glycol cooler unit
Glycol Cooler Unit: A Comprehensive Overview
A glycol cooler unit is a specialized piece of equipment that plays a vital role in heat transfer processes across different sectors. At its core, it utilizes a glycol-based solution as the heat transfer medium. Glycol, commonly ethylene glycol or propylene glycol, has properties that make it suitable for these applications, such as a low freezing point and good heat transfer capabilities.
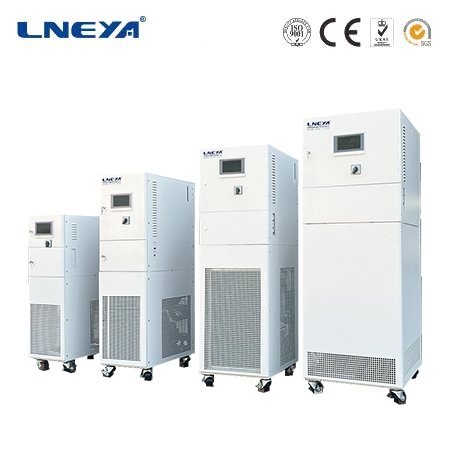
The basic working principle of a glycol cooler unit involves a closed-loop system. The glycol solution is pumped through the system. When it passes through the area or equipment that needs to be cooled (the heat source), it absorbs heat. The now warmer glycol solution then travels to a heat exchanger. In the heat exchanger, the heat from the glycol is transferred to another medium, usually air or water, depending on the design of the unit. As the heat is dissipated, the glycol cools down and is pumped back to the heat source to repeat the cycle.
The key components of a glycol cooler unit are as follows:
Heat Exchanger: This is where the actual heat transfer takes place. There are different types of heat exchangers used, such as shell and tube heat exchangers or plate heat exchangers. The design of the heat exchanger depends on factors like the required heat transfer rate, the properties of the fluids involved, and the space available for installation.
Pump: The pump is responsible for circulating the glycol solution throughout the system. It provides the necessary pressure to ensure a continuous flow of the solution, which is essential for efficient heat transfer.
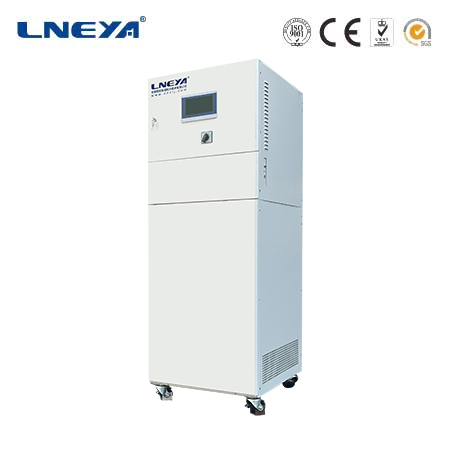
Controller: The controller monitors and regulates the operation of the glycol cooler unit. It can control parameters such as the flow rate of the glycol, the temperature of the solution, and the operation of the pump. This helps to maintain the desired cooling performance and ensures the unit operates within safe and efficient limits.
One of the significant advantages of glycol cooler units is their ability to operate in cold environments. Due to the low freezing point of the glycol solution, it can prevent freezing in the system even at sub-zero temperatures. This makes them ideal for applications in regions with harsh winters or in processes where maintaining a fluid’s liquid state is crucial.
In the food and beverage industry, glycol cooler units are used for cooling various products and processes. For example, in breweries, glycol is used to cool fermentation tanks to maintain the optimal temperature for yeast activity. In dairy processing, it helps in cooling milk and other dairy products to prevent spoilage.
In the chemical processing industry, glycol cooler units are employed to cool reactors, condensers, and other equipment. They ensure that chemical reactions occur at the desired temperatures and prevent overheating, which could lead to safety hazards or product quality issues.
In HVAC (Heating, Ventilation, and Air Conditioning) systems, glycol cooler units can be used in closed-loop systems to transfer heat between different parts of the building. They are especially useful in systems where water-based solutions may freeze in cold climates.
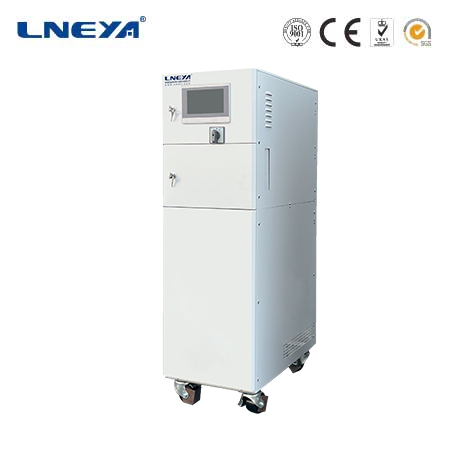
When installing a glycol cooler unit, several factors need to be considered. The location of the unit should be chosen carefully to ensure proper ventilation and access for maintenance. The sizing of the unit, including the capacity of the pump and the heat exchanger, should be based on the specific cooling requirements of the application.
During operation, it is important to monitor the glycol solution regularly. The concentration of the glycol in the solution should be maintained at the appropriate level to ensure its performance. Additionally, the temperature and pressure of the system should be checked to detect any potential issues early.
Maintenance of a glycol cooler unit includes tasks such as cleaning the heat exchanger to remove any fouling or deposits that could reduce its efficiency. The pump should be inspected for any signs of wear or damage, and the controller should be calibrated regularly to ensure accurate operation.
However, glycol cooler units also face some challenges. Over time, the glycol solution may degrade due to factors such as exposure to oxygen, heat, and contaminants. This can lead to a decrease in its performance and may require the solution to be replaced. Additionally, the handling and disposal of glycol need to be done in accordance with environmental regulations as some types of glycol, like ethylene glycol, can be toxic if not managed properly.
In conclusion, glycol cooler units are essential components in many industrial and commercial applications. Understanding their working principles, components, advantages, applications, and the considerations for installation, operation, and maintenance is crucial for maximizing their performance and ensuring their reliable operation.
Related recommendations
chilling system manufacturer
74IntroductionChilling systems are indispensable for maintaining optimal temperatures in a wide range of settings, from commercial buildings and data centers to industrial facilities and food proce...
View detailsflow through chiller
227Definition and Basic StructureA flow through chiller, also known as a direct - flow chiller, consists of several key components. At its core, it has a refrigerant circuit, a heat exchanger, a pump...
View detailsHow does the evaporator chiller reduce vibration and noise?
910How does the evaporator chiller reduce vibration and noise? Evaporator cooler is a device used to cool air or liquid, which can dissipate heat through evaporation. When using evaporator...
View detailsglycol chillers for sale
371Glycol Chillers for Sale: An In-Depth Overview Glycol chillers are crucial in applications where precise temperature control is required, such as in food processing, pharmaceuticals, and indust...
View details
HelloPlease log in