5000 ton chiller
In – Depth Guide to 5000 Ton Chillers
A 5000 ton chiller is a massive and highly efficient cooling device, primarily used in large – scale industrial and commercial applications. The “ton” in the context of chillers refers to the cooling capacity, where one ton of cooling is equivalent to the amount of heat required to melt one ton of ice in 24 hours, approximately 12,000 BTU (British Thermal Units) per hour. So, a 5000 ton chiller can remove 60 million BTU of heat per hour.
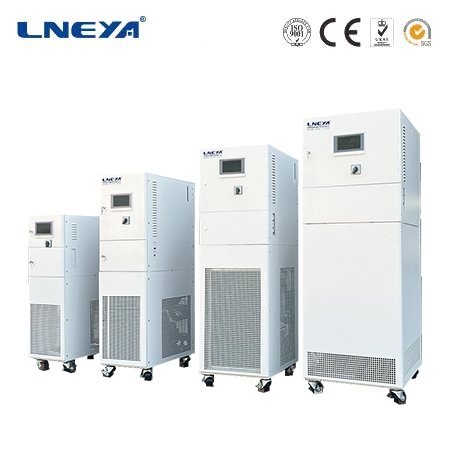
Working Principle
The fundamental working principle of a 5000 ton chiller is based on the vapor – compression refrigeration cycle, which is common across various chiller sizes.
Compression Stage: The compressor takes in low – pressure refrigerant vapor. For a 5000 ton chiller, the compressor is a large – scale, high – power unit. It compresses the refrigerant vapor to a high – pressure, high – temperature state. This process increases the internal energy of the refrigerant, raising its temperature substantially. The mechanical work done by the compressor is crucial for the entire refrigeration cycle to function.
Condensation: The hot, high – pressure refrigerant vapor enters the condenser. Here, heat is transferred from the refrigerant to a cooling medium. In air – cooled 5000 ton chillers, large – scale fans are used to blow ambient air over the condenser coils, dissipating heat. In water – cooled chillers, water from a cooling tower or other water sources circulates through the condenser, absorbing heat from the refrigerant and causing it to condense into a high – pressure liquid.
Expansion: The high – pressure liquid refrigerant passes through an expansion device, such as a thermostatic expansion valve or an electronic expansion valve. This valve reduces the pressure of the refrigerant, causing it to expand rapidly. As a result, the refrigerant’s temperature drops significantly, and it enters a low – pressure, low – temperature state.
Evaporation: The cold, low – pressure refrigerant enters the evaporator. In the evaporator, it comes into contact with the process fluid (usually water or a water – glycol mixture) that needs to be cooled. Heat from the process fluid is transferred to the refrigerant, causing the refrigerant to evaporate back into a vapor. The cooled process fluid is then circulated back into the industrial or commercial process.
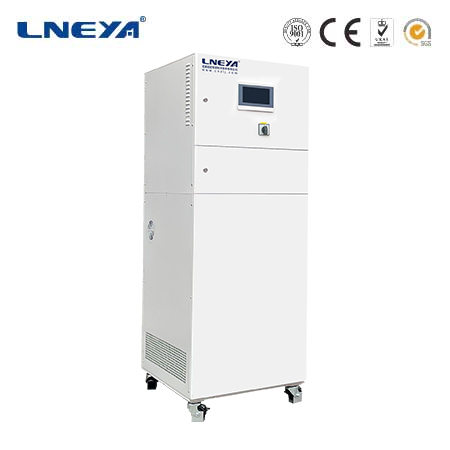
Types of 5000 Ton Chillers
Air – Cooled 5000 Ton Chillers
Advantages: These chillers are relatively easy to install as they do not require a complex water – cooling infrastructure like cooling towers. They are suitable for areas where water is scarce or difficult to access. They also have a simpler installation process compared to water – cooled chillers, which can be beneficial in terms of time and cost savings during the initial setup.
Limitations: However, air – cooled 5000 ton chillers are generally less energy – efficient than their water – cooled counterparts. The heat dissipation through air is not as effective as through water, which means they may consume more energy to achieve the same cooling capacity. Their performance can also be significantly affected by high ambient temperatures. When the outside air is hot, the ability of the chiller to reject heat is reduced, leading to a decrease in cooling efficiency.
Water – Cooled 5000 Ton Chillers
Advantages: Water – cooled 5000 ton chillers are highly energy – efficient. Water has a much higher heat capacity than air, allowing for more effective heat transfer. This makes them ideal for large – scale applications where energy savings are crucial. They also tend to operate more quietly than air – cooled chillers, which can be an important factor in some settings, such as near residential areas or in noise – sensitive commercial buildings.
Limitations: These chillers require a reliable source of water and a cooling tower. The installation cost is higher due to the need for additional equipment, such as cooling towers, water pumps, and extensive plumbing. Maintenance is also more complex, involving regular water treatment to prevent corrosion and scaling in the cooling system, as well as maintenance of the cooling tower and associated pumps.
Applications
Large – Scale Industrial Plants
In petrochemical refineries, 5000 ton chillers are used to cool various processes, such as distillation columns and chemical reactors. Precise temperature control is essential in these processes to ensure the quality of the refined products and the safety of the operations.
In large – scale data centers, which generate a massive amount of heat from servers and other electronic equipment, 5000 ton chillers are used to maintain the optimal operating temperature. This helps prevent server overheating, which can lead to data loss and system failures.
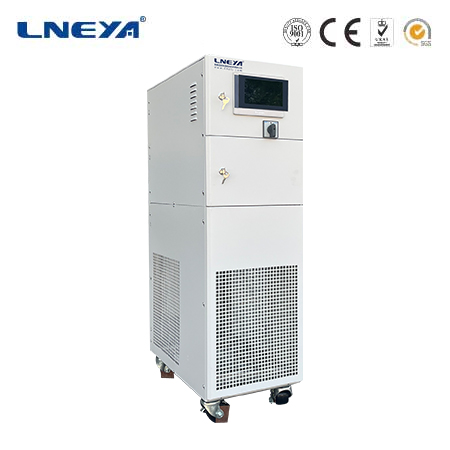
Commercial Buildings
In large – scale shopping malls and convention centers, 5000 ton chillers are used for central air – conditioning systems. These large – scale buildings require significant cooling capacity to provide a comfortable environment for occupants, especially during hot summer months.
In hospitals, 5000 ton chillers are crucial for maintaining the proper temperature in operating rooms, intensive care units, and pharmaceutical storage areas. Maintaining a stable temperature is essential for patient care and the integrity of medical supplies.
Cost Considerations
Initial Purchase Cost: The initial cost of a 5000 ton chiller is substantial. Water – cooled chillers are generally more expensive than air – cooled ones due to their more complex design and the need for additional equipment like cooling towers. The cost can also vary depending on the brand, quality, and additional features of the chiller. High – end models with advanced control systems and energy – saving features will be more costly.
Energy Consumption Cost: Over the lifespan of the chiller, energy consumption is a major cost factor. Water – cooled 5000 ton chillers, although more expensive upfront, may have lower energy costs in the long run due to their higher energy efficiency. However, factors such as local electricity rates and the actual operating hours of the chiller will also significantly impact the energy cost.
Maintenance Cost: Maintenance costs for 5000 ton chillers are relatively high. Regular maintenance is essential to ensure the reliable operation of the chiller. This includes tasks such as refrigerant level checks, compressor maintenance, and cleaning of heat exchangers. For water – cooled chillers, water treatment and cooling tower maintenance add to the overall maintenance cost.
Selection Criteria
Cooling Load Calculation: Accurately calculating the cooling load of the application is crucial. This involves considering factors such as the heat generated by equipment, the size of the space to be cooled, and any external heat sources. Oversizing or undersizing the chiller can lead to inefficiencies and higher operating costs.
Energy Efficiency: Look for 5000 ton chillers with high Energy Efficiency Ratio (EER) or Coefficient of Performance (COP) ratings. Energy – efficient chillers can save a significant amount of money on energy bills over their lifespan.
Maintenance Ease: Consider the ease of maintenance when selecting a chiller. Some models may be designed for easier access to components, which can simplify maintenance tasks. The availability of local service providers and spare parts should also be taken into account.
Noise and Vibration: In some applications, such as near residential areas or in quiet commercial settings, the noise and vibration levels of the chiller can be important factors. Water – cooled chillers generally operate more quietly than air – cooled ones, but proper installation and vibration isolation measures should also be considered.
Maintenance and Long – Term Operation
Regular Inspections: Regularly inspect the chiller for any signs of leaks, unusual noises, or vibrations. Check the refrigerant levels, oil levels in the compressor, and the condition of belts (if applicable). For water – cooled chillers, also check the water treatment system and the cooling tower for any signs of corrosion or scaling.
Cleaning: Clean the heat exchangers regularly to maintain optimal heat transfer efficiency. In air – cooled chillers, clean the air – cooled condensers to remove dust and debris. In water – cooled chillers, clean the cooling tower and the condenser tubes to prevent the build – up of deposits.
Filter Replacement: Replace the air and liquid filters as recommended by the manufacturer. Clogged filters can reduce the performance of the chiller and increase energy consumption.
Professional Servicing: Periodically, have a professional technician perform a comprehensive servicing of the chiller. This includes checking the electrical components, calibrating the controls, and performing any necessary repairs or adjustments. Regular professional servicing can extend the lifespan of the chiller and ensure its reliable operation.
In conclusion, 5000 ton chillers are complex and powerful cooling devices that play a crucial role in large – scale industrial and commercial applications. Understanding their working principle, types, applications, cost implications, selection criteria, and maintenance requirements is essential for making informed decisions and ensuring their efficient and reliable operation.
Related recommendations
What are the factors that affect the evaporation temperature of lab water chiller?
817What are the factors that affect the evaporation temperature of lab water chiller? The factors that affect the evaporation temperature of laboratory chillers include the following: oil ...
View detailscooling chillers
341Cooling Chillers: Technology, Efficiency, and Market Trends Cooling chillers play a critical role in temperature regulation across a spectrum of applications, including commercial HVAC systems ...
View detailsnitrogen heating system
373Introduction to Nitrogen Heating Systems Nitrogen heating systems are engineered to heat nitrogen gas to elevated temperatures for use in a variety of industrial processes. Nitrogen, being an i...
View detailscoolant chillers
191Coolant Chillers: A Comprehensive Guide Coolant chillers play a vital role in maintaining the efficiency and reliability of numerous industrial, commercial, and technological processes. By eff...
View details
HelloPlease log in