closed cycle cooling water system
Closed Cycle Cooling Water Systems: Principles and Advantages
Closed cycle cooling water systems are engineered to maintain optimal temperatures in various industrial processes. Unlike open systems, closed systems circulate a fixed volume of coolant, which is not replenished with makeup water and does not evaporate. This allows for precise control over the coolant chemistry, reducing the risk of corrosion and fouling that can compromise system efficiency.
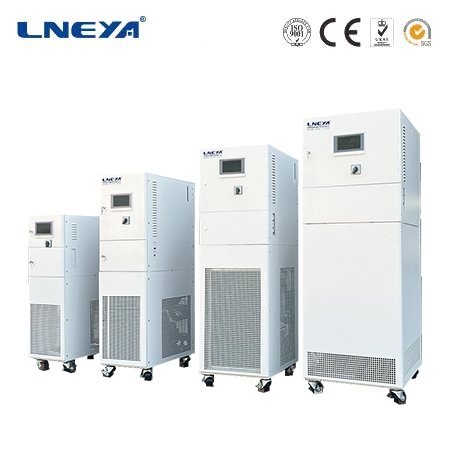
The primary advantage of closed cycle cooling water systems is their ability to operate with a controlled environment, which minimizes the impact of external variables such as ambient temperature and water quality. This control enables more efficient heat transfer and can lead to significant energy savings. Additionally, closed systems reduce water waste and environmental impact, as they do not require the continuous replenishment of water that open systems do.
Applications of Closed Cycle Cooling Water Systems
Closed cycle cooling water systems are used in a variety of industrial applications where precise temperature control is essential. These include steel mill furnace housings, refinery and chemical plant process heat exchangers, turbine lubricating oil coolers, pump bearings, air compressor interstages, and building heating/cooling systems. The suitability of closed cooling for many applications stems from the ability to carefully control the chemistry of the coolant.
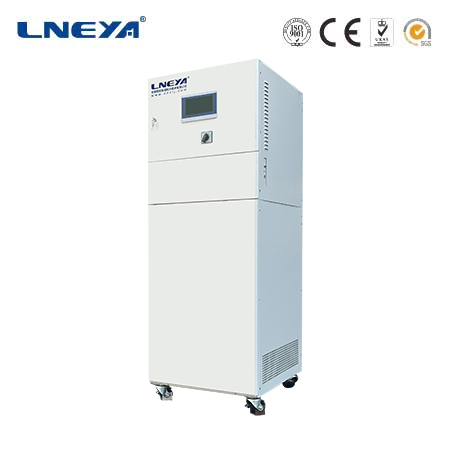
Water Treatment in Closed Cycle Systems
Proper water treatment and monitoring are crucial in closed cycle cooling water systems to prevent corrosion and fouling. Treatment programs often involve the use of corrosion inhibitors, such as nitrite or molybdate, which form protective films on metal surfaces. Additionally, microbiological control may be necessary to prevent the growth of microorganisms that can lead to fouling and under-deposit corrosion.
Energy Efficiency and Sustainability
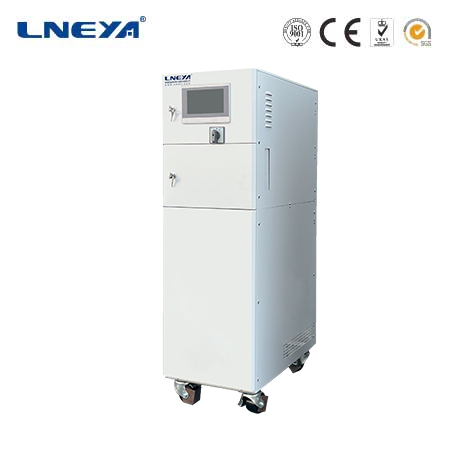
Closed cycle cooling water systems contribute to energy efficiency and sustainability in industrial processes. By controlling the coolant chemistry, these systems can operate more efficiently than open systems, reducing energy demand and costs. Furthermore, the reduced water usage and controlled environment of closed systems have a lower environmental impact compared to open systems, which can contribute to a facility’s sustainability goals.
Conclusion
Closed cycle cooling water systems are vital for precise temperature control in industrial processes. They offer advantages in efficiency, sustainability, and reliability over open systems. Proper water treatment and monitoring are essential for maintaining system integrity and preventing operational issues. As industries continue to seek more sustainable and energy-efficient cooling solutions, closed cycle cooling water systems will play a significant role in meeting these challenges.
Related recommendations
chiller bath
401Chiller Baths: Precise Temperature Control for Diverse Applications Chiller baths, also referred to as refrigerated circulators, are essential tools in scientific laboratories and industrial pr...
View detailsportable chiller
117IntroductionIn the realm of cooling technology, portable chillers have emerged as a practical and flexible solution for a variety of cooling needs. Unlike traditional, large - scale chiller syste...
View detailschillers system
102IntroductionChillers systems are integral to modern cooling technology, playing a crucial role in a wide range of applications. They are designed to remove heat from a fluid, typically water or a...
View detailschiller s
423Chiller Systems: An In-Depth Analysis Introduction to Chiller SystemsChiller systems, or simply chillers, are used to cool fluids, typically water or a mixture of water and glycol, for various ...
View details
HelloPlease log in