cooler temperature control
Cooler Temperature Control: Technologies and Applications
Temperature control in coolers is critical for ensuring the quality, safety, and longevity of stored items, whether it’s food, pharmaceuticals, or industrial materials. This article provides an in-depth look at the principles, technologies, and applications of cooler temperature control, emphasizing the importance of precise temperature management.
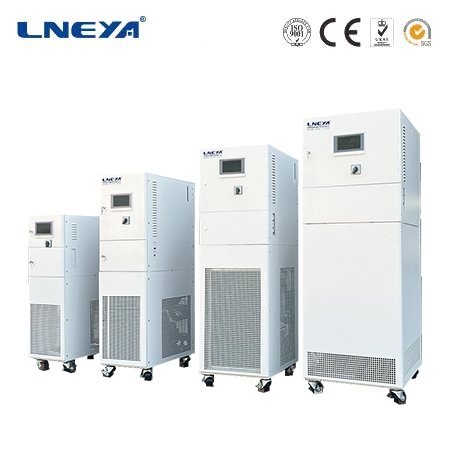
Principles of Temperature Control in Coolers
The primary goal of cooler temperature control is to maintain a stable and consistent temperature within a specified range. This is achieved through a combination of insulation, refrigeration, and monitoring systems.
Insulation: Proper insulation reduces heat transfer between the cooler’s interior and the surrounding environment, minimizing the need for active cooling.
Refrigeration Systems: These systems remove heat from the cooler’s interior through a cycle of compression, condensation, expansion, and evaporation. Common refrigerants include ammonia, carbon dioxide, and various synthetic compounds like R-134a and R-410A.
Monitoring and Control: Accurate temperature monitoring is crucial for maintaining the desired temperature setpoint. Sensors placed within the cooler provide real-time data, which is used by control systems to adjust the refrigeration system as needed.
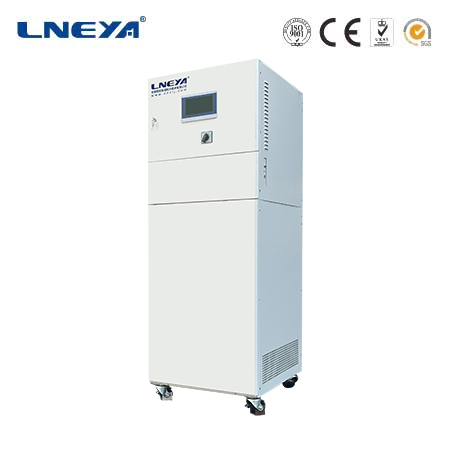
Technologies Used in Cooler Temperature Control
Several technologies are employed in cooler temperature control, each with its own advantages and applications.
Thermostat: A basic thermostat monitors temperature and switches the cooling system on or off to maintain a set temperature. While simple, this on-off control can lead to temperature fluctuations.
PID Controllers: Proportional-Integral-Derivative (PID) controllers offer more precise control by continuously adjusting the cooling system’s output based on the error between the setpoint and the actual temperature. This results in tighter temperature control and reduced energy consumption.
Advanced Control Systems: Modern coolers may employ microprocessors and sensors to monitor and control temperature, humidity, and other parameters. These systems can adapt to changing conditions and optimize performance for various loads and ambient temperatures.
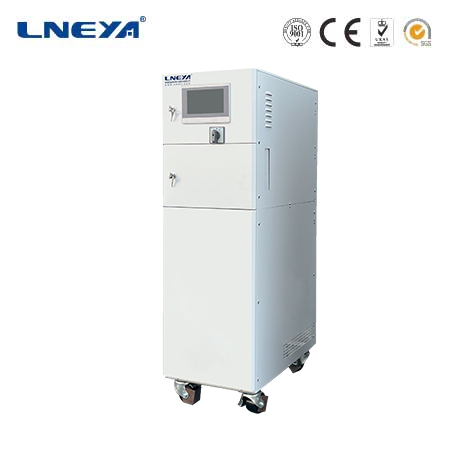
Applications of Cooler Temperature Control
Cooler temperature control is essential in a variety of industries and settings:
Food and Beverage: Accurate temperature control in refrigerated storage is crucial for preserving the freshness and safety of perishable goods. It also helps in complying with food safety regulations.
Pharmaceuticals: Many drugs and vaccines require specific temperature conditions for stability and efficacy. Coolers with precise temperature control ensure that these products remain within their required temperature ranges.
Industrial Processes: In industries such as chemical manufacturing, temperature control is critical for maintaining the quality and consistency of products and for ensuring the safety of processes.
Energy Efficiency and Sustainability
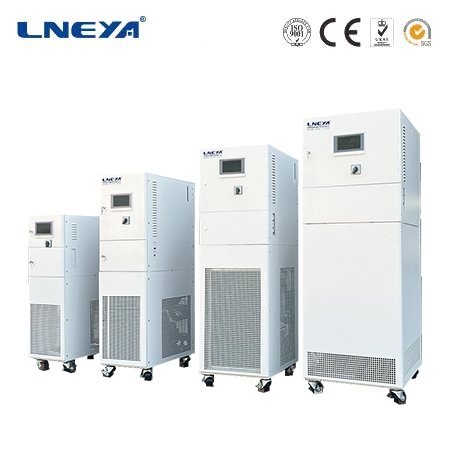
Cooler temperature control systems have a significant impact on energy consumption and sustainability. By optimizing temperature control, coolers can operate more efficiently, reducing energy use and environmental impact.
Energy-Efficient Refrigeration: Modern refrigeration systems and control technologies can significantly reduce the energy consumption of coolers. For example, frequency conversion compressors adjust their speed based on the cooling demand, saving energy during periods of low demand.
Sustainable Practices: The use of natural refrigerants and energy recovery systems in coolers can further reduce their environmental impact. Natural refrigerants have lower global warming potentials, while energy recovery systems capture waste heat for use in other processes.
Conclusion
Cooler temperature control is a critical aspect of maintaining the quality, safety, and longevity of stored items across various industries. By understanding the principles and technologies involved, and by adopting best practices in temperature management, we can ensure the effectiveness and sustainability of cooler operations. As technology continues to advance, we can expect even more precise and energy-efficient solutions for cooler temperature control.
Related recommendations
thermal oil heating system
291Thermal oil heating systems, also known as hot oil systems, are engineered to transfer heat generated by a furnace or other heat sources to process fluids in various industrial applications. These...
View details1.5 hp glycol chiller
100Working PrincipleThe operation of a 1.5 hp glycol chiller is based on the principles of the refrigeration cycle. The cycle consists of four main components: the compressor, condenser, expansion v...
View details600 ton chiller
225600 Ton Chiller: A Comprehensive Overview A 600 ton chiller is a powerful cooling device with the capacity to remove a significant amount of heat from a system. Types of 600 Ton Chillers ...
View detailsdifference between chiller and cooler
60Definition and Core PurposeChiller: A chiller is a complex refrigeration system designed to generate chilled water or another coolant, which is then circulated to absorb heat from large spaces, i...
View details
HelloPlease log in