250 ton chiller
A 250 ton chiller is a powerful and substantial piece of cooling equipment designed to handle large-scale cooling requirements. With a cooling capacity of 250 tons, which equates to the removal of 3,000,000 British Thermal Units (BTUs) of heat per hour (since 1 ton of cooling capacity is 12,000 BTUs per hour), it is capable of providing significant cooling in various environments.
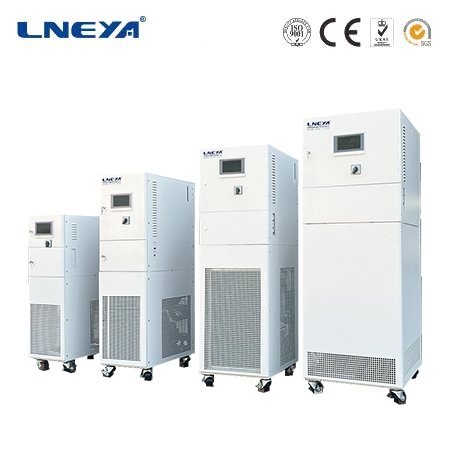
The components of a 250 ton chiller are engineered to function efficiently at this high capacity. Compressors are a central component. There are different types available, such as centrifugal compressors, which are often preferred for their high efficiency and ability to handle large volumes of refrigerant in high-capacity applications. Screw compressors are also common, offering good part-load efficiency and reliability. Reciprocating compressors, though less common in such large-scale units, can still be used in some cases. The compressor’s role is to raise the pressure and temperature of the refrigerant gas, which is then directed to the condenser.
The condenser is where the heat absorbed by the refrigerant is dissipated. Air-cooled condensers use fans to blow air over the condenser coils to transfer the heat to the surrounding atmosphere. However, for 250 ton chillers, water-cooled condensers are often more practical, especially in industrial or large commercial settings. In a water-cooled system, the heat is transferred to a water source, which may be a cooling tower or a closed-loop water system. The cooled refrigerant then passes through an expansion valve, where its pressure drops, allowing it to evaporate in the evaporator.
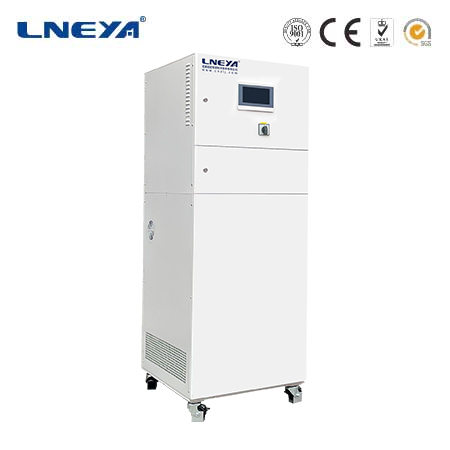
The evaporator is where the actual cooling occurs. As the refrigerant evaporates, it absorbs heat from the medium being cooled, such as water in a chilled water system. This cooled water can then be circulated through the facility to provide cooling. The expansion valve plays a crucial role in regulating the flow of the refrigerant and ensuring that it enters the evaporator at the appropriate pressure and temperature.
In large commercial buildings, 250 ton chillers are commonly used for air conditioning. Malls, hotels, and large office complexes often require a significant amount of cooling to maintain a comfortable indoor environment. These chillers can cool the water that is distributed through the building’s air handling units, which in turn cool the air supplied to the various spaces. The ability to handle large volumes of heat makes them suitable for these sprawling structures.
In industrial settings, 250 ton chillers are used for process cooling. For example, in manufacturing plants that produce chemicals, pharmaceuticals, or electronics, precise temperature control is essential for the production process. The chiller can cool the equipment or the process fluids to maintain the optimal operating temperature, ensuring product quality and process efficiency.
Data centers also rely on high-capacity chillers like the 250 ton variety. These facilities generate a massive amount of heat due to the operation of servers and other equipment. Effective cooling is crucial to prevent overheating, which can lead to system failures and data loss. The 250 ton chiller can provide the necessary cooling power to keep the data center environment within acceptable temperature ranges.
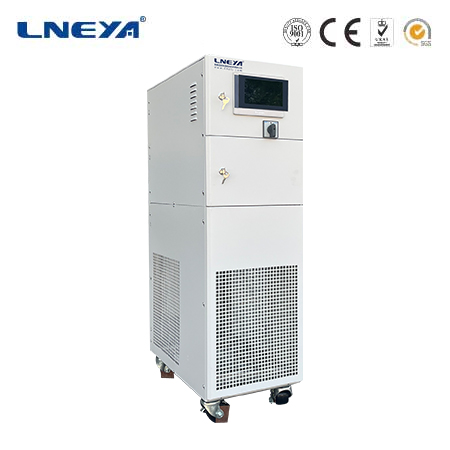
The working principle of a 250 ton chiller is based on the refrigeration cycle. The refrigerant continuously circulates through the system, undergoing a series of phase changes. It absorbs heat in the evaporator, is compressed to a higher temperature and pressure in the compressor, releases heat in the condenser, and then expands and cools down again in the expansion valve before returning to the evaporator.
Maintenance of a 250 ton chiller is of utmost importance to ensure its reliable and efficient operation. Regular inspections of the components are necessary to detect any signs of wear, damage, or leaks. Checking the refrigerant levels and ensuring that there are no leaks in the refrigerant system is crucial for maintaining the cooling capacity. Cleaning the heat exchangers, both the condenser and the evaporator, helps to improve heat transfer efficiency, which in turn reduces energy consumption. Additionally, monitoring the performance of the compressor, pumps, and other mechanical components and conducting preventive maintenance as recommended by the manufacturer can extend the lifespan of the chiller.
In conclusion, a 250 ton chiller is a vital piece of equipment for large-scale cooling needs. Its components, applications, working principle, and maintenance requirements all contribute to its effectiveness in providing the necessary cooling in various settings. By understanding these aspects, users can optimize the performance of the chiller and ensure its long-term operation.
Related recommendations
industrial chiller machine
61Types of Industrial Chiller MachinesIndustrial chillers are classified based on their cooling method, compressor type, and intended application, each offering unique advantages for specific indus...
View detailsair and water cooling system
370Air and Water Cooling Systems: Efficient Temperature Control for Diverse Applications Air and water cooling systems are engineered to provide optimal temperature control in a variety of setting...
View detailsportable chiller unit
173Portable Chiller UnitIn an increasingly dynamic and diverse range of industries, the demand for efficient and adaptable cooling solutions has led to the prominence of portable chiller units. Thes...
View detailssmall chiller plant
513Small Chiller Plant: Selection and Efficiency A small chiller plant is an essential component of heating, ventilation, and air conditioning (HVAC) systems, particularly where precise temperatur...
View details
HelloPlease log in