s environmentally conscious world, the environmental impact of process coolers is an important consideration. As mentioned, the choice of refrigerant can significantly affect the environmental footprint of the cooler. Additionally, the energy source used to power the cooler, especially for mechanical vapor compression and absorption coolers, has an impact. Coolers that can utilize renewable energy sources or waste heat are more environmentally friendly. Evaporative coolers, while they require a water supply, generally have a lower environmental impact in terms of greenhouse gas emissions compared to traditional mechanical refrigeration systems. When evaluating the environmental impact, consider the entire lifecycle of the cooler, from its manufacturing process to its end – of – life disposal, and choose options that align with sustainable practices and environmental goals.
Conclusion
Process coolers are integral to a wide range of industrial processes, ensuring the smooth operation, quality control, and energy efficiency of various industries. With a diverse array of types, each with its own working principles, advantages, and applications, understanding process coolers is essential for industries to make informed decisions when selecting the right cooling solution. By carefully considering factors such as cooling capacity, energy efficiency, refrigerant type, maintenance requirements, and environmental impact, industries can optimize their operations, reduce costs, and contribute to a more sustainable future. As technology continues to advance, we can expect to see further innovations in process cooler design, leading to even more efficient, environmentally friendly, and reliable cooling solutions.
Related recommendations
therm heating system
98Introduction to Therm Heating SystemA therm heating system, also known as a thermal heating system, is a mechanism designed to generate, transfer, and distribute thermal energy to meet specific h...
View detailsheat source system
290Introduction to Heat Source SystemsHeat source systems are essential in providing heat for a multitude of applications, from industrial processes to domestic heating. These systems can be powered ...
View detailschiller engineering
152Chiller engineering is a specialized field within mechanical and HVAC (Heating, Ventilation, and Air Conditioning) engineering. It focuses on the design, development, installation, and maintenance...
View detailsheating water bath
132Heating Water Bath: A Comprehensive GuideA heating water bath is a versatile piece of equipment designed to provide a stable and controlled heat source by heating water within a contained vessel....
View details
HelloPlease log in